Tornalama
Ürün gözden geçirme
Delik işleme barası seçimi, üretim ekonomisinde büyük bir etkiye sahiptir. Sandvik Coromant takım programı kapsamlıdır ve 24 saat içinde teslim edilen standart takımlar olarak 10'dan 100 milimetreye kadar (0.40 - 9.84 inç) çözümler içerir. Bu aralık dışında, 600 milimetreye kadar (23.6 inç) özel, ısmarlama çözümler de sunulmaktadır.
Coromant Capto için 3–14 x BD bara kullanma mesafeleri mevcuttur ve 16 - 100 milimetreye kadar (0.63 - 3.94 inç) çap seçenekleri bulunmaktadır.
Kısa kullanma mesafeleri için verimlidir
Genelde 4 x BD'lik kullanma mesafelerinde çelik ya da karbür delik işleme baraları kullanabilirsiniz, ama bu ürün aralığında bile Silent Tools barası size verimlilik anlamında avantaj sağlayacaktır. 10 x BD'ye kadar çıkan kullanma mesafeleri için genelde sönümlemeli çelik delik işleme barası kullanılırken 10 x BD üzeri kullanma mesafelerinde radyal sapma ve titreşimi önlemek için karbür takviyeli ve sönümlemeli delik işleme barası kullanılır.
Delik işleme barası çapı, DMM | ||||
inç | ||||
![]() | ![]() ![]() | |||
Maksimum kullanma mesafesi | ||||
Çelik sönümlemeli delik işleme baraları | Karbür takviyeli sönümlemeli delik delme baraları |
![]() | Sipariş üzerine imal edilen ürünler | |
![]() | CoroTurn® SL – QC | |
![]() | CoroTurn® SL | |
![]() | Entegre |
Kesme kafaları ve Silent Tools sönümlemeli delik işleme baralarıyla birlikte çalışıyorsanız, uç yuvasında hasar olduğunda kafayı rahatlıkla değiştirebilirsiniz.
Genel tornalama, ayırma, kanal açma ve diş açma işlemleri için 32 ve 80 mm çapında (1.26 ve 3.15 inç) Quick Change QS ürününün de bulunduğu 500 farklı kesme kafasından oluşan geniş kapsamlı bir çözüm bulunmaktadır. CoroTurn HP kesme kafalarının bulunduğu özel bir program da mevcuttur.
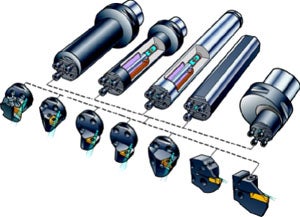
Kesme kafaları ve Silent Tools sönümlemeli delik işleme baraları bir arada kullanıldığında farklı uygulamalarda yüksek esneklik sunar.
Büyük silindirik delik işleme baraları, Coromant Capto ve Quick Change bağlama üniteleri gibi birçok farklı bağlamayla gelir.
CoroTurn® SL
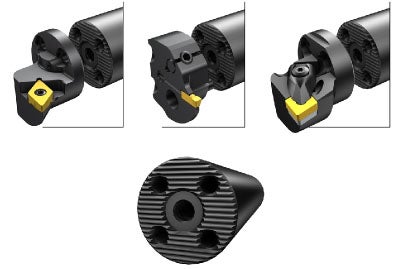
Quick Change QS
![]() | ![]() |
![]() | |
![]() |
Bara tipleri
Delik tornalama titreşime karşı çok hassastır. Olabilecek en iyi stabiliteyi ve hassaslığı elde etmek için takım kullanma mesafesini küçültün ve mümkün olan en büyük takım boyutunu seçin. Çelik sönümlü delik delme baralarıyla delik tornalama için ilk bara tercihi 570-3C'dir.
Radyal kuvvetlerin tornalamaya göre daha büyük olduğu kanal ve diş açma işlemleri için önerilen bara tipi 570-4C'dir.
