Overcoming the e-mobility manufacturing challenges
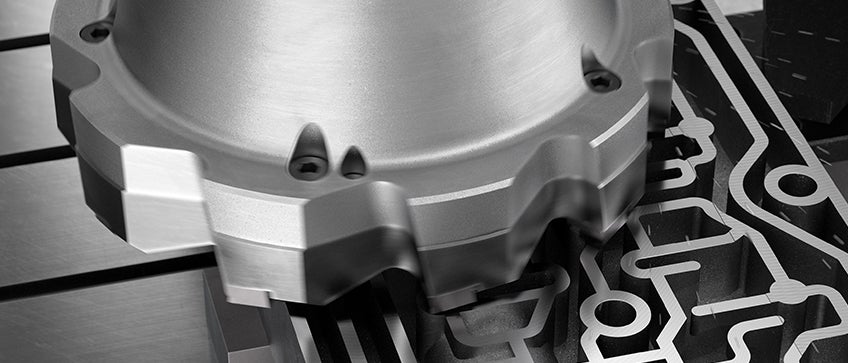
Manufacturers must adapt to more sustainable manufacturing and production. In automotive, this means machining components for different types of electric vehicles (EVs) with tough materials like aluminium. But EV designs are more varied than people realise, with fully-electric, different hybrid and battery-powered systems all set to grow in popularity.
Expectations for new low and zero-emission automobiles are constantly rising. For instance, the European Legislation roadmap aims to reduce the average grams of carbon dioxide per kilometre (g/km) produced by vehicles by half by 2025 — compared to the acceptable limit in 2015.
The introduction of EVs and hybrid vehicles has been a great step in reducing global emissions, but manufacturing components for electric vehicles is not as easy. Manufacturers must ensure the vehicles are lightweight enough to improve efficiency.
That means using lightweight metals like aluminium. What’s more, original equipment manufacturers (OEMs) must sustainably produce these components for a range of EV designs — including fully-electric, hybrids that use both combustion engine and electric motors and battery electric vehicles.
“Electric mobility or e-mobility is more diverse than just pure electric motor-powered vehicles, and the variety means different components present their own machining challenges,” said Fernando Oliveira, Aluminium Automotive sales manager at Sandvik Coromant. “Engine designs for EVs will be less-uniform than today’s combustion engine models.”
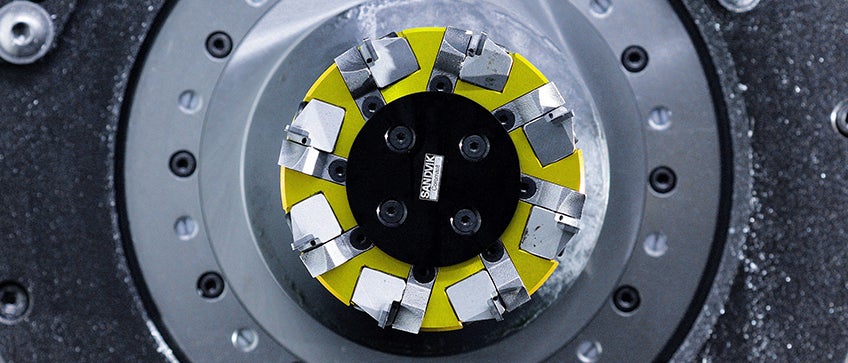
The M5R90 is a roughing and semi-finishing concept for shoulder milling operations
That’s why Sandvik Coromant has developed its M5 range of dedicated milling cutters for automotive aluminium components. While each tool benefits various machining operations, depending on the application, the tools are customised for thin wall machining of aluminium with minimal burring, scratching and chipping — something that’s is often unavoidable with conventional milling cutters.
The M5 family comprises milling cutters with unique axial and radial positioning for easier machining of aluminium. The M5Q90 is a cubing cutter to clean the surfaces of newly casted aluminium components. The M5R90 is a roughing and semi-finishing concept for shoulder milling operations. M5B90 face milling concept is a highly-effective milling cutter for super finishing cylinder heads, blocks and other aluminium components with wide cutting engagements.
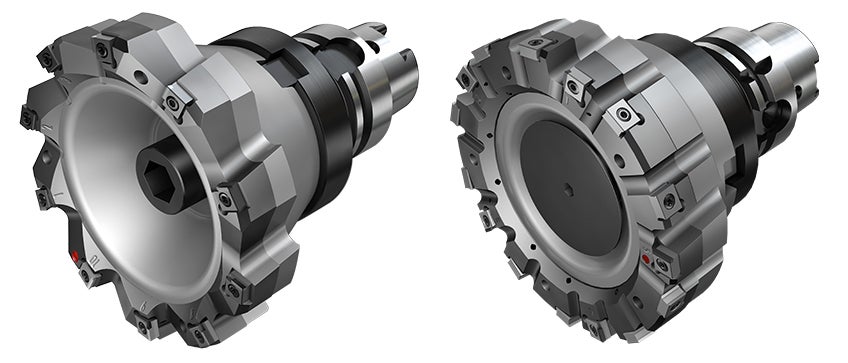
M5 family cutters M5B90 (left) and M5C90 (right)
The M5C90 offers smooth cutting actions free of burrs, scratches and breakages with indexable inserts in a stepped configuration, which enables roughing and finishing operations in one operation. Finally, the M5F90 is a dedicated face milling cutter for machining thin-walled aluminum components in a single operation.
By using M5 milling cutters, customers have realized dramatically improved tool life and productivity increases which has led to a substantial reduction in cost per part.
E-mobility is paving the way for a greener future, with tools like the M5 range, this is achieved with greater productivity, improved quality and reduced tool wear.