Vinkkejä reikien kalvintaan
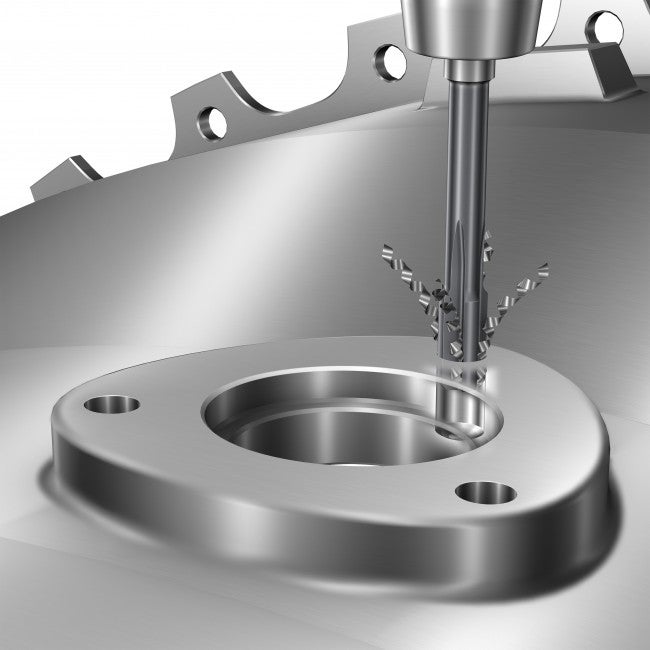
Reiän kalvinnassa on tärkeää noudattaa seuraavia suosituksia.
Työvara
Kalvinnassa suositeltava työvara riippuu koneistettavasta materiaalista ja esireiän pinnankarheudesta. Seuraavaan taulukkoon on koottu yleisiä suositusarvoja työvarasta.
Ø, mm | ||||||
Materiaali | 1–3 | 3–5 | 5.1–10 | 10.1–20 | 20.1–30 | > 30 |
P1 | 0.1–0.2 | 0.1–0.2 | 0.2 | 0.2–0.3 | 0.3–0.4 | 0.4–0.5 |
P2 | 0.1–0.2 | 0.1–0.2 | 0.2 | 0.2 | 0.3 | 0.3–0.4 |
P3 | 0.1–0.2 | 0.1–0.2 | 0.2 | 0.2 | 0.3 | 0.3–0.4 |
P4 | 0.1–0.2 | 0.1–0.2 | 0.2 | 0.2–0.3 | 0.3–0.4 | 0.4–0.5 |
P5 | 0.1–0.2 | 0.1–0.2 | 0.2 | 0.2 | 0.3 | 0.3–0.4 |
M1 | 0.1–0.2 | 0.1–0.2 | 0.2 | 0.2 | 0.3 | 0.3–0.4 |
M2 | 0.1–0.2 | 0.1–0.2 | 0.2 | 0.2 | 0.3 | 0.3–0.4 |
M3 | 0.1–0.2 | 0.1–0.2 | 0.2 | 0.2 | 0.3 | 0.3–0.4 |
K1 | 0.1–0.2 | 0.1–0.2 | 0.2 | 0.3 | 0.3 | 0.5 |
K2 | 0.1–0.2 | 0.1–0.2 | 0.2 | 0.2–0.3 | 0.3–0.4 | 0.4–0.5 |
K3 | 0.1–0.2 | 0.1–0.2 | 0.2 | 0.3 | 0.4 | 0.5 |
K4 | 0.1–0.2 | 0.1–0.2 | 0.2 | 0.3 | 0.4 | 0.5 |
K5 | 0.1–0.2 | 0.1–0.2 | 0.2 | 0.3 | 0.4 | 0.5 |
N1.1 | 0.1–0.2 | 0.1–0.2 | 0.2–0.3 | 0.3–0.4 | 0.4–0.5 | 0.5 |
N1.2 | 0.1–0.2 | 0.1–0.2 | 0.2–0.3 | 0.3–0.4 | 0.4–0.5 | 0.5 |
N1.3 | 0.1–0.2 | 0.1–0.2 | 0.2–0.3 | 0.3–0.4 | 0.4–0.5 | 0.5 |
N1.4 | 0.1–0.2 | 0.1–0.2 | 0.2–0.3 | 0.3–0.4 | 0.4–0.5 | 0.5 |
N2 | 0.1–0.2 | 0.1–0.2 | 0.2–0.3 | 0.3–0.4 | 0.4–0.5 | 0.5 |
N3.1 | 0.1–0.2 | 0.1–0.2 | 0.2–0.3 | 0.2–0.3 | 0.3 | 0.5 |
N3.2 | 0.1–0.2 | 0.1–0.2 | 0.2–0.3 | 0.2–0.3 | 0.3 | 0.3–0.4 |
N3.3 | 0.1–0.2 | 0.1–0.2 | 0.2–0.3 | 0.2–0.3 | 0.3 | 0.3–0.4 |
N3.4 | 0.1–0.2 | 0.1–0.2 | 0.2–0.3 | 0.2–0.3 | 0.3 | 0.3–0.4 |
N4 | 0.1–0.2 | 0.1–0.2 | 0.2–0.3 | 0.2–0.3 | 0.3 | 0.3–0.4 |
S1 | 0.1–0.2 | 0.1–0.2 | 0.2 | 0.2–0.3 | 0.3–0.4 | 0.4–0.5 |
S2 | 0.1–0.2 | 0.1–0.2 | 0.2 | 0.2 | 0.3 | 0.3–0.4 |
