Karbon fiber bazlı kompozit malzemelerin üretim hattındaki büyük zorluklara rağmen daha hafif araç araştırmalarında önemli bir rol oynaması beklenmektedir.
Daha sıkı çevre talepleri ve gelişen şehirlerde sürekli artan araç kullanımı otomobil endüstrisinin yeni yöntemlerle düşünmesini gerektirmiştir. Hedef; hibrid veya tamamen elektrikli araçlar formunda hafif ağırlığa sahip yeni gövde şekilleri ve uzun akü ömrüdür.
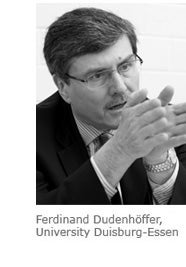
En geç 2014'e kadar neredeyse tüm araç üreticileri hibrid araçları piyasaya sunmaya başlayacaktır ve bu daha sadece başlangıç olacaktır. Almanya Duisburg-Essen Üniversitesi'nde profesör ve Otomotiv Araştırma Merkezi'nin başında olan Ferdinand Dudenhöffer teknolojide bir değişimden bahsediyor.
“2025'e kadar sadece yakıt ile çalışan araçların küresel payı yüzde 35'e düşecektir,” diyor.
Başka bir tahmin de 10 yıl içerisinde her yıl yaklaşık 24 milyona yakın hibrid veya elektrikli aracın satılacağını öngörüyor. Dudenhöffer bu düşüncenin de muhafazakar olduğunu söylüyor. Ancak tüm araç üreticileri aynı problemle boğuşacak – ağırlık. Bir akü takıldığında sadece elektrikle çalışan bir aracın ağırlığı yaklaşık 250 kilogram artar, prizi üstünde bir hibrid araç için için bu değer 200 kilogramdır.
Volvo Cars olası bir çözüm üzerinde çalışıyor. Londra Kraliyet Koleji'nin (Londra Imperial College) Havacılık Departmanındaki araştırmacılar ile birlikte Göteborg, İsveç'deki mühendisler enerji şarj etme ve saklama özelliğine sahip karbon fiber ve polimerden oluşan bir kompozit malzeme geliştirdiler. Buradaki amaç gelecekteki Volvo aracının gövdesinin elektrokimyasal bir akü olarak görev yapmasıdır. Peki bu çözüm ne kadar uzak?
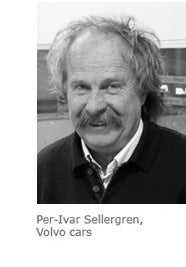
Volvo Cars Malzeme Merkezi'nde geliştirme mühendisi olan Per-Ivar Sellergren bu konuda iyimser. “Eğer her şey plana uygun giderse 2012'nin sonuna kadar araç bagajı şeklinde bir prototip yapacağız,” diyor. Maliyet tabi bir problem, ancak Sellergren, halen çelik ve alüminyumdan çok daha pahalı olmasına rağmen, geleceğin elektrikli ve hibrid araçlar için kompozit malzemelerde olduğunu düşünüyor.
Volvo'nun hesaplarına göre yeni akü malzemesinden yapılacak bir kaputun maliyeti orijinal kaput artı lityum-iyon akününkine eşit olacak. O, “Üreticiler olarak karbon fiber kaput için küçük bir miktar ekleyebiliriz, çünkü aslında akü için maliyet olmayacaktır" diyor.
Volvo Cars’da kompozit uzmanı Ulf Carlund'a göre şu ana kadar üretim yöntemleri çok yavaş kaldı ve geleneksel otomotiv fabrikalarında yapılan yatırımların kullanılması gerekiyordu. Bunun nedeni kısmen geleneksel çelik kullanan otomotiv üreticilerinin kompozitler ile düşünmesinin ve çalışmasının zor olmasıydı. Ancak, Volvo uzmanlarına göre değişim için büyük bir istek var ve insanlar yeni araçların içinde ve dışında her geçen gün daha fazla polimer malzeme görecek.
Audi, alüminyum araç A2'ye sahip olmanın üstünlüğü ile hafif araç üretiminde önderdir. Firmanın Güney Almanya'daki “hafif ağırlık” merkezinde Audi mühendisleri iştiraklerinden olan Lamborghini tarafından kullanılan karbon fiber teknolojisi ile birlikte ana firma Volkswagen’in lüks Bugatti modeli tarafından geliştirilen kompozit teknolojisi/uzmanlığını kullanmaktadır.
