Crankshaft solutions
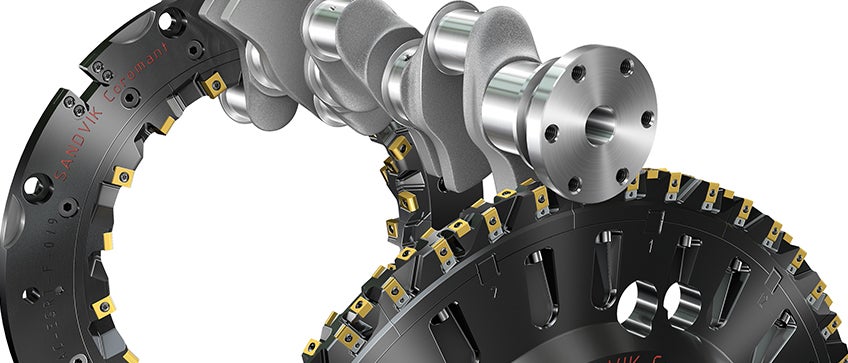
Sandvik Coromant has an extensive and complete offer for crankshaft machining and have been a providing solutions for the main OEM's and MTM's around the globe for over 40 years.
We can provide a number of different engineered solutions, see below for some examples:
Turn-turn broaching or chasing
For machining different shapes on the main journals, post ends and flanges, use an engineered turn-turn-broaching tool with indexable inserts for the best result.
Turn-turn broaching is a smart combination of turning and turn broaching that provides productive, cost effective and flexible machining with short cycle times, high flexibility and fast tool-setting.
The turning and turn broaching cassettes are mounted radially on a disk turret that moves into the crankshaft and along the bearings as the crankshaft rotates. Use Sandvik Coromant inserts for disc tools of up to 48 cassettes. The standard inserts are delivered within 24 hours in C, T, W and S styles with screw clamping for best stability.
Chasing (multi teeth) inserts is a patented Sandvik Coromant development, some variants are available as stocked items.
- Various functional width dimensions (WF)
- A variety of tool cutting edge angles (KAPR)
- Can be mounted either from below or above
- 1 or 2 tip seats per cassette
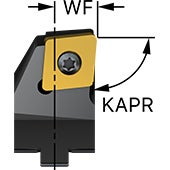
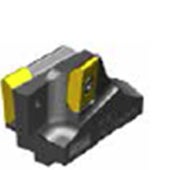
Two inserts
Available tip seats:
- CNMU 12
- WNMU 08
- SNMU 12
- TNMU 16
- VBMT 16
- Q-Cut (maximum seat size 60)
- CoroCut (maximum seat size K)
- Special inserts
T651 Turn-turn broaching soft tools
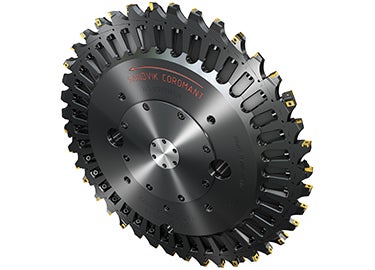
Turn-turn broaching discs
- Up to 48 cassette seats and diameter of 750 mm (29.5 inches)
- Up to 45 cassette seats and diameter of 700 mm (27.6 inches)
- Up to 40 cassette seats and diameter of 642mm (25.3 inches)
- Widths from 16 mm (0.630 inch)
- A variety of couplings for different machine tool makers
- Light weight solutions < 15 kg
Turn-turn broaching cassettes
- Up to now, ca. 600 different cassettes realized
- 7,5°, 8° or 9° pitch ( most common )
- Various width ( min. 16 mm )
- Various WF dimension
- Various KAPR angle
- To be mounted from below or from top
- 1 or 2 tip seats per cassette
Sandvik Coromant can provide a wide range of standard and tailor made turn-turn broaching inserts with advanced grades for high performance machining of crankshafts.