S3 | 0.1–0.2 | 0.1–0.2 | 0.2 | 0.2 | 0.3 | 0.3–0.4 |
S4 | 0.1–0.2 | 0.1–0.2 | 0.2 | 0.2–0.3 | 0.3–0.4 | 0.3–0.4 |
S5 | 0.1–0.2 | 0.1–0.2 | 0.2 | 0.2–0.3 | 0.3–0.4 | 0.3–0.4 |
S6 | 0.1–0.2 | 0.1–0.2 | 0.2 | 0.2–0.3 | 0.3–0.4 | 0.3–0.4 |
H1 | 0.1–0.2 | 0.1–0.2 | 0.2 | 0.2 | 0.3 | 0.3–0.4 |
H2 | 0.1–0.2 | 0.1–0.2 | 0.2 | 0.2 | 0.3 | 0.3–0.4 |
H3 | 0.1–0.2 | 0.1–0.2 | 0.2 | 0.2 | 0.3 | 0.3–0.4 |
H4 | 0.1–0.2 | 0.1–0.2 | 0.2 | 0.2 | 0.3 | 0.3–0.4 |
Ø, tuumaa | ||||||
Materiaali | 0.0394–0.1181 | 0.1181–0.1969 | 0.1969–0.3937 | 0.3937–0.7874 | 0.7874–1.1811 | > 1.1811 |
P1 | 0.004–0.008 | 0.004–0.008 | 0.008 | 0.008–0.012 | 0.012–0.016 | 0.016–0.020 |
P2 | 0.004–0.008 | 0.004–0.008 | 0.008 | 0.008 | 0.012 | 0.016–0.020 |
P3 | 0.004–0.008 | 0.004–0.008 | 0.008 | 0.008 | 0.012 | 0.016–0.020 |
P4 | 0.004–0.008 | 0.004–0.008 | 0.008 | 0.008–0.012 | 0.012–0.016 | 0.016–0.020 |
P5 | 0.004–0.008 | 0.004–0.008 | 0.008 | 0.008 | 0.012 | 0.016–0.020 |
M1 | 0.004–0.008 | 0.004–0.008 | 0.008 | 0.008 | 0.012 | 0.016–0.020 |
M2 | 0.004–0.008 | 0.004–0.008 | 0.008 | 0.008 | 0.012 | 0.016–0.020 |
M3 | 0.004–0.008 | 0.004–0.008 | 0.008 | 0.008 | 0.012 | 0.016–0.020 |
K1 | 0.004–0.008 | 0.004–0.008 | 0.008 | 0.008 | 0.012 | 0.020 |
K2 | 0.004–0.008 | 0.004–0.008 | 0.008 | 0.008–0.012 | 0.012–0.016 | 0.016–0.020 |
K3 | 0.004–0.008 | 0.004–0.008 | 0.008 | 0.012 | 0.016 | 0.020 |
K4 | 0.004–0.008 | 0.004–0.008 | 0.008 | 0.012 | 0.012 | 0.020 |
K5 | 0.004–0.008 | 0.004–0.008 | 0.008 | 0.012 | 0.012 | 0.020 |
N1.1 | 0.004–0.008 | 0.004–0.008 | 0.008–0.012 | 0.012–0.016 | 0.016–0.020 | 0.020 |
N1.2 | 0.004–0.008 | 0.004–0.008 | 0.008–0.012 | 0.012–0.017 | 0.016–0.020 | 0.020 |
N1.3 | 0.004–0.008 | 0.004–0.008 | 0.008–0.012 | 0.012–0.018 | 0.016–0.020 | 0.020 |
