Käyttö – avarrus
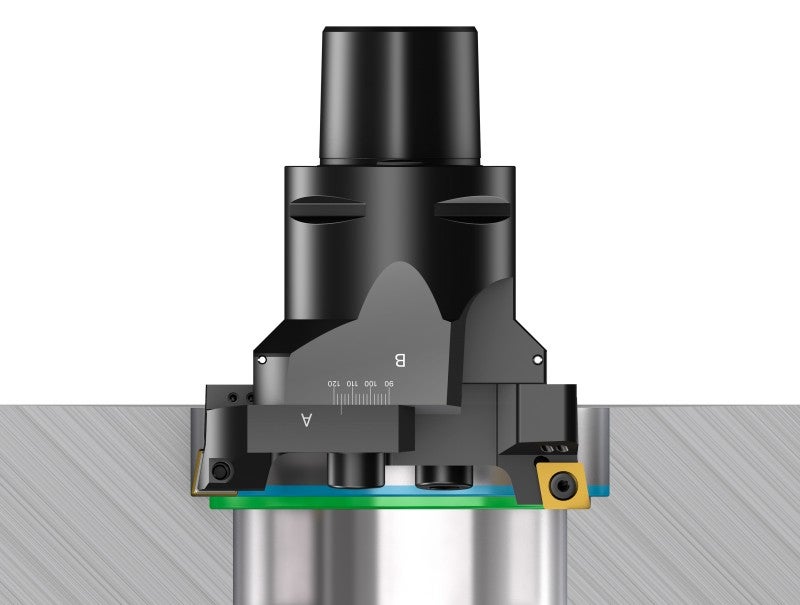
Avarrusprosessin optimoinnissa on otettava huomioon useita tekijöitä. Työkalukokoonpanon, terän ja lastuamisarvojen valinta on tehtävä huolellisesti tehokkaan lastunhallinnan takaamiseksi. Vinkeillämme pääset korkealaatuiseen lopputulokseen.
Tukeva avarrinkokoonpano
Avarrustöihin sopivaa pidintä valittaessa tärkeimpiä kriteerejä ovat taivutusjäykkyys ja vääntömomentin välityskyky. Paras tukevuus ja reiän laatu saadaan käyttämällä Coromant Capto® -kiinnitystä tai, pienillä halkaisijoilla, muuta modulaarista järjestelmää.
Coromant Capto® on ainoa todella tukeva moduulirakenteinen työkalujärjestelmä, joka on suunniteltu kaikenlaiseen metallin lastuamiseen, myös reikien koneistukseen. Eri töissä ja koneissa voidaan käyttää samoja lastuavia työkaluja ja liitäntäkappaleita, ja koko koneistamon työkalut voidaan yhtenäistää. Muistettavaa:
- Valitse mahdollisimman lyhyt liitäntäkappale
- Valitse mahdollisimman luja liitäntäkappale
- Jos tarvitaan supistuskappale, valitse mahdollisuuksien mukaan kartiomalli
- Käytä pitkillä vapaapituuksilla (> 4 × DCON) värinävaimennettuja liitäntäkappaleita
- Pitkillä vapaapituuksilla on varmistettava, että kiinnitys on tukeva, mieluiten niin että laippa tukeutuu karaan
Pienille halkaisijoille suunnitellut modulaariset järjestelmät, esimerkiksi Coromant® EH, tarjoavat paljon työkaluvaihtoehtoja. Käytössä on laaja valikoima erilaisia teräpäitä, liitäntäkappaleita ja varsia. Vakioiduilla työkaluilla voidaan pienentää työkaluvarastoa ja minimoida tuotantokatkokset.
Käyttö:
- Pitkää vapaapituutta vaativiin avarrustöihin isoissa koneistuskeskuksissa, halkaisijat 1–36 mm (0.039–1.42 in).
- Syvien taskujen koneistukseen, koska ratkaisulla saadaan vaadittu ulottuvuus tinkimättä prosessivarmuudesta
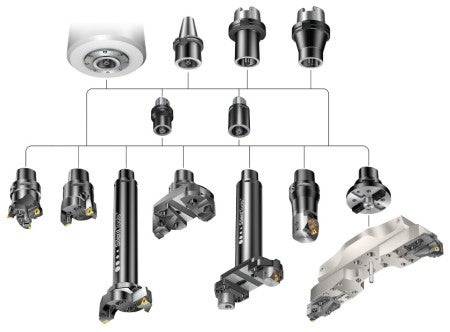
Ohjeita ja vinkkejä
- Parhaan tukevuuden saat käyttämällä mahdollisimman suurta liitoskokoa ja lyhyttä vapaapituutta
- Paranna puomin dynaamista jäykkyyttä hyödyntämällä vaimennusmekanismia
- Käytä pitkillä vapaapituuksilla (> 4 × kiinnityshalkaisija) värinävaimennettuja työkaluja
- Jos tarvitaan supistuskappale, valitse mahdollisuuksien mukaan kartiomalli
- Työkalukokoonpanon ja tukevuuden voi optimoida Coromant Capto® Tailor Made -supistuskappaleilla ja -jatkokappaleilla
- Pitkillä vapaapituuksilla paras tukevuus saadaan kiinnityksellä, jossa pitimen laippa tukeutuu karaan, esimerkiksi Coromant Capto®, HSK ja BIG-PLUS®.