Aşağıdaki tabloda farklı bara tipleri için önerilen maksimum kullanma mesafeleri bulunmaktadır.
Karbür takviyeli bir baranın statik sertliği, aynı kullanma mesafesine sahip bir çelik baraya kıyasla yaklaşık 2.5 kat daha yüksektir.
Farklı kullanma mesafeleri için farklı sönümleme sistemleri bulunmaktadır:
Bara tipi | Tornalama | Kanal açma | Diş çekme | |
Çelik delik işleme baraları | 4 x BD | 3 x BD | 3 x BD | |
Karbür delik işleme baraları | 6 x BD | 5 x BD | 5 x BD | |
Çelik sönümlemeli delik işleme baraları | ![]() | 10 x BD | 5 x BD | 5 x BD* |
Karbür takviyeli sönümlemeli delik işleme baraları | ![]() | 14 x BD | 7 x BD | 7 x BD |
______________________________________________________________
* 570-4C baralar
Uygun uzunluk - çap oranı elde etmek için delik işleme barası malzemesini seçin. Karbür bara çelik baradan daha yüksek statik sertliğe sahiptir, bu yüzden daha uzun kullanma mesafeleri tercih edilebilir.
Şekilde görüldüğü üzere, uygun uzunluk - çap oranını elde etmek için aşağıdaki delik işleme barası malzemeleri seçilebilir.
Diş ve kanal açma tornalamaya göre daha büyük radyal kesme kuvvetleri uygular ve bu da önerilen maksimum kullanma mesafesini düşürür. Sönümleme mekanizması dinamik sertliği yükseltir ve daha büyük kullanma mesafelerine izin verir.
1 = yekpare çelik bara | |
2 = karbür baralar | |
3 = çelik sönümlemeli, kısa versiyon 4–7 x BD | |
4 = çelik sönümlemeli, uzun versiyon 7–10 x BD | |
5 = karbür takviyeli sönümlemeli delik işleme barası 10–12 x BD & 12–14 x BD |
Temel dikkat edilecekler
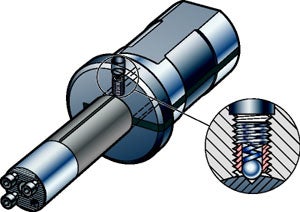
Bağlama kararlılığı ve doğru eksen ayarı, parçanızda doğru boyutsal toleranslar ve yüzey kalitesi elde etmek için iki önemli faktördür. Maksimum temas alanı sağlamak için, silindirik delik işleme barasını ayrı bir yarıklı kovan tutucuda bağlayın. EasyFix kovanlarla en kararlı bağlama ve en doğru eksen yüksekliğine ulaşabilirsiniz. Eksen ayarı hem talaş açısını hem de takımdaki kesme kuvvetini etkiler.
Tavsiye edilen bağlama toleransı ISO H7'dir ve kalıcı deformasyonun önlenmesi için minimum 45 HRC'lik ayrı bir yarıklı kovan malzemesi önerilmektedir. Baraya hasar verebileceği için vidaları kesinlikle bara sapıyla temas ettirmeyin.
Uzun takım taşma mesafelerinde doğru bağlamaya fazla değer verilemez.
Delik işleme baraları - genel
- Yeterli bağlama teması için ~1 μm'lik yüzey kalitesine ulaşılmalıdır
- Önerilen bağlama uzunluğu 4 × BD'dir. Mümkünse 200 mm (7.87 inç) üzerindeki delik işleme baraları için 6 x BD bağlama uzunluğu önerilmektedir
- Yarıklı kovanlarda silindirik delik işleme baraları. Tavsiye edilen bağlama toleransı ISO H7'dir
- Kalıcı deformasyonun önlenmesi için yarıklı kovan malzemesi minimum 45 HRC olmalıdır
- Bara büyükse çift rulman başlığı kullanın
- En iyi bağlama kararlılığı için yarıklı bir delik işleme barası tutucusu kullanın
Delik işleme barasının çapını ve uzunluğunu parça tasarımı ve boyutları belirlemelidir. En iyi bağlama kararlılığı için ilk tercih Coromant Capto kaplin ve yarıklı kovanlardır. Tabana ulaşmak için gereken delik çapı ve uzunluğu hangi delik işleme barasının kullanılacağını gösterecektir.
