Toczenie wzdłużne
Przegląd produktów
Wybór wytaczaka ma duże znaczenie dla ekonomiki produkcji. Szeroki asortyment standardowy gotowych rozwiązań Sandvik Coromant obejmuje narzędzia o średnicach 10-100 milimetrów (0.40-9.84 cala), dostarczane do klienta w ciągu 24 godzin. Oferujemy też narzędzia niestandardowe o średnicy do 600 milimetrów (23.6 cala).
Dostępne są wytaczaki do obróbki na wysięgach 3–14 x BD. Ze złączem Coromant Capto proponujemy narzędzia o średnicach 16-100 milimetrów (0.63-3.94 cala).
Produktywna obróbka na krótkich wysięgach
Zasadniczo, na wysięgach do 4 x BD można stosować wytaczaki stalowe lub węglikowe, ale nawet w tym zakresie długości wytaczaki Silent Tools pozwalają uzyskać znaczną poprawę produktywności. Na wysięgach do 10 x BD stosuje się zazwyczaj stalowe wytaczaki z tłumieniem drgań, zapewniające odpowiednie warunki procesu obróbki. Wysięgi dłuższe niż 10 x BD wymagają użycia wzmacnianych węglikiem wytaczaków z tłumieniem drgań, zmniejszających ugięcie promieniowe i drgania.
Średnica wytaczaka, DMM | ||||
cale | ||||
![]() | ![]() ![]() | |||
Maks. wysięg | ||||
Stalowe wytaczaki z tłumieniem drgań | Wzmacniane węglikiem wytaczaki z tłumieniem |
![]() | Produkty specjalne | |
![]() | CoroTurn® SL – QC | |
![]() | CoroTurn® SL | |
![]() | Zintegrowane |
W przypadku wytaczaków składających się z trzonka z modułem tłumiącym i wymiennej głowicy, uszkodzenie gniazda płytki przynosi konieczność wymiany tylko tej ostatniej.
Asortyment głowic obejmuje około 500 modeli do ogólnych zastosowań tokarskich, przecinania i toczenia rowków oraz gwintów. W tym między innymi szybkowymienne głowice QS o średnicach 32 i 80 mm (1.26 i 3.15 cala). W ofercie jest także rodzina dedykowanych głowic CoroTurn HP.
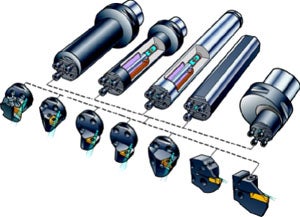
Łącząc głowicę z trzonkiem wytaczarskim z tłumieniem drgań Silent Tools zyskujemy dużą elastyczność zastosowań, w zależności od przeznaczenia głowicy.
Duże trzonki wytaczaków z chwytem cylindrycznym są dostępne z różnymi złączami, m. in. Coromant Capto i złączami szybkowymiennymi.
CoroTurn® SL
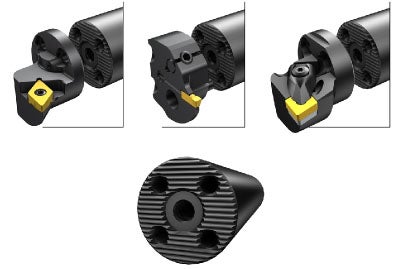
Rozwiązania szybkowymienne
![]() | ![]() |
![]() | |
![]() |
Typy wytaczaków
Toczenie wewnętrzne to rodzaj obróbki bardzo podatny na powstawanie drgań. Najlepszą stabilność i precyzję można uzyskać stosując narzędzie o możliwie największym przekroju i jak najmniejszym wysięgu. Stalowe trzonki wytaczaków z tłumieniem drgań serii 570-3C stanowią pierwszy wybór w operacjach toczenia wewnętrznego.
Trzonki serii 570-4C zalecane są do zgrubnej obróbki rowków i gwintów, gdzie działają większe siły promieniowe niż podczas toczenia ogólnego.
W tabeli poniżej przedstawiono maksymalny zalecany wysięg dla różnych typów trzonków wytaczaków.
