어떻게 만들었을까요?
세계 최초로 3D 프린터를 사용해 파손 방지 기타를 만든 샌드빅
수십년 동안 록스타들은 기타를 박살 내왔지만, 스웨덴 태생의 기타 거장 잉베이 맘스틴(Yngwie Malmsteen)만큼 더 열정적으로 박살 낸 기타리스트는 드물다. 샌드빅은 세계 최초로 전체가 금속으로 된 부서지지 않는 기타를 만들어 맘스틴에게 마음대로 박살 내보라고 함으로써 자사의 최첨단 기술을 테스트하기로 결정했다.
샌드빅은 회사 전체의 전문가들을 모아 자사의 엔지니어들이 어떻게 지속 가능한 최첨단 기술을 이용해 고도로 정밀하며 내구성도 탁월한 제품을 만들 수 있는지 보여주었다.
"기타 거장을 위한 복잡하고 아름다운 기타를 만들기 위해 첨단 소재, 정밀 가공, 적층 가공, 데이터 중심 생산 같은 첨단 프로세스를 총동원했습니다."라고 샌드빅 머시닝 솔루션 사장 클라스 폿스스트룀(Klas Forsström)은 말한다. "또한 잉베이가 얼마나 세게 기타를 박살 내려고 시도하는지에 상관없이 절대 부서지지 않는다는 것을 보여주기 원했습니다. 이 프로젝트는 우리의 기술과 역량뿐 아니라 잉베이의 기타를 박살 내는 솜씨를 모두 확인할 수 있는 완벽한 프로젝트였습니다."
처음부터 시작된 협력
플로리다 콘서트가 있기 몇 달 전 스웨덴에서 샌드빅은 회사 전체의 소재, 가공 공정 및 적층 가공 분야 전문가들을 모아 이 과제를 수행하는 방법을 브레인스토밍했다.
샌드빅은 이전에 기타를 만든 적이 없기 때문에 유명한 기타 제조사인 영국의 Drewman Guitars와 협력했다. "우리는 위에서부터 아래로 혁신해야 했습니다."라고 Drewman의 디자이너 앤디 홀트(Andy Holt)는 말한다. "우리는 음악가들이 '이렇게 만들어진 기타는 처음 봐요'라고 말하기를 기대했습니다."
홀트에 따르면 그는 개발 과정 중에 샌드빅의 엔지니어들에게 매일 새로운 디지털 설계 파일을 보냈다. 기타 제조사와의 긴밀한 협력 끝에 기술적 창의성의 결정체라고 불릴만한 제품을 설계하는 데 성공했다.
세계 최초의 파손 방지 기타
샌드빅 코로만트의 가공 공정 개발자인 헨리크 로이카넨(Henrik Loikkanen)은 맘스틴을 우상으로 여겼던 청소년 시절부터 기타를 연주했다. 그러나 그는 한 번도 기타를 박살 내본 적이 없다(로이카넨에 따르면 '너무 비싸서' 부수지 않았다). 그래서 맘스틴이 기타를 부술 때 어떤 일이 일어나는지 알기 위해 YouTube를 보았다.
"기타를 부술 수 있는 모든 방향에서 부서지지 않는 기타를 설계해야 했습니다."라고 로이카넨은 말한다. "엔지니어링 측면에서 보면 기타에서 금이 잘 가는 부분인 넥과 바디 사이의 조인트가 과제였습니다." 그래서 샌드빅 코로만트 엔지니어들은 조인트를 제거하기로 결정했다. 기타 바디 깊숙이까지 있는 직사각형 '허브'로 넥과 지판이 모두 연장되었다.
스캘럽 지판을 사용하면 잉베이가 음을 더 잘 컨트롤할 수 있기 때문에 엔지니어들은 프렛 사이를 길고 매끄러운 호 모양으로 파내야 했다. 기타를 최대한 가볍게 만들기 위해 샌드빅 코로만트는 넥과 지판의 내부 표면을 파냈다.
"각 프렛의 높이가 완벽하게 정렬되어야 했습니다. 그렇지 않은 경우 기타줄이 프렛의 일부를 건드려 소리가 납니다."라고 로이카넨은 말한다.
최첨단 데이터
지판이나 넥 같이 길고 가는 가공물은 가공 공정 중의 비틀림에 특히 취약하다. 샌드빅 코로만트는 1차 절삭을 수행하기 전에 첨단 소프트웨어를 사용해 작업을 디지털 방식으로 시뮬레이션했다.
"정밀도가 관건이었습니다."라고 헨리크 로이카넨은 말한다. "이 소프트웨어는 수년간의 경험을 바탕으로 개발되었습니다. 소프트웨어에서 제공한 공구 및 절삭 조건 권장사항은 지판을 1mm의 두께로 밀링하는 까다로운 작업에서 큰 도움이 되었습니다."
