Hoe hebben we deze gemaakt?
Hoe Sandvik 's werelds eerste 3D-geprinte, smash-bestendige gitaar maakt
Rocksterren verbrijzelen al decennia lang gitaren, maar slechts weinigen met meer enthousiasme dan de in Zweden geboren gitaarvirtuoos Yngwie Malmsteen. Sandvik besloot om hun geavanceerde technieken te testen en 's werelds eerste volledig metalen, onbreekbare gitaar te bouwen en Malmsteen zijn verbrijzelingsvaardigheden er op los te laten.
Sandvik bracht experts uit het hele bedrijf bij elkaar om aan te tonen hoe haar ingenieurs duurzame, geavanceerde technieken konden gebruiken om iets te maken dat zowel uiterst precies is als een verbazingwekkende levensduur heeft.
“Geavanceerde materialen, precisie-bewerking, additieve productie, data-gedreven productie — dat is het soort processen dat nodig is om iets te maken dat zo complex en mooi is als een gitaar voor een topmuzikant ,” zegt Klas Forsström, President van Sandvik Machining Solutions. “Maar we wilden ook aantonen dat we deze onbreekbaar konden maken, ongeacht hoe hard Yngwie probeerde deze kapot te slaan. Het project leek een perfecte match voor onze vaardigheden en capaciteiten — en voor die van hem.”
Samenwerking vanaf het begin
Maanden voor het Florida concert, terug in Zweden, verzamelde Sandvik experts op het gebied van materialen, bewerkingsprocessen en additieve productie uit het hele bedrijf om te brainstormen over manieren om de uitdaging aan te gaan.
Omdat Sandvik nog nooit eerder een gitaar had gemaakt, werkte het bedrijf samen met de gerenommeerde gitaarbouwer Drewman Guitars uit het VK. “We moesten top down innoveren,” zei Drewman ontwerper Andy Holt. “We wilden dat muzikanten zouden zeggen, ‘Ik heb nog nooit een gitaar gezien die zo gemaakt zoals deze.’”
Holt zei dat er een periode was tijdens het ontwikkelingsproces waar hij ingenieurs bij Sandvik elke dag een nieuw digitaal ontwerp stuurde. In nauwe samenwerking met de gitaarbouwer ontwierpen zij wat uiteindelijk, zoals beide van mening waren, een meesterstuk op het gebied van technologische creativiteit was.
's Werelds eerste smash-proof gitaar
Henrik Loikkanen, bewerkingsproces-ingenieur bij Sandvik Coromant, speelt al gitaar sinds zijn jeugd toen hij Malmsteen als idool had. Maar hij had nog nooit een gitaar stukgeslagen (“te duur,” zei Loikkanen). Dus om te begrijpen wat er gebeurt wanneer Malmsteen een instrument vernietigd, stak Loikkanen zijn licht op bij YouTube.
“We moesten een gitaar ontwerpen die niet stuk te slaan is op alle verschillende manieren waarop je een gitaar kunt kapotslaan,” zei Loikkanen. “De ontwerp-uitdaging zat hem in de kritische verbinding tussen de hals en de body welke het meestal begeeft bij een gitaar.” Dus besloten Sandvik Coromant ingenieurs deze verbinding te elimineren. Zowel de hals als het fretboard zijn verlengd tot in een rechthoekige “naaf” die diep in de body van de gitaar ligt.
Omdat een gegolfd fretboard Yngwie in staat stelt noten beter te beheersen, moesten ingenieurs materiaal verwijderen in lange, soepele bogen tussen de frets. Om de gitaar zo licht mogelijk te maken, holde Sandvik Coromant de binnenoppervlakken van de hals en het fretboard uit.
“De hoogte van elke fret moest perfect uitgelijnd worden, anders konden we horen dat de snaren sommige van de frets zouden aanraken,” zei Loikkanen.
Gegevens over de snijkant
Lange, slanke componenten zoals het fretboard en hals zijn met name gevoelig voor vervorming in het bewerkingsproces. Geavanceerde software stelde Sandvik Coromant in staat de taak digitaal te simuleren voordat de eerste snede werd gemaakt.
“Precisie was cruciaal,” zei Henrik Loikkanen. “Onze software is gebouwd op jaren ervaring. Het biedt het soort gereedschap en snijgegevensaanbevelingen die ons hebben geholpen het fretboard te frezen tot een uitdagende dikte van één millimeter op sommige plekken."
