How efficiency boosts throughput and output
The throughput approach: Machining efficiency x Utilization x Lead times
At the heart of this search lies a simple idea: optimization. Let’s break it down:
Machining efficiency
Cutting chips, not time—efficiency means keeping machines running, cutting chips, and minimizing downtime. The longer your machines are cutting rather than idling, the greater the overall output. It’s about ensuring that each second is used productively, with reduced interruptions.
Equipment utilization
Maximizing machine potential—idle machines mean missed opportunities, and by fully utilizing CNC mills, lathes, or laser cutters, you tap into their full capabilities. The more you increase utilization, the more you can achieve in a given timeframe, driving throughput to new heights.
Lead times
Swift transitions—quick, seamless transitions between design, material sourcing, machining, and post-processing minimize delays and improve throughput. Reducing downtime between stages ensures smoother operations and improves the workflow.
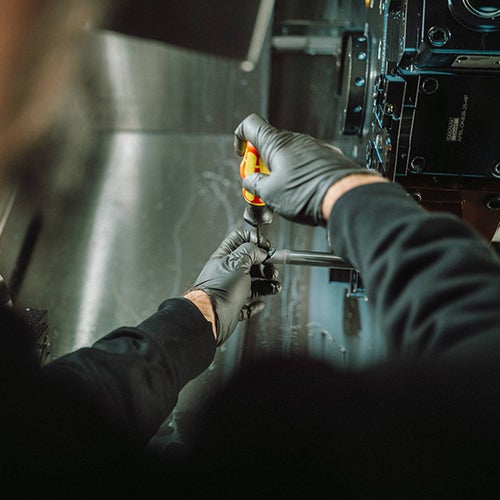
The value chain impact
Total output is an affect of everything that happens across the manufacturing value chain. Waste in the industry is massive – only a small part of resources spent are converted into valuable output.
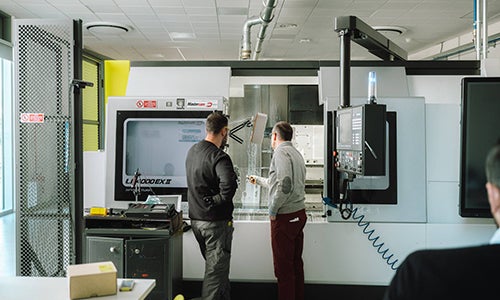
Investing in new machines
The smartest move in a fast world. As technology races ahead, workshop managers face complex orders. With global competition heating up, efficiency is key, and future-proofing your production is a must. Read more about Sandvik Coromant's machine investment offer here
Explore related solutions
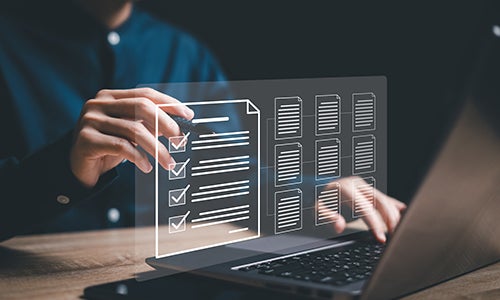
Access data and best practice
Utilize knowledge and competence to shorten lead times and optimize process.