Hyvä lastunhallinta avarruksessa
Lastunmuodostus ja -poisto ovat avarruksessa kriittisiä tekijöitä, varsinkin umpireikien koneistuksessa.
Varmista, että lastunpoisto on tehokasta. Lastutukokset heikentävät reiän laatua sekä terän luotettavuutta ja kestoikää. Terägeometria ja lastuamisarvot ovat ratkaisevan tärkeitä. Käytä lastuamisnestettä lastunpoiston tehostamiseksi, terien kestoiän pidentämiseksi ja reiän muototarkkuuden varmistamiseksi.
Sopimattomat lastuamisarvot voivat synnyttää liian lyhyitä/paksuja lastuja ja liian suuria lastuamisvoimia, jotka aiheuttavat työkalun taipumista ja värinää. Liian pitkät lastut voivat jäädä reikään ja huonontaa pinnankarheutta ja aiheuttaa tukoksia ja johtaa jopa terärikkoon.
Paras lastujen muoto on säännöllinen katko- tai spiraalilastu. Tällöin lastut poistuvat helposti reiästä. Lastunmurtoon vaikuttavia tekijöitä ovat:
- Terän mikro- ja makrogeometria
- Lastuamissyvyys ja -nopeus sekä syöttö
- Lastuttava materiaali
- Nirkonsäde
- Asetuskulma (asetuslisäkulma)
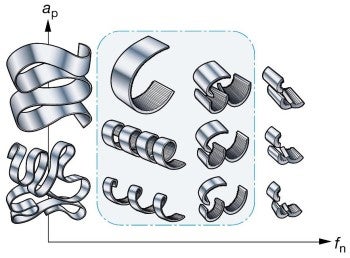
Lastuamisarvot avarruksessa
Pitkillä vapaapituuksilla lastuamisnopeutta on pienennettävä. Kaaviosta näkyy yleisperiaate, jonka mukaan lastuamisnopeutta tulee pienentää eri vapaapituuksilla ja geometrioilla.
vc
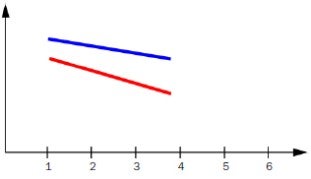
L1 / D5m
Lastuamisnopeus suhteessa vapaapituuteen eri geometrioilla
Sininen: -PR
Punainen:-WM
vc
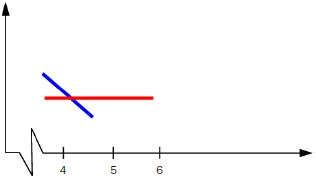
L1 / D5m
Lastuamisnopeus suhteessa vapaapituuteen
Sininen: Tavanomainen liitäntäkappale
Punainen: Värinävaimennettu liitäntäkappale
Huom:
Kaaviot kuvaavat ainoastaan yleisellä tasolla lastuamisnopeuden ja vapaapituuden/liitoskoon välistä suhdetta.
Yleensä voidaan noudattaa valitulle terälle ja laadulle annettuja suosituksia, mutta on syytä muistaa seuraavat poikkeukset:
- Tehokkaan lastunpoiston varmistamiseksi suositeltu lastuamisnopeuden aloitusarvo rouhinnassa on 200 m/min (656 ft/min) ja viimeistelyssä 240 m/min (790 ft/min).