Audi 120.000 euro üzerinde maliyete sahip olan ve günde sadece 15–20 adet üretilen Audi R8 Spyder spor araçta tavan kutusunun üzerinde ve her iki tarafta karbon fiber takviyeli polimer kullanmaktadır. Daha ucuz seri üretilen araçlarda bunu daha tasarruflu hale getirebilecek bir ön koşul çok sayıda alüminyum parçanın tek bir karbon fiber parça ile değiştirilebilecek olmasıdır. “Beş veya altı kalıp yerine sadece tek bir kalıba ihtiyacınız olacak,” diyor Audi Leichtbauzentrum'de geliştirme mühendisi olan Karl Durst.
Burada diğer projelerle birlikte alüminyuma karşı olan ağırlık avantajını yüzde 17-18'lerden yüzde 25'e çıkarmak için fiberler kompozit malzemeler şeklinde paketleniyor. Proje alüminyum ile aynı çekme ve pres ağırlığı yük özelliğine sahip bir malzemeyi kullanmaktadır. Buna rağmen halen çözülmesi gereken küçük ve büyük problemler olduğunu söyleyen Durst bunlardan birinin de kompozitler ile diğer malzemeler arasındaki korozyon olduğunu belirtiyor. Bir de gürültü faktörü var. Aracın hafif hale gelmesi için düşürülen her kilogram için gürültü seviyesi artar ve yalıtım gerekir, bu da daha fazla ağırlık eklenmesi anlamına gelir. Başka bir zorluk da araç teknikerlerinin malzemeyi tanıması olacaktır. “Dünyanın herhangi bir yerindeki en küçük Audi servisinde bile aracın tamiri ve kompozit araç parçalarının değiştirilmesi mümkün olmalı,” diyor Durst.
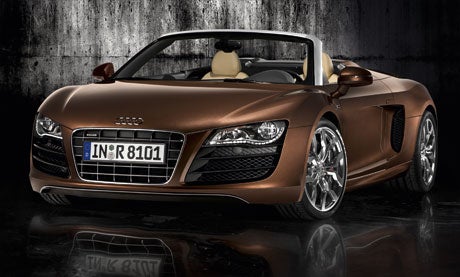
Audi R8 Spyder spor araç tavan kutusunun üzerinde ve her iki tarafta karbon fiber takviyeli polimer kullanmaktadır.
Üretim prosesinin iyileştirilmesi gereklidir. Alman makine üreticisi Voith’in iştiraki olan Voith Composites'in genel müdürü Lars Herbeck birçok alanda büyük ihtiyaç olacağını öngörmektedir. Bunlaradn biri malzemeler için optimum akış prosesi, diğeri ise yılda 100.000 parçanın üzerinde hızlı üretim ile birlikte çok daha hızlı çevrim süresidir. Bir saniye içerisinde üretilebilen alüminyum parçalar ile karşılaştırıldığında büyük kompozit parçaların üretimi 20 dakika ile bir saat arasında sürebilir. Bu havacılık endüstrisi için uygun olabilir, ancak dünya çapında yılda 55 milyon aracın üretildiği otomotiv endüstrisinin büyük ölçekli montaj hatları için uygun olmayacaktır.
Pfintzal, Almanya'da Fraunhofer-Institut für Chemische Technologie enstitüsünde kompozit malzemeler departmanında araştırmacı olarak çalışan Oliver Geiger birçok sektörde büyük şirketler ile birlikte çalışmanın yollarını arıyor. Audi’de Durst ise daha yavaş evrimsel gelişmeler yerine teknolojide ileri doğru bir sıçrama olması gerektiğinden bahsediyor.
2004 yılından beri SLR McLaren yarış arabasında karbon fiber kullanan Daimler de teknolojinin geliştirilmesine yoğunlaşmış durumda. Nisan 2010'da dünyanın önde gelen karbon fiber üreticisi olan Japon kimya şirketi Toray ile işbirliği başlattı. Amaç üç yıl içerisinde şirketin yılda ortalama 20.000 ile 40.000 arasında üreteceği modeller için karbon fiberden yapılmış parçalar geliştirmek.
Bu sırada ezeli rakip BMW ise çok daha cesur. BMW Alman ortağı SGL Carbon ile Amerika Birleşik Devletleri'ndeki Moses Lake, Washington'da kompozit fabrikasına 100 milyon dolar yatırım yapıyor. BMW Finans Başkanı Friedrich Eichiner'e göre fabrika ilk kez “rekabetçi fiyatlarda yüksek hacimler” üretebilecek. Amaç şu anda yarış arabalarında kullanılan ve kilogram maliyeti 22 ile 55 USD arasında olan karbon fiberin mevcut fiyatını yarıya indirmek.
