Backstage in Gimo: Small and large strategies for cutting costs
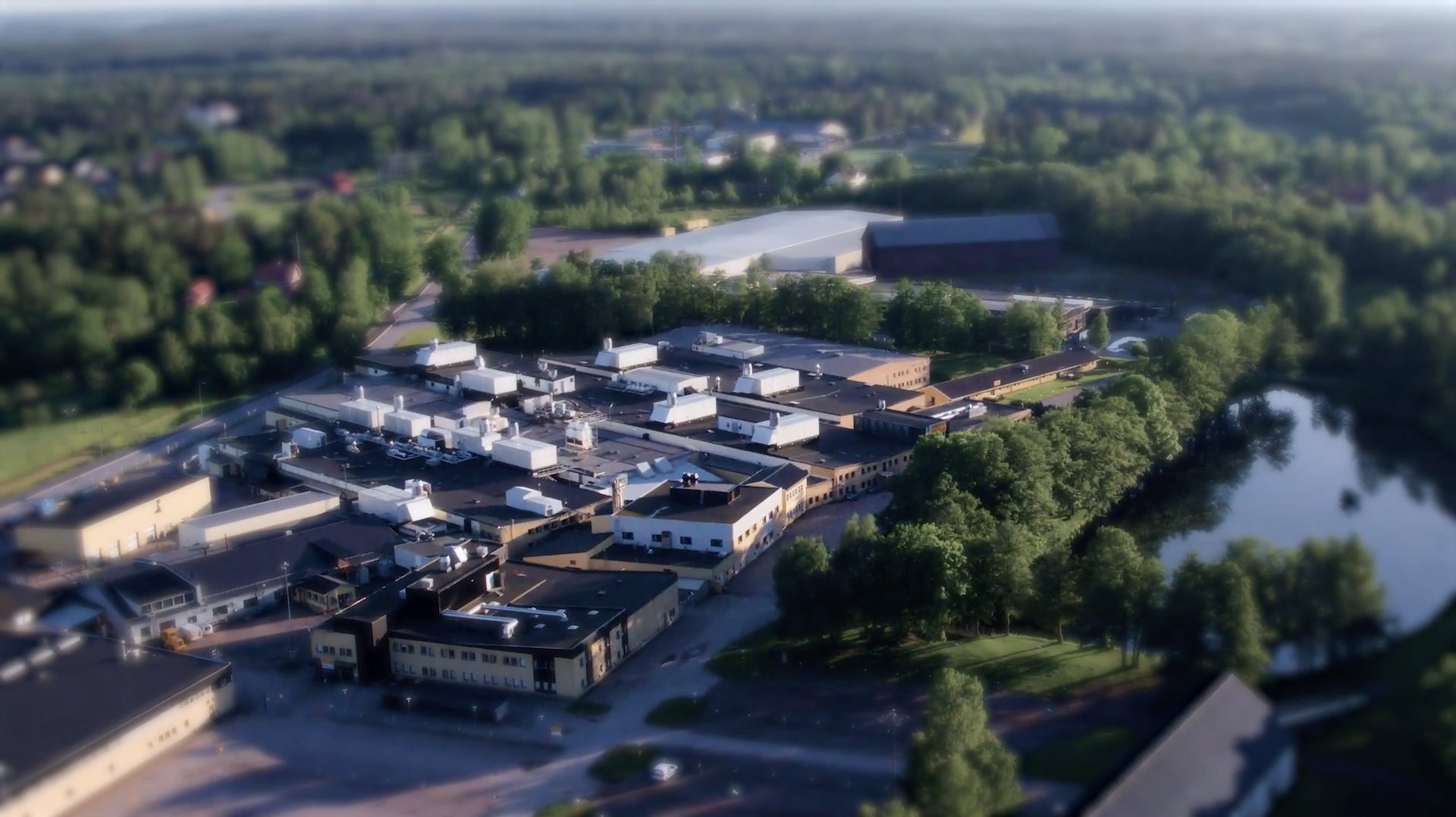
Optimized tools can pay off in the end
Let’s start with tools of course. It’s no surprise that a metal cutting tool company places huge importance on the use of high-performance tools. Call this a shameless plug, but one tool that has made a vast difference for their production is the CoroMill Plura Heavy Duty (HD) end mill. “It really is as good as promised, the larger cutting depth combined with increased cutting speed and feed made the productivity increase extreme”, says Per Arvidsson, Manufacturing Engineer.” By switching, we got twice the production rate but also increased process stability, incredible time savings and increased output”.