Sztywność statyczna trzonka wzmacnianego węglikiem jest około 2,5 raza większa niż trzonka stalowego na wysięgu tej samej długości.
W zależności od długości wysięgu, stosowane są różne układy tłumiące:
Wykonanie trzonka wytaczaka | Toczenie | Toczenie rowków | Toczenie gwintów | |
Wytaczaki stalowe | 4 x BD | 3 x BD | 3 x BD | |
Wytaczaki węglikowe | 6 x BD | 5 x BD | 5 x BD | |
Stalowe wytaczaki z tłumieniem drgań | ![]() | 10 x BD | 5 x BD | 5 x BD* |
Wzmacniane węglikiem wytaczaki z tłumieniem drgań | ![]() | 14 x BD | 7 x BD | 7 x BD |
______________________________________________________________
* Narzędzia serii 570-4C
Rodzaj trzonka wytaczaka należy dobrać względem długości/średnicy toczenia. Wytaczaki węglikowe mają większą sztywność statyczną niż wytaczaki stalowe, dlatego mogą być stosowane na dłuższych wysięgach.
Jak przedstawiono na rysunku, dla danego wysięgu należy stosować wytaczak z odpowiedniego materiału.
Podczas toczenia zarysu gwintu i rowków działają większe siły promieniowe niż przy toczeniu wzdłużnym, ograniczając maksymalny zalecany wysięg. Moduł tłumiący zwiększa sztywność dynamiczną i umożliwia obróbkę na dłuższych wysięgach.
1 = monolityczny wytaczak stalowy | |
2 = wytaczaki węglikowe | |
3 = stalowe wytaczaki z tłumieniem drgań, wersja krótka 4–7 x BD | |
4 = stalowe wytaczaki z tłumieniem drgań, wersja długa 7-10 x BD | |
5 = wzmacniane węglikiem wytaczaki z tłumieniem drgań 10–12 x BD i 12–14 x BD |
Uwagi ogólne
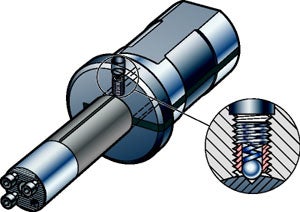
Stabilność mocowania i prawidłowe ustawienie w osi to dwa czynniki decydujące o klasie dokładności wykonania i chropowatości powierzchni przedmiotu. Aby uzyskać jak największą powierzchnię styku, zaleca się zamocować wytaczak cylindryczny za pomocą tulei dzielonej. Tuleje EasyFix zapewniają najbardziej stabilne mocowanie i dokładne ustawienie narzędzia w osi. Od ustawienia w osi zależy kąt natarcia i siły działające na narzędzie.
Zalecana tolerancja otworu mocującego to ISO H7. Dla uniknięcia odkształcenia plastycznego zaleca się, aby tuleja wykonana była z materiału o twardości przynajmniej 45 HRC. Śruby w żadnym wypadku nie mogą stykać się z chwytem wytaczaka, aby go nie uszkodzić.
Przy obróbce na długich wysięgach, właściwe mocowanie odgrywa kluczową rolę.
Wytaczaki - uwagi ogólne
- Dla zapewnienia właściwego styku mocowania, wymagana jest chropowatość powierzchni ~1 µm
- Zalecana długość mocowania to 4 × BD. W miarę możliwości, dla wytaczaków o długości powyżej 200 mm (7.87 cala) zalecamy długość mocowania 6 × BD
- Wytaczaki cylindryczne powinno się mocować za pomocą tulei dzielonych. Zalecana tolerancja otworu mocującego to ISO H7 Zalecana tolerancja mocowania to ISO H7
- Dla uniknięcia odkształcenia plastycznego zaleca się, aby tuleja wykonana była z materiału o twardości przynajmniej 45 HRC
- Do dużych wytaczaków można użyć podwójnego mocowania dzielonego
- Najlepszą stabilność mocowania wytaczaka zapewni dzielone mocowanie do wytaczaków
Średnicę i długość wytaczaka najlepiej dostosować do konstrukcji i wymiarów obrabianego przedmiotu. Rozwiązaniem pierwszego wyboru zapewniającym najlepszą stabilność mocowania jest złącze Coromant Capto lub tuleja dzielona do wytaczaków. O wyborze wytaczaka decydują średnica otworu i jego głębokość.
