Flatbed lathes
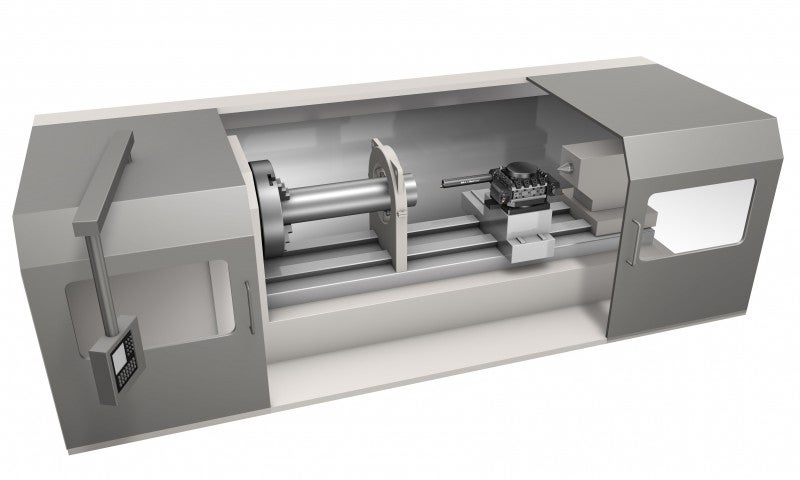
Flatbed lathes are widely used in heavy-duty turning offering a reliable, stable and powerful machining process with high productivity.
Flatbed lathes machine configuration
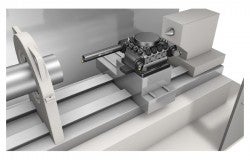
Heavy duty and flatbed lathes have extremely high stability but have a more limited tool changing and indexing possibility compared to slantbed turning centres and vertical lathes. Large component/swing diameters combined with long lengths make steady rest and tailstock a standard fixture.
Flatbed lathes are generally considered easier to accommodate the loading and unloading of large components. A "gap" between the headstock and bed can also be useful to permit increased component swing diameters – leading to the name "gap bed lathes".
Large machines often have large bore headstocks and some headstocks can have double chucks fitted to permit through headstock loading.
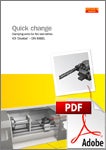
The bed lengths are often well over four meters and easily permit the use of multiple steady-rests. However, it should be noted that these are often "fixed" steadies and normally cannot be used in the same way as the hydraulically operated "turn-through" types generally used on slantbed machines or turning centres (the slantbed design can also permit easier axial positioning).
Not all flatbed lathes are fitted with chip conveyors, therefore always consider chip removal possibilities. Sometimes front and rear conveyors are a good option to reduce downtime.
Turret configuration
Turning operations can be classified as heavy duty requiring high stability and the tool post design is often preferred over the revolver design. If the machine is to be fitted with an indexable tool post, then a VDI dovetail (DIN 69881) provides extremely good stability and is still the most robust solutions for the demanding cutting depths as well as for providing sufficient clamping stiffness for long boring bars. Sizes 115 and 140 are commonly used, 140 is preferred for heavy duty cutting and long boring bars.
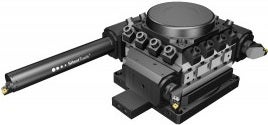
VDI dovetail
The VDI dovetail four post type turret gives plenty of adjacent tool clearance, however with only four indexing positions for all operations this produces some limitations when using shank tooling.
Long boring bars loaded to the turret may restrict the tool post from indexing. Quick change coupling boring bars are now standard up to Ø100 (10×D) which permits easy and accurate tool change to maximize the utilization of the machine.
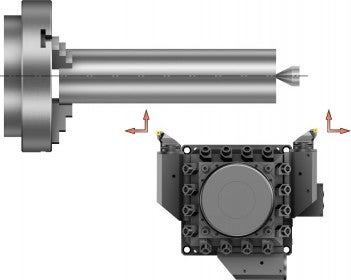
External set-up
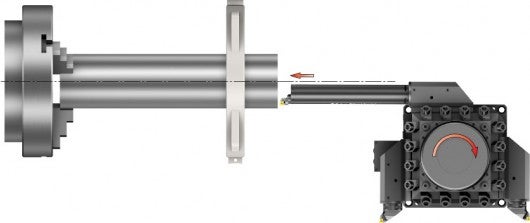
Internal set-up
Deep hole machining
Flatbed lathes are commonly used for deep internal machining. The following areas need to be considered:
- Boring bar saddle/cross slide Boring bars up to diameter 600 mm (23.622 inch) can be utilizedIt is important to have split cap clamping on the saddle for at least 4×DThe moment of the boring bar needs to be consideredA counterweight might be needed depending upon the diameter/overhang
- Drilling spindle – rotating/stationary
- Pump capability for deep hole drilling – pressure/flow
- Coolant tank capacity
Quick change in flatbed lathes
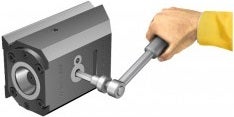
Flatbed lathes offer high stability but slow tool indexing and changing. Shank tool holders are heavy and with the limited number of tool positions quick change has a dramatic effect on machine efficiency.Read more about quick change solutions
Vertical lathes
Vertical lathes, or VTL:s, are one of the most traditional machine types. They are... chevron_right
Vertical turning centres
A vertical turning centre is a cross hybrid from the turning centre and the vertical... chevron_right
Sliding head machines
Sliding head machines provide unrivalled performance for small high-volume components... chevron_right
Machining centres
Machining centres satisfy all demands for components and operations like milling,... chevron_right