Fräsen
Produktüberblick
Es steht eine breite Auswahl von serienmäßigen Silent Tools-Fräsadaptern zur Auswahl, entweder mit HSK- oder modularen Coromant Capto-Kupplungen. Wenn sich keine unserer Standard-Adapter eignen, fragen Sie nach einer maßgeschneiderten Lösung. Adapter für Trennfräser, eingebaute Dämpfer in großen Scheibenfräsern und Walzenstirnfräser sind ebenfalls als maßgeschneiderte Lösungen erhältlich.
Schaftfräser und Eckfräser | Schwingungsgedämpfte Adapter für Plan- und Eckfräser | |
CoroMill® 390D | Schwingungsgedämpfte Adapter – Coromant Capto | Schwingungsgedämpfte Adapter – HSK |
![]() | ![]() | ![]() |
Zylinderschaft oder Coromant Capto Back-End Kupplung | Coromant Capto Back-End Kupplung (C4, C5, C6 und C8) | HSK Back-End Kupplung (HSK 63 und HSK 100) |
Weite, enge und extra enge Teilung | Breites Angebot austauschbarer Schneidköpfe | Breites Angebot austauschbarer Schneidköpfe |
DC: 20-40 mm (0.787-1.575 Zoll) | Innere Kühlschmierstoffzufuhr | Innere Kühlschmierstoffzufuhr |
Überhang: ≤ 5 x BD | BD: 40-80 mm (1.968-3.150 Zoll) | BD: 63-100 mm (2.480-3.937 Zoll) |
DMM: 16-32 mm (0.750-1.500 Zoll) | DMM: 16-27 mm (0.750-1.000 Zoll) | |
Überhang: ≤ 8 x BD | Überhang: ≤ 8 x BD |
- Schwingungsgedämpfte Lösungen ab 20 - 40 mm (0.79–1.57 Zoll) mit integrierten CoroMill 390 Fräsern sind im Standardsortiment erhältlich
- Ab 40 mm (1.57 Zoll) und größer stehen schwingungsgedämpfte Adapter in den Coromant Capto-Größen C4 - C8 zur Verfügung, standardmäßig mit Kühlschmierstoffzufuhr durch die Fräserdornaufnahme. Kombiniert mit einem Grundhalter kann der Adapter ein montiertes schwingungsgedämpftes Werkzeug für die meisten Maschinenschnittstellen sein.
- Für Maschinen mit HSK-Kupplungen sind integrierte Adapter verfügbar, die mit HSK-Grundhaltern von Sandvik Coromant verwendet werden können
- MSSC-Schaftadapter mit Schraubkupplung sind ebenfalls im Standardprogramm verfügbar
Adapterdurchm., BD | |||
Zoll | mm | ||
![]() | Überhang LU/BD |
![]() | Maßgeschneiderte Produkte |
![]() | Coromant Capto® & HSK Adapter für rotierende Werkzeuge Schwingungsgedämpfte Adapter für Plan- und Eckfräser |
![]() | CoroMill® 390D Schaftfräser und Eckfräser |
CoroMill® 390D – Anwendungsbereich
Der CoroMill 390D ist ein echter Produktivitätstreiber für lange und schlanke Werkzeuge, der sowohl in Vertikal- als auch in Horizontalmaschinen eingesetzt werden kann. Die Fräser sind für große Reichweiten ausgelegt, gleichzeitig aber auch effizient, wenn es sich um Arbeiten nahe am Bohrfutter in Multi-Task Maschinen handelt.
Das Programm besteht aus den Coromant Capto-Größen C6 und C5 sowie zylindrischen Schäften in den Durchmessern 20, 25 und 32 mm (0.79, 0.94 und 1.26 Zoll) in einem Bereich, der 3- bis 5-mal größer als der Schnittdurchmesser (DC) ist.
