Wie haben wir das gemacht?
Wie Sandvik die weltweit erste 3D-gedruckte, unzerstörbare Gitarre herstellte
Seit vielen Jahrzehnten lieben es Rockstars, ihre Gitarren auf der Bühne zu zerstören. Und kaum jemand zeigt dabei mehr Einsatz als der schwedische Gitarrenvirtuose Yngwie Malmsteen. Daher entschied sich Sandvik, seine innovativen Verfahren in einem ungewöhnlichen Versuch zu testen: Das Unternehmen stellte die weltweit erste unzerstörbare Gitarre vollständig aus Metall her und ließ Malmsteen darauf seine beeindruckenden Fähigkeiten demonstrieren.
Sandvik holte Experten aus dem ganzen Unternehmen an einen Tisch, um zu beweisen, dass man mit nachhaltigen, innovativen Verfahren etwas schaffen kann, das gleichzeitig hochpräzise und unglaublich stabil ist.
„Fortschrittliche Werkstoffe, Präzisionszerspanung, additive Fertigung, datengesteuerte Produktion – all das ist notwendig, um etwas so kompliziertes und schönes wie eine Gitarre für einen genialen Ausnahmemusiker herzustellen“, erklärt Klas Forsström, Präsident von Sandvik Machining Solutions „Aber wir wollten auch zeigen, dass wir sie unzerstörbar machen können, ganz gleich, wie sehr sich Yngwie auch bemühte, sie zu demolieren. Dieses Projekt war perfekt, um unsere Fähigkeiten und Möglichkeiten zu demonstrieren – und seine auch.“
Zusammenarbeit von Anfang an
Schon Monate vor dem Konzert in Florida holte Sandvik Experten für Werkstoffe, Zerspanungsprozesse und additive Fertigung aus dem ganzen Unternehmen an einen Tisch, um zu überlegen, wie die Herausforderung gemeistert werden könnte.
Da bei Sandvik noch niemand eine Gitarre gebaut hatte, arbeitete das Unternehmen mit dem renommierten Gitarrenbauer Drewman Guitars aus Großbritannien zusammen. „Wir mussten im Grunde alles neu erfinden“, sagt Drewman-Designer Andy Holt. „Wir wollten, dass Musiker sagen: ‚Ich habe noch nie eine Gitarre gesehen, die so gemacht ist.‘ “
Holt erinnert sich, dass es im Entwicklungsprozess eine Zeit gab, in der er den Ingenieuren bei Sandvik jeden Tag eine neue Digitaldesign-Datei schickte. So wurde in enger Zusammenarbeit mit dem Gitarrenbauer etwas geschaffen, das beide Seiten als ein Meisterwerk technologischer Kreativität bezeichnen.
Die erste unzerstörbare Gitarre der Welt
Henrik Loikkanen, Zerspanungsprozessentwickler bei Sandvik Coromant, spielte schon als Jugendlicher Gitarre und war schon damals Fan von Yngwie Malmsteen. Aber er hat noch nie eine zerschlagen – „zu teuer“, wie er sagt.Um zu verstehen, was passiert, wenn Malmsteen ein Instrument zerstört, machte sich Loikkanen deshalb bei YouTube schlau.
„Wir mussten eine Gitarre entwickeln, die unzerstörbar ist – egal auf welche Weise man versucht, sie zu zerschlagen“, erklärt Loikkanen. „Die technische Herausforderung war die Verbindung zwischen Hals und Korpus, die meist als erstes bricht.“ Deshalb entschieden sich die Ingenieure bei Sandvik Coromant dafür, einfach auf diese Verbindung zu verzichten. Sowohl der Hals als auch das Griffbrett laufen in einem rechteckigen Mittelstück aus, das weit in den Korpus der Gitarre hineinreicht.
Da Yngwie auf vertieften Bünden spielt, um die Töne noch besser kontrollieren zu können, mussten die Ingenieure zwischen den Bundstäbchen Material in langen, glatten Bögen herausfräsen. Um die Gitarre so leicht wie möglich zu machen, höhlten die Techniker von Sandvik Coromant den Hals und das Griffbrett aus.
„Die Bundstäbchen mussten exakt in gleicher Höhe angeordnet werden, sonst würde man hören, wie die Saiten die Stäbchen berühren“, erläutert Loikkanen.
Daten auf dem neuesten Stand
Lange, schlanke Komponenten wie das Griffbrett und der Hals sind besonders anfällig für Verzug im Zerspanungsprozess. Dank zukunftsweisender Software konnte Sandvik Coromant den Fräsvorgang digital simulieren, bevor der erste Schnitt gemacht wurde.