- Aloitusnopeussuositukset hienoavarruspuomeille: Lyhyet teräs- ja kovametallipuomit: 120 m/min (395 ft/min)Pitkät teräspuomit: 90 m/min (295 ft/min)Täyskovametallipuomit hiotuilla geometrioilla: 60 m/min (195 ft/min)
- Liian pieneltä leveydeltä lastuava terä voi aiheuttaa kitkasta johtuvaa värinäalttiutta, jolloin lastuaminen ei ole sujuvaa
- Jos työkalun halkaisija on asetettu minimiarvoonsa, lastunpoisto on erityisen kriittinen tekijä, joten lastuamissyvyyttä voi olla syytä pienentää
- Hienoavarruksessa syöttöä rajoittaa vaadittu pinnankarheus
Näin pidennät terin kestoikää avarruksessa
Kolme tärkeintä parametria avarruksessa ovat lastuamisnopeus, syöttö ja lastuamissyvyys, joista jokainen vaikuttaa terän kestoikään. Niistä lastuamissyvyydellä on pienin vaikutus, ja seuraavana tulee syöttö. Lastuamisnopeudella on selvästi suurin vaikutus terän kestoikään.
Lastuamisnopeuden vaikutus
Liian pieni
- Irtosärmä
- Särmän tylsyminen
- Epätaloudellista
Liian suuri
- Nopea viistekuluminen
- Huono pinnankarheus
- Nopea kuoppakuluminen
- Plastinen muodonmuutos
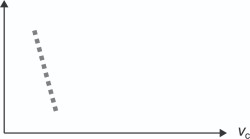
Lastuamisnopeus, vc, vaikuttaa merkittävästi kestoikään.
Valitse taloudellisin vc-arvo. (Terän kestoikä Y-akselilla)
Syötön vaikutus
Liian pieni
- Lastu ei katkea
- Nopea viistekuluminen
- Irtosärmänmuodostus
- Epätaloudellista
Liian suuri
- Heikko lastunhallinta
- Huono pinnankarheus
- Kuoppakulumista/plast. muodonmuutoksia
- Suuri tehontarve
- Lastujen hitsautuminen
- Lastuhakkauma
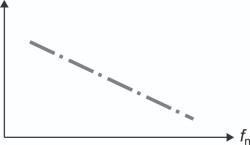
Syöttö, fn, vaikuttaa kestoikään vähemmän kuin vc.
(Terän kestoikä Y-akselilla)
Lastuamissyvyyden vaikutus
Liian pieni
- Huono lastunhallinta
- Värinä
- Liiallinen kuumeneminen
- Epätaloudellista
Liian suuri
- Suuri tehontarve
- Terärikot
- Suuret lastuamisvoimat
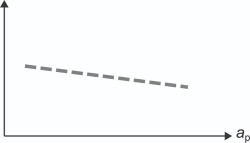
Lastuamissyvyydellä, ap, on vähäinen vaikutus kestoikään.
(Terän kestoikä Y-akselilla)
Oikean avarrusterän valinta
Hyvän lastunhallinnan varmistamiseksi on tärkeää valita oikea teräkoko ja -muoto, geometria ja nirkonsäde.
- Terän lujuuden ja taloudellisuuden kannalta on paras valita suurin soveltuva kärkikulma
- Terän lujuuden kannalta on paras valita suurin soveltuva nirkonsäde
- Jos työ on värinäaltis, valitse pienempi nirkonsäde
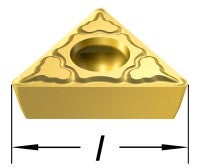
l = teräsärmän pituus (terän koko)
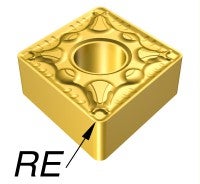
RE = nirkonsäde
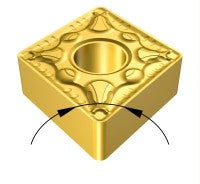
Kärkikulma
Lisätietoja: Rouhinta-avarrus ja Viimeistelyavarrus.
Avarrusterän muoto
Avarrusterien muoto ja kärkikulmat vaihtelevat suuresti kolmikulmaisista teristä, joilla on pieni kärkikulma, aina pyöreisiin teriin.
Kullakin muodolla on luonteenomaiset piirteensä. Tietyillä malleilla saadaan paras lujuus rouhintaan, toisilla taas hyvä ulottuvuus hienoavarruksessa.
Kullakin muodolla on myös omat rajoituksensa. Esimerkiksi erittäin ulottuvan terän varjopuolena on heikompi teräsärmä.

Särmälujuus (iso kärkikulma)
- Vahvempi teräsärmä
- Suuremmat syötöt
- Suuret lastuamisvoimat
- Värinäalttiimpi
Vähäinen värinäalttius (pieni kärkikulma)
- Heikompi teräsärmä
- Parempi ulottuvuus
- Pienemmät lastuamisvoimat
- Vähemmän värinäaltis
Pyöreät terät
Pyöreiden terien teräsärmä on kolmionmallisia lujempi, ja siksi ne kestävät suurempia lastuamissyvyyksiä.
