How to increase metal-cutting efficiency
It’s all about smarter machining
As machining becomes more complex and material costs climb, sharpening your metal-cutting processes becomes beyond essential. The right strategies do more than streamline operations; they cut waste and dial down energy use, keeping you ahead in a competitive landscape.
With that said, there are several things that can be done to prevent downfalls and cost leaks in overlooked or rushed processes.
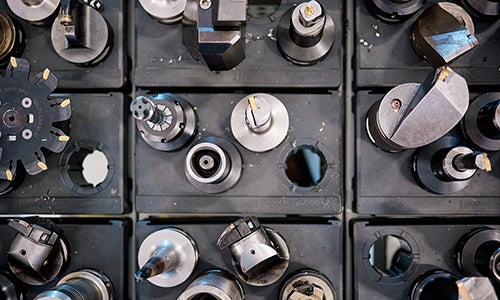
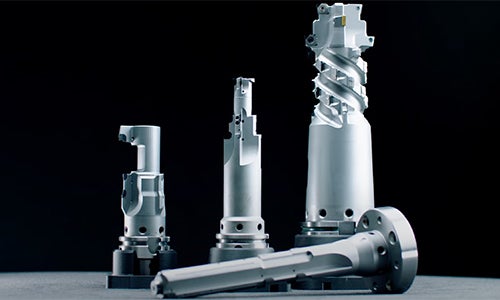
Pick the right cutting parameters
Some rules of thumb to significantly reduce cutting times and enhance tool life:
- Material: Start by understanding the material you are working with, as different materials require different handling.
- Speed and feed: Adjust the cutting speed according to the hardness of the material; lower speeds for harder materials to prevent wear, and higher speeds for softer materials to improve throughput. Set the feed rate to balance between efficiency and quality; higher rates for rough cuts and lower rates for fine finishes.
- Depth of cut: Choose deeper cuts for bulk material removal and shallower cuts for finishing to optimize tool use and achieve desired surface quality.
Save as much of your tools as possible
Factors to consider when selecting tools:
- Material hardness vs tool material
- Tool geometry and material compatibility
- Grades and coatings for longevity
- Speed and feed
- Machining operation
Pair these considerations with diligent tool management to ensure your machinery performs at its best.
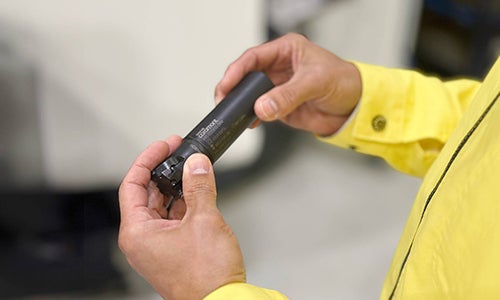
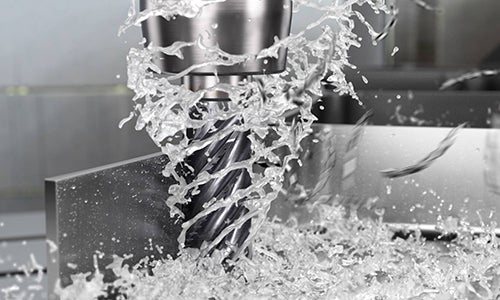
Cool down before sparks start flying
Effective cooling and lubrication are key to boosting cutting performance and tool longevity. Methods like flood cooling, mist, and MQL (Minimum Quantity Lubrication) are popular, but under and over coolant methods provide targeted cooling directly to the cutting zone. Over coolant attacks heat from above, directly on the cutting edge, while under coolant cools from beneath, reducing thermal stress and maintaining tool integrity. Together, they ensure precise temperature control, improving chip evacuation and reducing the risk of premature tool failure.
The many advantages of digital twins
Using digital twin simulation in the pre-machining phase will mirror your physical operations, allowing you to predict outcomes, optimize efficiency, and reduce errors before they happen. Digital twins allow you to:
- Validate designs faster and streamline troubleshooting: Use simulations to diagnose and solve production issues without disrupting actual operations.
- Reduce material waste
- Enhance safety: Identify and rectify potential safety issues in the virtual environment to prevent real-world accidents.
- Improve training: Train new operators in a risk-free virtual environment, speeding up their learning curve and reducing training costs.
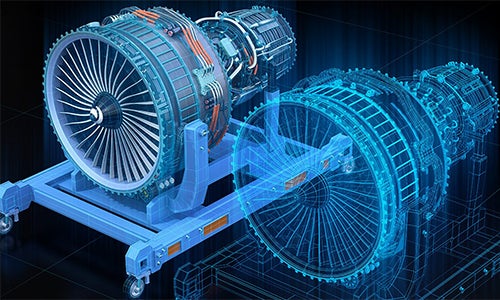
Precision and efficiency—watch CoroCut® 2 in action
Explore solutions to increase metal-cutting efficiency
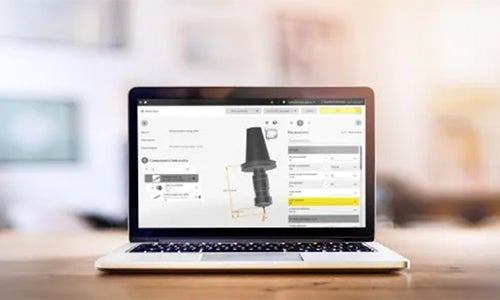
CoroPlus®
The CoroPlus® portfolio contains several connected solutions that will boost the predictability factor in your machining.
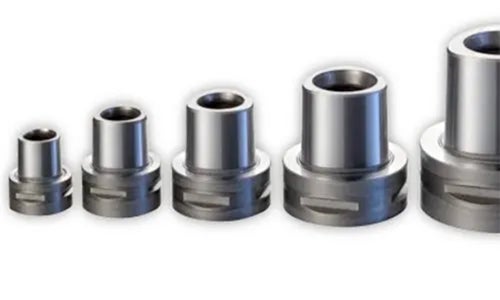
Coromant Capto®
Predictable machining relies on stable tool holding. Find out more about Coromant Capto®.
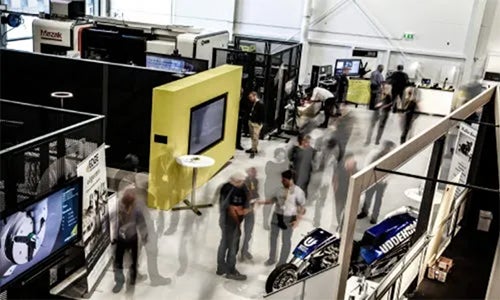
Visit our Sandvik Coromant Centers
The focal point of our machining expertise, knowledge, digital machining, and sustainability.
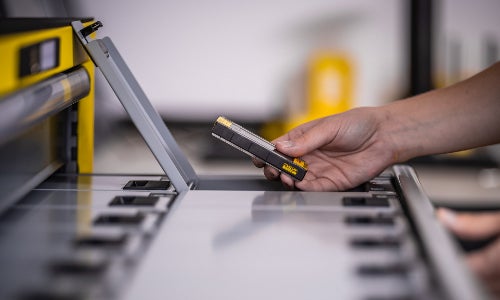
Tool inventory management
Controlling your inventory is not just a necessity; it's the key to securing your productivity and boosting your bottom line.