Heat exchanger
The conversion of fossil energy carriers to electricity takes place via a power plant. These plants burn coal and oil – as well as biomass and wood as alternative sources of energy – to produce hot steam. In these boiler systems, smooth-tube or finned tube heat exchangers serve as air pre-heaters. Heat exchangers are also found in oil and gas, as well as nuclear industry.
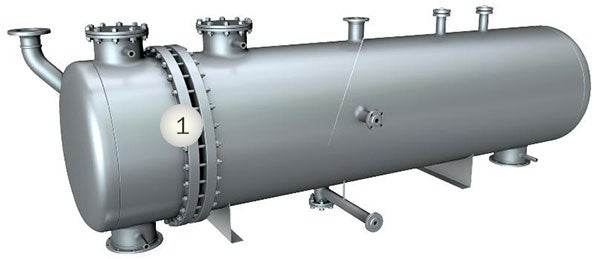
1. Heat exchanger plate
Heat exchanger plates
The nuclear heat exchangers are operating on a high pressure which means that the heat exchanger plate (HEP) thickness is around 600 – 800 mm (23.622 –31.496 inch). The material used for these applications is a combination of low carbon steel and ISO S cladding or low carbon steel and stainless cladding.
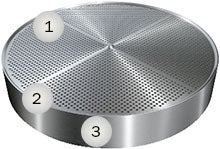
2. Short hole drilling with
CoroDrill® 870
3. CoroTurn® 107 and T-Max® P
Short hole drilling
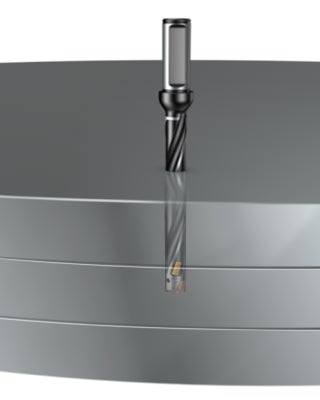
The short hole drilling process in heat exchangers is used for the support of the tubes on the vessel side. These support plates are around 30 mm (1.181 inch) thick. The drilling is normally done as stack drilling. The most common material is stainless steel due to a strong corrosion resistance needed.
For this type of operation we recommend ®CoroDrill 870.
Learn more about general drilling here.
Machining challenges
- Reliable process
- Maximum number of plates in stack
- Poor tool life
®Solution with CoroDrill 870
- Reliable and secure process
- Easy handling and secure tip changing
- Optimized chip control and evacuation
- Long predictable tool life and high productivity
- Low cost per hole and excellent hole quality
Heavy turning
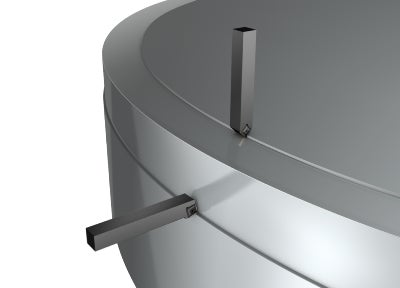
A typical heavy turning application is turning of large components with uneven surfaces in combination with very large and varying cutting depth. It is performed in order to remove the forging or casting skin and other defects from the components surface. Wtih the clean surface the component is ready for further processing.
For this type of operations, we recommend using bot ®T-Max P and ®CoroTurn 107 with positive and negative inserts.
Learn more about heavy turning here.
Machining challenges
- Reliable process
- Maximum number of plates in stack
- Good tool life
Solution with T-Max®
P and CoroTurn 107
®
- Reliable and secure machining, even in roughing applications
- Full range of clamping and coolant systems for all materials and applications
- Possibility to optimize by using dampened tools
CoroDrill® DE10
For high-volume hole making across all industries Typical components are heat exchanger... chevron_right
Stack drilling
What is stack drilling? Stack drilling is a method used for drilling a large number... chevron_right
Blisk
Blisks located on the cold compressor side of the engine are made of titanium, while... chevron_right
Tubing hanger
A tubing hanger is a component used in the completion of oil and gas production wells.... chevron_right