Feinaufbohren
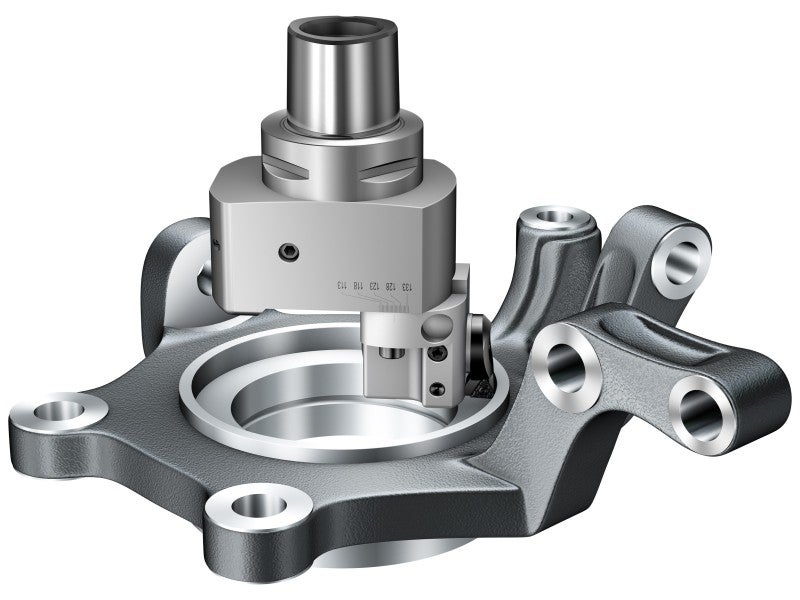
Das Feinaufbohren wird verwendet, um eine vorhandene Bohrung fertigzustellen und eine enge Bohrungstoleranz, korrekte Positionierung und hohe Oberflächengüte zu erhalten. Die Bearbeitung erfolgt mit geringen Schnitttiefen, üblicherweise unter 0,5 mm (0,020 Zoll).
Das einschneidige Aufbohren wird für das Schlichten mit geringen Schnitttiefen verwendet, wenn eine enge Toleranz (IT6 bis IT8) oder eine hohe Oberflächengüte gefordert werden. Der Durchmesser eines Feinaufbohrwerkzeugs kann über einen Präzisionsmechanismus im Mikrometerbereich eingestellt werden. Das einschneidige Aufbohren kann beim Schlichten von Bohrungen mit Toleranzen von IT9 und höher mit einem Aufbohrwerkzeug zum Schruppen erfolgen.
Rückwärtsaufbohren
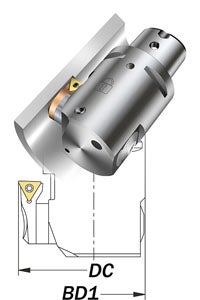
Das Rückwärtsaufbohren wird bei der Bearbeitung einer Bohrung mit einer Schulter, die nicht von der entgegengesetzten Seite erreicht werden kann, eingesetzt. Es findet aber auch Anwendung bei der Optimierung des Rundlaufs einer Bohrung mit einer Schulter, da der gesamte Bohrbereich von nur einer Position aus bearbeitet wird.
Hinweis: Achten Sie darauf, dass das Aufbohrwerkzeug mit der Schulter durch die Bohrung dringt und es nicht mit dem Bauteil kollidiert. Für das Rückwärtsaufbohren wird eine Durchgangsbohrung mit einem Mindestdurchmesser von DC/2 + BD1/2 benötigt.
Werkzeugeinstellung für das Rückwärtsaufbohren:
- Den Gewindestift aus dem oberen Kühlschmierstoffauslass entfernen und am unteren Auslass für Kühlschmierstoff montieren
- Kühlschmierstoffdüse einschrauben, um die richtige Position für den Kühlschmierstoff zu erhalten (bei den kleinsten Werkzeuggrößen kann der Gewindestift nicht am unteren Kühlschmierstoffauslass angebracht werden)
- Einbauhalter um 180° drehen
- Bei Bedarf Schneidenträgerverlängerung verwenden
- Drehrichtung umkehren
Außenaufbohren
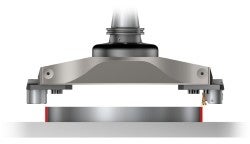
Die Außenbearbeitung kann mit einem Feinaufbohrwerkzeug durchgeführt werden, um eine enge Durchmessertoleranz zu erreichen.
