このギターが完成するまでの経緯は?
サンドビックが3Dプリンタで世界初の壊れないギターを作るまで
ここ何十年の間、数々のロックスターたちがギターを破壊してきたが、スウェーデン生まれのカリスマ・ギタリスト、イングヴェイ・マルムスティーン氏ほど「ギター破壊」に情熱を燃やすミュージシャンはいないだろう。世界的なエンジニアリング会社であるサンドビックは、自社の最先端の技術を試すべく、世界初となるオールメタル製の壊れないギターを製作し、マルムスティーン氏にその破壊スキルを思う存分ぶつけてもらうことにした。
サンドビックは、いかにして最先端の持続可能な技術を使って、高精度かつ驚異的な耐久性を持つものを作ることができるかを実証するために、全社からエキスパートを集めた。
「先端材料、精密加工、アディティブマニュファクチャリング、データに基づいた生産、これらはみな、第一線のミュージシャンにとってのギターのように複雑で美しいものを作り出すために用いられるプロセスです。」と、サンドビック・マシニングソリューション社長のクラス・フォーストロムは述べている。「ただ、私たちは、複雑で美しく、かつ、イングヴェイがどれだけ破壊しようと試みても壊れないギターを作ることができる、そのことを示したかったのです。このプロジェクトは、当社の高いスキルと能力、そして彼のスキルと能力との完璧な組み合わせだと思いました。」
共同作業によるスタート
フロリダでのマルムスティーン氏のライブから遡ること数か月前のスウェーデンで、サンドビックは材料、加工プロセスおよびアディティブマニュファクチャリングのエキスパートを全社から集め、この課題にどのように取り組むかについて、ブレインストーミングを行った。
これまでギターを作ったことは一度もなかったため、サンドビックは、イギリスに拠点を置くギター製作会社、Drewman Guitars社の著名なギター設計者と共同で、このプロジェクトを立ち上げることにした。「私たちは上から下まですべてを新たに開発しなくてはなりませんでした。」と、Drewmanの設計者、アンディ・ホルト氏は語る。「私たちは、ミュージシャンに『こんなふうに作られたギターは今まで見たことがない』と言わせたいと望んでいました。」
ホルト氏曰く、開発プロセスの間、サンドビックのエンジニアに毎日、新しいデジタル設計ファイルを送っていた時期があったそうだ。ギター製作会社との緊密な協力関係により、最終的に彼らが両者共に納得が行く形で完成させた設計は、優れた技術と独創性から生まれた傑作だった。
世界初の壊れないギター
サンドビック・コロマントの加工プロセス開発担当者、ヘンリク・ロイカネンは、若い頃からマルムスティーン氏に傾倒し、ギターを弾き続けてきたエンジニアだ。ただ、彼は一度もギターを破壊したことはない(「高価すぎるからね。」と、ロイカネンは言う)。彼はまず、マルムスティーン氏がギターを破壊するとき、どのような現象が起きるのかを把握しようと考え、YouTubeをチェックした。
「可能な限りのあらゆる破壊方法でも壊れないギターを設計することが必要でした。」と、ロイカネンは振り返る。「エンジニアリング上の課題だったのは、ネックとボディの間の重要な接合部で、通常はこの部分でギターが折れます。」そこで、サンドビックのエンジニアは、ネックとボディの間の接合部をなくすことを選択した。ネックと指板の両方の先が長方形の「ハブ」として、ギターボディに差し込まれる構造だ。
