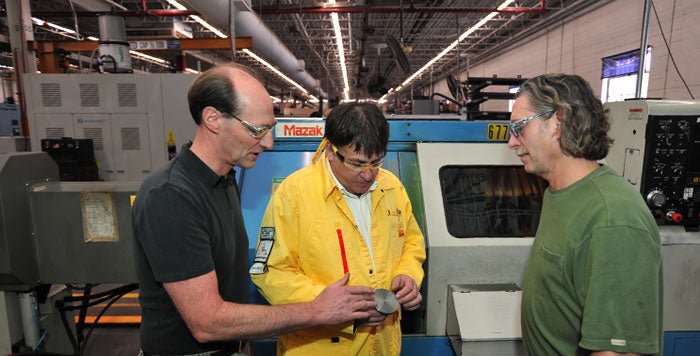
David Turk, Jim Pappas (sales engineer, Sandvik Coromant) and Tom Waite examine the component finish achieved by CoroCut® QD.
Although marginally faster tooling options had become available, David Turk and BUCHER Emhart Glass were reluctant to change from their tried-and-true parting off tool. But a new product that tripled their productivity finally triggered a switch.
Glass containers and bottles are so ubiquitous that most people have used containers that were formed and inspected on a BUCHER Emhart Glass machine. Providing quality glass containers for more than a century, Bucher Emhart Glass developed the industry-standard Individual Section (IS) machine, now the most widely used glass container forming device preferred by glass manufacturers throughout the world. This machine has a bank of five to 20 identical sections, each of which contains a complete set of mechanisms for making different-sized formed glass containers – most destined for the medical, scientific, or food and beverage industries.
In glass manufacturing, inspection and defect analysis is a critical step. To ensure Bucher Emhart Glass continued to provide top quality glass containers, they purchased Powers Manufacturing in Elmira, N.Y in 1982. Powers Manufacturing was a company that had built an international reputation supplying quality cold-end inspection equipment.
The Elmira N.Y. outpost of BUCHER Emhart Glass still designs, machines, assembles and ships complex inspection machines to this day. The Elmira location employs about 140 people, with a machine shop and assembly all under one roof. The machine shop portion of the facility occupies roughly 12,000 square feet, with 25 employees covering two shifts.
The shop is equipped with seven vertical machines, two horizontals, three 3-axis-lathes and a 7-axis-lathe. The brand mix includes a Mazak mill and turning machine, three Hardinge lathes, two Haas machines, one Komo, and a Bridgeport vertical. Primary materials include leadloy 12L14, which tends to be softer and easier to machine, and aluminum bronze and stainless steel, which tend to be tougher.
The workflow at the Emhart machine shop is punctuated by numerous short-run jobs. To limit downtime, this schedule requires operator flexibility as frequent changeovers put increased pressure on the machines and tooling to run as quickly as possible. These short-run jobs require optimal cutting speeds and long tool life in order for the shop to stay productive.
“We’ve been using Sandvik Coromant tooling since the mid-1990s, mostly for milling and turning,” says David Turk, MFG/CNC engineer at Emhart Glass. “Sandvik Coromant is our dominant insert and tool holder supplier. We have a few others, but they account for probably 80 to 85 percent of our indexable carbide. We have a good relationship with our local tool supplier, One Time Tool, and they suggested we try Sandvik Coromant – we did and we’ve been using it ever since.”
Although Turk was already using Sandvik Coromant tooling for other operations, he was not convinced to change the current operation for parting off components on a lathe. Sticking with a process and a product he has used for years, he kept an eye out for products offering significant improvement, but nothing he tested was that much better. Parting off is not a rarely-used operation by Emhart. It is actually required for several components.
“As it’s frequently the final stage of the machining process, parting off is a crucial step.”
As it’s frequently the final stage of the machining process, parting off is a crucial step. Between machine setups, programming, and time already spent making chips, operators and machines have invested quite a bit into machining the component by the time parting off is considered. Parts have already been turned, tapped, drilled, grooved and finished prior to parting off. Scrapping a part after such an investment in time and machine capacity is simply not an option at this point. So sticking with the process that Turk and others at Emhart believed to be the safest bet was what they were going to do unless something could radically change their productivity levels.
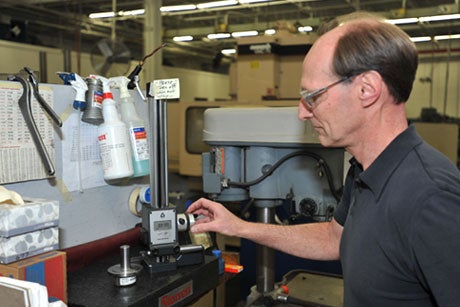
Warranting a switch
“We had tried different inserts, different suppliers, even some inserts from Sandvik Coromant, we just didn’t see enough results to warrant any changes,” Turk says. “Because we do a lot of short run jobs, and there already is a lot of setting up and making programming changes, we wanted to see something where we could get a lot of bang for our buck upon making the switch. Over the years we saw some marginal increases in speed and efficiency with other inserts and tooling, but not enough to push our hand to make a change.”
