Ask the expert – aluminium machining
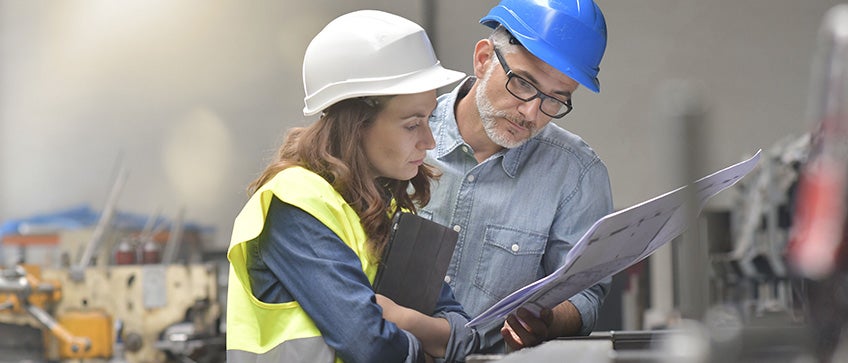
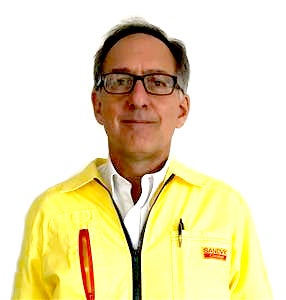
Brent Marsh
Questions with Brent Marsh
Sandvik Coromant’s Automotive Machining Specialist discusses the challenges of working in aluminum and how proper tooling can help.
1) For high-volume aluminum engine blocks and power-trains, what are some best practices to speed production while meeting quality specs?
Reliable, accurate, high-speed tooling solutions are mandatory, and the tooling supplier must offer the best selection of standard tools for aluminum machining and be able to provide custom solutions for automotive component production.
Best practices are using the most advanced polycrystalline diamond (PCD) solutions; accurate, balanceable tools and holders; minimum quantity lubrication (MQL); feed-out solutions; bi-metal capability for cast-in ferrous metal requirements; and digital solutions for tool-data monitoring.
2) You offer several specialized solutions for cylinder boring and cylinder-head machining. What advantages come from these engineered solutions?
Sandvik Coromant has designed and produced tools that do one-shot boring from rough to finish; we have dampened solutions; and we even have developed coolant-actuated feed-out tools. Our designs allow for flexible application of multiple step boring inserts.
Finishing can be coupled with post-process gaging to feed data to the machine controller, instructing the spindle to place an element on the end of the tool and turn the tool slightly. This precisely adjusts the cutting diameter to automatically compensate for tool wear.
Our engineers also work with machine tool builders to implement programmable drawbar actuated tools, as many builders now offer such technology through their custom spindle interfaces. We can also offer a wide variety of cylinder head valve guide and seat tools.
3) Can producers eliminate aluminum machining processes to reduce cycle times and costs?
Sandvik Coromant solutions for aluminum include unique, patented cutter designs that make trouble-free, accurate, burr-free milling possible. These designs combine axial and radial step insert placement and high-feed milling technology. For example, our M5C90 cutter offers rough and finish milling in one pass – in many cases up to 6.0mm axial depth. We have seen tool life extended 5x with 200% cycle time reduction. Speeds as high as 6,000m/min. and feed rates as high as 20,000mm/min. are possible.
For complex surfaces such as transmission valve body faces, we can eliminate costly secondary process deburring with the M5F90. It also uses step technology with precise, long-lasting, brazed-in PCD tips.
The step technology in our M5-B-, C-, and F-series of cutters allows each cutting edge to progressively remove a bit more material – axially and radially – similar to a broach but in a circular configuration. The last tooth is a wiper design that provides superior finish and flatness. It also eliminates complex and time-consuming pre-setting procedures because the wiper and teeth are fixed.
We also have a unique CBN cutter, M610, that will finish the top deck of a cylinder block or bed plates, both aluminum cast-in iron materials. It requires no setup and no adjustment, and results in high feed rates without chipping, burring, or scratching on the parts.