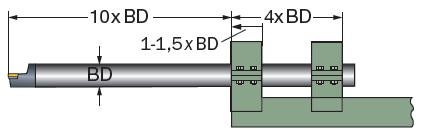
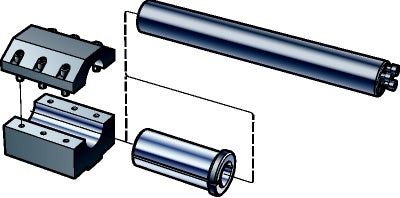
Mocowanie wytaczaków z tłumikiem drgań
Przeszkodą w uzyskaniu sztywności układu jest konstrukcja głowicy rewolwerowej w tokarce CNC oraz elastyczności obrabiarki wielozadaniowej. W przypadku dużych wytaczaków cylindrycznych, mała szerokość głowicy rewolwerowej nie zapewni dostatecznie dużego stosunku długości mocowania do średnicy wytaczaka, pogarszając tym samym stabilność układu.
Dla tokarek z głowicą rewolwerową rozwiązaniem zapewniającym stabilne zamocowanie i to bez użycia długich tulei, za to oferującym funkcję szybkiej wymiany, jest złącze typu Coromant Capto.
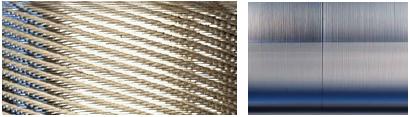
Właściwe mocowanie odgrywa kluczową rolę. Na zdjęciach
przedstawiono powierzchnie uzyskane przy 1) nieprawidłowym mocowaniu oraz 2) z użyciem dzielonego mocowania do wytaczaków.
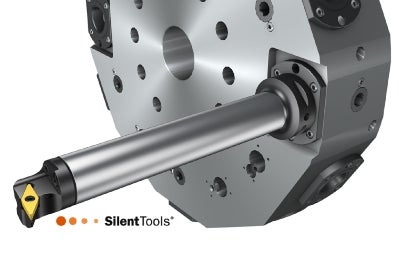
Tokarki z płaskim łożem
Tokarki z płaskim łożem i sztywnym uchwytem zapewniają zwykle lepszą sztywność i stabilność w porównaniu do tokarek z głowicą rewolwerową, mogą też utrzymać większe i dłuższe wytaczaki. Ograniczeniem po stronie obrabiarki może być w tym przypadku zastosowany imak narzędziowy, wielkość obrabiarki i sztywność wynikająca z zastosowanej konstrukcji.
Stabilność sań i prowadnic decyduje o wynikach obróbki z użyciem wytaczaków Silent Tools na długich wysięgach. Aby zoptymalizować wyniki obróbki, sztywny imak należy mocować za pomocą dużych, równomiernie i naprzemiennie rozmieszczonych suportów poprzecznych o długości równej lub większej od długości mocowania, 4 x BD. Należy pamiętać, że masa znacząco wzrasta ze wzrostem wielkości wytaczaka:
- Średnica 100 mm (3.94 cala) = 88 kg (194.0 lb)
- Średnica 120 mm (4.72 cala) = 140 kg (308.7 lb)
Najlepsza konstrukcja sztywnego uchwytu to rama typu A, na której wytaczak jest zamocowany bezpośrednio nad i pomiędzy saniami tokarki. | ![]() |
Czynniki decydujące o optymalnej wydajności wytaczaka to powierzchnia styku, konstrukcja i tolerancja wymiarowa narzędzia i oprawki. Najlepszą stabilność zapewnia oprawka całkowicie obejmująca chwyt wytaczaka. Nie zaleca się oprawek pryzmatycznych, ani oprawek z otworem cylindrycznym, gdzie trzonek dokręca się za pomocą śrub.
