Solutions for productive aluminium machining in the automotive industry
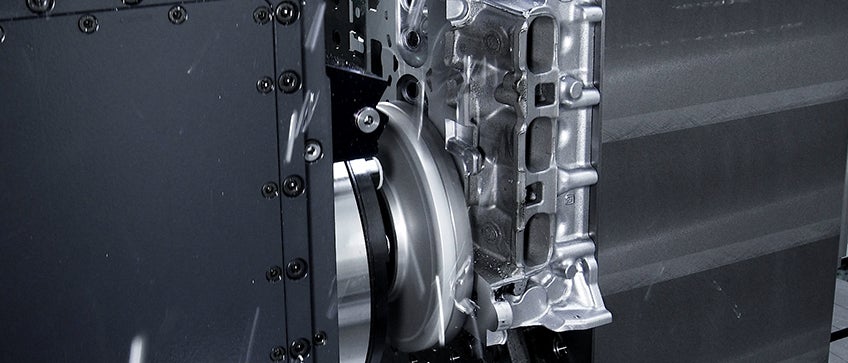
The automotive sector is increasing its use of aluminium engine, powertrain, water pump and brake system parts. The challenge for original equipment manufacturers (OEMs) and their supply chain partners is to deliver more productive milling operations. Because the correct application of optimized milling cutters across the entire range of engine component machining operations can pay significant dividends, tooling selection is key to genuine market differentiation in this segment. Here Emmanuel David, global product manager engineered solutions automotive aluminium at Sandvik Coromant explains.
The move towards lightweight materials has seen a growth in the popularity of aluminium in the automotive industry. In fact, the amount of aluminium in an average car has increased from 50 kilograms (kg) in 1990 to 151 kg in 2019. Predictions for 2025 suggest this could rise to 196 kg, according to European Aluminium.
To meet rising demand, Sandvik Coromant now has a complete offering for machining aluminium in the automotive industry, from first-stage cubing, through roughing, semi-finishing and finishing. Each engineered milling tool, five in total, is designed to deliver optimized quality and cost per part. To help achieve the latter, certain tools in the range fulfil a combination of tasks, such as performing both roughing and finishing in a single operation to reduce cycle times.
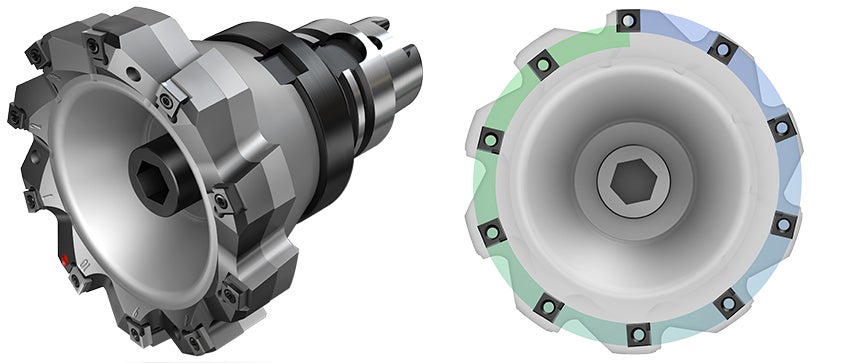
One example is the M5B90 super-finishing face mill with its unique axial and radial positioning of inserts. This configuration, together with the wiper insert, ensures burr-free cutting with excellent surface quality. This is because the model comes with an extra row of inserts tangentially positioned on the outer diameter, resulting in higher feed rates reducing process time.
One of the key applications where a M5B90 is critical is in the manufacture of cylinder heads for passenger cars. These are important components because they seal the top of the cylinder to create the combustion chamber. Furthermore, the cylinder head also houses the valve gear and spark plugs.
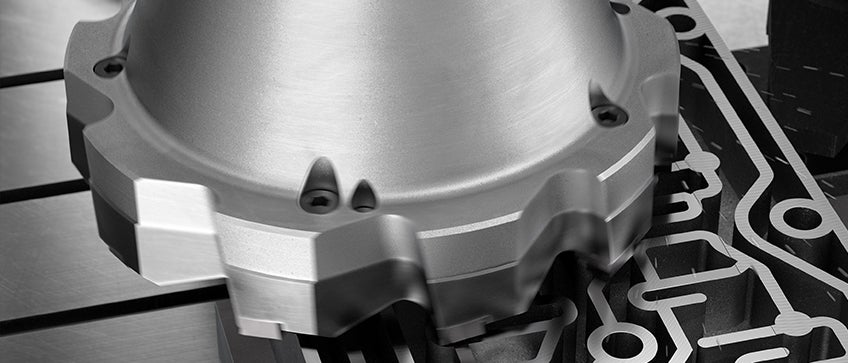
Due to the precision of the operation, many producers suffer from process instability, issues with burrs and unpredictable insert life. Most cutters for this procedure require constant cartridge adjustments that differ from set-up to set-up. Switching to the M5B90 cutter provides a smooth finishing operation with predictable wear and no burr. The tool produces only very thin chips, which are easily removed during the cutting process to avoid any damage to the component face. In addition, changing to M5B90 can extend tool life from 30,000 to 45,000 parts on average.
In all cases, the potential to reduce cycle times and cost per part, while at the same time improving tool life and quality, is very real. In the automotive industry, where high-volume production is prevalent, even a small saving in cycle time can equate to significant financial returns. With this thought in mind, any technology that can demonstrate the ability to deliver larger gains, is difficult to ignore.