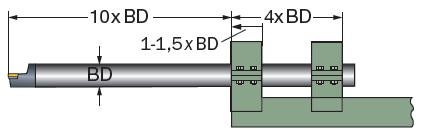
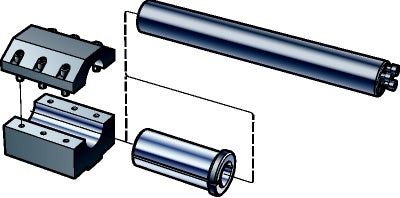
Silent Tools baralarının bağlanması
CNC torna taret tasarımı ya da çok amaçlı tezgah esnekliği sebebiyle, rijitlik genelde düşürülür. Küçük taret genişliği, büyük silindirik delik işleme baralarında bağlama uzunluğu ile bara çapı arasındaki oranı küçültür ve dolayısıyla kurulum kararlılığını zayıflatır.
Coromant Capto kaplin aynı zamanda taretli bir torna tezgahında da çözüm olabilir. Uzun kovanlara ihtiyaç kalmaz ve ekstra avantajlarla birlikte kararlı bir kurulum elde edilir.
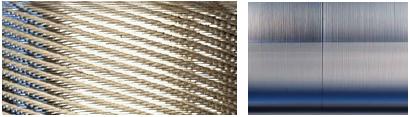
Doğru bağlamanın önemi azımsanamaz. Resimlerde
1) hatalı bağlama ve 2) yarıklı kovan bağlamasıyla elde edilen yüzey kaliteleri gösterilmektedir.
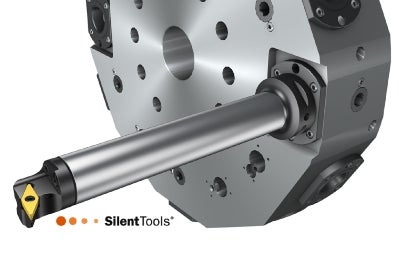
Düz yataklı tornalar
Taretli tornalara kıyasla, takım taşıyıcılı (suportlu) düz yataklı tornalar genelde daha rijit ve kararlıdır ayrıca daha büyük ve uzun delik işleme baralarını taşıyabilir. Bu durumda tezgahı; takım taşıyıcı, tezgah ölçüsü ve tasarımdaki rijidite sınırlandırıyor olabilir.
Tezgah kızaklarının ve kamalarının kararlılığı, uzun takım taşma mesafelerine sahip Silent Tools delik işleme baralarında iyi sonuç almak için önemlidir. En iyi sonuca ulaşmak için takım taşıyıcı bağlaması, çapraz kamalar tamamen ayrı, eşit ya da 4 x BD bağlama uzunluğundan daha geniş olacak şekilde kullanılmalıdır. Bara boyutu arttıkça ağırlığın da çok ciddi bir artış gösterdiği unutulmamalıdır:
- Çap 100 mm (3.94 inç) = 88 kg (194.0 lb)
- Çap 120 mm (4.72 inç) = 140 kg (308.7 lb)
En iyi takım taşıyıcı tasarımı, baranın tezgahın doğrudan üstüne ve kızaklarının arasına yerleştirildiği A çerçevesidir. | ![]() |
Delik işleme barasında en iyi performans ulaşmak için takım ile takım tutucu arasındaki temas, tasarım ve boyut toleransı önemli faktörlerdir. En iyi kararlılık, barayı tamamen kavrayan bir tutucuyla elde edilir. V tipi bara tutucu ve vidalı silindirik tutucular tavsiye edilmez.