Werkzeugeinstellung für das Außenaufbohren:
- Drehrichtung umkehren
- Schneidkopf um 180° drehen
- Die maximal mögliche Bearbeitungslänge, l3, und den Außendurchmesser des Werkzeugs beachten, um Kollisionen zu vermeiden
Bei der Außenbearbeitung rotieren die Masse des Schneidenträgers und des Feinaufbohrkopfes um das Werkstück herum und erzeugen hohe Zentrifugalkräfte. Deshalb muss die maximale Schnittgeschwindigkeit für die Außenbearbeitung in Bezug auf die maximale Schnittgeschwindigkeit für den Durchmesser bei einem um 180° gedrehtem Kopf berechnet werden, womit das Werkzeug für das Feinaufbohren konfiguriert ist.
Berechnungsbeispiel:
- Zu bearbeitender Außendurchmesser: 80 mm (3.15 Zoll)
- Der Innendurchmesser, der (mit dieser Position von Schneidenträger und Kopf) bearbeitet werden kann, beträgt dann: 210 mm (8.27 Zoll)
Hinweis: Immer 130 mm (5,12 Zoll) zu dem zu bearbeitenden Durchmesser hinzufügen, um den Durchmesser zur Berechnung der maximalen Drehzahl zu ermitteln. - Die max. Schnittgeschwindigkeit ist abhängig von der Innenbearbeitung (in diesem Beispiel für CoroBore® 825): 1200 m/min (3937 Fuß/min)
- 1200 m/min (3937 Fuß/min) bei Durchmesser 210 mm (8,27 Zoll) entspricht 1820 U/min. Somit ist 1820 U/min das Maximum, das für diese Position von Schneidenträger und Kopf erreicht werden kann.
- Für die Außenbearbeitung entspricht 1820 U/min einer Schnittgeschwindigkeit von 460 m/min (1509 Fuß/min) bei einem Durchmesser von 80 mm (3,15 Zoll).
Wahl der Wendeschneidplatte zum Schlichten
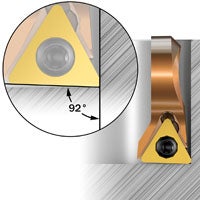
Wendeschneidplatten mit positiver Grundform sind die erste Wahl für alle Aufbohrbearbeitungen, da sie geringere Schnittkräfte als Wendeschneidplatten mit negativer Grundform erzeugen. Daneben ist ein großes Sortiment an Plattengeometrien verfügbar.
Der Einstellwinkel sollte beim Feinaufbohren mindestens 90° (0° Eintrittswinkel) betragen, um radiale Schnittkräfte zu minimieren und Vibrationen zu vermeiden.
Die meisten Feinaufbohrwerkzeuge von Sandvik Coromant haben einen Einstellwinkel von 92° (-2° Eintrittswinkel), um die Bearbeitung von Schultern und Grundbohrungen ohne Eingriff der gesamten Schneidkante zu ermöglichen.
Weitere Informationen zur Wahl der richtigen Wendeschneidplatte.
Schnittkräfte beim Feinaufbohren
Wenn sich das Werkzeug im Schnitt befindet, neigen eine tangentiale und eine radiale Komponente der Schnittkraft dazu, das Werkzeug vom Werkstück weg abzulenken. Die tangentiale Komponente drückt das Werkzeug nach unten und von der Mittellinie weg. Dies verkleinert den Freiwinkel.
Jede radiale Ablenkung bedeutet eine Verringerung der Schnitttiefe und der Spandicke, was eine Vibrationsneigung zur Folge hat.
