Geleceğin fabrikası
Sandvik Coromant'ın İsveç'teki Gimo kentinde bulunan takım üretim tesisi, Dünya Ekonomik Forumu tarafından gelişmiş bir Endüstri 4.0 tesisi olarak tanındı.
Stockholm'ün kuzeyindeki Gimo'da bulunan Sandvik Coromant takım üretim tesisi, dijital bağlantılı üretimin getirdiği çok sayıda avantajdan tam olarak yararlanan, yüksek düzeyde otomasyona sahip bir tesistir. Bu durumu onaylayan Dünya Ekonomik Forumu kısa bir süre önce, Gimo'nun global "deniz feneri" tesislerinden biri olduğunu açıkladı. Deniz fenerleri 1000'den fazla sayıda üretim birimi arasında yapılan bir ankete dayalı olarak, dijital teknolojileri benimseme ve somut avantajlar ortaya çıkarma kriterleri dikkate alınarak belirlenir.
Dünya Ekonomik Forumuna göre Gimo fabrikası üretim prosesleri üzerinden oluşturduğu dijital iş parçacığı ile önemli bir verimlilik artışı sağladı. Bu konudaki örneklerden biri insansız vardiyalarda bile çalışan ve tasarım modellerinin otomatik olarak değiştirilmesini sağlayan "el değmeden değişim" özelliğidir. Gimo, sınıfının en iyisi olan bu tür gelişmeler sayesinde global deniz feneri ağının bir parçası haline geldi ve diğer üretici işletmelere kapılarını açarak bilgi paylaşımında bulunmaya başladı.
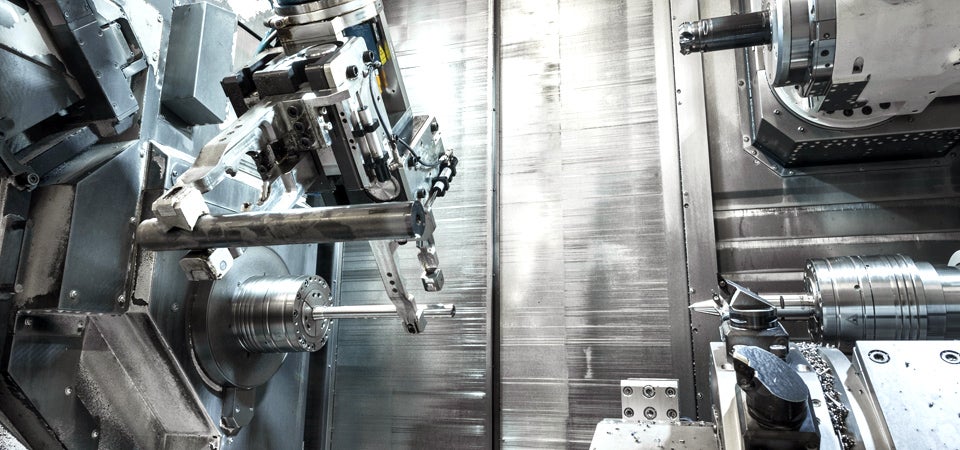
Sandvik Coromant üretim teknolojisi araçları direktörü Lars Matiasson özellikle, yeniliği teşvik etme yönünde yıllardan beri devam eden çalışmaların ulaştığı doruk noktasını takdir eden ödülün Gimo'da büyük bir gururla karşılandığını belirtiyor. “Gimo'daki dijitalleşme yolculuğumuz aslında 30 yıl önce parametrik CAD/CAM uygulamasıyla başlamıştı. Ardından, birkaç yıl sonra bunu akıllı otomasyon sistemimize bağlayarak üretimdeki ilk dijital iş parçacığımızı oluşturduk. Aslında buna devrim değil, evrim demek daha doğru olacaktır.
Bugün stok yönetiminden tezgah performansına ve öngörücü bakıma kadar bütün tesisi kapsayan bir dijital iş parçacığı yapısına sahibiz. Yenilik ruhu, her kademede kararlı bir şekilde yaşatılır. Gimo'daki direktörler ve müdürler her zaman mühendisleri farklı şekilde düşünmeleri ve yeniliğin öncüsü olmaları konusunda teşvik eder. Sonuçta, fabrikanın verimliliğini yükseltmek ve rekabet gücünü artırmak için teknolojinin nasıl kullanılacağı araştırılır. Bu da, sürdürülebilir bir gelecek için bize destek sağlar."