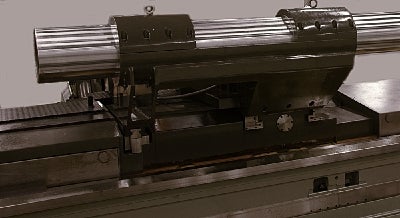
300 mm (11.81 inç) bara çapı için ayrı tutucu. Çapraz kızaklar arasındaki mesafe 1,200 mm'dir (47.24 inç) (4 x BD).
Eksen ayarı yapma takımıTüm silindirik CoroTurn SL baralarında, kesici kenarın eksen ayarını doğru yapmanın hızlı ve kolay bir yöntemi vardır:
İşleme sırasında bara hafiften eksenin altına kaysa da, baranın doğru montajı eksen çizgisi üzerindedir. Alternatif araçlar olarak yükseklik mastarı ve çapraz test kolu kullanılabilir. | ![]() | |
![]() | ||
![]() |
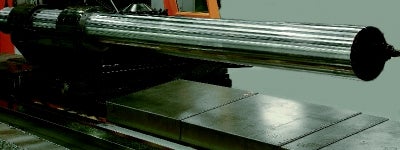
10 x BD takım taşma mesafeli, sönümlemeli 300 mm CoroTurn SL hızlı değiştirmeli delik işleme barası.
Basınç ve yön
En iyi takım ömrü ve işleme emniyeti için kesme sıvısını kesme bölgesine yönlendirin. SL hızlı değiştirme başlıkları bulunan takımlarda, kesme sıvısının kesme bölgesine yönlendirilmesini sağlamak için kesme sıvısı nozülleri manuel olarak ayarlanmalıdır. En iyi sonuçları almak için entegre kesme sıvısı teminli ve birkaç nozülü bulunan takımları kullanın. Bu, uzun takım taşma mesafelerine sahip iç çap tornalama işlemleri için de eşit öneme haizdir. Kesme sıvısı akışını açıp kapatmak için altıgen anahtar kullanın.
Delik işleme barası ile deliğin içi arasındaki mesafe, talaş tahliyesi ve radyal sapmayı önlemek için çok önemlidir. 100 mm'lik (3.94 inç) delik çapı için 80 mm'lik (3.15 inç) bara kullanılmalıdır. Böylece talaş tahliyesi için yeterli boşluk kalır ve takıma ve parçaya zarar gelmez.
İngiliz Standart Boru (BSP) dişli bağlantı parçaları ile kesme sıvısı delik işleme barasının arkasına uygulanabilir. Sandvik Coromant sönümlemeli delik işleme baralarında önceden diş açılmış kesme sıvısı giriş deliği bulunmaktadır.
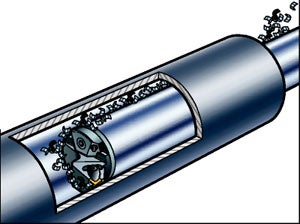
Titreşimi etkileyen etkenler
Titreşim eğilimlerini minimize etmek için;
- Büyük giriş açısı ve pozitif talaş açısı kullanın
- Büyük burun yarıçapı ve uç açısı kullanın
- Pozitif makro bir geometri kullanın
- Mikro geometride aşınma yapısını ve ER uygulamasını kontrol edin
- Kesme derinliği burun yarıçapından büyük olmalıdır.
Düşük radyal kuvvet daha az radyal sapmaya ve daha az titreşim sorununa yol açar. En iyi sonuçlar için; 90° giriş açısı (0° boşluk açısı) kullanırken burun yarıçapından büyük radyal kesme derinliği uygulayın. Radyal kesme derinliği daha küçükse 45° giriş açısıyla aynı sonuçlara ulaşabilirsiniz.