- Hohe Stabilität
- Umfangreiches Angebot an Grundhaltern
- 1. Wahl bei Arbeiten mit erschwertem Zugang
- Hohe Stabilität
- Umfangreiches Angebot an Grundhaltern
- Integrierte Multi-Task-Spindeln
- 1. Wahl bei Arbeiten mit leichtem Zugang
- Coromant Capto® C5
- Coromant Capto® C6
- Zylinderschäfte
- CoroChuck™ 930 zum richtigen Spannen des Fräsers
- Spannzangenfutter
Kurze und lange Grundhalter
Mit einer Kombination aus Fräserdornaufnahme an den Adaptern und Grundhaltern mit unterschiedlichen Längen sind Lösungen für die meisten Anwendungen bis zu 8 x BD im Angebot. Für Überhänge über 8 x BD oder bei speziellen Kundenanforderungen sind die maßgeschneiderten Tailor Made-Lösungen die beste Alternative.
Ungedämpft/Vollhartmetall | ![]() |
Maßgeschneiderte Lösung |
Schwingungsgedämpfte Adapter für Plan- und Eckfräser
- Cx-391.05CD
- 392.41005CD
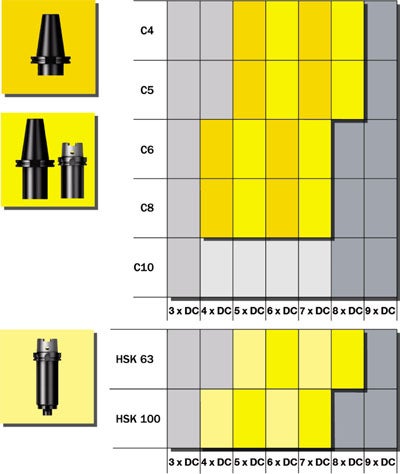
Wichtige Überlegungen
Die Bearbeitung mit rotierenden Werkzeugen unterscheidet sich vom Drehen, bei dem eine Bohrstange in einer Aufnahme sitzt, die meisten Bedingungen für eine erfolgreiche Zerspanung sind jedoch dieselben:
| ![]() |
Vibrationen reduzieren
Bauteilspannung und Maschinenstabilität sind zwei wichtige Einflussfaktoren, die sorgfältig beachtet werden sollten, um Vibrationen zu minimieren.
Bauteil
- Bauteil in der bestmöglichen Art einspannen, um die im Zerspanungsprozess auftretenden Schnittkräfte zu unterstützen
- Fräskonzepte mit Konstruktion und Einstellwinkel einsetzen, die Schnittkräfte in der stabilsten Richtung des Bauteils generieren
- Bearbeitungsstrategie und -richtung optimieren, um die Schnittbedingung möglichst stabil zu gestalten
Maschine
- Der Zustand der Maschine hat einen großen Einfluss auf Vibrationen. Übermäßiger Verschleiß des Spindellagers oder des Zustellmechanismus führen zu schlechten Bearbeitungseigenschaften.
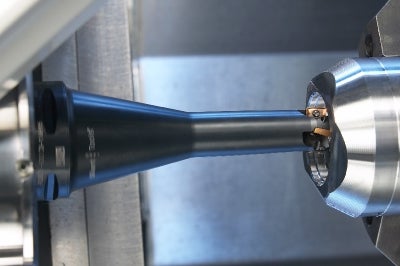
Alle schwingungsgedämpften Werkzeuge sind für verschiedene Überhänge ausgelegt und verfügen über unterschiedlich eingestellte Dämpfer. Die besten Leistungen werden durch Anwendung der optimalen Länge und nicht durch zusätzliche Verlängerungen erreicht. Wird mehr als 7–8 x BD benötigt, fragen Sie nach einem maßgeschneiderten Adapter.
Schwingungsgedämpfte Adapter im jeweils optimalen Bereich verwenden! |
Programmierungsrichtlinien
Eine allgemeine Regel für das Planfräsen besagt, dass der Fräser konstant im Eingriff sein sollte, anstatt Durchläufe mit verschiedenen Längen zu absolvieren. Dadurch wird die Anzahl der Ein- und Austritte minimiert und ungünstige Lasten, die zu Vibrationen führen könnten, werden von den Schneidplatten ferngehalten.
![]() | ![]() |
Einkopieren um Radius | Den Fräser konstant im Eingriff lassen |
Einkopieren um Radius
Dieses Verfahren im Uhrzeigersinn für dünne Späne angewendet, nahe bei Null am Austritt. Dieses Hineinrollen verhindert die Vibrationsneigungen, die von einem
dicken Span am Austritt herrühren könnte.