Karbon fiber her biri yılda 1.500 ton kapasiteye sahip iki hatta üretilecek ve tek bir şarj ile 100 kilometrenin üzerinde menzile sahip, 35 kWh lityum akü kullanan dört koltuklu bir hatchback olan BMW'nin yeni elektrikli aracı Megacity Vehicle'da kullanılacak. Ek bir küçük dizel motora ve iki elektrikli motora sahip bir spor araç versiyonu saatte 200 kilometre hızın üzerine çıkabilecek özelliklere sahip olacak.
Megacity'nin BMW'nin 400 milyon euro'nun üzerinde yatırım yaptığı Leipzig'deki üretim hatlarından 2013–2014 yılında çıkması bekleniyor. BMW'ye göre bu, alüminyum bir şasi üzerinde tamamen hafif karbon fiberden üretilen yolcu alanına sahip dünyadaki ilk seri üretilen araç olacak. BMW tarafından yayınlanan ilk çizimler coupe'nin tabanına bir yatak gibi yerleştirilmiş akü, büyük ölçülü tekerlekler ve dinamik, hatta agresif görüntüsü ile aracın bir bilimkurgu filmden çıkmış olduğu hissini uyandırıyor.
Kalan tek şey baskı altında olan bir endüstride bunun fabrika zemininde olan etkisini görmek olacaktır. “Bu bir kumar,” diyor BMW’nin rakiplerinden birinde çalışan bir hafif ağırlık uzmanı.
Yönetici Norbert Reithofer de risklerin farkında. Ekim 2010'da Nürnberg'de gerçekleşen bir otomotiv konferansında şunları söyledi: “Bu teknoloji ile ilk üretim döngüsünde para kazanmama ihtimalimiz var, ancak sonrasında geleneksel teknikler tarafından desteklenecektir.”
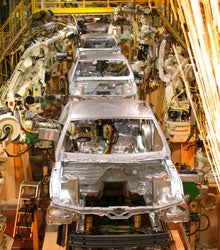
Geleceğin araçları için montaj hatlarında üretim de önemli bir zorluk teşkil ediyor.
2025 yılına kadar
24
milyon hibrid veya elektrikli araç satılacak.
Tahminlere göre 2025 yılına kadar yeni araçların sadece
%35'i
yakıt ile çalışacaktır.
Karbon fiber
Havacılık ve otomotiv endüstrilerinde kullanılan kompozitler çoğunlukla karbon fiber ile takviye edilmiş epoksi veya vinilesterden üretilmektedir. Bu kompozitlerin avantajları düşük ağırlıkları ve yüksek gerginlikleri gibi mekanik özellikleri olacaktır. Karbon fiberler kolayca ayrılabilir, ancak yüksek miktarda enerji soğurmak için de şekillendirilebilir. Bu yüksek hızlarda doğrudan çarpışma tehlikesi yüksek olan yarış arabalarında gereklidir.
Daha az gelişmiş fiber takviyeli plastikler de araba endüstrisinde uzun zamandır kullanılmaktadır. Eski Doğu Almanya'da 3 milyondan fazla Trabant, Sovyetler Birliği pamuğu ve kimyasal fabrikalardan gelen fenollü reçineden oluşan duroplastikten yapılmıştı.
TEKNİK BAKIŞ
Çok fazla belirsizlik
Havacılık endüstrisindeki kompozitler zaten büyüyen bir pazar. Sandvik Coromant PCD (polikristalin elmas) ve karbür matkaplar dahil olmak üzere bu alanda sunabileceği çok sayıda takım çözümüne sahiptir. Otomotiv endüstrisinde ise kompozitlere nasıl bir ihtiyaç olabileceği konusunda çok fazla belirsizlik bulunuyor.
Karbon fiber teknolojisi mevcut durumda zaten Formula-1 yarış arabalarında ve pahalı lüks spor araçlarda kullanılmaktadır. Ancak bunlar düşük miktarda ve az çok el ile üretilen araçlardır.
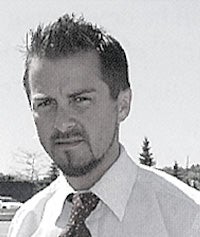
“Seri üretim söz konusu olduğunda halen araştırma ve geliştirme aşamasındayız,” diyor Sandvik Coromant'da kompozit geliştirme üzerine çalışan Francis Richt. “Ancak elektrikli ve hibrid araçların ağırlığını azaltmak için kullanılan bu yeni malzemeye güveniyoruz.” Richt; kalite için yüksek gereksinimler ve kompozitler ile birlikte titanyum gibi diğer malzemelerin eş zamanlı olarak işlenmesi nedeniyle, havacılık endüstrisindeki cihazların araçlardakine göre çok daha kompleks olduğunu ekliyor.