![]() | Titreşim eğilimi |
Giriş açısı | |
Kılavuz açı | |
Burun yarıçapı ve uç açısı. mm (inç) | |
Makro geometri | |
Mikro geometri | |
Burun yarıçapına bağlı kesme derinliği |
Kuvvetlerin yeniden yönlendirilmesi yer değiştirmeyi (sapmayı) azaltabilir:
- Giriş açısı 90°'ye olabildiğince yakın olursa (boşluk açısı 0°) çalışma parçasından eksenel yönde gelen ilerleme kuvveti bölümü maksimize edilir. Eksenel yöndeki kuvvet, radyal yöndeki eşit bir kuvvetten daha az takım sapmasına yol açar.
- İç çap tornalamada giriş açısı kesinlikle 75°'den (kılavuz açı 15°) daha az olmamalıdır.
- Talaş açısı ne kadar pozitifse parçayı işlemek için daha az kesme kuvveti gereklidir. Kesme kuvveti azaldığında sapma da azalır.
- Daha az radyal sapma oluşturan radyal yönde daha düşük kuvvet
![]() | ![]() | |
![]() | ![]() | |
Kuvvet yönü: genelde eksenel | Kuvvet yönü: hem eksenel hem radyal | |
![]() | ![]() | |
Negatif talaş açısı kesme kuvvetlerini arttırır | Pozitif talaş açısı kesme kuvvetlerini azaltır |
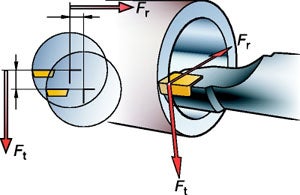
F
t
= teğetsel kuvvetler ve Fr = radyal kuvvetler
Kesici uç açısı
Giriş açısına ve takımın ulaşılabilirlik koşullarına göre bir kesici uç şekli seçin. Genel kurallardan biri, titreşim eğilimini azaltmak için en küçük burun yarıçapını seçmektir. Söz konusu uç açısı olduğunda iki yol izlenebilir:
- Küçük kesici ucu açısı, takım radyal yönde titreşime başlarsa, izleme yüzeyinde iyi bir boşluk sağlayarak ve küçük talaş alanı değişimleriyle takım kararlılığını artırır.
- Büyük kesici uç açısı, kesimde daha uzun bir kesme kenarı olduğu için, kesici uç dayanımını ve güvenilirliği arttırır, ancak daha fazla tezgah gücü gerektirir
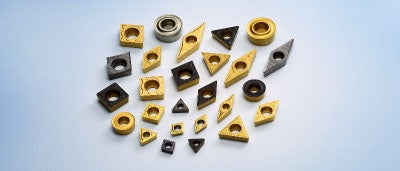
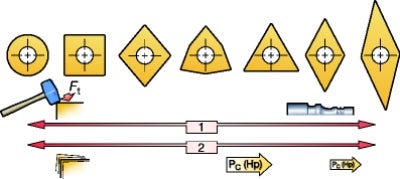
Pozitif geometriler
Pozitif geometriler ve pozitif talaş açıları daha az kesme kuvveti ve takım yer değiştirmesi (sapması) oluşturur. Dolayısıyla, kesme değerlerine uygun bir talaş kırıcıyla birlikte, olabilecek en pozitif geometriyi seçin. Bu durumda aşınma direnci, kenar güvenliği ve talaş kontrolü azalabilir, bu yüzden titreşim kontrolü her zaman bir denge unsurudur.
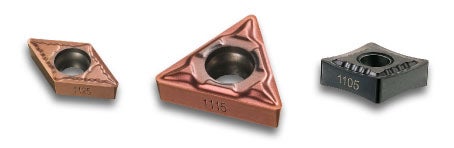
Silici (wiper) kesici uçlar
Siliciler, titreşimi önlemek söz konusu olduğunda ilk tercih değildir, çünkü yüksek kesme kuvvetlerinin ve radyal sapmanın üstesinden gelmek son derece zordur. Çok kararlı şartlarda ise silici uçlar yüzey kalitesinde ve yüksek kesme değerlerinde büyük avantajlar sunabilir.
