Jak została zrobiona?
Firma Sandvik stworzyła pierwszą na świecie gitarę wytworzoną z użyciem metod drukowania przestrzennego w pełni odporną na uderzenia
Gwiazdy rocka od dziesięcioleci niszczą gitary na scenie, ale niewielu robi to z większym entuzjazmem niż szwedzki wirtuoz gitary, Yngwie Malmsteen. Firma Sandvik zdecydowała się w niecodzienny sposób przetestować swoje najnowsze rozwiązania techniczne. Stworzyła pierwszą na świecie, wykonaną w całości z metalu gitarę, której nie da się złamać, a następnie pozwoliła Malmsteenowi spróbować swoich sił w dziele zniszczenia.
Chcąc pokazać, w jaki sposób inżynierowie firmy Sandvik mogą wykorzystać zrównoważone, najnowocześniejsze techniki do wykonania przedmiotu, który byłby zarazem bardzo precyzyjny i zdumiewająco trwały, w przedsięwzięcie zaangażowano ekspertów z różnych działów firmy.
– Zaawansowane materiały, precyzyjna obróbka skrawaniem, wytwarzanie addytywne, produkcja sterowana danymi – oto procesy konieczne do stworzenia przedmiotu tak skomplikowanego i pięknego jak gitara przeznaczona dla wirtuoza – mówi Klas Forsström, prezydent Sandvik Machining Solutions. – Chcieliśmy także pokazać, że jesteśmy w stanie stworzyć przedmiot, którego nie da się połamać bez względu na to, jak bardzo Yngwie będzie starał się go zniszczyć. Ten pomysł wydawał się idealnie dostosowany do umiejętności i potencjału – naszych i jego.
Współpraca od samego początku
Kilka miesięcy przed koncertem na Florydzie, firma Sandvik zorganizowała w Szwecji spotkanie zatrudnionych w różnych działach specjalistów w dziedzinach, takich jak inżynieria materiałowa, procesy obróbki wiórowej i drukowanie przestrzenne, aby wspólnie zastanowić się nad tym, jak sprostać temu wyzwaniu.
Ponieważ firma Sandvik nigdy wcześniej nie produkowała gitar, zdecydowano się na współpracę z renomowanym producentem tych instrumentów, firmą Drewman Guitars z Wielkiej Brytanii. – Musieliśmy wykonać projekt całkowicie innowacyjny – przyznaje Andy Holt, projektant firmy Drewman. – Chcieliśmy, aby muzycy mówili: „Nigdy nie widziałem gitary wykonanej w ten sposób”.
Holt mówi, że w trakcie etapu projektowania był okres, gdy codziennie drogą elektroniczną wysyłał do inżynierów z firmy Sandvik nową wersję dokumentacji. W ścisłej współpracy z producentem gitar stworzono coś, co okazało się w opinii obu stron arcydziełem myśli technicznej.
Pierwsza na świecie niezniszczalna gitara
Henrik Loikkanen, inżynier technolog ds. obróbki skrawaniem w firmie Sandvik Coromant, gra na gitarze odkąd były nastolatkiem, kiedy to jego idolem był Malmsteen. Sam jednak nigdy nie roztrzaskał żadnej gitary (gdyż – jak wyjaśnia – były na to za drogie). Aby prześledzić, jak Malmsteen niszczy instrumenty, Loikkanen korzystał z serwisu YouTube.
– Musieliśmy zaprojektować gitarę, której nie można połamać w żaden możliwy sposób – mówi Loikkanen. – Wyzwaniem dla inżynierów było uporanie się z krytycznym, bo najczęściej pękającym elementem gitary, którym jest połączenie między korpusem a gryfem. Dlatego też inżynierowie firmy Sandvik zdecydowali się wyeliminować to połączenie. Prostopadłościenna, sięgająca daleko w głąb korpusu gitary, centralna jego część stała się przedłużeniem gryfu i podstrunnicy.
Ponieważ wgłębienia na gryfie umożliwiają Yngwiemu lepszą artykulację określonych dźwięków, inżynierowie musieli wyciąć długie, łagodne łuki między progami. Aby gitara była jak najlżejsza, w firmie Sandvik Coromant wydrążono wewnętrzne powierzchnie gryfu i podstrunnicy.
– Wysokość każdego progu musiała być idealnie dostosowana, aby wprawione w drgania struny nie stykały się z progami samoczynnie – mówi Loikkanen.
Bezcenne informacje
Długie, smukłe elementy, takie jak gryf i podstrunnica, są szczególnie podatne na odkształcenia w procesie obróbki. Zaawansowane oprogramowanie umożliwiło firmie Sandvik Coromant dokonanie cyfrowej symulacji zadania przed przystąpieniem do skrawania.
– Decydujące znaczenie miała precyzja – mówi Henrik Loikkanen. – Nasze oprogramowanie powstało na podstawie wieloletnich doświadczeń.Dostarczyło ono wskazówek dotyczących doboru narzędzi i parametrów skrawania, które pomogły nam w pokonaniu wyzwania, jakim było frezowanie podstrunnicy mającej miejscami grubość jednego milimetra.