N1.4 | 0.004–0.008 | 0.004–0.008 | 0.008–0.012 | 0.012–0.019 | 0.016–0.020 | 0.020 |
N2 | 0.004–0.008 | 0.004–0.008 | 0.008–0.012 | 0.012–0.020 | 0.016–0.020 | 0.020 |
N3.1 | 0.004–0.008 | 0.004–0.008 | 0.008–0.012 | 0.008–0.012 | 0.012 | 0.020 |
N3.2 | 0.004–0.008 | 0.004–0.008 | 0.008–0.012 | 0.008–0.012 | 0.012 | 0.016–0.020 |
N3.3 | 0.004–0.008 | 0.004–0.008 | 0.008–0.012 | 0.008–0.012 | 0.012 | 0.016–0.020 |
N3.4 | 0.004–0.008 | 0.004–0.008 | 0.008–0.012 | 0.008–0.012 | 0.012 | 0.016–0.020 |
N4 | 0.004–0.008 | 0.004–0.008 | 0.008–0.012 | 0.008–0.012 | 0.012 | 0.016–0.020 |
S1 | 0.004–0.008 | 0.004–0.008 | 0.008 | 0.008–0.012 | 0.012–0.016 | 0.016–0.020 |
S2 | 0.004–0.008 | 0.004–0.008 | 0.008 | 0.008 | 0.012 | 0.016–0.020 |
S3 | 0.004–0.008 | 0.004–0.008 | 0.008 | 0.008 | 0.012 | 0.016–0.020 |
S4 | 0.004–0.008 | 0.004–0.008 | 0.008 | 0.008–0.012 | 0.012–0.016 | 0.016–0.020 |
S5 | 0.004–0.008 | 0.004–0.008 | 0.008 | 0.008–0.012 | 0.012–0.016 | 0.016–0.020 |
S6 | 0.004–0.008 | 0.004–0.008 | 0.008 | 0.008–0.012 | 0.012–0.016 | 0.016–0.020 |
H1 | 0.004–0.008 | 0.004–0.008 | 0.008 | 0.008 | 0.012 | 0.016–0.020 |
H2 | 0.004–0.008 | 0.004–0.008 | 0.008 | 0.008 | 0.012 | 0.016–0.020 |
H3 | 0.004–0.008 | 0.004–0.008 | 0.008 | 0.008 | 0.012 | 0.016–0.020 |
H4 | 0.004–0.008 | 0.004–0.008 | 0.008 | 0.008 | 0.012 | 0.016–0.020 |
Työkappaleen kiinnitys
- Varmista, että kalvittava työkappale on kiinnitetty asianmukaisesti
- Jos koneistetaan läpireikää, varmista että lastunpoistolle on riittävästi tilaa
- Jos työkappale on ohutseinäinen, varmista että kiinnitysvoimat ovat tasaiset koko kappaleessa
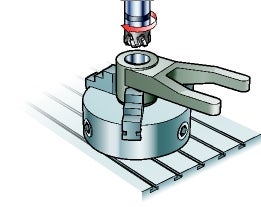
Lastuamisneste kalvinnassa
Lastuamisnesteen syötössä tärkeintä on tuoda nestesuihku suoraan teräsärmään, jolloin terien kestoiästä tulee pitkä ja lastunpoisto on tehokasta.