Het geautomatiseerde proces betekende ook dat het fretboard in slechts één machine gefreesd kon worden. Het proces benodigde 90 afzonderlijke bewerkingen en werd afgerond zonder de machines te stoppen of nieuwe gereedschappen en snedes in te stellen.
“Je plaatst er een onbewerkt stuk materiaal in en een afgewerkt onderdeel komt er uit,” zei Loikkanen. “Het is een intelligentere manier om materiaal te verwijderen. Je kunt de cyclustijd reduceren en componenten produceren tegen lager kosten.”
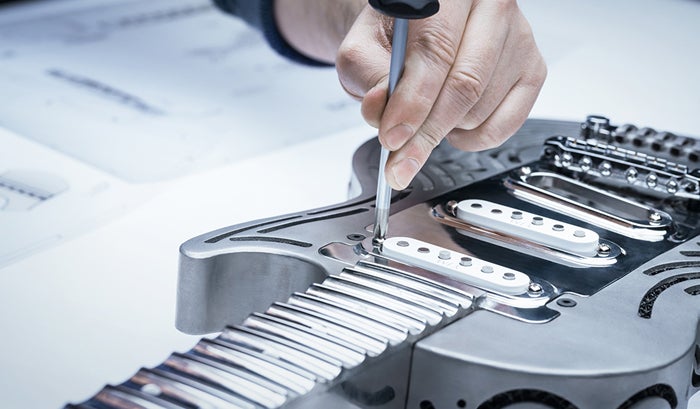
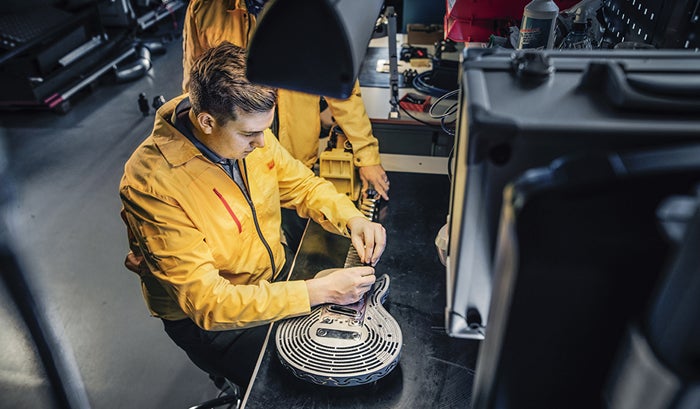
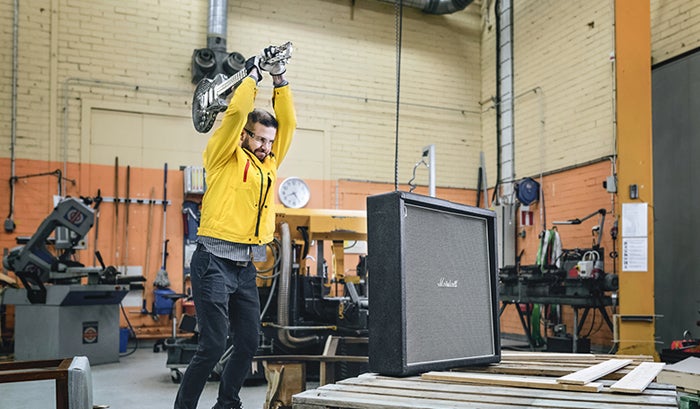
Ingenieurs waren in staat elk prototype lichter te maken dan de voorgaande versie, tot de uiteindelijke gitaar werd geproduceerd. CoroMill® nabewerkings-snijgereedschappen werkten het metaal af in prachtige gladde en glimmende oppervlakken.
Loikkanen zei dat samenwerking met andere Sandvik divisies van essentieel belang was bij het produceren van de smash-proof gitaar. Hij kon Sandvik Additive Manufacturing helpen bij de afwerking van de gitaarbody en kleine componenten, die alle 3D werden geprint van titanium. Sandvik Coromant werkte ook samen met Sandvik Materials Technology voor het selecteren van het componentstaal en het opnemen van een hyper-duplex rasterstructuur binnenin de hals. Dat teamwork, zei hij, was het echte doel van het maken van de gitaar.
“Sandvik Coromant staat er om bekend klanten te helpen bij complexe taken — niet slechts door het bieden van gereedschappen, maar ook bij het helpen van het ontwikkelen van de beste methoden voor het gebruik van onze gereedschappen in hun processen,” zei Loikkanen.