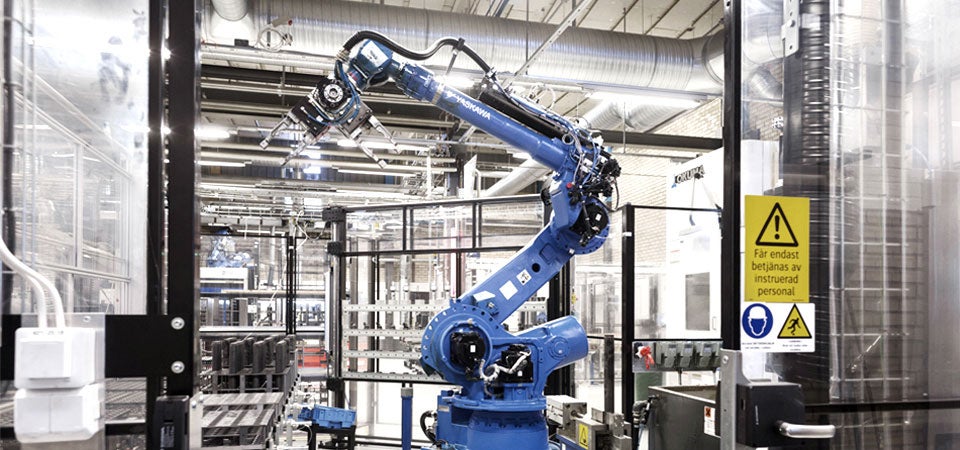
El değmeden değişim, bu konuya tipik bir örnektir. Geçmişten bu yana, üretim hücrelerindeki tasarım şablonlarının manuel olarak değiştirilmesi gerekiyordu; gündüz vardiyasında çalışan operatörler tezgahları gece çalışması için hazırlıyorlardı. Zaman ve kaynak gerektiren bu çalışma şeklinde insansız vardiyalarda esneklik de sınırlı kalıyordu. Alternatif yaklaşım, karmaşık bir işlem olan el değmeden değişimi insan gözetimine gerek kalmadan gerçekleştirmek üzere akıllı otomasyona yatırım yapmayı ve ultra esnek robotlar, tezgahlar, takımlar ve fikstürler kullanmayı içeriyordu.
Matiasson şöyle dedi: “Tekli dakikalarda kalıp değiştirme gibi yalın üretim tekniklerinden söz edildi, ancak biz bunun da ötesine geçmek istedik. Sıfır iş gücüyle kurulumu hedefledik.
Öğrenmemiz biraz zaman aldı. İlk otomasyon hücresi umduğumuz kadar iyi çalışmadı. İşin doğrusu, bir operatör ve bir tezgahın çalışması kadar bile verimli değildi. Ancak, dijitalleşmeye geçiş böyle bir şey; öğrenirken başarısızlıkları aşmanız gerekiyor. Zaman içinde önemli ilerlemeler kaydettik ve robot hücrelerimiz gereken verimi sağlamaya başladı. Bu konuda ilerlerken, deneme ve yanılma işimizin hep bir parçası oldu.”

Gimo'da, bakım gibi diğer bazı alanlarda da dijital teknoloji kullanılarak ilerleme sağlanıyor. Fabrikadaki pek çok ekipmana takılan ve sayısı günden güne artan sensörler yardımıyla basınç, sıcaklık, titreşim ve ses gibi giderek çoğalan pek çok parametreye ait veriler toplanıyor. Bu veriler, karmaşık analizlerle birlikte kullanıldığı zaman çalışma kesintileri ortaya çıkmadan önce problemler belirlenebiliyor.
Mühendisler artık üretim tesisinin her yerinden veri alabiliyor; robotlar, CNC tezgahları ve hatta kesici takımlar bile veri kaynağı olabiliyor. Bu veriler çekilip analiz edildiğinde ekipmanların sağlığı konusunda değerli bilgilere ulaşılabilir. Bu bilgi arızaların öngörülmesi ve önlenmesi için kullanılabilir ve böylece tesis verimliliği iyileştirilebilir.
Sandvik Coromant'ın üretim ortamında gerçek zamanlı analizin rolü de giderek artıyor. Böylece tezgahlarda daha doğru ve iyi zamanlanmış ayarlar yapılabiliyor. “Bundan sonraki aşamada yapay zeka ve makine öğrenimi gibi çok sofistike teknikler devreye alınarak tezgahların geçmişe ait verilerden öğrenmeleri ve kendi kendilerini kontrol etmeleri sağlanabilir. Bu, gerçekten de heyecan verici bir alan.”
Bu dikkat çekici teknik ilerlemelere ve Dünya Ekonomik Forumunun deniz feneri ödülüne rağmen Gimo'daki dijitalleşme yolculuğu duraklamadan devam edecek.