Fräsrichtung
Gleichlauffräsen ist die 1. Wahl für die meisten Fräsabläufe. In einigen Fällen, wenn die Maschine z. B. nicht leistungsfähig genug ist oder das Bauteil sehr biegsam, wird vorzugsweise das Gegenlauffräsen eingesetzt. Denken Sie jedoch daran, dass die Schnittkraft dazu neigt, das Bauteil beim Gegenlauffräsen anzuheben. Das muss insbesondere beim Aufspannen des Bauteils beachtet werden.
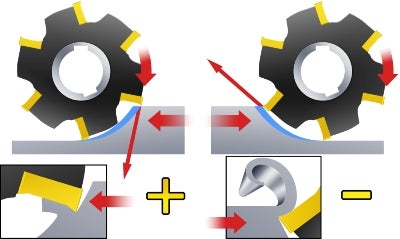
Position und Durchmesser
Im Allgemeinen sollte beim Planfräsen der Fräserdurchmesser 20 - 50 % größer als die Schnittbreite sein, und der Fräser sollte etwas außerhalb der Mitte positioniert werden. Den Fräser nicht genau in der Mitte platzieren.
Ist der Fräserdurchmesser kleiner als das Bauteil, wird eine maximale Schnittbreite von 60 - 70 % des Fräserdurchmessers empfohlen.
Beim Vollnutenfräsen ist es wichtig, die Anzahl der Schneidplatten im Eingriff zu senken, um Vibrationen zu vermeiden.
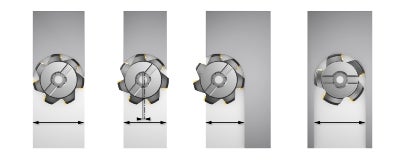
Die Vibration beeinflussende Faktoren
Es gibt vier Grundfaktoren, die Einfluss auf Vibrationen haben:
- Einstell-/Anstellwinkel und Schnittkräfte
- Fräserdurchmesser im Verhältnis zur radialen Schnitttiefe
- Plattengeometrie
- Fräserteilung
Einstellwinkel
Der Einstellwinkel ist wichtig, da er die Richtung der Schnittkräfte bestimmt. Je größer der Winkel Kappa (KAPR), desto höher die radialen Schnittkräfte. Wählen Sie deshalb das Fräskonzept in Übereinstimmung mit Prozess und Anwendung aus.
Erhöhen sich die radialen Schnittkräfte, können Sie den Unterschied in der Funktionalität zwischen schwingungsgedämpften und ungedämpften Werkzeugen sehen.
Mit einem kleinen Einstellwinkel in Kombination mit einem kürzeren Überhang könnte die maximale Schnitttiefe am Fräser erreicht werden, bevor Vibrationen auftreten.
Erhöhte Werkzeugstabilität | |||
![]() | |||
CoroMill 390/ CoroMill 490 | CoroMill 345 | CoroMill 200/ CoroMill 300 | CoroMill 210 |
Fräserdurchmesser im Verhältnis zur radialen Schnitttiefe
Ein kleinerer Werkzeugdurchmesser senkt nicht nur die Leistungsaufnahme und Drehmomentbedarf, sondern reduziert auch die ablenkenden Schnittkräfte. Das Verhältnis von Fräserdurchmesser und radialem Eingriff muss kleiner als jeder Maximalwert gehalten werden.
Plattengeometrie
Die Geometrie des Schneidwerkzeugs sollte für leichte oder mittlere Bearbeitungen ausgelegt sein.
Silent Tools - Funktionsbeeinträchtigung
Hohe Temperaturen können die Funktionsweise des Dämpfungssystems verändern. Wenn möglich, Luftkühlung oder innere Kühlschmierstoffzufuhr einsetzen. Eine extreme n (U/min) kann ebenfalls die Funktion des Dämpfungssystems beeinträchtigen.

Fräserteilung
Sind mehrere Schneidplatten in Kontakt mit dem Werkstoff, erhöht sich das Vibrationsrisiko. Solange Sie mit Schnitttiefen arbeiten, die unter dem kritischen Wert für Vibrationen liegen, ist jedoch eine höhere Anzahl von Platten produktiver. Arbeiten Sie sowohl mit radialem Eingriff als auch mit der Teilung des Fräsers, um das beste Ergebnis zu erzielen. In den meisten Fällen ist eine weite Teilung die 1. Wahl für produktive Zerspanung mit schwingungsgedämpften Werkzeugen.