Standard inserts
iC | Screw | Shim | Shim Screw | P | P | K | |||
GC | GC | GC | |||||||
4415 | 4425 | 3210 | |||||||
![]() | CNMU 120408 | - PF | 12 | 1/2 | 5513 020 - 25 | 5322 232 -02 | • | ||
CNMU 120412 | - PM | 5513 020 - 25 | 5322 232 -02 | • | • | ||||
CNMU 120412 | - PM | 5513 020 - 13 | 5322 232 -02 | • | • | ||||
CNMU 120416 | - PR | 5513 020 - 25 | 5322 232 -02 | • | |||||
CNMU 120416 | - PR | 5513 020 - 13 | 5322 232 -02 | • | |||||
CNMU 120412 | - QM | 5513 020 - 25 | 5322 232 -02 | • | • | ||||
CNMU 120412 | - KM | 5513 020 - 13 | 5322 232 -02 | • | |||||
CNMU 120612 | - KM | 5513 020 - 13 | 5322 232 -02 | • | |||||
CNMU 120612 | - KR | 5513 020 - 13 | 5322 232 -02 | • | |||||
WNMU 080412 | - KM | 5513 020 - 25 | 340.885 322 N131 | • | |||||
![]() | WNMU 080412 | - WF | 5513 020 - 25 | 340.885 322 N131 | • | ||||
WNMU 080412 | - WM | 5513 020 - 25 | 340.885 322 N131 | • | • | ||||
WNMU 080612 | - WM | 5513 020 - 13 | 340.885 322 N131 | • | • | ||||
![]() | TNMU 160408 | - PF | 16 | 3/8 | 5513 020 - 25 | • | |||
TNMU 160412 | - KM | 5513 020 - 25 | • | ||||||
TNMU 160412 | - WM | 5513 020 - 25 | • | • | |||||
![]() | SNMU 120416 | - KM | 12 | 1/2 | 5513 020 - 25 | 5322 420 - 02 | • | • |
Tailor made inserts
P | P | P | P | K | K | K | ||
GC | GC | GC | GC | GC | GC | GC | ||
4305 | 4315 | 4325 | 4335 | 3225 | 3205 | 3210 | ||
![]() | S-CNMU 120412 - PM | • | ||||||
S-CNMU 120616 - PR | • | • | • | • | ||||
S-CNMU 120412 - QM | • | |||||||
S-CNMU 120412 - KM | • | • | ||||||
S-CNMT 120416 - MR | • | • | • | • | ||||
![]() | S-WNMU 080412 - WM | • | • | • | ||||
S-WNMU 080612 - WM | • | |||||||
S-WNMU 080412 - KM | • | |||||||
S-TNMU 160412 - KM | • | • | ||||||
![]() | S-TNMU 160412 - WM | • | • | |||||
S-SNMU 120416 - KM | • | |||||||
![]() | S-RCKX 1204M0 - KH | • | • | • | ||||
Internal milling
M641 (tangential mounted inserts) and M642 (radial mounted inserts) crankshaft disc milling concepts
This is a stable system with good process security, which provides an unrivalled cost efficiency. The different tools range from lightweight up to large tools for ship diesel crankshafts.
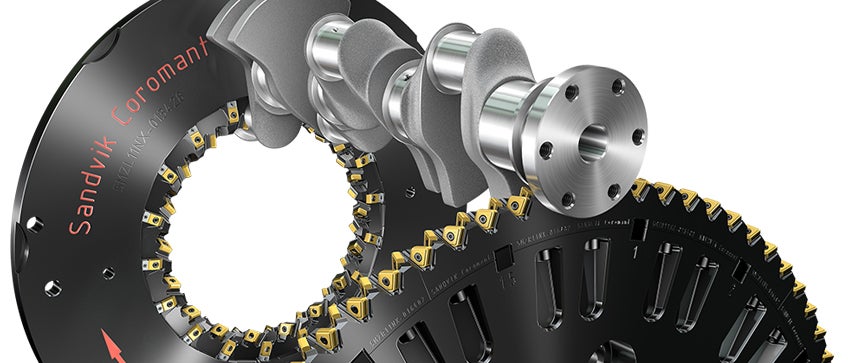
Concept description
M641 and M642 are crankshaft disc milling concepts with tangential (M641) and radial mounted inserts (M642).
The design developed for CoroMill® 745 (face milling) resulted in a new method for positioning inserts on cutters. This gave M642 greater chip room and greater number of effective teeth compared to conventional tangential mounted milling tools.
This new patent pending design results in reduced cycle times and better chip evacuation.
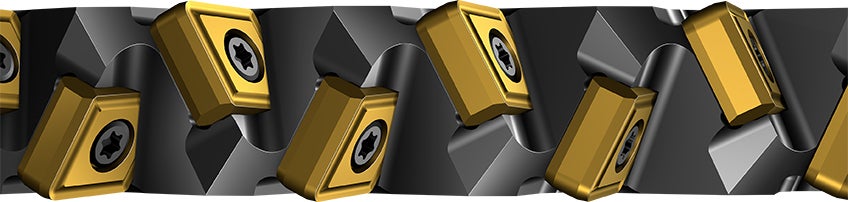
Customer benefits internal milling
- High stability and productivity
- Low carbide cost due to fewer inserts in the cutter
- Quick tool exchange and low tool weight
Features and facts M641/M642 Internal milling (I.D) tools
- Diameters ranging from 170 to 420 mm (6.693–16.535 inches)
- Widths from 15 to 100 mm (0.590–3.94 inches)
- Light weight solutions < 15 kg (33 pounds)
- Solid disc or segment solution
- Variety of segment mountings
- Various couplings for different machine tool makers
- Simultaneous machining of several bearings
- Tandem cutters
- The back face of the insert is protected by the tip seat with the new design
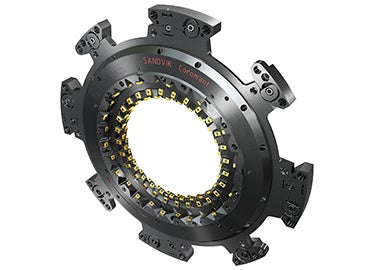
Coupling example
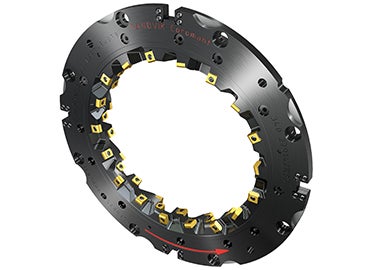
Coupling example
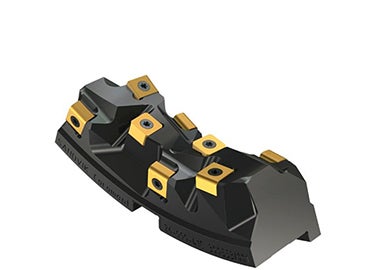
Internal milling segment
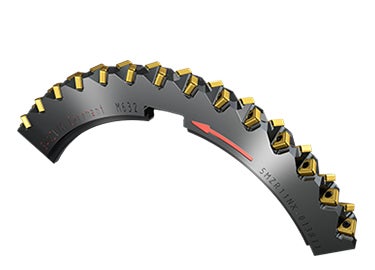
External milling
M631 (tangential mounted inserts) and M632 (radial mounted inserts) crankshaft disc milling concepts
External milling is a flexible and productive method used mainly for large volume machining of small to medium-sized automotive crankshafts. The large discs have a high number of effective teeth and are designed to ensure excellent chip removal, high cutting speeds and process security.
M631 (tangential) and M632 (radial) are innovative solutions that substantially reduces tool change requirements as only the segments with a weight of less than seven kilograms are exchanged. This removes the need to have a crane in front of the machine.
The design developed for CoroMill® 745 (face milling) resulted in a new method for positioning inserts on milling cutters. This gave M632 (radial mounted inserts) greater chip room or greater number of effective teeth compared to conventional tangential mounted milling tools.
This new patent pending design results in reduced cycle times and better chip evacuation.
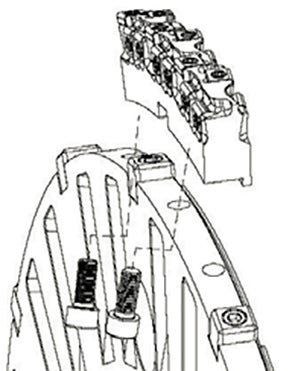
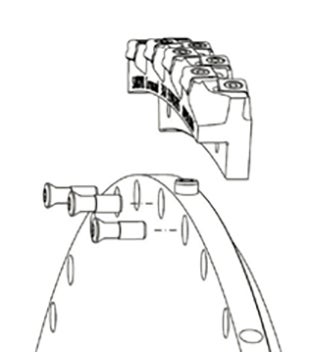
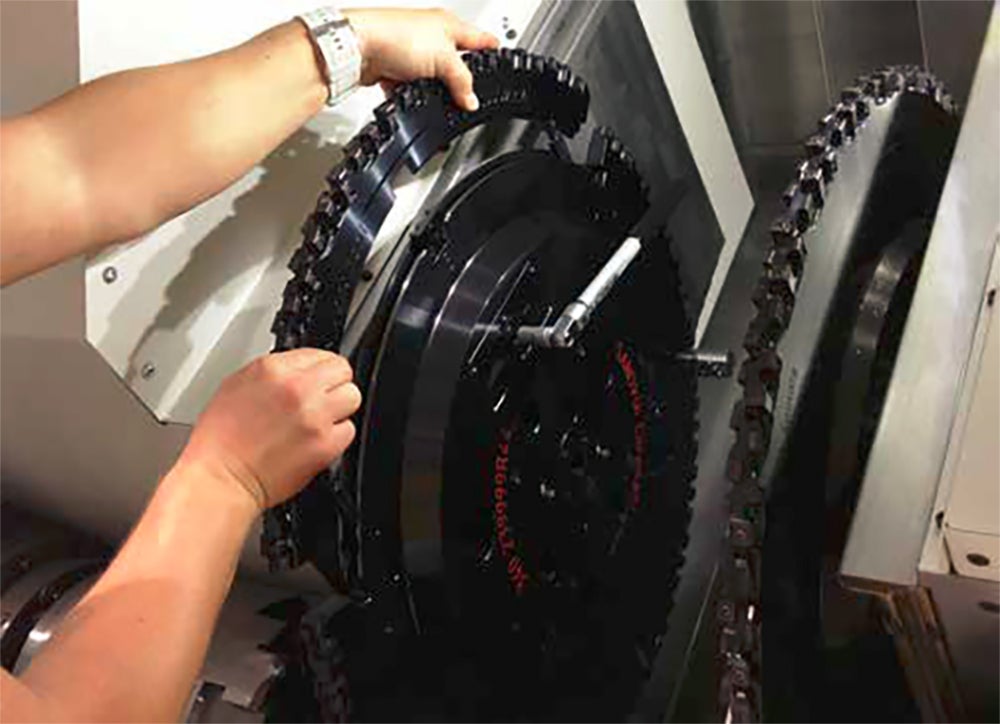
Customer benefits
- Flexible concept
- Light cutting, less cutting forces
- Good chip evacuation
- High cutting speed
Features and facts M631/M632 External milling (O.D) tools
- Diameters up to 1,500 mm (59 inches)