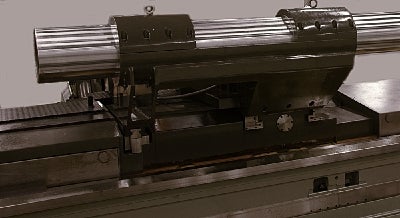
Mocowanie tulejami dzielonymi do wytaczaków o średnicy 300 mm (11.81 cala). Odległość między suportami poprzecznymi wynosi 1200 mm (47.24 cala) (4 x BD).
Przyrząd do ustawiania poprawnej wysokości ostrza w obrabiarcePoprawną wysokość ostrza wszystkich wytaczaków CoroTurn SL z chwytem cylindrycznym można ustawić szybko i dokładnie:
Nawet jeśli wytaczak ugnie się nieznacznie poniżej osi podczas obróbki, część chwytowa wytaczaka pozostaje w osi. Inne przyrządy do ustawiania poprawnej wysokości ostrza to wzorzec lub kieł. | ![]() | |
![]() | ||
![]() |
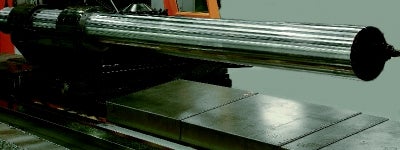
Szybkowymienna głowica CoroTurn SL na trzonku z tłumieniem drgań o średnicy 300 mm na wysięgu 10 x BD.
Ciśnienie chłodziwa i jego kierunek
Dla zapewnienia optymalnej trwałości narzędzia i bezpieczeństwa obróbki, chłodziwo należy kierować bezpośrednio do strefy skrawania. W przypadku narzędzi z głowicami szybkowymiennymi SL, regulację dysz podających chłodziwo należy przeprowadzać ręcznie, aby chłodziwo docierało wprost do strefy skrawania. Dla zapewnienia optymalnych wyników, należy stosować narzędzia ze zintegrowanym systemem podawania chłodziwa i kilkoma dyszami. Jest to ważne również przy toczeniu wewnętrznym na długich wysięgach. Dopływ chłodziwa reguluje się za pomocą klucza sześciokątnego.
Odstęp między wytaczakiem a wewnętrznymi ściankami otworu ma kluczowe znaczenie dla odprowadzania wiórów i ugięcia promieniowego. Do obróbki otworu o średnicy 100 mm (3.94 cala) można stosować wytaczak 80 mm (3.15 cala), który zapewnia wystarczający odstęp do odprowadzania wiórów chroniąc przed uszkodzeniem narzędzia i przedmiotu.
Chłodziwo można doprowadzać od tyłu wytaczaka złączami o ujednoliconej wielkości zaopatrzonymi w gwint BSP. Wytaczaki z tłumieniem drgań Sandvik Coromant są wyposażone w gwintowane otwory do podawania chłodziwa.
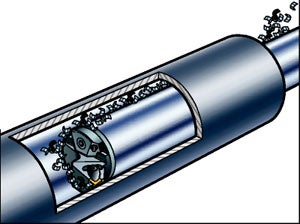
Czynniki wpływające na powstawanie drgań
Aby zminimalizować ryzyko drgań:
- Stosuj duży kąt przystawienia i dodatni kąt natarcia
- Stosuj płytki z dużym promieniem i kątem naroża
- Stosuj dodatnie makrogeometrie
- Obserwuj zużycie i zaokrąglenie krawędzi mikrogeometrii
- Głębokość skrawania powinna być większa niż promień naroża płytki skrawającej.
Przy małych promieniowych siłach skrawania maleje ugięcie narzędzia i ryzyko drgań. Najlepsze wyniki uzyskamy, gdy promieniowa głębokość skrawania będzie większa niż promień naroża płytki, przy kącie przystawienia 90° (0°). Jeśli promieniowa głębokość skrawania jest mniejsza, podobne rezultaty uzyskamy dla kąta przystawienia 45°.
![]() | Tendencja do drgań |
Kąt przystawienia wg ISO | |
Kąt przystawienia wg ANSI | |
Promień i kąt naroża, mm (cale) | |
Makrogeometria | |
Mikrogeometria | |
Stosunek głębokości skrawania do promienia naroża |
Należy pamiętać, że zmiana kierunku działania sił skrawania może przyczynić się do zmniejszenia ugięcia narzędzia:
- Przy kącie przystawienia bliskim 90° (0°), duża część siły posuwowej wraca od przedmiotu obrabianego w kierunku osiowym. Siły działające w kierunku osiowym powodują mniejsze ugięcie narzędzia niż siły o tej samej wartości działające w kierunku promieniowym.