This shows a typical case when an initial investment brings substantial long-term benefits. The optimized CoroMill Plura tools are more expensive than versatile tools, but, as in this case, when you are working with large batches or one specific type of operation, it’s definitely worth going with the optimized tool.
Sustainable savings: Your trash could also be your treasure
Another cost-saving example on the subject of end mills is reconditioning. Lots of money can be saved by reusing worn-out end mills — the process provides tools with exact diameters up to three times. With the potential to recondition millions of tools each year, the impact on sustainability is immense.
Talking about sustainability, we automatically touch on another topic: energy use. The plant in Gimo is looking into their energy productivity in a structured way by putting sensors on the tools to measure energy use. “Besides measuring, you can keep track and check the power balance, operate faster when not in cut and make use of energy more effectively”, says Carl-Olof Wiebensjö, Technical Production Manager. Needless to say, substantial amounts of money and resources can be saved.
Implement new technologies
It’s easy to get stuck in a rut. Sometimes you actively look up new solutions, other times circumstances — in this case automation — are what push you forward. The production in Gimo was going to build in a newer turning centre to a machining cell. The existing machine was operated manually with one person constantly supervising production. Chip breaking issues forced stops every four minutes to remove chips.
The primary challenge was to reduce the number of tools in the turret. This was a brilliant occasion to try out new tools and technologies, and they seized the opportunity. Y-axis parting, PrimeTurning and dynamic turning with round inserts were all implemented, resulting in improved chip control, predictable tool life and a massive productivity increase of up to 800%. What made Markus Svensk, Process Planning and CAM Automation Manager, especially satisfied were two Tailor Made tools, which replaced 7 different tools and enabled a standard rigging of the turret. “We ended up going from 17 to 8 tools and an unmanned cell. With minutes saved on every piece and less idle time, this was an investment that certainly paid off.”
Keep an eye on the insert wear!
The insert edge spends its time in close encounter with our most important object, the component, yet its condition is sometimes overlooked. If that’s the case in your production, there are potential savings to make. “We have really delved into insert wear analyses and that has paid off” says Markus, and Per adds: “For example, when machining with a new milling tool, instead of checking it after 40 minutes or when something seems wrong, have a look at the insert wear every five minutes to see how the wear evolves. This way you don’t have to start all over at square one if something happens.”
To work preventively with tool wear, and to regularly examine the complete tool, such as checking the insert seats, brings a much safer process — it helps you to go from gut feel to predictable tool life.
From calendar time to operating time
Planning is key and that applies very well to tool maintenance. Proper maintenance prevents problems and saves money. By scheduling maintenance based on actual machining time instead of only by time passed, you are in control and know the actual condition your tools and machines are in and can plan maintenance stops instead of repairing broken machines. This way you work preventively but also skip unnecessary maintenance. There are also machining cells calculating when it’s time for maintenance, making planning and scheduling even easier.
Don’t manage without tool management
A straightforward way to reduce cost is to implement a tool management system. The plant in Gimo employs the SmartPick input-output system. “By using a streamlined procurement process, we get an overview of the tools available, which effectively reduces inventory levels”, concludes Per. “Since the tool cabinet automatically orders the tools, we can free up time and people for more productive tasks.”
In fact, the software can, besides keeping track of the inventory levels, also make digital machining simulations. All tool components are built up in a database, which is connected to the Vericut simulation software. By simulating the operation digitally, you can keep costly mistakes to a minimum and optimize the tool paths.
Useful links recommended by our team
You can find a great amount of information on the Sandvik Coromant web page. Especially the Knowledge pages with the Troubleshooting section for each tooling area can be of great value.
CoroPlus Tool Guide: Optimize your cutting parameters
“A really good tool we are actively using”. There are lots of ways to use it to simplify your production. One way is working with start values. Instead of using print values in catalogues you can optimize the values completely for your specific operation and parameters. Optimize the figures, test different values, adjust parameters and tailor the results.
Get started with analyzing tool wear, this app can serve as a starting point.
Find the ones that can help you improve production and reduce costs effectively.
It never hurts to know just a little bit more on the topic. Walk the workshop floor with our infographic, talk with an lean expert, or get straight to business with our cost-cutting guide: