Problemas e soluções em torneamento
Controle de cavacos
Cavacos emaranhados, longos e contínuos em volta da ferramenta ou das peças. Normalmente gerados pelo baixo avanço e profundidade de corte baixa e/ou rasa.
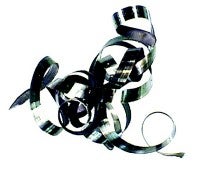
Causa | Solução |
|
|
|
|
|
|
|
|
Controle de cavacos
Cavacos muito pequenos, que geralmente grudam, devido à quebra de cavacos ser muito difícil.
A difícil quebra de cavacos geralmente resulta na redução da vida útil da ferramenta ou até na quebra de pastilhas, devido à alta carga de cavacos sobre a aresta de corte.
Causa | Solução |
|
|
|
|
|
|
Acabamento superficial
A superfície apresenta irregularidades e não atende às exigências de tolerância.
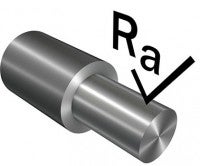
Causa | Solução |
|
|
|
|
|
|
Formação de rebarbas
A formação de rebarbas na peça ao entrar ou sair da peça.
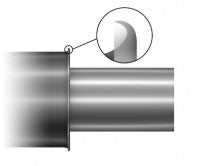
Causa | Solução |
|
|
|
|
|
|
Vibração
Forças de corte radiais altas devido à vibração ou marcas de trepidação causadas pela ferramenta ou pela instalação da ferramenta. Comum em usinagem interna com barras de mandrilar.
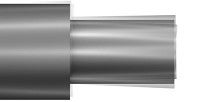
Causa | Solução |
|
|
|
|
|
|
|
|
Vibração
Forças de corte radiais altas.
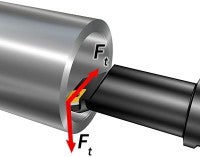
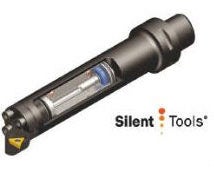
Causa | Solução |
|
|
|
|
|
|
|
|
|
|
Desgaste da pastilha
Para obter dados de corte otimizados, a melhor qualidade possível da peça e melhor vida útil da ferramenta, lembre-se sempre de verificar a aresta de corte/pastilha após a usinagem. Use esta lista de causas e soluções para diferentes padrões de desgaste da pastilha como uma referência para um torneamento bem-sucedido.
![]() Desgaste de flanco |
|
|
Desgaste tipo entalhe ![]() |
|
|
Craterização ![]() |
|
|
![]() ![]() Deformação plástica |
|
|
Arestas postiças (B.U.E) ![]() |
|
|
Escamação ![]() |
|
|
Lascamento na aresta ![]() |
|
|
Tricas térmicas ![]() |
|
|
Quebra ![]() |
|
|
Fratura em camadas - cerâmica ![]() |
|
|
Lascamento fora da zona de corte ![]() |
|
|
Problemas e soluções
Superfície insatisfatória Use uma ferramenta estável e curta Remova os cavacos... keyboard_arrow_right
Problemas e soluções
As dicas sobre problemas e soluções em fresamento como vibração, entupimento por... keyboard_arrow_right
Problemas e soluções
A observação cuidadosa da pastilha/aresta de corte após a usinagem pode ajudar a... keyboard_arrow_right
Dicas de aplicação para torneamento de roscas
Um problema comum no torneamento de roscas são os cavacos enroscarem em robôs, mandris,... keyboard_arrow_right