Fabriek van de toekomst
De gereedschapsfabriek van Sandvik Coromant in Gimo (Zweden) is door het Wereld Economisch Forum aangemerkt als een geavanceerde Industry 4.0-faciliteit.
De gereedschapsfabriek van Sandvik Coromant in Gimo (ten noorden van Stockholm) is een sterk geautomatiseerde faciliteit die de vele voordelen van een digitaal verbonden productie volledig omarmt. Dit is onlangs bevestigd door het Wereld Economisch Forum, dat Gimo aangemerkt heeft als een van zijn wereldwijde “lighthouse”-locaties. Elk ‘lighthouse’ is gekozen op basis van een onderzoek bij meer dan 1000 productievestigingen. Hierbij is gekeken naar de mate van succes bij het toepassen van digitale technologieën en het presenteren van tastbare voordelen.
Volgens het Wereld Economisch Forum heeft de fabriek in Gimo een digitale draad door zijn productieprocessen gevlochten waardoor de productiviteit aanzienlijk is gestegen. Een voorbeeld is de ‘contactloze wisseling’, waarbij ontwerppatronen automatisch verwisseld worden, zelfs tijdens onbemande diensten. Dergelijke uitmuntende verbeteringen betekenen dat Gimo nu onderdeel wordt van het wereldwijde netwerk van ‘lighthouses’. Het gaat zijn deuren openen voor en kennis delen met andere productiebedrijven.
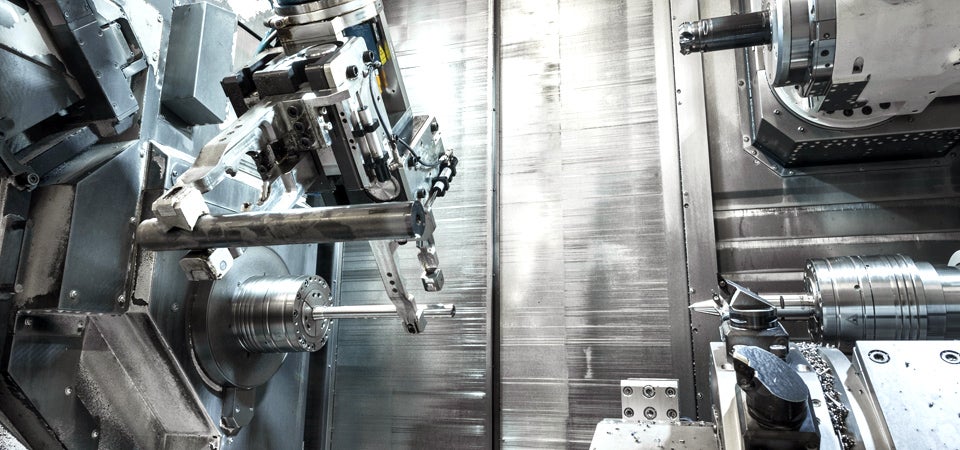
Gimo heeft volgens Lars Matiasson, directeur ‘Production Technology Tools’ bij Sandvik Coromant, vol trots op deze award gereageerd, met name omdat dit het hoogtepunt vormt van alle langdurige inspanningen om innovatie te stimuleren: “De digitaliseringsreis hier in Gimo is feitelijk 30 jaren geleden begonnen met de invoering van parametrische CAD/CAM. En enkele jaren later hebben we dat gekoppeld aan onze slimme automatisering, waarbij we de eerste digitale draad in onze productie creëerden. Het was eerder een evolutie dan een revolutie.”
“Nu zien we een digitale draad door de fabriek lopen: van voorraadbeheer helemaal tot aan machinebewerkingen en voorspellend onderhoud. Deze innovatiegeest heeft altijd een top-downkarakter gehad. De directeuren en managers in Gimo hebben de technici altijd gestimuleerd anders te denken en het veranderingsproces voort te stuwen. Uiteindelijk heeft centraal gestaan hoe technologie gebruikt kan worden om de efficiëntie te verbeteren en de concurrentiepositie van de fabriek te versterken. Dat heeft op zijn beurt weer bijgedragen aan een duurzame toekomst.”
