課題: 旋盤における無人工具交換を増やし、切りくず処理問題を解決すること。
解決策: 旋盤の工具交換を自動化し、クーラントをより高圧に変更。
製造業界では旋盤を使用することが最も多い。サイズにかかわらず多くの旋盤では、工具交換が手作業であるため無駄な機械の停止が長く、また加工箇所にはクーラントが効果的に働いていない傾向がある。このような機械に生じる計画的あるいは突発的な停止を最小限に抑える取組みが続いている。
今日では自動工具交換機能のないマシニングセンタの購入を検討する人はいないだろうが、この機能は旋盤においては標準的ではない。これは、自動工具交換を可能にするタレット用の共通ツールホルダがないのが一因である。工程面では、横型ターニングセンタにはY軸、2タレット、サブスピンドル、効率的な大量生産のための監視及び測定設備などが搭載されるようになり、実際の加工の効率性および汎用性が著しく向上した。立て型旋盤は、次のステージへと進化し、自動工具交換がオプションとなってきた。これは、機械の無人運転、汎用性の向上、最小限の部品移動、タレット位置を制限することなく長いボーリングバイトを使える能力などの製造業界のニーズに起因する動きである。
自動工具交換装置や標準タレットインターフェースが将来機械コンセプトの一部になることは自明である。工具開発は機械開発に促されてきた一方、機械開発を促してきた。製造業界は加工コストを重視しながら、新技術の開発を促し、新技術に対応している。
最新機械の多くは高圧クーラントシステムを 使用するが、加工工程に実質的な違いを生むような形で使われているものは少ない。コロターンHP のように30バールから80バールの高圧能力を備えるものもある。このような工具では、直線的に正確に噴射されるクーラントが発生する切りくずを押し上げ、冷却し、ターニングセンタの切りくず処理を改善する。この結果、多くの材質に対する無人生産の性能と安全性が改善する。
しかし、より切りくず処理が難しい材質への高圧旋削において最大限の恩恵を受けるためには、よりクーラント速度が早く、高圧(最高150バール)のクーラントが大多数の加工において必要である。この結果、加工プロセスおよび加工ゾーンとチップコンベヤにおける切りくず管理において、大きなな効果が得られる。難削材や長い切りくずの出る被削材が切りくず処理時間の長期化を招き、自動加工を実現するための信頼性を損なう可能性があるターニングセンタにおいては、この新しい機能を検討する余地がある。
これらの解決策は、IS O規格であるコロマントキャプト・モジュラーツーリングシステムを元としている。このシステムは、固定及び回転工具ホルダを搭載した旋盤の手動工具交換システムとして長年幅広く使用されてきた。今日では、立て型旋盤も複合加工機も自動工具交換機能を持つ共通のインターフェースを使用する。コロマントキャプトの次なるステップは、自動工具交換が可能な旋盤の開発である。コロマントキャプトの開発が、固定及び回転工具の共通インターフェース、そして自動工具交換を確立するための基準となる。
クーラントの高圧化に備えて、最低でも150バールの圧力に耐えうるシーリング能力のある新しいクランプ機構が開発された。これは、旋盤用手動クランプユニット用であり、また複合加工機の回転スピンドルをクランプするためでもある。現在進行中の開発の主な利点は、インターフェースが統一化され、既存のカッティングユニットやアダプタとの間に完全な互換性があることだ。
自動工具交換装置や標準タレットインターフェースが将来機械コンセプトの一部になることは自明である。
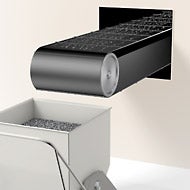
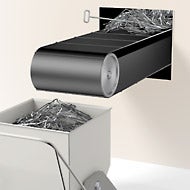
安定した切りくず処理
難削材において安定した切りくず処理を実現するためには、現在一般的に使われている圧力以上の高圧を利用する必要がある。主要な加工を網羅するために最高150バールの圧力が不可欠だ。これにより加工プロセス、そして加工ゾーン及びコンベヤにおける切りくず管理が大きく改善する。
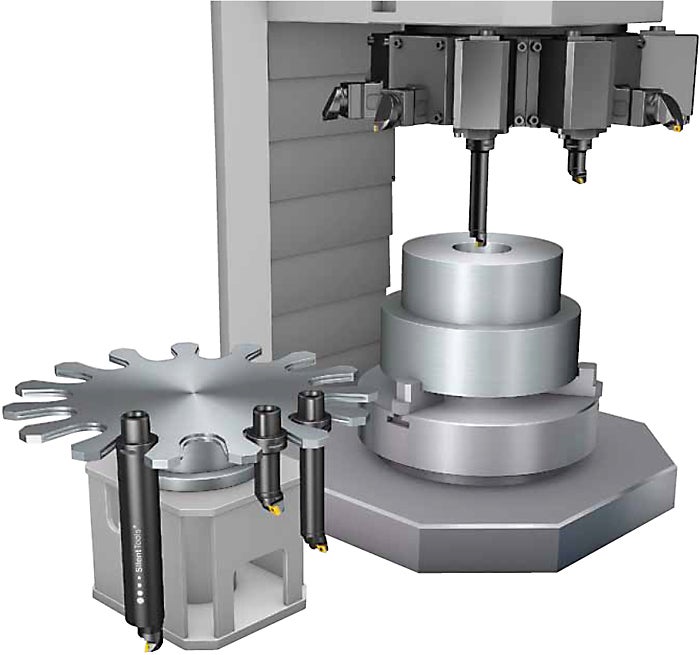
立て型旋盤
マシニングセンタ同様、立て型旋盤にも工具交換の自動化が進んでいる。短い工具での加工の妨げとなる長い工具の取り外し作業、効率性を高め、無人製造を進めるニーズがあるからだ。コロマントキャプトの開発が、固定及び回転工具の共通インターフェース、そして自動工具交換を確立するための基準となる。
総括
工具交換時間及び加工箇所へのクーラントの使用方法の変更が、将来的に加工現場、特に旋盤加工での競争力強化につながる。
この記事の初出は、サンドビック・コロマントの顧客向け雑誌「Metalworking World 」である。