- Przy toczeniu wewnętrznym kąt przystawienia nie powinien być mniejszy niż 75° (15°).
- Im bardziej dodatni kąt natarcia, tym mniejsze siły skrawania są potrzebne do obróbki przedmiotu. Małe siły skrawania to małe ugięcie narzędzia.
- Im mniejsze siły promieniowe, tym mniejsze ugięcie promieniowe
![]() | ![]() | |
![]() | ![]() | |
Kierunek działania sił: głównie osiowy | Kierunek działania sił: osiowy i promieniowy | |
![]() | ![]() | |
Przy ujemnym kącie natarcia siły skrawania wzrastają | Przy dodatnim kącie natarcia siły skrawania maleją |
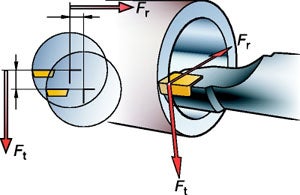
F
t
= siła styczna (skrawania) i Fr = siła promieniowa (odporowa)
Kąt naroża płytki
Kształt płytki należy dobierać do kąta przystawienia i możliwości podejścia do powierzchni przedmiotu. Praktyczna zasada mówi, że w celu zminimalizowania ryzyka drgań należy wybierać płytkę o jak najmniejszym promieniu naroża. Wyboru kąta naroża płytki można dokonywać według dwojakich kryteriów:
- Mały kąt naroża poprawia stabilność narzędzia, zapewnia duży luz między powierzchnią przedmiotu a tylną krawędzią płytki i małe zmiany przekroju warstwy skrawanej w przypadku, gdy narzędzie zacznie drgać w kierunku promieniowym.
- Duży kąt naroża sprawia, że płytka jest mocna i niezawodna, ale wymaga większej mocy obrabiarki, ponieważ większy odcinek krawędzi pozostaje zagłębiony w materiale
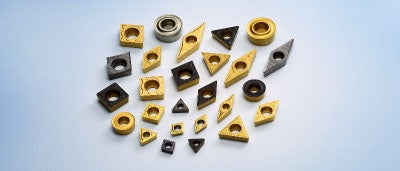
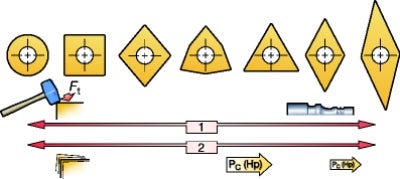
Geometrie dodatnie
Geometrie dodatnie i płytki z dodatnim kątem natarcia wywołują mniejsze siły skrawania i mniejsze ugięcie narzędzia. Z tego względu, zalecamy stosować płytki o silnie dodatniej geometrii i łamaczu wiórów dostosowanym do parametrów skrawania. Krawędź płytki o silnie dodatniej geometrii jest mniej odporna na zużycie i słabsza, a kontrola wiórów gorsza - opanowanie drgań wymaga kompromisu.
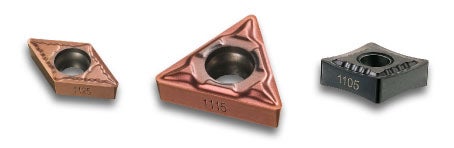
Płytki dogładzające wiper
Po geometrie wiper raczej nie należy sięgać w zastosowaniach podatnych na drgania, ponieważ opanowanie dużych sił skrawania i ugięcia promieniowego jest utrudnione. Natomiast w bardzo stabilnych warunkach, płytki wiper umożliwiają uzyskanie bardzo dobrej jakości wykończenia powierzchni i obróbkę z większymi parametrami skrawania.