Automatyzacja procesu oznaczała także, że frezowanie podstrunnicy mogło zostać wykonane na pojedynczej obrabiarce. Proces wymagający wykonania 90 osobnych operacji został zrealizowany bez zatrzymywania obrabiarek w celu ustawienia nowych narzędzi i wykonania przejść testowych.
– Wkładasz nieobrobiony kawałek materiału, a otrzymujesz gotowy przedmiot – mówi Loikkanen. – To bardziej inteligentny sposób na usuwanie naddatku. Można skrócić czas cyklu i obrabiać przedmioty mniejszym kosztem.
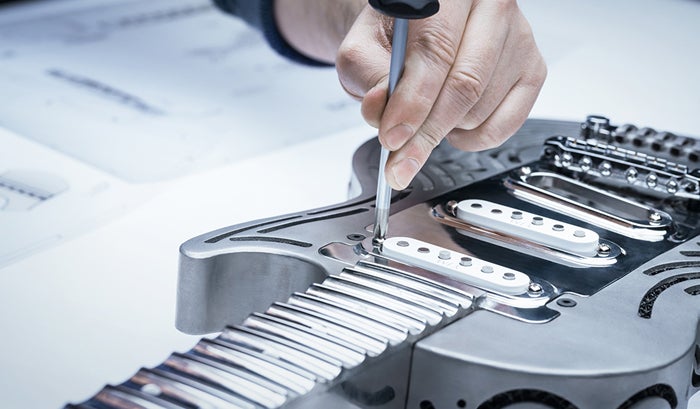
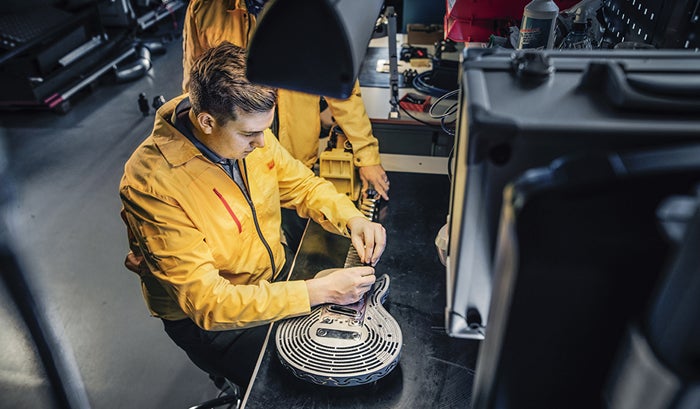
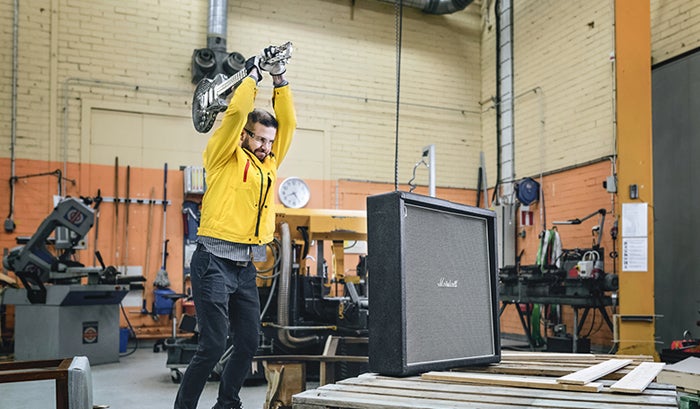
Inżynierowie byli w stanie sprawić, że każdy kolejny prototyp był lżejszy od poprzedniej wersji, aż do uzyskania ostatecznego kształtu gitary. Narzędzia frezarskie CoroMill® do obróbki wykończeniowej sprawiły, że wykończone powierzchnie metalu cechują się gładkością i pięknym połyskiem.
Loikkanen twierdzi, że współpraca z innymi działami firmy Sandvik była kluczem do stworzenia tak odpornej na uderzenia gitary. Udało mu się wspomóc dział firmy Sandvik zajmujący się wytwarzaniem addytywnym we frezowaniu wykończeniowym korpusu gitary i małych elementów, które zostały bez wyjątku wykonane z udziałem metod drukowania przestrzennego przy użyciu tytanu. Sandvik Materials Technology razem z Sandvik Coromant pracowały także nad wyborem stali do produkcji gryfu i zintegrowaniem struktury kratownicowej wykonanej ze stali typu hyper-duplex w jego wewnętrzu. Jak twierdzi, prawdziwym celem wykonania gitary była praca zespołowa.
– Jako firma Sandvik Coromant słyniemy z tego, że pomagamy naszym klientom w realizacji złożonych zadań – nie tylko jako dostawca narzędzi, lecz także jako twórcy najlepszych metod wykorzystania naszych narzędzi w procesach klienta – podsumowuje Loikkanen.