Jak jsme ji vyrobili?
Jak společnost Sandvik vyrobila první nezničitelnou kytaru pomocí 3D tisku na světě
Rockové hvězdy všude po světě rozbíjí kytary již desítky let, ale jen málo z nich to činí s větší vervou než švédský kytarový virtuóz Yngwie Malmsteen. Společnost Sandvik se rozhodla otestovat své špičkové technologie a vyrobit s jejich pomocí první celokovovou nerozbitnou kytaru a nechat Malmsteena, aby se ji pokusil roztřískat.
Firma Sandvik tedy sezvala všechny své odborníky, aby společně prokázali, jak lze využít udržitelné nejmodernější technologie na výrobu něčeho, co je vysoce přesné i neskutečně odolné.
„Pokročilé materiály, přesné obrábění, aditivní výroba, výroba poháněná daty – to jsou právě ty procesy, které potřebujete k výrobě tak složitého a nádherného produktu, jako je kytara pro mistrovského hudebníka,“ říká Klas Forsström, prezident Sandvik Machining Solutions. „Chtěli jsme ale také dokázat, že může být i nerozbitná, ať už se Yngwie bude snažit sebevíc. Tento projekt se zdál jako perfektní zkouška našich schopností a možností – a stejně tak i jeho.“
Spolupráce od samého začátku
Společnost Sandvik již několik měsíců před plánovaným koncertem na Floridě sezvala do Švédska všechny odborníky na materiály, obráběcí procesy a aditivní výrobu napříč celou společností, aby se společně zamysleli nad tím, jak se s tou výzvou vypořádat.
Jelikož společnost Sandvik kytaru nikdy předtím nevyráběla, navázala spolupráci s vyhlášeným výrobcem kytar ze Spojeného království, firmou Drewman Guitars. „Museli jsme přijít s naprosto inovativním návrhem,“ říká designér společnosti Drewman Andy Holt. „Chtěli jsme, aby muzikanti říkali, že takto vyrobenou kytaru nikdy předtím neviděli.“
Holt vzpomíná, že v průběhu vývoje nastalo období, kdy inženýrům ze společnosti Sandvik posílal nové digitální návrhy každý den. V úzké spolupráci s výrobcem kytar tak vzniklo něco, o čem obě strany prohlásily, že je mistrovským dílem technologické kreativity.
První nerozbitná kytara na světě
Henrik Loikkanen, vývojář obráběcích procesů ve společnosti Sandvik Coromant, na kytaru hraje již od svého mládí, kdy začal zbožňovat Malmsteena. Nikdy ale žádnou nerozbil („Vyšlo by to moc draho,“ přiznává Loikkanen). Aby tedy Loikkanen pochopil, co se přesně děje, když Malmsteen nástroj rozbíjí, vyhledal si záznam na YouTube.
„Museli jsme navrhnout kytaru, která je nerozbitná všemi způsoby, kterými se můžete pokusit kytaru rozbít,“ vysvětluje Loikkanen. „Největší konstrukční výzvou byl kritický spoj mezi krkem a tělem kytary, který se většinou rozlomí jako první.“ Proto se inženýři ze Sandvik Coromant rozhodli tento spoj úplně eliminovat. Krk s hmatníkem se rozšiřovaly do obdélníkové desky, která sahala hluboko do těla kytary.
Jelikož má Yngwie nad tóny nejlepší kontrolu na vroubkovaném hmatníku, inženýři museli materiál mezi pražci řezat v dlouhých, hladkých obloucích. Aby byla kytara co nejlehčí, společnost Sandvik Coromant vydlabala vnitřní část krku a hmatníku.
„Výška pražců musela být naprosto dokonale zarovnaná, jinak by mohlo být slyšet, jak se struny některých pražců dotýkají,“ říká Loikkanen.
Data na špici
Dlouhé, štíhlé díly, jako je právě hmatník a krk, jsou při obráběcím procesu nejvíce náchylné ke zkroucení. Sandvik Coromant proto využil pokročilého software k digitální simulaci postupu ještě před tím, než byl proveden první řez.
„Přesnost byla naprosto kritická,“ vysvětluje Henrik Loikkanen. „Náš software je postaven na letech zkušeností. Poskytl nám doporučení ohledně nástrojů a způsobů obrábění, které nám umožnily na některých místech hmatník vyfrézovat až do komplikované tloušťky jednoho milimetru.“
Díky automatizovanému procesu mohl být hmatník vyroben na jediném stroji. Celý proces zahrnoval 90 samostatných úkonů a podařilo se jej dokončit bez zastavení stroje či nasazování nových nástrojů a úprav způsobu obrábění.
