Miten me teimme sen?
Miten Sandvik valmisti maailman ensimmäisen 3D-tulostetun hajoamattoman kitaran
Rock-tähdet ovat hajottaneet kitaroitaan jo vuosikymmenten ajan, mutta harva heistä on tehnyt sitä niin antaumuksella kuin ruotsalaissyntyinen kitaravirtuoosi Yngwie Malmsteen. Sandvik päätti testata uraa uurtavia tekniikoitaan ja rakentaa maailman ensimmäisen täysmetallisen, rikkoutumattoman kitaran ja antaa sitten Malmsteenin esitellä kitaranhajotustaitojaan tällä luomuksella.
Sandvik kokosi asiantuntijoita ympäri konsernin osoittaakseen, miten sen insinöörit pystyvät hyödyntämään kestävän kehityksen mukaista huipputekniikkaa ja luomaan jotain, joka edellyttää sekä äärimmäistä tarkkuutta että hämmästyttävää kestävyyttä.
"Edistykselliset materiaalit, tarkka koneistus, lisäaineiden valmistus, tieto-ohjattu tuotanto ‒ tällaisia prosesseja vaaditaan luomaan jotain niin monimutkaista ja kaunista kuin mestarimuusikon kitara", sanoo Klas Forsström, President, Sandvik Machining Solutions. "Halusimme kuitenkin myös osoittaa, että pystymme tekemään siitä rikkoutumattoman, vaikka Yngwie yrittää hajottaa sitä miten kovaa tahansa. Tämä projekti tuntui sopivan täydellisesti meidän taitojemme ja kykyjemme testaamiseen ‒ samoin kuin hänen."
Yhteistyötä alusta alkaen
Jo kuukausia ennen Floridan konserttia Sandvik alkoi koota Ruotsissa materiaalien, koneistusprosessien ja lisäainevalmistuksen asiantuntijoita eri puolilta konsernia aivoriiheen siitä, miten haasteeseen vastataan.
Sandvik ei ole koskaan ennen valmistanut kitaraa, joten yritys päätti tehdä yhteistyötä maineikkaan brittiläisen kitaranvalmistajan Drewman Guitarsin kanssa. "Meidän täytyi innovoida ylhäältä alaspäin", Drewmanin suunnittelija Andy Holt kertoo. "Halusimme muusikoiden sanovan, että eivät ole koskaan nähneet tällä tavoin rakennettua kitaraa."
Holt kertoo, että suunnitteluvaiheessa oli sellaisia päiviä, jolloin hän lähetti Sandvikin insinööreille joka päivän uuden design-tiedoston. Läheisessä yhteistyössä ammattimaisen kitaranvalmistajan kanssa päädyttiin lopulta siihen, mistä molempien osapuolten mielestä tuli teknologisen luovuuden mestariteos.
Maailman ensimmäinen hajoamaton kitara
Henrik Loikkanen, koneistusprosessikehittäjä Sandvik Coromantilla, on soittanut kitaraa nuoruudestaan saakka, jolloin hänen idolinaan oli juuri Malmsteen. Hän ei ole kuitenkaan koskaan hajottanut kitaraa ("liian kallista", Loikkanen sanoo). Niinpä Loikkanen kääntyi YouTuben puoleen selvittäessään, mitä oikein tapahtuu, kun Malmsteen rikkoo soittimensa.
"Meidän piti suunnitella kitara, jota ei voi hajottaa millään eri tavalla, jolla kitaran voi nyt ylipäänsä lyödä säpäleiksi", Loikkanen sanoo. "Insinööritaidon suhteen kriittisin kohta oli liitos kitaran kaulan ja rungon välillä, josta kitara helpoiten murtuu." Sandvik Coromantin insinöörien ratkaisu oli poistaa tuo liitos. Sekä kaula että otelauta jatkuivat suorakaiteen muotoiseen "napaan", joka ulottuu syvälle kitaran runkoon.
Yngwie kykenee hallitsemaan sointia paremmin nauhojen välisten otelaudan koverrusten ansiosta. Niinpä insinöörien piti leikata materiaalia pois nauhojen välistä pitkinä, pehmeinä kaarina. Sandvik teki kaulasta ja otelaudasta ontot, jotta kitarasta tuli mahdollisimman kevyt.
"Jokaisen nauhan korkeuden piti sopia täydellisesti, muutoin se kuuluisi läpi, kun kielet koskettavat joitakin nauhoja", Loikkanen sanoo.
Data ja yhteistyö tärkeässä roolissa
Pitkät, hoikat komponentit kuten otelauta ja kaula ovat erityisen herkkiä vääntymään koneistuksessa. Edistyksellisen ohjelmiston ansiosta Sandvik Coromant pystyi simuloimaan työtehtävää digitaalisesti ennen kuin ensimmäinen lastu irtosi työkappaleesta.