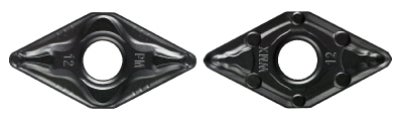
Kenar yuvarlamaKüçük kenar yuvarlama (ER) tüm yönlerde daha düşük kesme kuvvetleri sağlar. Bunun anlamı; kolay kesme etkisi ve daha az takım sapmasıdır. Taşlanmış kesici uçlar, doğrudan preslenmiş uçlardan daha küçük kenar yuvarlamasına sahiptir, aynı durum kaplanmamış veya ince kaplanmış kesici uçlar için de geçerlidir. | ![]() |
![]() | ![]() | ![]() | ||
M = Doğrudan preslenmiş kesici uçlar | G = Taşlanmış kesici uçlar, genelde daha küçük ER | E = Dar toleranslar ve keskin kenar için taşlanmış kesici uç |
Kesme değerleri
Serbest yüzey aşınması gibi aşırı kesici uç aşınması önlenmelidir, aksi takdirde takım ile parça cidarı arasındaki boşluk açısı değişebilir ve bu da titreşim sorunları yaratabilir.
![]() | ![]() |
![]() |
Kesme hızı, vc
Doğru kesme hızı, yüzey kalitesini, kesme kuvvetlerini ve takım ömrünü etkileyebilen bir yığıntı talaş (BUE) oluşumunu önler.
- Aşırı yüksek kesme hızı, özellikle derin delikler işlenirken talaş sıkışması, zayıf talaş tahliyesi ve kesici uç kırılması sebebiyle emniyeti ve güvenilirliği azaltan serbest yüzey aşınmasına yol açabilir
- Çok düşük kesme hızları yığıntı talaş (BUE) oluşumuna yol açar
- Düzensiz aşınma deseni takım ömrünü ve yüzey kalitesini düşürür, bu yüzden aşınma desenine dikkat edilmelidir
- İş parçası malzemesi, uygulayabileceğiniz kesme hızı üzerinde büyük bir etkiye sahiptir
Kesme derinliği, ap, ve ilerleme, fn
ap ve fn kombinasyonu en iyi talaş alanlarını elde etmek için önemlidir. İki genel kural:
- Programlanan ap burun yarıçapından büyük olmalıdır
- Bir fn programlaması, istenen yüzey kalitesine bağlı olarak burun yarıçapının minimum %25'i kadar olmalıdır
Uzun takım taşma mesafelerinde titreşim oluyorsa ilk olarak ilerleme artırılmalı, ikinci olaraksa kesme hızı değiştirilmelidir. Genelde daha yüksek kesme hızıyla en iyi sonuçlara ulaşılır.
Talaş alanı
- Talaş alanı çok büyük olursa kesme kuvveti de çok büyük olur
- Talaş alanı çok küçük olursa takım ile çalışma parçası arasındaki sürtünme çok büyük olur ve bir ovma etkisine yol açabilir
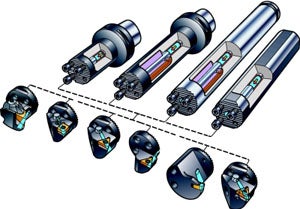
İp uçları ve tavsiyeler
Olabilecek en büyük bara çapıyla en küçük kullanma mesafesini seçerek titreşim riskini düşürün. Önerilen bağlama uzunluğu olan minimum 4 x BD'yi kullanın.
10 x BD üzeri CR delik işleme baralarının kesilmesine müsaade edilmez. 570-4C baralarda sönümleme mekanizması üstünde bağlama yapılabilir, ancak bu işlem 3C baralarda yapılamaz. 570-3C kısa tasarımlı bara minimum uzunluğa kesildiğinde, sönümleme mekanizması üzerine bağlamayı önlemek için bağlama uzunluğu 3 x BD'yi geçmemelidir. 570-3C baraları >100mm (3.94 inç) çapta kesinlikle kesmeyin.