- Tool solutions widths from 15 to 60 mm (0,590–2.36 inches)
- Light weight <15 kg (33 pounds)
- Solid disc or segment solution
- Variety of segment mountings
- Various couplings for different machine tool makers
- Adjustable finishing tools
- Tandem cutters
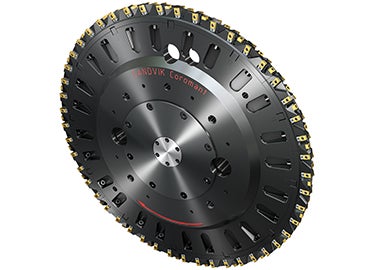
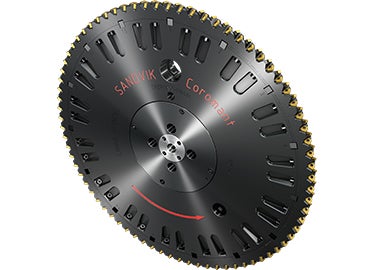
Stocked or made to order?
Some of the cutting tools in this page are available around the clock, with 24-hour delivery. However, solutions engineered according to your specific requirements will take a little longer to fulfil. For more details and quotations please contact your local Sandvik Coromant representative.
Customer case
Changan Automobile Co. Ltd. is a leading Chinese automobile brand that offers a range of different passenger and commercial vehicles. It produces and sells almost three million vehicles annually. At the starting stage of the production line construction, the company ordered five new crankshaft production lines, including a total of 38 machines and a supply of tools for the production of 700,000 crankshafts.
Sandvik Coromant provided the tools and was responsible for the total tooling and engineering solution. The main challenges of the project were the large variety of different manufacturing methods and operations, along with the tight schedule. In addition to general applications such as turn-turn broaching of flange ends, post-ends and main bearings, the customer also needed special tooling and external milling of pin bearings, specific tapping operations and deep-hole drilling. The deadlines for this project were also very strict, with only seven weeks between order receipt and the first delivery.
Gear wheels
Gears come in many different shapes and forms, and they transform the vehicle power... chevron_right
Tailor Made
Tailor Made - customized tools for you Sandvik Coromant introduces thousands of... chevron_right
Sandvik Coromant announces partnership with HCL CAMWorks
S andvik Coroman t Part of global industrial engineering group Sandvik, Sandvik... chevron_right
Sandvik Coromant announces latest partnership with Siemens
Sandvik Coromant Part of global industrial engineering group Sandvik, Sandvik Coromant... chevron_right