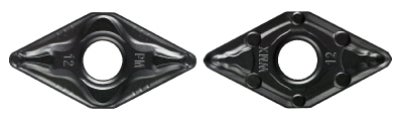
Zaokrąglenie krawędziPrzy mniejszym zaokrągleniu krawędzi, siły skrawania są mniejsze we wszystkich kierunkach. Dzięki temu, skrawanie przebiega łatwiej, a ugięcie narzędzia jest mniejsze. Krawędź płytek szlifowanych jest mniej zaokrąglona niż płytek prasowanych, podobnie w przypadku płytek niepokrywanych lub z cienkim pokryciem. | ![]() |
![]() | ![]() | ![]() | ||
M = Płytka prasowana | G = Typowa płytka szlifowana z mniejszym zaokrągleniem krawędzi | E = Płytka szlifowana z ostrą krawędzią, zapewniającą węższe tolerancje |
Parametry skrawania
Nie należy stosować płytek zużytych w poważnym stopniu, gdzie występuje np. starcie powierzchni przyłożenia (VB), ponieważ może ono prowadzić do ograniczenia niezbędnego luzu między krawędzią skrawającą a powierzchnią przedmiotu obrabianego i powodować drgania.
![]() | ![]() |
![]() |
Prędkość skrawania, vc
Przy właściwej prędkości skrawania na płytce nie powstaje narost, który pogarsza jakość wykończenia powierzchni, zwiększa siły skrawania i zmniejsza trwałość narzędzia.
- Zbyt duża prędkość skrawania może być przyczyną starcia powierzchni przyłożenia, które pogarsza bezpieczeństwo i przewidywalność obróbki z uwagi na zakleszczanie się wiórów, problemy z ich odprowadzaniem i ryzyko złamania płytki, szczególnie przy obróbce głębokich otworów
- Przy zbyt małej prędkości skrawania na płytce powstaje narost
- Nierównomierne zużycie skraca trwałość płytki i pogarsza jakość wykończenia powierzchni, dlatego zużycie narzędzia należy uważnie obserwować
- Prędkość skrawania w znacznej mierze zależy od obrabianego materiału
Głębokość skrawania, ap, i posuw, fn
Odpowiednie ap i fn decydują o polu przekroju poprzecznego warstwy skrawanej. Praktyczne wskazówki są następujące: Oto dwie żelazne zasady:
- Zaprogramuj ap większe od promienia naroża płytki
- Zaprogramuj wartość fn równą przynajmniej 25% promienia naroża płytki, w zależności od wymaganej chropowatości powierzchni
W przypadku wystąpienia drgań podczas obróbki na dużych wysięgach należy zastanowić się: po pierwsze, nad zwiększeniem posuwu, po drugie, nad zmianą prędkości skrawania. Zazwyczaj, lepsze wyniki obróbki uzyskujemy przy większych prędkościach skrawania.
Przekrój warstwy skrawanej
- Jeśli przekrój warstwy skrawanej jest zbyt duży, generowane są duże siły skrawania
- Jeśli przekrój warstwy skrawanej jest zbyt mały, wzrasta tarcie, które może doprowadzić do ścierania narzędzia i przedmiotu obrabianego
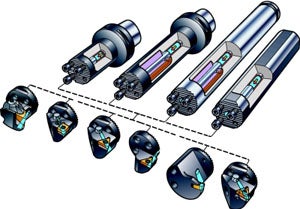
Wskazówki i porady
Aby zmniejszyć ryzyko drgań, wybieraj wytaczak o możliwie największej średnicy i stosuj jak najmniejszy wysięg. Stosuj się do zaleceń w zakresie długości mocowania - przynajmniej 4 x BD.
Niedozwolone jest skracanie wytaczaków wzmacnianych węglikiem o długości powyżej 10 x BD. W przypadku trzonków wytaczaków 570-4C, dopuszczalne jest mocowanie w miejscu modułu tłumiącego, czego nie wolno robić z wytaczakami 3C. Jeśli krótki trzonek wytaczaków serii 570-3C zostanie skrócony do długości minimalnej, długość mocowania nie może przekraczać 3 x BD, aby uniknąć mocowania w miejscu modułu tłumiącego. W żadnym wypadku nie należy skracać wytaczaków 570-3C o średnicy >100 mm (3.94 cala).