"Tarkkuus oli kriittistä", Henrik Loikkanen kertoo. "Ohjelmistomme on rakennettu vuosien kokemuksen perusteella. Se antoi käyttöömme sellaiset työkalut ja lastuamissuositukset, jotka auttoivat meitä jyrsimään otelaudan paikoitellen aina haasteelliseen yhden millimetrin paksuuteen saakka."
Automatisoitu prosessi merkitsi myös sitä, että otelauta voitiin jyrsiä vain yhtä konetta käyttäen. Prosessiin tarvittiin 90 erillistä operaatiota ja se vietiin läpi konetta pysäyttämättä. Sitä ei tehty edes uusien työkalujen tai leikkausten takia.
"Laitat kappaleen raakamateriaalia koneeseen ja ulos tulee valmis osa", Loikkanen sanoo. "Tämä on järkevä tapa poistaa materiaalia. Jaksoajat pienenevät ja osia pystytään tuottamaan pienemmin kustannuksin."
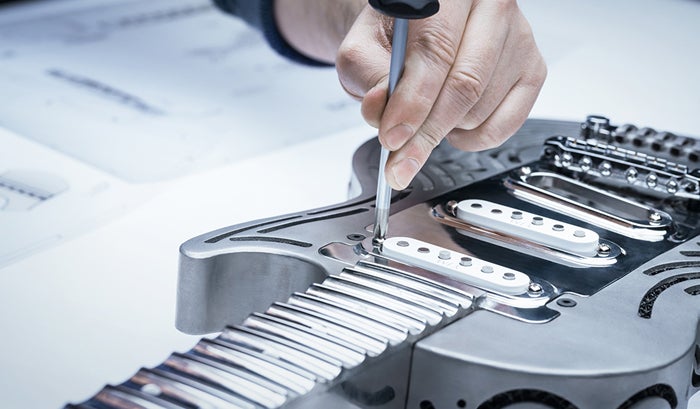
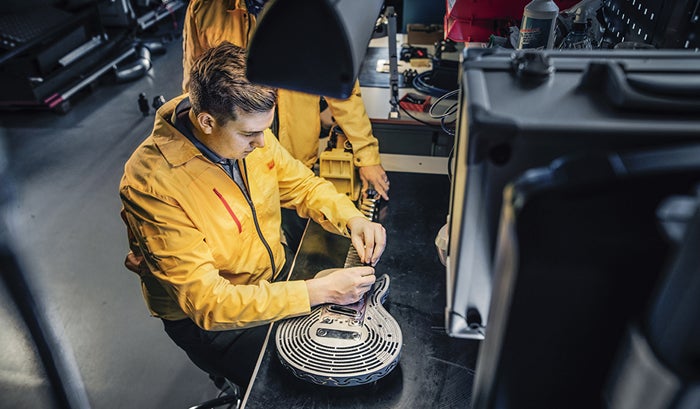
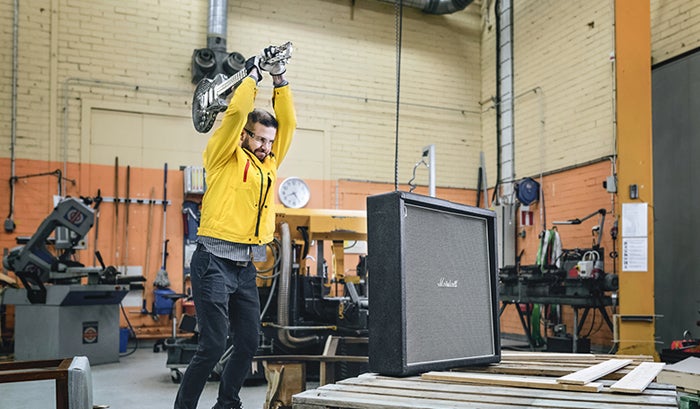
Insinöörit pystyivät tekemään jokaisesta prototyypistä aina edellistä kevyempiä, kunnes lopullinen kitara vihdoin valmistui. CoroMill®-lastuamistyökalut viimeistelivät metallipinnat kauniin sileiksi ja kiiltäviksi.
Loikkasen mukaan juuri yhteistyö Sandvikin muiden divisioonien kanssa tuotti lopputuloksena hajoamattoman kitaran. Hän oli itse auttamassa Sandvik Additive Manufacturing mill -divisioonaa viimeistelemään kitaran rungon ja pienet osat, jotka kaikki oli 3D-tulostettu titaanista. Sandvik Coromant työskenteli myös Sandvik Materials Technology -divisioonan kanssa komponenttiteräksen valintaan liittyvissä kysymyksissä ja hyper-kaksikerrosristikkorakenteen liittämiseksi kaulan sisään. Loikkanen toteaa, että juuri tiimityö oli kitaranvalmistuksen perimmäinen tarkoitus.
"Sandvik Coromant tunnetaan siitä, että se auttaa asiakkaitaan monimutkaisissa tehtävissä ‒ ei pelkästään työkalujen valmistajana, vaan kehittämällä parhaita menetelmiä työkalujemme hyödyntämiseen asiakkaiden prosesseissa", Loikkanen sanoo.