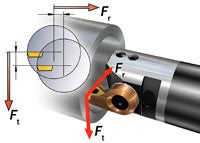
Auswuchten beim Feinaufbohren
Unwuchten, die durch ein asymmetrisches Werkzeug oder eine große Rundlauf-Ungenauigkeit entstehen, üben eine Kraft auf das Aufbohrwerkzeug aus. In den meisten Anwendungen ist die durch Unwucht hervorgerufene Kraft im Vergleich zu den Schnittkräften vernachlässigbar.
Bei hohen Schnittgeschwindigkeiten, insbesondere mit langen Überhängen, kann die Unwucht zu Vibrationen führen und damit die Qualität der Bohrung beeinflussen.
Suchen Sie Werkzeugempfehlungen?
Hier finden Sie unsere Zerspanungswerkzeuge chevron_right
Brauchen Sie Beratung?
Stellen Sie uns eine Frage chevron_right
Was es sonst noch über die Grundlagen unserer Metallzerspanung zu lernen gibt?
Registrieren Sie sich für unser kostenloses E-Learning Programm chevron_right
Werkzeugablenkung
Die Größen der tangentialen und radialen Komponenten der Schnittkraft werden beeinflusst durch die Schnitttiefe, den Eckenradius und den Einstellwinkel.
Ablenkungen in radialer Richtung beeinflussen den zu bearbeitenden Bohrungsdurchmesser. Die tangentiale Ablenkung führt dazu, dass die Schneidkante nach unten, weg von der Zentrumslinie gelenkt wird. Folgen Sie unseren Empfehlungen, um radiale Ablenkungen auszugleichen. Die Feinaufbohrwerkzeuge von Sandvik Coromant sind mit einem Einstellmechanismus ausgestattet, mit dem der Durchmesser in Schritten von 2 μm (0,0787 μZoll) eingestellt werden kann.
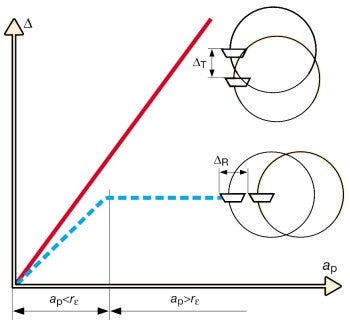
X-Achse: Schnitttiefe
Y-Achse: Ablenkung
Rote Linie: Tangentiale Ablenkung
Blaue Linie: Radiale Ablenkung
Checkliste für Feinaufbohranwendungen
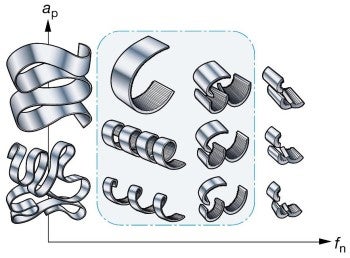
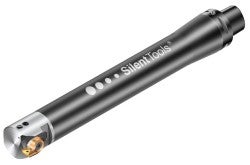
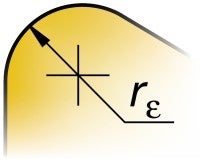
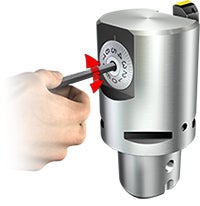
- Größtmögliche Kupplungsgröße oder größtmöglichen Bohrstangendurchmesser wählen.
- Einwandfreie Spankontrolle gewährleisten. Kurze/harte Späne können zu Vibrationen führen, und lange Späne können die Oberflächengüte verschlechtern oder Plattenbruch verursachen
- Kürzestmöglichen Überhang wählen, und bei Überhängen größer als 4xKupplungsgröße schwingungsgedämpfte Bohrstangen verwenden
- Ein großer Eckenradius (RE) verbessert die Prozesssicherheit und die Oberflächengüte, kann jedoch zu Vibrationen führen. Eckenradien von mehr als 0,4 mm (0,016 Zoll) werden nicht empfohlen. Beim Einsatz von Bohrstangen für kleine Durchmesser wird ein Eckenradius von 0.2 mm (0.008 Zoll) empfohlen
- Wendeschneidplatten mit dünnen Beschichtungen oder unbeschichtete Wendeschneidplatten sorgen normalerweise für geringere Schnittkräfte im Vergleich zu Wendeschneidplatten mit hoher Schichtdicke. Dies ist besonders wichtig bei einem großen Länge/Durchmesser-Verhältnis des Werkzeugs.