„Präzision war das A und O“, erklärt Henrik Loikkanen. „Unsere Software basiert auf jahrelanger Erfahrung. Sie liefert Empfehlungen zum Werkzeug und zu den Schnittdaten, mit deren Hilfe wir den Gitarrenhals an einigen Stellen bis auf eine Dicke von nur einem Millimeter fräsen konnten.“
Dank des automatisierten Prozesses konnte das Griffbrett außerdem auf einer einzigen Maschine gefräst werden. Der Prozess erforderte insgesamt 90 separate Arbeitsschritte. Er wurde durchgeführt, ohne die Maschine anzuhalten, um neue Werkzeuge oder Schnitte einzurichten.
„Man steckt ein Stück Rohmaterial hinein, und ein fertiges Bauteil kommt heraus“, so Loikkanen. „Das ist eine viel intelligentere Methode, um Material zu entfernen. Man kann die Zykluszeiten verkürzen und Bauteile kostengünstiger herstellen.“
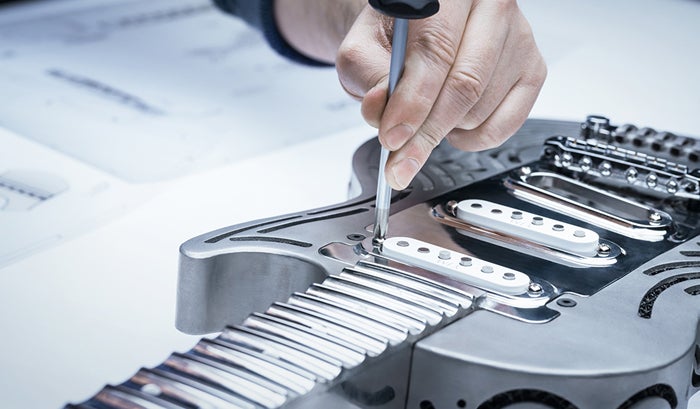
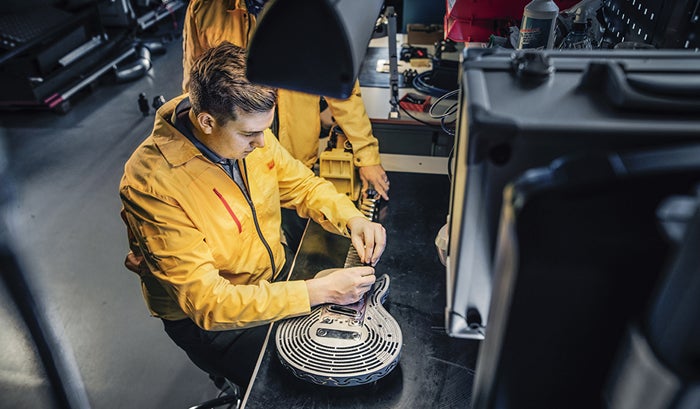
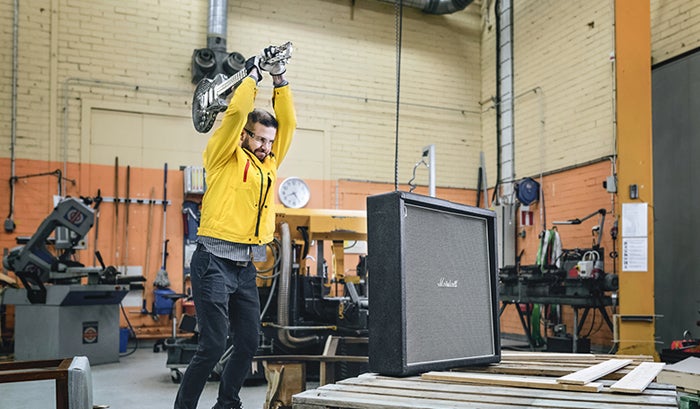
Die Ingenieure von Sandvik konnten jeden neuen Prototyp leichter machen als seinen Vorgänger – bis schließlich die endgültige Gitarre produziert wurde. Feine CoroMill® Zerspanungswerkzeuge sorgten schließlich für eine schöne glatte und glänzende Oberfläche des Metalls.
Laut Loikkanen war die Zusammenarbeit mit anderen Sandvik Geschäftsbereichen bei der Herstellung der unzerstörbaren Gitarre ein Schlüsselfaktor für den Erfolg. Beispielsweise konnte er Sandvik Additive Manufacturing beim Fräsen der Oberflächen für den Gitarrenkorpus und die kleinen Bauteile helfen, die alle im 3D-Druck aus Titan gefertigt wurden. Außerdem arbeitete Sandvik Coromant mit Sandvik Materials Technology zusammen, um den Stahl auszuwählen und eine Gitterstruktur aus Hyper-Duplexstahl im Inneren des Halses unterzubringen. Loikannen ist davon überzeugt, dass die Teamarbeit der eigentliche Zweck dieses Gitarrenprojekts war.
„Sandvik Coromant ist bekannt dafür, seinen Kunden bei komplexen Aufgaben zu helfen – nicht nur mit der Bereitstellung von Werkzeugen, sondern auch bei der Entwicklung bestmöglicher Methoden, um unsere Werkzeuge in ihren Prozessen einzusetzen“, erklärt Loikkanen.