Modyfikacja standardowych wytaczaków
Średnica trzonka | L, długość minimalna po skróceniu | |
BD | Wersja krótka 4–7 × BD | Wersja długa 7-10 × BD |
mm | mm | mm |
16 | 100 | 155 |
20 | 125 | 200 |
25 | 155 | 255 |
32 | 190 | 320 |
40 | 240 | 410 |
50 | 305 | 520 |
60 | 380 | 630 |
80 | 630 | 630 |
100 | 770 | 770 |
Zalecana min. długość mocowania 4 × BD
Średnica trzonka | L, długość minimalna po skróceniu | |
BD | Wersja krótka 4–7 × BD | Wersja długa 7-10 × BD |
cale | cale | cale |
0.625 | 4 | 7 |
0.750 | 5 | 8 |
1.000 | 7 | 11 |
1.250 | 8 | 13 |
1.500 | 10 | 17 |
1.750 | 10.4 | 18 |
2.000 | 12 | 21 |
2.500 | 15 | 25 |
3.000 | 20 | 20 |
4.000 | 30.3 | 30.3 |
Zalecana min. długość mocowania 4 × BD
Dwie linie na wytaczaku oznaczają minimalny i maksymalny wysięg. Należy upewnić się, że stosowany wysięg mieści się w tym przedziale. W przeciwnym razie, nie ma gwarancji skuteczności działania modułu tłumiącego.
Odprowadzanie wiórów
Aby odprowadzanie wiórów odbywało się bezproblemowo, zaleca się stosować oprawkę ze zintegrowanym systemem podawania chłodziwa i płytki o geometrii formującej krótkie, spiralne wióry. W rozwiązaniu problemów z odprowadzaniem wiórów może pomóc zwiększenie natężenia przepływu chłodziwa, zmiana geometrii lub zwiększenie prędkości skrawania.
Można też spróbować zmodyfikować drogę prowadzenia narzędzia. Odwrócenie narzędzia
również może poprawić odprowadzanie wiórów.
Należy zadbać o wystarczający do odprowadzania wiórów luz między wytaczakiem a ściankami otworu. Jeśli zostanie to zaniedbane, narzędzie może wciskać wióry w ścianki otworu, może też dojść do uszkodzenia korpusu.
![]() | ![]() |
Regulacja dysz
Dopływ chłodziwa reguluje się za pomocą klucza sześciokątnego. Tego samego klucza można użyć do regulacji kierunku dysz głowic szybkowymiennych SL.
Płytki dogładzające wiper
Płytki dogładzające wiper pozwalają poprawić jakość wykończenia powierzchni i zwiększyć produktywność w stabilnych warunkach obróbki. Zaleca się stosować płytki wiper by zwiększyć posuw lub móc zastosować płytki o mniejszym promieniu naroża.
Wykonywanie gwintów wewnętrznych
W celu zmniejszenia ryzyka drgań, należy przestrzegać następujących zaleceń:
- Stosuj zmodyfikowany dosuw boczny
- Dosuw wgłębny na przejście powinien wynosić przynajmniej 0.06 mm (0.0024 cala) i nie przekraczać 0.2 mm (0.0078 cala)
- Ostatnie przejście wykonuj zawsze ze zmniejszonym dosuwem
- Wybieraj płytki o ostrej geometrii, aby zmniejszyć siły skrawania
Aby zapewnić optymalny przebieg odprowadzania wiórów:
- Stosuj zmodyfikowany dosuw boczny, który skieruje wióry w stronę wylotu otworu
- W stabilnych warunkach stosuj posuw od środka otworu do jego wylotu. Wybierz prawy lub lewy bok zarysu w zależności od potrzeby ukierunkowania spływu wióra
- Zastosowanie chłodziwa usprawni odprowadzanie wiórów
Kierunek spływu wiórów | Kierunek posuwu | ||
![]() | ![]() | ||
Posuw od środka otworu do jego wylotu | Zmodyfikowany dosuw boczny odprowadza wióry z otworu |
Wykonywanie rowków wewnętrznych i profilowanie
W celu zmniejszenia ryzyka drgań, należy przestrzegać następujących zaleceń:
- Stosuj konfigurację z jak najkrótszym wysięgiem i geometrią generującą jak najmniejsze siły
- Wybieraj płytki o wąskim ostrzu i wykonuj obróbkę nie w jednym, ale w kilku przejściach
- Aby zapewnić optymalny przebieg odprowadzania wiórów, zaczynaj od wylotu otworu i prowadź narzędzie w jego głąb tak, by przejścia częściowo się nakładały
- Jako metodę obróbki wykończeniowej rozważ toczenie wzdłużne. Zaczynaj od dna otworu
i prowadź narzędzie ku wylotowi - W celu poprawy kontroli wiórów i zmniejszenia ryzyka drgań, stosuj zagłębianie skośne/ toczenie wzdłużne
- Aby kontrolować wióry podczas obróbki zgrubnej, stosuj płytki prawe lub lewe
Typowa konfiguracja
Jeśli wytaczak pracuje w typowej konfiguracji, siły skrawania odpychają płytkę od materiału.
