Irregular surface drilling
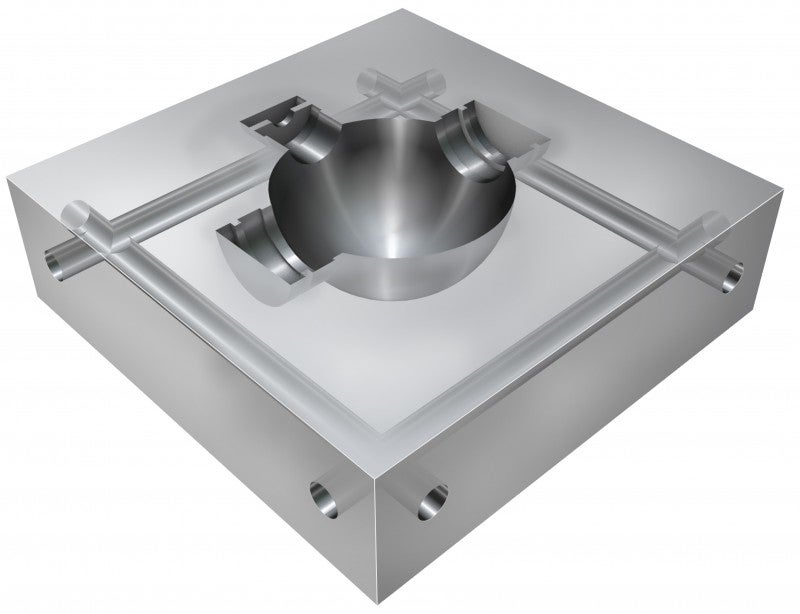
Drilling irregular surfaces can lead to excessive, uneven forces on drill cutting edges, which leads to premature wear. It is important to follow the guidelines and reduce feed when necessary.
Learn more about the challenges and strategies for each drill type.
Indexable insert drills
Irregular surface drilling
Irregular
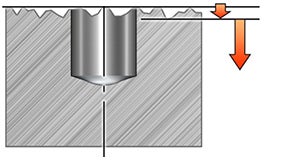
Convex
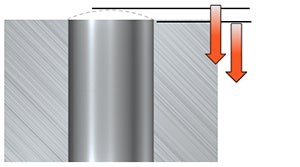
Concave
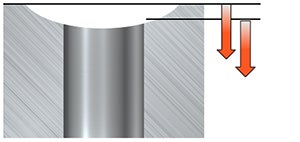
- Use shortest drill possible to minimize vibration tendencies and decrease the effects of deflection
- Recommended start values for cutting speed and lowest recommended feed
- Not recommended for 6–7×DC when concave radius is same or smaller than drill radius
Pre-drilled holes
- To keep the cutting force balanced between the central and peripheral insert on an acceptable level, the pre-drilled hole should not be larger than DC/4
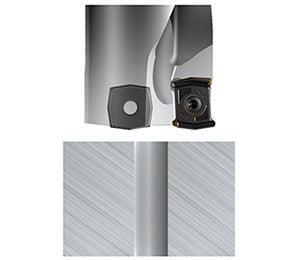
Cross hole drilling
Challenges:
- Chip evacuation is affected, might become more problematic
- Deburring in the crossing is hard. Burr formation must be as small as possible
- Causes more tool wear than conventional drilling
Guidelines:
- For holes with different diameter: drill the larger hole first to reduce burr formation
- Start with lowest recommended feed during the crossing of holes
- Not recommended in long-chipping materials due to chip evacuation while crossing holes
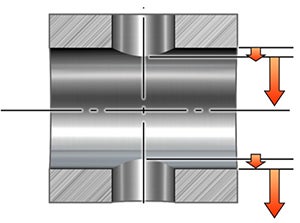
Drilling inclined entrances/exits
Generates uneven and excessive forces acting on the cutting edges
- Intermittent cutting as the drill enters/exits the workpiece
- Increases chance of vibration
- Can distort the drilling profile
- Causes more tool wear than conventional drilling
General recommendations:
- Stability is crucial. A small length to diameter ratio will help to keep the tolerances
- Milling a small flat surface is recommended when entering workpieces with a large inclination
Angled or inclined surfaces, entry
- Use shortest drill possible to minimize vibration tendencies and decrease the effects of deflection
- Start with lowest recommended cutting speed and 1/3 of lowest recommended feed (or lower) until fully engaged and then return to normal feed
- 4–5×DC the inclined entry can be angled up to 15º
- 6–7×DC the inclined entry can be angled up to 10º
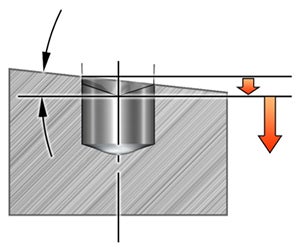
Angled or inclined surfaces, exit
- Use shortest drill possible to minimize vibration tendencies and decrease the effects of deflection
- Recommended start values for cutting speed and lowest recommended feed (or lower)
- 4–5×DC the inclined exit can be angled up to 15º
- 6–7×DC the inclined exit can be angled up to 5º
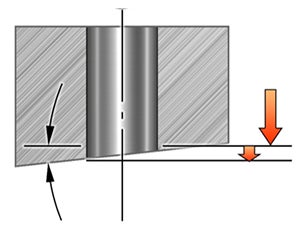
Drilling asymmetrically curved surfaces
- Use shortest drill possible to minimize the drill bending outwards from the center, similar to an inclined surface
- Reduce feed to 1/3 of the initial penetration rate for a concave surfaces
- Radius of curved surface should be bigger than drill radius
- Not recommended for 6–7×DC drills
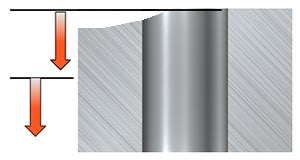
Exhangeable-tip drills
Irregular surfaces