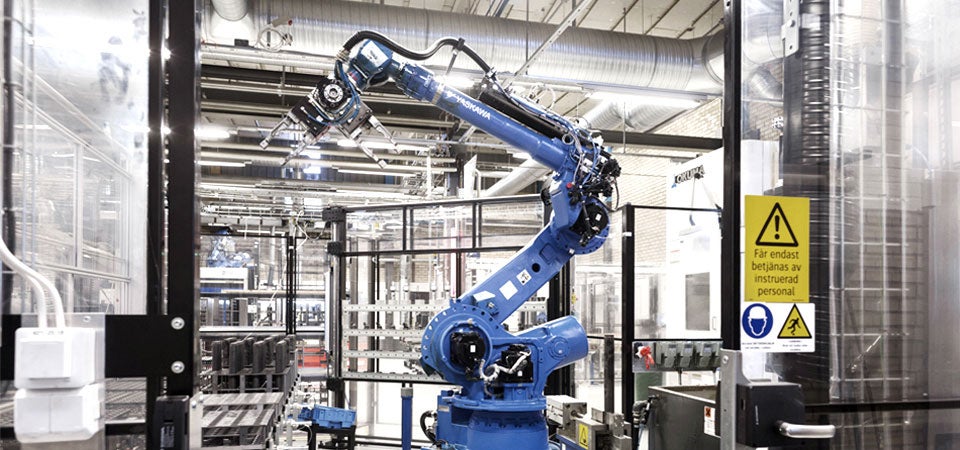
De contactloze wisseling is een goed voorbeeld. Historisch gezien moesten ontwerppatronen altijd handmatig verwisseld worden, waarbij operators uit de dagdienst de machines gereedmaakten voor ’s avonds en ’s nachts. Dit kostte tijd en middelen en beperkte de flexibiliteit tijdens onbemande diensten. Het alternatief was investeren in slimme automatisering met ultraflexibele robots, machines, gereedschappen en opspanningen die gezamenlijk en zonder menselijk toezicht de complexe contactloze wisseling konden uitvoeren.
“Men heeft het over lean productiemethoden zoals de 1-minuutwisseling van matrijzen, maar we wilden verdergaan dan dat. We wilden onbemande instelling”, aldus Matiasson.
“Het was een leercurve. De eerste geautomatiseerde cel werkte niet zo goed als we hadden gehoopt. In feite was hij zelfs minder efficiënt dan de combinatie van één operator en één machine. Maar zo gaat dat bij digitalisering: je moet van je fouten kunnen leren. Geleidelijk aan begonnen we aanzienlijke vooruitgang te boeken en konden de robotcellen de efficiëntie realiseren die we nodig hadden. Trial-and-error is belangrijk om beter te worden.”

Digitale technologieën worden in Gimo ook gebruikt voor verbeteringen op andere terreinen, zoals onderhoud. In toenemende mate worden sensoren aangebracht op een grote verscheidenheid aan apparatuur in de fabriek. Ze verzamelen gegevens van steeds meer parameters, zoals druk, temperatuur, vibratie en akoestiek. Deze gegevens kunnen in combinatie met geavanceerde analyses patronen en problemen blootleggen voordat er stilstand optreedt.
Technici verzamelen nu gegevens in de gehele productiefabriek: van de robots, de CNC-machines en zelfs de snijgereedschappen zelf. Wanneer deze gegevens zijn opgehaald en geanalyseerd, kunnen ze waardevolle inzichten geven in de bedrijfszekerheid van de apparatuur. Deze informatie kan weer gebruikt worden om storingen te voorspellen en te voorkomen, waardoor de efficiëntie van de fabriek verbetert.
Sandvik Coromant maakt bovendien in toenemende mate gebruik van real-time analyse van de productieomgeving, zodat het de machines nog nauwkeuriger en sneller aan kan passen. “De volgende fase zal de invoering van uiterst geavanceerde technieken zoals kunstmatige intelligentie en machinaal leren omvatten, waarbij machines kunnen leren van historische gegevens en een bepaalde mate van zelfbesturing hebben. Dat is echt een spannend terrein.”
Ondanks deze opvallende technische vooruitgang en de bestempeling door het Wereld Economisch Forum als ‘lighthouse’ eindigt de digitaliseringsreis in Gimo nooit.