Prozesssicherheit und Kostenersparnis – Hand in Hand
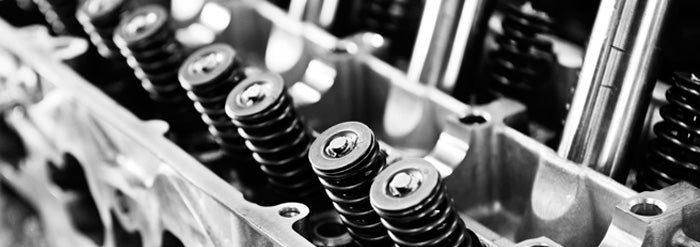
In der Produktionsstätte in Brasilien vertiefte sich die Partnerschaft zwischen dem Hersteller von Motorblöcken und Sandvik Coromant noch weiter, nachdem der Kunde den Vorschlag annahm, eine wichtige aber unzuverlässige Maschine, in der LKW-Dieselmotoren bearbeitet wurden, auszutauschen.
Die Ausfälle einer alten Maschine, in der die Herstellung der Bohrungen in den Motorblöcken erfolgte, kosteten 80.000 BRL (über 30.000 EUR) jährlich an Nebenzeit, und die Reparaturkosten für 2011 wurden mit ca. 30.000 BRL (12.000 EUR) angesetzt.
Ein unerwarteter Vorschlag
Der Kunde wandte sich zunächst an Sandvik Coromant, um nach einer Übergangslösung für die alte Maschine zu suchen. Unser Vertriebsmitarbeiter Antonio Granzoto schlug indes vor, einige Anwendungen auf neuere, flexiblere Maschinen zu verteilen. Aber was vielleicht noch entscheidender war: mit dem neuen Aufbau würden die Maschinenbediener in einer sehr viel sichereren Umgebung arbeiten.
Ein Fertigungsingenieur in der Firma erinnert sich: „Es gab schon vorher Leute mit Ideen, aber die haben nichts gebracht. Als wir uns jedoch seinen Vorschlag ansahen, dachten wir: 'Ja, das müssen wir ausprobieren'. Das könnte wirklich klappen.’“
Umgestaltung der Bearbeitungslinie
Sandvik Coromant, der als Partner des Kunden bereits seit 2005 vor Ort präsent ist, hatte schon zuvor erfolgreiche Teams für Prozesswechsel aufgestellt. Dieses Mal strukturierten die Partner die gesamte Bearbeitungslinie neu.
Eine Fertigungslinie kann nur so schnell sein wie ihre langsamste Maschine. Die Umrüstung der Fertigungslinie erforderte zwei grundlegende Veränderungen. Erstens die Einführung einer neuen Technologie in Form von Silent Tools als Ersatz für die Operation 120. Als nächstes mussten die restlichen Bearbeitungsprozesse der alten Maschine auf andere Bereiche der Fertigungslinie verteilt werden, ohne die Produktionszeit zu verlängern.
Glücklicher Produktionsleiter
Granzotos Plan führte aus, dass kein einzelner Bearbeitungsschritt länger als 12 Minuten dauern würde. Die Umsetzung des Projekts erforderte allerdings eine komplette Umorganisation der Linie. Aber im besten Falle könnten Einsparungen von 700.000 BRL (270.000 EUR) pro Jahr erzielt werden, also viel mehr als die derzeitigen Gesamtkosten des Projekts. Und es hat tatsächlich geklappt! Selbst in der Anfangsphase sparte das neue System bereits jährlich 180.000 BRL (fast 70.000 EUR) allein an Betriebskosten ein. Der verantwortliche Vorarbeiter im Werk stellt fest:
„Das Projekt hatte zweifellos große Auswirkungen, nicht nur in finanzieller, sondern auch in ergonomischer Hinsicht. Wir sind sehr glücklich damit. Wir haben in der Testphase allein in diesem Jahr acht neue Werkzeuge eingeführt.
Diese "Zweihändige Zusammenarbeit" hat Tradition. „Ein Partner macht den Anfang, aber die Verbesserungen und die Entwicklungstätigkeiten erfolgen immer in zweihändiger Zusammenarbeit,“ fügt er hinzu.
„Der neue Linienaufbau und die Werkzeuge senkten die Kosten, während gleichzeitig die Effizienz gesteigert und die Produktionszeit reduziert werden konnten.“
Aus technischer Sicht
Operation 120 war ein Aufbohrprozess, bei dem es immer wieder zu Ausfällen kam. Auch die Sicherheit stellte ein Problem dar. Hier entwickelte Sandvik Coromant eine neue Lösung mithilfe seines Programms zur Produktivitätsverbesserung (PIP), um die Bearbeitungsprozesse der alten Maschine auf andere zu verteilen.
Die Lösung beruhte auf einem neuen Werkzeug aus der Silent Tools-Familie, welches robust genug ist, um die Bohrung mit 120 mm Ø auf einer flexiblen Maschine statt auf einer Spezialmaschine präzise auszuführen. Die schwingungsgedämpfte Bohrstange erlaubt eine Bearbeitung großer Längen und macht einen Einsatz des Werkzeugs in einer CNC-Maschine mit automatischem Werkzeugwechsel statt nur wie bisher auf einer Spezialmaschine mit einer Funktion möglich.
Reduzierung der Bearbeitungsdauer von 6 auf 2 Minuten
Entscheidend war, dass die für die Schruppbearbeitung des Nockenwellenlagers benötigte Zeit von sechs auf zwei Minuten gesenkt werden konnte, eine Zeiteinsparung riesigen Ausmaßes.
Die gesamte Produktionslinie wurde umstrukturiert, und sieben weitere Prozesse wurden auf die Maschinen von Heller und GROB verlagert. „Der neue Linienaufbau und die Werkzeuge senkten die Kosten, während gleichzeitig die Effizienz gesteigert und Produktionszeit eingespart werden konnten.“
Möchten Sie die Produktivität und Rentabilität Ihrer Maschinen optimieren? Kontaktieren Sie unsere Fertigungsspezialisten.
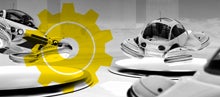
Die dritte industrielle Revolution
3D-Druck und eine neue Generation von Roboterassistenten sind beides Beispiele für die tiefgreifende Umgestaltung der traditionellen Produktion.
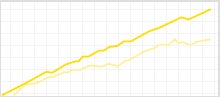
Eine gute Bilanz
Mit unserem Manufacturing Economics Calculator können Sie berechnen, wie sich eine von Sandvik Coromant empfohlene Prozessoptimierung finanziell auswirkt.

Nutzen Sie unser breitgefächertes Angebot
Als Werkzeughersteller kennen wir uns in der Produktion aus. Durch unsere Kompetenz und langjährigen Erfahrungen mit den unterschiedlichsten Branchen können wir Sie umfassend beraten und ganzheitliche Lösungen anbieten. Unser Dienstleistungsangebot zielt darauf ab, Ihre Herstellungskosten pro Einheit zu senken und Ihnen somit Geld zu sparen. Denken Sie über neue Maschinen, Werkstoffe oder Prozesse nach? Fragen Sie uns. Wir können Ihnen helfen.