Pyöreät terät ovat tuottava ratkaisu pinnoitemateriaalien, esim. öljy- ja kaasuteollisuuden käyttämien Inconel 625 -hitsausten koneistuksessa.
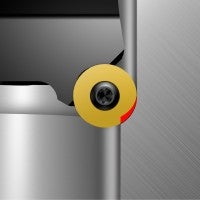
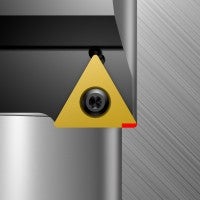
Terän nirkonsäde ja lastuamissyvyys
Nirkonsäde RE on yksi avarruksen tärkeimmistä parametreista. Nirkonsäteen valinta riippuu lastuamissyvyydestä ja syötöstä, ja se vaikuttaa pinnankarheuteen, lastunmurtoon ja terän vahvuuteen.
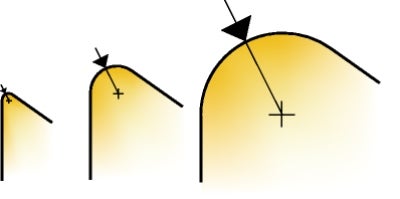
Pieni nirkonsäde
- Ihanteellinen pienille lastuamissyvyyksille
- Vähentää värinää
- Heikko teräsärmä
Suuri nirkonsäde
- Suuret syötöt
- Iso lastuamissyvyys
- Suuri särmälujuus
- Suuremmat radiaaliset lastuamisvoimat
Nirkonsäteen ja lastuamissyvyyden suhde vaikuttaa värinäalttiuteen. Usein edullinen ratkaisu on lastuamissyvyyttä pienempi nirkonsäde.
Pienillä lastuamissyvyyksillä lastuamisvoimat ovat radiaalisia ja pyrkivät painamaan terää irti reiän pinnasta. Kun lastuamissyvyys kasvaa, lastuamisvoimat muuttuvat aksiaalisiksi.
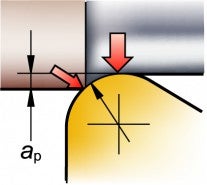
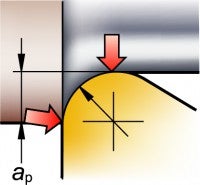
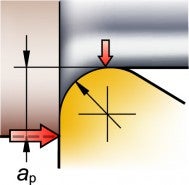
Nyrkkisääntönä voidaan todeta, että lastuamissyvyyden tulisi olla vähintään 2/3 nirkonsäteestä. Viimeistellessä pienillä lastuamissyvyyksillä on varottava, ettei lastuamissyvyys laskisi alle 1/3:aan nirkonsäteestä.
Pieni nirkonsäde minimoi radiaaliset lastuamisvoimat. Suuren nirkonsäteen etuna taas on vahvempi teräsärmä, parempi pinnankarheus ja särmään kohdistuvan paineen tasaisempi jakautuminen.
Nirkonsäde ja syöttö vaikuttavat suoraan koneistetun pinnan laatuun. Lisätietoa hyvän pinnankarheuden varmistamisesta.

Wiper-terät
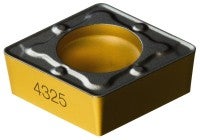
Wiper-terillä saadaan parempi pinnankarheus normaaleilla lastuamisarvoilla tai sama pinnankarheus tuntuvasti isommilla syöttöarvoilla.
Wiper-teriä ei suositella ei-tukeviin olosuhteisiin eikä pitkille vapaapituuksille.
Lastuamisneste ja jäähdytys avarruksessa
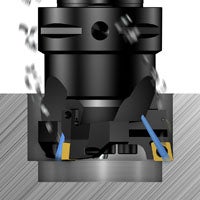
Lastuamisnesteen päätehtävät ovat lastunpoisto sekä terän ja työkappaleen jäähdytys ja voitelu. Lastuamisnesteen käyttö vaikuttaa reiän laatuun ja terän kestoikään. Läpijäähdytetyllä työkalulla lastuamisneste saadaan mahdollisimman lähelle teräsärmää.