- Reduce feed rate to ¼ of normal rate to avoid chipping
- If unstable conditions, make a pilot hole (preferably with short CoroDrill® 870) or spot-mill to create a flat surface
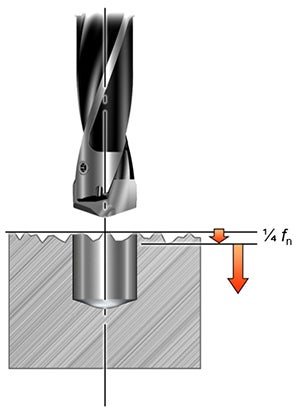
Convex/Concave surfaces
Convex
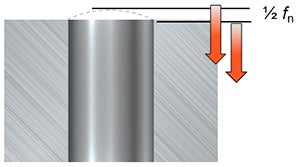
Concave
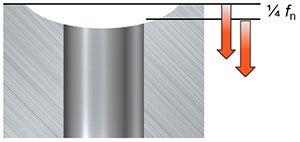
- The hole must be perpendicular to the surface
- Min. recommended radius of surface
- Convex: 4×DC
- Concave: 1×DC
- Ensure stable conditions and use shortest possible drill
- Reduce feed during entrance
- Convex: ½ of normal rate
- Concave: ¼ of normal rate
- Hole quality and tool life could be affected compared with favourable conditions
- Make a pilot hole or spot-mill to create a flat surface if radius is smaller than recommended
Pre-drilled holes
- Not recommended due to risk of chipping on cutting edge
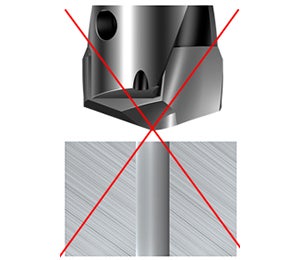
Cross hole drilling
Challenges:
- Chip evacuation is affected, might become more problematic
- Deburring in the crossing is hard. Burr formation must be as small as possible
- Causes more tool wear than conventional drilling
Guidelines:
- Always drill the larger hole first in order to minimize internal burr formation
- Min. recommended diameter on the hole to be crossed is 2×DC (to ensure that the centre of the tip enters the workpiece first)
- Ensure stable conditions and use shortest possible drill
- Reduce feed to ¼ of during entrance and exit of holes
- Reduce retract feed
- Hole quality and tool life could be affected compared to favourable conditions
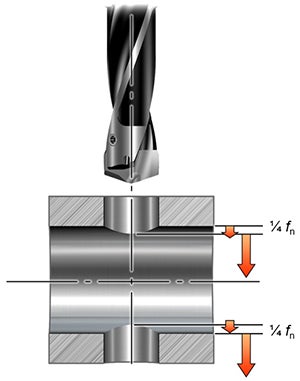
Drilling inclined entrances/exits
Generates uneven and excessive forces acting on the cutting edges
- Intermittent cutting as the drill enters/exits the workpiece
- Increases chance of vibration
- Can distort the drilling profile
- Causes more tool wear than conventional drilling
Angled or inclined surfaces, entry
- Maximum recommended angle from centre to corner is 6 degrees to ensure the tip enters the workpiece first
- Ensure stable conditions and use shortest possible drill
- Reduce feed to 1/3 of normal rate during entrance
- Make a pilot hole (preferably with short CoroDrill® 870) or spot-mill to create a flat surface if larger angle or longer lengths
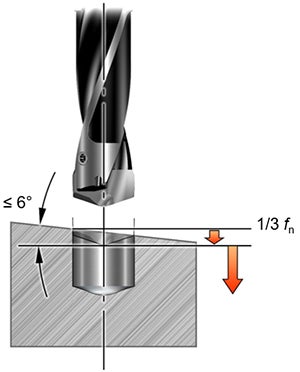
Angled or inclined surfaces, exit
- Maximum recommended angle is 30 degrees
- Ensure stable conditions and use shortest possible drill
- Reduce feed to 1/3 of normal rate during hole exit
- Reduce retract feed
- Hole quality and tool life could be affected compared with favourable conditions
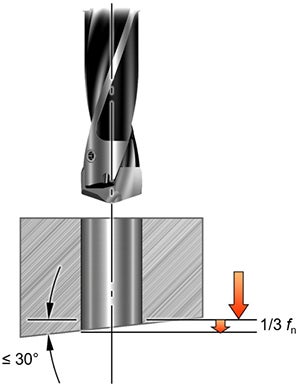
Drilling asymmetrically curved surfaces
Causes the drill to bend away from the centre line of the hole
- Initially only the periphery of the cutting edge is in contact
- Similar but not identical to inclined surfaces
- Maximum recommended angle from centre to corner is 6 degrees
- Stable conditions
- Use shortest possible drill
- Reduce feed to of normal rate during entrance
- Hole quality and tool life could be diminished compared to drilling in favourable conditions
- Make a pilot hole or spot-mill to create a flat surface if there is a larger angle or longer length
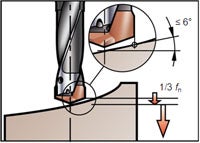