But even though Turk hadn’t been sufficiently wowed by any other parting off tooling on the market, the operator, Tom Waite, again asked him to keep an eye out for new tooling for the parting off operation in the fall of 2013. Meanwhile, Jim Pappas, sales engineer at Sandvik Coromant, had just completed training on the company’s new CoroCut QD parting and grooving tool. The timing was serendipitous for Pappas to give Turk a ring.
“We were talking about new product releases and got to the parting and grooving tooling, I mentioned Tom’s request for these kinds of tools, and the light bulb went on for both of us,” Turk says. “Jim came in to the machine shop with the CoroCut QD, gave us the parameters, got a big piece of stock and started testing. Right out of the box we were impressed by the way the chips came off that thing - it was amazing.”
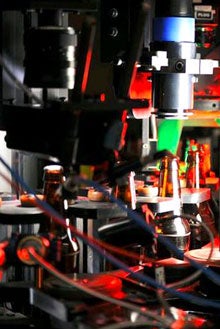
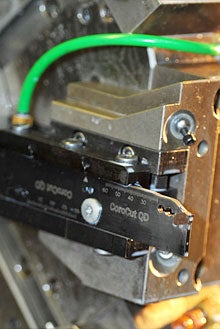
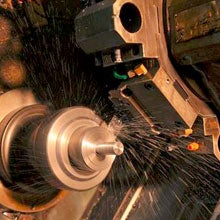
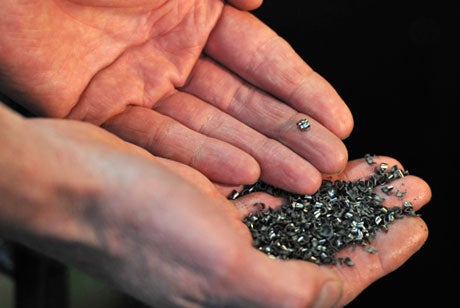
Out-of-the-box improvements
From day one, Turk got the results he had been searching for in his parting off applications. With CoroCut QD, he was tripling the chips per revolution and tripling the surface feet. Material was moving so fast that they actually had to apply the breaks a bit, slowing the spindle speed down so as to optimize tool life, which Turk says has also been notable.
“We had probably been going through about five inserts per week before; now that’s down to about one per week,” Turk says. “As for speed, we were originally doing about 220 surface feet per minute, doing .002 inches per revolution, now we’re at 600 surface footage and .007 inches per revolution, so that’s a dramatic increase.”
Moving more material directly translates to getting more parts done. Timing is always dependent on the diameter of the turned component, but for a piece of 3-inch stock, Waite and Turk have gone from a 20-second part off time to about a 6-to 8-second part off time. By taking a conservative margin of 10 seconds per part (due to changes in diameter), Turk’s quick math says that the CoroCut QD is probably saving 15 minutes per shift which equates to a half hour per day. Extrapolating that figure out to the year, that’s 125 hours saved.
But all the speed in the world would be useless without accuracy. Guaranteeing repeatable straight cuts is just as important.
“The quality of the cut is there, plus it’s nice and straight.”
“The quality of the cut is there, plus it’s nice and straight. When parting off, you can sometimes get a concave or convex taper; bellow in or bellow out,” Turk says. “We used an indicator, a measuring instrument designed to check for taper, to make sure the blade was running perpendicular to the component’s surface. Once we were calibrated, we were good from there.”
With all of the major tests showing dramatic improvement in productivity while maintaining the highest degree of accuracy, Turk was impressed. But as the machine operator, Waite would also require some convincing. The crucible here happened on an operation where the lathe’s turret configuration required running the CoroCut QD right side up instead of upside down.
“Common protocol on turning machines is to face the cutting surface upside down, so gravity will assist with chip removal. Without gravity’s assistance, chips can become choked in comparatively narrow parting and grooving applications, which can be 3/16 inch (or 5 mm); that’s a narrow slot we’ve got to evacuate chips from,” Turk says. “Tom was quick to mention how impressed he was with the way the coolant forces the chips out of the groove—even when cutting right side up.”
According to Turk, the internal coolant which flows through the tool to transport a steady stream right at the cutting edge, helps with both the longevity of the tool and the chip evacuation. The previous parting off cutter had relied on an external coolant line which didn’t provide the same precise coolant delivery.
The instinct to stick with a system that works is usually a good one, especially if nothing is lights-out better than a current process. But sometimes staying with a tried-and-true process prevents shops from learning about new solutions that could provide them with a giant technical leap forward. Turk and Waite are prime examples of engineers and operators who were patient enough to wait for the right product at the right time, and experienced enough to make a change after discovering the next big thing in parting off applications.
“From day one, Turk got the results he had been searching for in his parting off applications.”
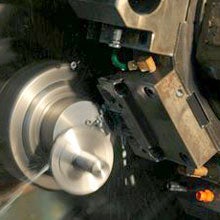
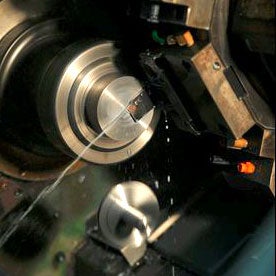
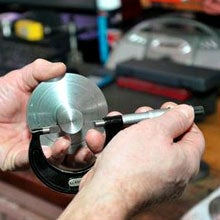