Standart baralarda modifikasyon
Bara çapı | L, kesme sonrası minimum uzunluk | |
BD | Kısa tasarım 4–7 × BD | Uzun tasarım 7–10 × BD |
mm | mm | mm |
16 | 100 | 155 |
20 | 125 | 200 |
25 | 155 | 255 |
32 | 190 | 320 |
40 | 240 | 410 |
50 | 305 | 520 |
60 | 380 | 630 |
80 | 630 | 630 |
100 | 770 | 770 |
Minimum 4 x BD bağlama uzunluğu önerilmektedir
Bara çapı | L, kesme sonrası minimum uzunluk | |
BD | Kısa tasarım 4–7 × BD | Uzun tasarım 7–10 × BD |
inç | inç | inç |
0.625 | 4 | 7 |
0.750 | 5 | 8 |
1.000 | 7 | 11 |
1.250 | 8 | 13 |
1.500 | 10 | 17 |
1.750 | 10.4 | 18 |
2.000 | 12 | 21 |
2.500 | 15 | 25 |
3.000 | 20 | 20 |
4.000 | 30.3 | 30.3 |
Minimum 4 x BD bağlama uzunluğu önerilmektedir
Baradaki iki çizgi minimum ve maksimum kullanma mesafelerini gösterir. Takım taşma mesafesi bu aralıkta olmalıdır. Bu aralığın dışına çıkıldığında sönümleme fonksiyonu çalışmayabilir.
Talaş tahliyesi
En iyi talaş tahliyesi için kısa ve spiral talaşlar bırakan entegre kesme sıvısı ve kesici uç geometrisi bulunan bir takım tutucu kullanın. Kötü talaş tahliyesi durumunda; daha kısa talaşlar elde etmek için; kesme sıvısı debisini artırın, kesici uç geometrisini değiştirin ya da kesme hızını yükseltin.
Bir başka alternatif de başka bir takım yolu seçmektir. Baş aşağı
kesme üniteleri talaş tahliyesinin iyileşmesini önler.
Bara ile delik arasında talaşlar için yeterli boşluk olduğundan emin olun. Aksi takdirde, takım talaşları yüzeye ittirerek takım gövdesine hasar verebilir.
![]() | ![]() |
Nozül ayarı
Kesme sıvısı akışını açıp kapatmak için altıgen anahtar kullanın. SL Quick Change başlıklarında nozül yönünü ayarlamak için aynı altıgen anahtarı kullanın.
Silici (wiper) kesici uçlar
Daha iyi yüzey kalitesi ve daha yüksek verimlilik için çok kararlı şartlarda silici (wiper) kesici uçlar optimize edici olabilir.Silici (wiper) kesici uçlar kullanılırken ilerleme artırılmalı ve küçük bir burun yarıçapı kullanılmalıdır.
İç çapa diş çekme
Titreşim riskini azaltmak için aşağıdakileri uygulayın:
- Modifiyeli yanal ilerleme kullanın
- Paso başına ilerleme 0,2 mm'yi (0.0078 inç) geçmemeli ve 0,06 mm'den (0.0024 inç) düşük olmamalıdır
- Son paso daima düşük ilerleme hızıyla yapılmalıdır
- En düşük kesme kuvvetleri için keskin geometri kullanın
En iyi talaş tahliyesi için;
- Spiral talaşları deliğin açık tarafına yönlendirmek için modifiyeli yanal ilerleme kullanın
- Kararlı şartlarda içten dışa doğru ilerleme yönü uygulayın. Talaş akışı yönünü değiştirmek için sol veya sağ yanal yüzeyi seçin
- En iyi talaş tahliyesi için kesme sıvısı kullanın
Talaş yönü | İlerleme yönü | ||
![]() | ![]() | ||
İlerleme yönü içeriden dışarıya olmalıdır | Modifiyeli yanal ilerleme talaşları delikten dışarı yönlendirir |
İç çap kanal açma ve profil işleme
Titreşim riskini azaltmak için aşağıdakileri uygulayın:
- Mümkün olan en hafif kesme geometrisyle mümkün olan en kısa takım taşma mesafeli kurulum kullanılmalıdır
- Küçük bir kesici uç kullanın ve bir kesim yerine birkaç kesim yapın
- En iyi talaş tahliyesi çin dışarıdan başlayın ve üst üste binen kesimler yapın
- İnce talaş işlemi bir yan tornalama şeklinde yapılabilir. İçeriden
başlayıp dışarıya doğru dönün - Yüksek talaş kontrolü için tırmanarak tornalama yöntemi uygulanabilir ve böylece titreşim azaltılabilir
- Kaba talaş işlemi sırasında talaşları yönlendirmek için sağ kesme yönlü veya sol kesme yönlü tipte kesici uçlar kullanın
Yaygın kurulum
Baranın klasik şekilde kullanılması, kesici ucu aşağı iten kesme kuvvetleri yaratır.