Solid carbide drills
Irregular surfaces
- Can damage drill when penetrating the surface and/or exiting the hole
- Pay special attention for small diameter drills, deflection may occur causing miss-alignment, hole wander and even tool breakage
- Reduce feed to 25% of recommended rate until full diameter is in cut to reduce risk of chipping
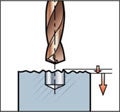
Convex surfaces
- Possible to drill if radius is > 4 times drill diameter and the hole is perpendicular to the radius
- Feed: 50–100% of recommended rate until full diameter is in cut
- Alternatively, mill a small flat on the surface before drilling
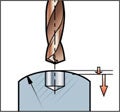
Concave surfaces
- Possible to drill if radius is >15 times drill diameter and the hole is perpendicular to the radius
- Reduce feed to 30% of recommended rate until full diameter is in cut
- Alternatively, mill a small flat on the surface before drilling
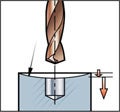
Pre-drilled holes
- Not recommended due to risk of chipping on cutting edge
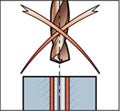
Cross hole drilling
Challenges:
- Chip evacuation is affected, might become more problematic
- Deburring in the crossing is hard. Burr formation must be as small as possible
- Causes more tool wear than conventional drilling
General guidelines:
- Feed reduction is generally necessary as the drill crosses the existing hole
- For holes with different diameters: drill the largest hole first to reduce burr formation
- For drilling depths below 12×D, reduce feed to 25% of recommended rate when crossing the existing hole
- For holes with different diameters: drill the larger hole first to reduce burr formation
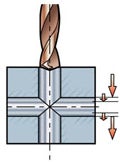
Drilling inclined entrances/exits
Generates uneven and excessive forces acting on the cutting edges
- Intermittent cutting as the drill enters/exits the workpiece
- Increases chance of vibration
- Can distort the drilling profile
- Causes more tool wear than conventional drilling
General recommendations:
- Stability is crucial. A small length to diameter ratio will help to keep the tolerances
- Milling a small flat surface is recommended when entering workpieces with a large inclination
- Inclinations up to 10 degrees
- Reduce feed to 30% of recommended rate until full diameter is in cut
- Inclinations of more than 10 degrees
- Not recommended for drilling
- Alternative for large inclinations – mill a small flat surface, then drill the hole
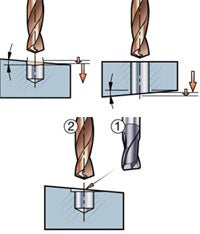
Drilling asymmetrically curved surfaces
- Cannot be used - only parts of the cutting edge will cut and the tip may not contact the surface first
- High risk of chipping
Related information
Boring with indexable drills
Indexable insert drills can be used in boring operations in order to save tool changing... keyboard_arrow_right
Troubleshooting
Milling troubleshooting tips about vibration issues, chip jamming, re-cutting of... keyboard_arrow_right
Circular ramping
What is circular ramping with indexable insert drills? A rotating tool makes a hole... keyboard_arrow_right
Internal grooving
Long overhangs and poor chip evacuation are two of the challenges with internal grooving.... keyboard_arrow_right