또한 자동화된 공정 덕분에 한 기계에서만 지판을 밀링 가공할 수 있었다. 공정은 90개의 개별 작업으로 구성되었고 새로운 공구와 절삭을 셋업하기 위해 기계를 중단하지 않고 공정을 완료했다.
"원자재를 투입하면 완성된 부품이 나옵니다."라고 로이카넨은 말한다. "이는 소재를 제거하는 더욱 스마트한 방법입니다. 사이클 시간을 줄이고 더 낮은 비용으로 부품을 생산할 수 있습니다."
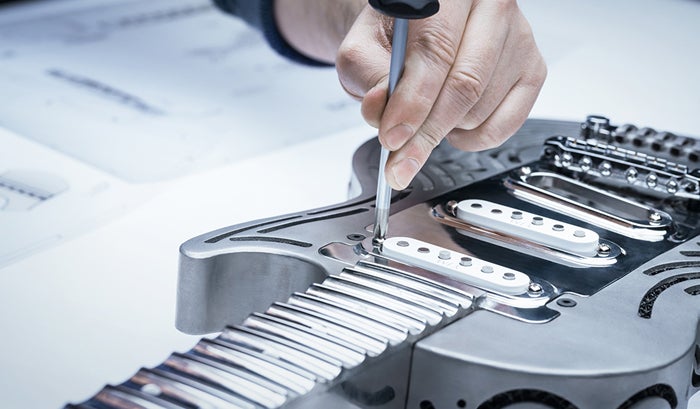
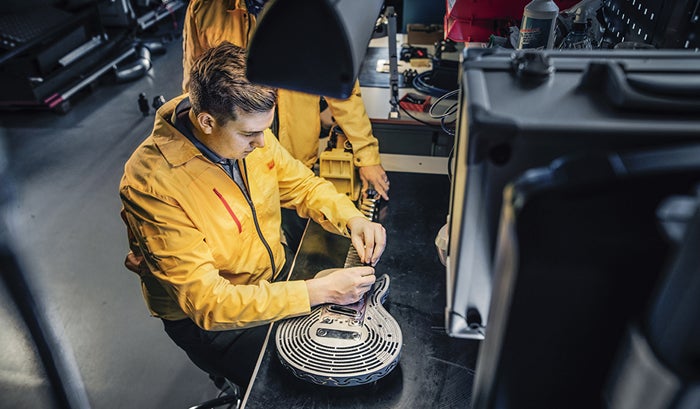
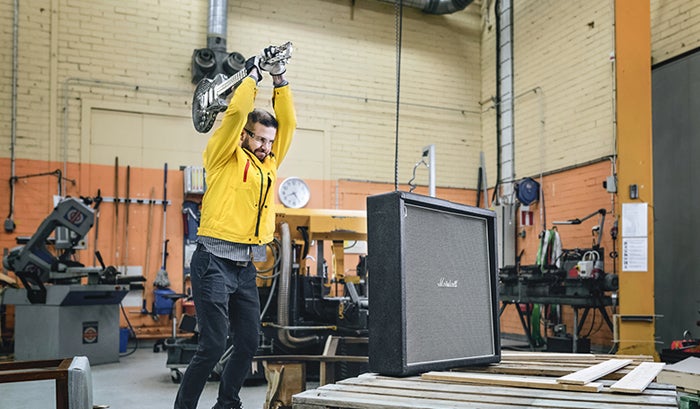
엔지니어들은 매번 이전 버전보다 더 가벼운 프로토타입을 만들 수 있었고, 이는 최종 기타를 생산할 때까지 계속되었다. 정밀한 CoroMill® 절삭 공구를 사용해 매끄럽고 광택이 나는 금속 표면을 가공했다.
로이카넨에 따르면 다른 샌드빅 사업부와의 협력이 파손 방지 기타를 만드는 열쇠였다. 그는 샌드빅 애디티브 매뉴팩처링이 티타늄을 사용해 3D 프린터로 제작한 기타 바디와 작은 부품들을 최종적으로 밀링 가공하도록 도왔다. 또한 샌드빅 코로만트는 샌드빅 머티리얼 테크놀로지와 협력하여 강재를 선택하고 넥 내부에 하이퍼 듀플렉스 격자 구조를 구현했다. 로이카넨은 이러한 팀워크야말로 기타를 만든 진짜 목적이었다고 말한다.
"샌드빅 코로만트는 공구를 제공할 뿐만 아니라 공정에서 공구를 사용하는 최상의 방법을 개발해 고객이 복잡한 작업을 성공적으로 완수하도록 돕는 것으로 유명합니다."라고 로이카넨은 말한다.