- Täyskovametallisissa kalvimissa nestesuihku on suorauraisessa mallissa työkalun suuntainen ja kierreuraisessa mallissa sivuttainen
- Emulsiolla saadaan yleensä parempi terien kestoikä kuin öljyllä
- Suositeltava nestepaine on 15 baaria
- Suurempi nestepaine voi olla hyödyllinen lastunhallinnan ja -murron kannalta
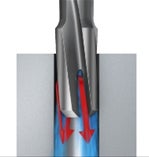
Kierreurat – sivuttaiset nestesuihkut
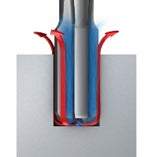
Suorat urat – suorat nestesuihkut
Kalvimen paikoitus
Alkureiän ja kalvimen välisen asentopoikkeaman tulee olla värinöiden välttämiseksi mahdollisimman pieni.
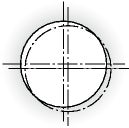
Hakkaava lastuaminen
Kalvimilla voidaan normaalisti koneistaa:
- halkaisijaltaan alle 2 mm:n (0.079 in) risteäviä reikiä, kun kalvinpään halkaisija on alle 22 mm (0.866 in)
- Halkaisijaltaan alle 3 mm:n (0.118 in) risteäviä reikiä, kun kalvinpään halkaisija on 22 mm (0.866 in) tai isompi.
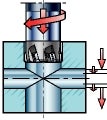
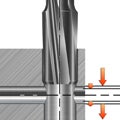
Kaltevat pinnat
Kaltevien pintojen kalvinta:
- Suurin suositeltu sisäänmenopinnan kaltevuus on 5°
- Pidä heitto aina mahdollisimman pienenä
- Pyydä asiantuntijalta ohjeet kovametallikalvinten käyttöön
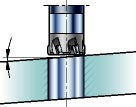
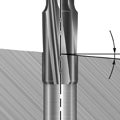
Alkureiän kalvinta
Kalvimalla ei voida korjata alkureiän sijainti- tai suoruusvirheitä.
- Alkureiän suoruustoleranssin tulisi olla alle 0.05 mm (0.002 in).
- Varmista, että alkureiän halkaisija sallii suositellut radiaaliset lastuamissyvyydet.
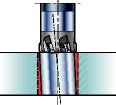
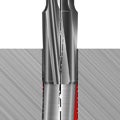
Kalvinta
Kalvinta on viimeistelymenetelmä erittäin tarkkojen reikien koneistukseen moniteräisellä... chevron_right
Viisteiden jyrsintä
Yleisiä työkappaleiden reunoihin tehtäviä koneistuksia ovat viisteet, V-urat, pääteurat,... chevron_right
Viimeistelyavarrus
Hienoavarruksessa viimeistellään olemassa oleva reikä niin, että toleranssi-, sijainti-... chevron_right
Lastuamisnesteen käytössä huomioitavaa
Toisinaan voi olla ympäristö- tai kustannussyistä perusteltua koneistaa ilman lastuamisnestettä.... chevron_right