- Eine scharfe Schneidkante verbessert normalerweise die Qualität der Bohrung, weil sie weniger zu Vibrationen neigt
- Eine Geometrie mit offenem Spanbrecher wirkt sich häufig vorteilhafter aus
- Leicht schneidende Geometrie wählen, um eine gute Oberflächengüte zu erzeugen (nicht bei instabilen Bedingungen oder großen Überhängen empfohlen)
- Ein unzureichender Schneideneingriff kann durch Reibung während der Bearbeitung zu erhöhten Vibrationen führen
- Ein übermäßiges Eingreifen der Schneide (hohe Schnitttiefe und/oder hoher Vorschub) kann durch Werkzeugablenkung zu erhöhten Vibrationen führen
- Eine Wendeschneidplattensorte mit höherer Zähigkeit kann in einigen Situationen verwendet werden, wenn die Gefahr eines Spanstaus oder Vibrationsneigung besteht
- Zum Erreichen enger Bohrungstoleranzen immer sicherstellen, dass eine abschließende Einstellung nach der Messung des Bohrungsdurchmessers vorgenommen wird, während sich das Werkzeug noch in der Maschinenspindel befindet. Dadurch werden jegliche Fehlausrichtungen zwischen der Voreinstellvorrichtung und der Maschinenspindel, radiale Ablenkungen oder Verschleiß der Wendeschneidplatte ausgeglichen.
- Sicherstellen, dass Aufbohrwerkzeug und Werkstück sicher gespannt sind
- Kühlschmierstoff verwenden, um die Spanabfuhr, Standzeit und Bohrungsgeometrie zu verbessern
- Modulares System für kleine Durchmesser Ein konischer Schaft sorgt unabhängig vom verwendeten Spannfutter für eine geradere Bohrung bei langen Überhängen. Für Überhänge bis 6xD sollte ein konischer Schaft aus Vollhartmetall verwendet werdenBei kurzen Überhängen ist ein zylindrischer Schaft die beste Wahl für eine hohe GeradheitSchwermetallschäfte für höchste Stabilität und reduzierte Vibrationsneigung bei kurzen Überhängen wählenHochpräzisions-Hydraulikspannfutter für beste Stabilität und Prozesssicherheit verwenden
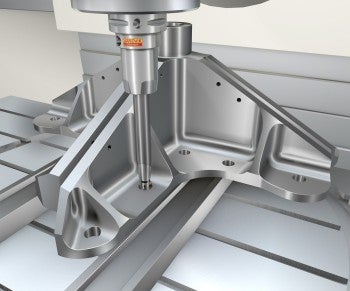
Für allgemeine Empfehlungen, siehe Aufbohren - Korrekte Anwendung.
Für Empfehlungen zu Drehmomentwerten, siehe Bedienanleitung unten.
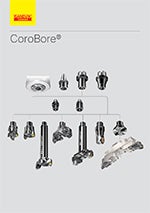
Suchen Sie Werkzeugempfehlungen?
Hier finden Sie unsere Zerspanungswerkzeuge chevron_right
Brauchen Sie Beratung?
Stellen Sie uns eine Frage chevron_right
Was es sonst noch über die Grundlagen unserer Metallzerspanung zu lernen gibt?
Registrieren Sie sich für unser kostenloses E-Learning Programm chevron_right
Fine boring head
Das vielseitige 391.37A/B System kann sowohl zum Feinaufbohren als auch Axialeinstechen... chevron_right
Schruppen
Das Schruppen erfolgt mit Fokus auf die Zerspanung und dient der Erweiterung einer... chevron_right
Bohren
Bohren und Gewindebohren sind Anwendungen, die am Ende des Produktionszyklus durchgeführt... chevron_right
Aufbohren
Das Aufbohren ist ein Bearbeitungsprozess zum Vergrößern oder zur Verbesserung der... chevron_right