Konfiguracja alternatywna
Obrócenie wytaczaka zmienia kierunek sił skrawania, co wpływa na poprawę stabilności, a niekiedy także na usprawnienie odprowadzania wiórów. Metoda ta wymaga rozwagi i ostrożności, nawet przy małych średnicach. Jeśli siły skrawania zmaleją do 0, jak ma to miejsce w obróbce przerywanej, wytaczak odbije się od obrabianego przedmiotu w kierunku toczenia nabierając dodatkowej siły, co może spowodować uszkodzenie narzędzia i przedmiotu.
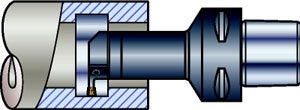
Konserwacja
Dla zapewnienia najwyższej wydajności obróbki, wszystkie części należy czyścić i smarować przynajmniej raz w roku. W razie potrzeby, substancję smarującą można zastosować także na śruby. Zużyte lub zniszczone śruby i podkładki należy wymienić.
Wytaczaki z tłumieniem drgań mogą ulec deformacji ze względu na cienkie ścianki. Podczas montażu należy sprawdzić prawidłowość mocowania wytaczaka. Korzystając z narzędzi Silent Tools należy zawsze dokładnie sprawdzić mocowanie. Prawidłowe dokręcenie śrub zapewnia klucz dynamometryczny.
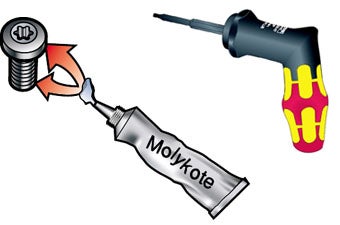
Podsumowanie: Jak unikać drgań
Zwiększ sztywność statyczną narzędzia
- Sprawdź mocowanie i konfigurację narzędzia
- Używaj oprawek Coromant Capto lub dzielonych uchwytów do wytaczaków
- Stosuj możliwie najmniejszy wysięg i narzędzia o jak największej średnicy
- Używaj narzędzi ze wzmocnionego materiału (w przypadku wytaczaków)
Zwiększ sztywność dynamiczną narzędzia
- Używaj płytek z mniejszym kątem naroża
- Stosuj narzędzia z tłumieniem drgań
- Zadbaj o jak najmniejszą masę w części roboczej narzędzia (czole)
Zmniejsz siły skrawania
- Stosuj dodatni kąt skrawania
- Używaj płytek o dodatniej geometrii z małym ER
Unikaj ugięcia narzędzia
- Zmień kierunek sił skrawania z promieniowego na osiowy
- Stosuj kąt przystawienia bliski 90° (0°)
- Głębokość skrawania powinna być większa niż promień naroża
Kontroluj wióry
- Zwiększ natężenie przepływu chłodziwa
- Zadbaj o luz między narzędziem a przedmiotem obrabianym
- Upewnij się, że ze strefy skrawania odprowadzane są wszystkie wióry
Uwaga!
Nie przeciążaj wytaczaków z tłumieniem drgań. Maksymalne dopuszczalne obciążenie jest podane na narzędziu. Możesz też obliczyć dopuszczalne obciążenie za pomocą kalkulatora dostępnego na stronie internetowej www.sandvik.coromant.com/calculators.