- Käytä 5–8 %:n öljypitoisuutta
- Mitä suurempi paine ja nestemäärä, sitä parempi lastunpoisto
- Joskus riittää öljysumu- tai minimivoitelu, varsinkin alumiinin koneistuksessa
- Lyhytlastuisia aineita voidaan avartaa kuivana, mieluiten kappaleen ollessa vaakasuorassa tai kun koneistetaan läpireikiä Terien kestoikä lyheneePaineilman käyttö tehostaa lastunpoistoa merkittävästi
Huom:
- Ruostumattomien terästen (ISO M) ja kuumalujien superseosten (ISO S) kuivakoneistusta ei suositella lainkaan
- Lyhytlastuisissa aineissa voidaan käyttää ulkoista lastuamisnesteensyöttöä, kunhan nestevirta on jatkuva ja osuu suoraan lastuavalle särmälle. Jos tämä ei ole mahdollista, kokeile kuiva-avarrusta
Avarrustyökalun kokoaminen
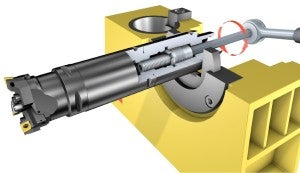
Sopiva avarrustyökalu on usein koottava useasta osasta:
- Luistit tai teräelementit
- Liitäntäkappaleet
- Supistuskappaleet
- Jatkokappaleet
- Peruskartiot
On tärkeää, että noudatetaan aina suositeltuja kiristysmomentteja ja käytetään sopivaa asennuslaitetta ja laadukasta esiasetuslaitetta.
Momenttiavain
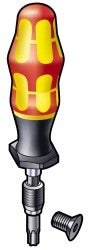
Avarrustyökalujen optimaalinen suorituskyky vaatii työkalun ja terien kiristämistä momenttiavaimella. Liian iso kiristysmomentti heikentää työkalun suorituskykyä ja voi johtaa terän, aluslevyn, joustavan aluslevyn ja ruuvin rikkoutumiseen. Liian pieni kiristysmomentti päästää terän liikkumaan, aiheuttaa värinää ja huonontaa koneistustulosta.
Tarkista avarrustyökalullesi suositeltu kiristysmomentti pyörivien työkalujen luettelosta.
Työkalujen kunnossapito

Tarkista säännöllisesti, etteivät teräsijat ole vaurioituneet koneistuksen tai käsittelyn yhteydessä. Tarkista, ettei teräsijoissa ole likaa tai lastuja.
Vaihda kuluneet ruuvit, aluslevyt ja joustavat aluslevyt. Käytä oikean kiristysmomentin takaamiseksi momenttiavainta.
Parhaan suorituskyvyn saamiseksi suosittelemme kaikkien naaras- ja urospuolisten osien puhdistamista ja öljyämistä vähintään kerran vuodessa. Voiteluainetta tulee levittää tarpeen mukaan sekä ruuvien kierteeseen että kantaan.
- Puhdista kaikki osat ennen kokoamista
- Käytä ruuveissa kierretahnaa
- Voitele osat vähintään kerran vuodessa
- Puhdista ja voitele hienoavarruspäät ja otsapistopää Vähintään kerran vuodessa, jatkuvassa käytössä kerran kuussa
- Käytä hapotonta kevyttä työstökoneöljyä, esim: Mobil Vactra Oil Nr. 2BP Energol HLP-D32Klueber Isoflex PDP 94
Hienoavarruspää voidellaan painamalla jousikuormitteinen kuula pohjaan ja tiputtamalla kuulalle muutama tippa kevyttä öljyä. Öljy pyrkii keskipakovoiman pakottamana ulospäin ja estää likaa pääsemästä liitäntäkappaleen sisään.
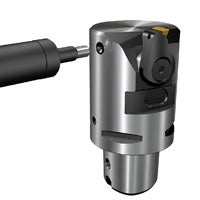
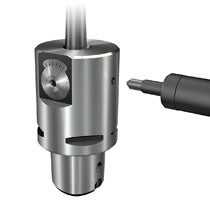
Hienoavarruspään voitelu
Eri aineiden avarrus
Katso yleissorvaussivujen osio Eri materiaalien sorvaus – samat suositukset pätevät myös avarrukseen.
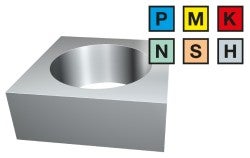
Rouhinta-avarrus
Rouhinnassa pääpaino on tehokkaassa aineenpoistossa ja tarkoituksena on valmistella... chevron_right
Avarrus
Avarrus on menetelmä, jossa olemassa olevaa reikää laajennetaan tai sen laatua parannetaan.... chevron_right
Avarrus
Tuotekokonaisuus Sandvik Coromantin valikoima sisältää rouhintaan ja viimeistelyyn... chevron_right
CoroBore® XL
CoroBore XL on isoille halkaisijoille tarkoitettu avarrinjärjestelmä. Laaja käyttöalue... chevron_right