Alternatif kurulum
Baranın yukarıdan aşağı kullanılması, kesme kuvvetlerinin yönünü değiştirir ve kararlılığı artırır. Bu aynı zamanda talaş tahliyesini de iyileştirilebilir. Küçük çaplarda bile, bu yöntem kullanılırken dikkatli olunmalıdır. Kesme kuvveti kesintili işleme yüzünden 0'a düşerse bara dönme yönünde iş parçasına çarpar ve daha büyük bir kesme kuvvetiyle hem takıma hem de parçaya zarar verebilir.
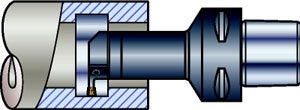
Bakım
En iyi performans için tüm parçaları yılda en az bir kere temizleyin ve yağlayın. Gerektiğinde vidalar da yağlanmalıdır. Aşınmış ve bozulmuş vidaları ve rondelaları değiştirin.
Sönümlemeli baralar, ince cidar kalınlığı sebebiyle deforme olabilir. Montaj sırasında baraları doğru tutun. Silent Tools ürünleriyle çalışırken bağlamayı daima kontrol edin. Vidaları doğru sıkmak için tork anahtarı kullanın.
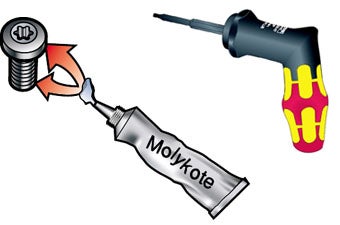
Özet: Titreşim nasıl önlenir?
Statik katılığı arttırın
- Bağlamayı ve kurulumu kontrol edin
- Coromant Capto veya yarıklı tutucu kullanın
- Minimum takım taşma mesafesi ve maksimum çap
- Malzeme takviyesi (delik işleme baraları)
Dinamik katılığı artırın
- Düşük kesici uç açısı
- Sönümlemeli takımlar kullanın
- Kesici takımının ön tarafında olabildiğince az ağırlık
Kesme kuvvetlerini azaltın
- Pozitif bir kesme açısı kullanın
- Küçük ER'li pozitif kesici uç geometrisi kullanın
Sapmayı önleyin
- Kesme kuvvetinin yönünü radyalden eksenele çevirin
- 90°'ye yakın giriş açısı (boşluk açısı 0°)
- Burun yarıçapından daha büyük kesme derinliği
Talaş kontrolü sağlayın
- Kesme sıvısı debisini arttırın
- Takım ile iş parçası arasında boşluk bırakın
- Tüm talaşların boşaltıldığını kontrol edin
Not!
Sönümlemeli delik işleme barasına aşırı yük uygulamayın. Maksimum yük ürünlerde işaretlenmiştir ve maksimum yükü belirlemek için www.sandvik.coromant.com/calculators adresindeki hesap makinesini de kullanabilirsiniz.