„Na začátku vložíte surový materiál a na konci máte dokončený díl,“ říká Loikkanen. „Jedná se o mnohem inteligentnější způsob úběru materiálu. Zkrátí se tak doba cyklu i náklady na výroby jednotlivých dílů.“
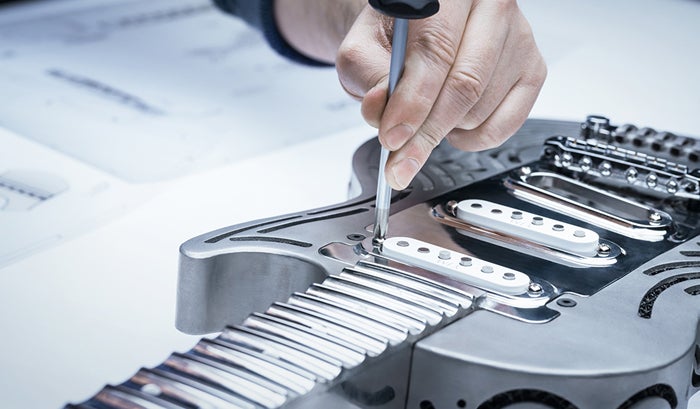
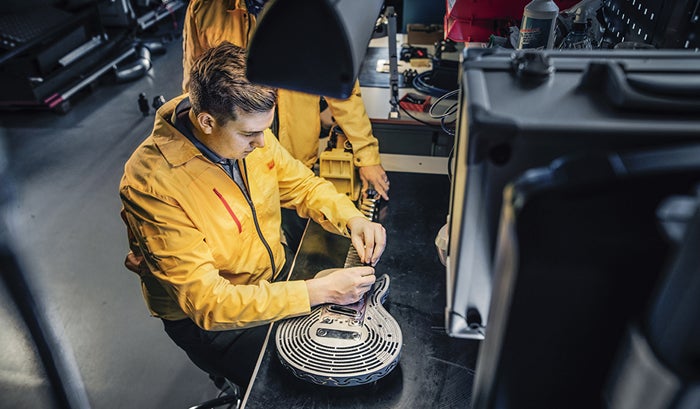
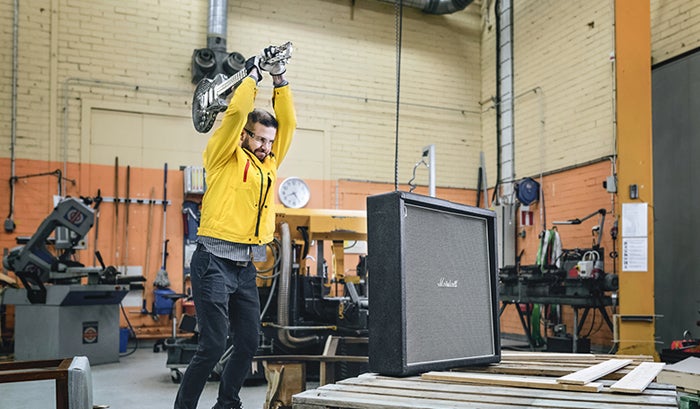
Inženýrům se dařilo vyrábět oproti předchozím verzím stále lehčí prototypy, až byla nakonec vyrobena výsledná kytara. Jemné obráběcí nástroje CoroMill® zajistily kovu krásně hladkou a lesklou povrchovou úpravu.
Podle Loikkanena byla pro výrobu nerozbitné kytary klíčová právě spolupráce různých divizí firmy Sandvik. Pomohl tak oddělení Sandvik Additive Manufacturing s frézováním povrchu těla kytary a menších dílů z titanu vytištěných na 3D tiskárně. Sandvik Coromant dále spolupracoval s Sandvik Materials Technology při výběru oceli a zabudování hyper-duplexní mřížkové struktury do krku. Týmová práce byla podle něj hlavním smyslem výroby této kytary.
„Společnost Sandvik Coromant je známá tím, že pomáhá svým zákazníkům se složitými úkoly, přičemž jim neposkytuje pouze nástroje, ale pomáhá též s vývojem těch nejlepších způsobů používání našich nástrojů v procesech našich zákazníků,“ říká Loikkanen.