指板に施したスキャロップ加工によって、イングヴェイは音符を巧みにコントロールすることができるのだが、そのために、エンジニアはフレットとフレットの間を長く、滑らかな円弧状に削る加工を行わなくてはならなかった。ギターの可能な限りの軽量化を図るため、サンドビック・コロマントはネックと指板の内部を中空にくり抜くことにした。
「各フレットの高さを完璧に揃えなくてはなりませんでした。さもないと、弦がいくつかのフレットに当たって音が出てしまいます。」と、ロイカネンは説明する。
最新の技術を駆使したデータ
指板やネックのような細長い形状の部品は、加工プロセスにおいて、ねじれや歪みに対して特に弱い性質がある。サンドビック・コロマントは、最新のソフトウェアを使って、最初の加工の前にデジタル技術によるフライス加工のシミュレーションを行った。
「精度がきわめて重要でした。」と、ヘンリク・ロイカネンは言う。「長年の経験を基に構築された当社のソフトウェアによって、最適な工具と推奨加工条件が提示されるので、部分的に厚さが1ミリになる難しい形状の指板をフライス加工で作ることが可能になったのです。」
さらに、自動化されたプロセスにより、たった1台の機械で指板をフライス加工することができた。このプロセスでは、90種類の個別の加工作業が必要となるが、一連の作業は、新しい工具や加工のセットアップのために機械を停止させることなく、最後まで行われた。
「原材料をセットするだけで、完成部品が出てきます。」と、ロイカネンは言う。「これは、被削材を加工する、よりスマートな方法です。サイクルタイムを短縮し、より安価なコストで部品を製造することができます。」
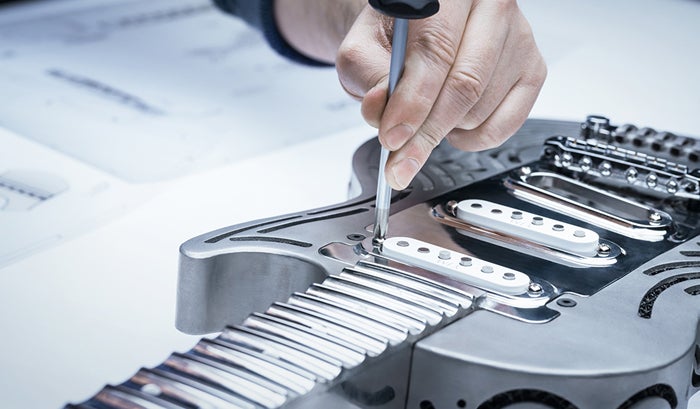
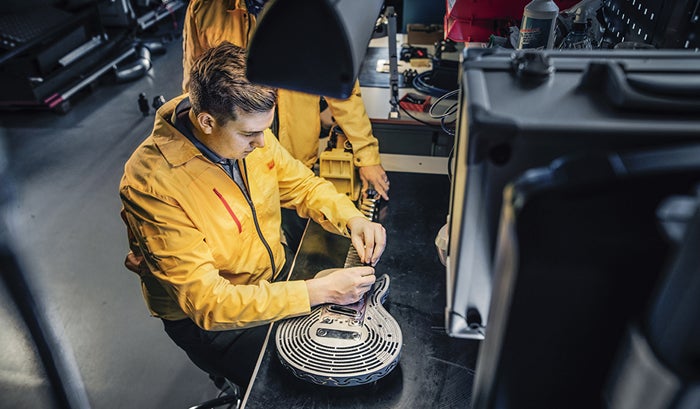
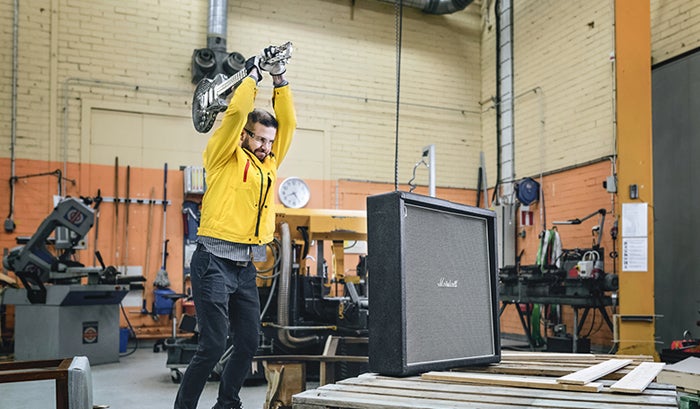
最終完成品のギターが製造されるまで、エンジニアたちはバージョンを重ねながら、より軽量な試作品を作っていった。高精度の切削工具であるCoroMill®カッターで仕上げ加工を行うと、金属製ギターの滑らかな表面は美しく輝いた。
ロイカネンは、サンドビックグループの他の部門との共同作業が、壊れないギターを作り出す重要な鍵となったと言う。サンドビック・アディティブマニュファクチャリングは、彼のサポートにより、ギターボディと小物部品のフライス仕上げ加工を行った。これらはすべて、チタン合金粉末を用いて3Dプリンタで製造した部品だ。サンドビック・コロマントは、サンドビック・マテリアルテクノロジーとも協力して、部品に使用する鋼材の選定を行い、ギターネック内部のハイパー二相鋼による格子構造を実現させた。このチームワークがギター製作の真の目的だったと、彼は評価する。
「サンドビック・コロマントは、複雑な課題を抱えたお客様へのサポートで有名ですが、それは単に工具を提供するだけではなく、当社の工具をお客様の加工プロセスで使用するための最適な方法を開発する手助けを行うことでもあるのです。」と、ロイカネンは言う。