Fräser mit DifferentialteilungHarmonische Kräfte verursachen Vibrationen; ein Fräser mit Differentialteilung ist deshalb der beste Weg, diese zu minimieren. Er durchbricht die harmonischen Kräfte und erhöht so die Stabilität. Außerdem ist er bei einem hohen ae-Wert und bei langen Überhängen ein nützliches Werkzeug. | ![]() |
Weite Teilung -L | Enge Teilung -M | Extra enge Teilung -H | ||
![]() | ![]() | ![]() | ||
Differentialgeteilter Fräser mit reduzierter Schneidplattenanzahl. 1. Wahl bei instabilen Bedingungen aufgrund der geringen Schnittkräfte. | Gleichmäßig oder differential geteilter Fräser, abhängig vom Konzept, mit mittlerer Anzahl Schneidplatten. 1. Wahl zum Schruppen bei stabilen Bedingungen. | Gleichmäßig geteilter Fräser mit maximaler Schneidplattenanzahl. 1. Wahl für eine hohe Produktivität bei geringem ae (mehr als eine Schneidkante in Kontakt). |
Tipps und Tricks
Schneidplattensorten und -geometrien
Eine kleine Kantenverrundung (ER = edge rounding) wählen. Von einer dicken zu einer dünnen Beschichtung wechseln. Bei Bedarf unbeschichtete Schneidplatten einsetzen. Scharfe und positive Schneidplatten mit spanformender Funktion einsetzen.
Einstellwinkel
Je kleiner der Einstellwinkel, desto dünner der Span und desto breiter wird er sich an der Schneidkante verteilen. Somit wird ein höherer Vorschub pro Zahn möglich. Ein kleinerer Einstellwinkel wird darüber hinaus einen größeren Teil der Schnittkraft direkt in axiale Richtung leiten und so das Vibrationsrisiko senken.
Fräserteilung
In den meisten Fällen ist eine weite Teilung die 1. Wahl für produktive Zerspanung mit schwingungsgedämpften Werkzeugen. Verwenden Sie deshalb einen Fräser mit weiter Teilung, um Änderungen in den Schnittkraftrichtungen zu verlangsamen. Eine reduzierte Anzahl von Schneidplatten bedeutet oftmals einen beträchtlichen Anstieg bei der axialen Schnitttiefe.
Vorschub pro Zahn
Ein höherer Vorschub pro Zahn kann der Werkzeugmaschinenspindel eine konstante Vorspannung verleihen, was wiederum dazu führt, dass sie das Spiel ihrer Lager nicht ausnutzt.
Maximalen Q-Wert erreichen
Als Startwert ae wenn möglich zwischen 60 und 80 % wählen. Die Anzahl der Schneidplatten reduzieren, um Q zu maximieren. Das ist insbesondere beim Vollnutfräsen wichtig.
Spanabfuhr
Druckluft einsetzen, um das erneute Zerschneiden von Spänen zu verhindern. Das ist besonders wichtig beim Fräsen von tiefen Taschen. Beachten Sie jedoch, dass ein Fräser mit weiter Teilung keinen Raum mehr für die Spanabfuhr zur Verfügung hat.
Ein- und Austritt
Vermeiden Sie Situationen, in der die Mittelachse oder der Fräser auf einer Linie mit der Bauteilkante liegen. Dann verlässt die Schneidplatte das Bauteil, wenn die Spandicke am größten ist, wodurch sehr hohe Schockbelastungen an Ein- und Austritt entstehen.
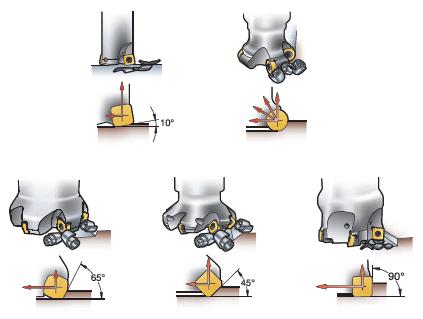