“Arabaların uçaklara göre daha homojen bir yapıya sahip olduğunu biliyoruz, bu da örneğin binlerce delik delme ve geniş alanları frezeleme gibi ihtiyaçları azaltıyor,” diyor Richt. “Diğer taraftan da başka delikler veya kaviteler açmaya da hazır olmak gerekiyor. Yine de çok gelişmiş havacılık endüstrisine göre otomotivde başka talepler görüyoruz.”
Bugün araba endüstrisinde kullanılabilecek takımlar mevcut. Örneğin bazı Sandvik Coromant CoroDrill matkaplar delik kalitesini ve kullanıcıların tezgahlarının performansını artırmak için elmas bir yüzeye sahiptir.
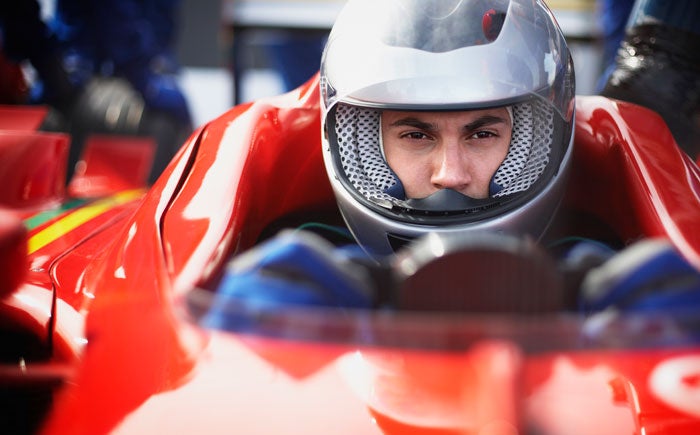
Kompozitler bhali hazırda Formula-1 yarış arabalarında kullanılmaktadır. Buradaki zorluk tekniği özel arabaların seri üretiminde kullanmak.
Bir araç gövdesi nasıl bir aküye dönüştürülür
Daha hafif elektrikli araçlar için Volvo Cars’ın çözümü basit: Ağır aküler kullanmak yerine şirket aracın gövdesinin tamamını bir aküye dönüştürmeyi umut ediyor. Bu 250 kilograma kadar ağırlık tasarrufu sağlayabilir ve elektrikli araçların gerçek olması için her kilogram çok önemli. Bu yeni tekniğin merkezinde ise yeni kompozit malzemelerin kullanılması bulunuyor. İşte çözümün çalışma prensibi:
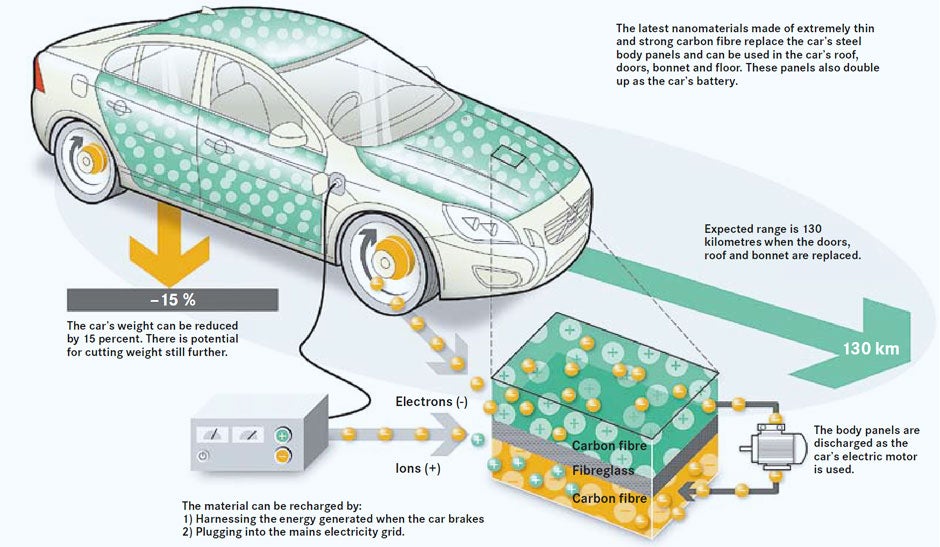
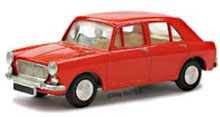