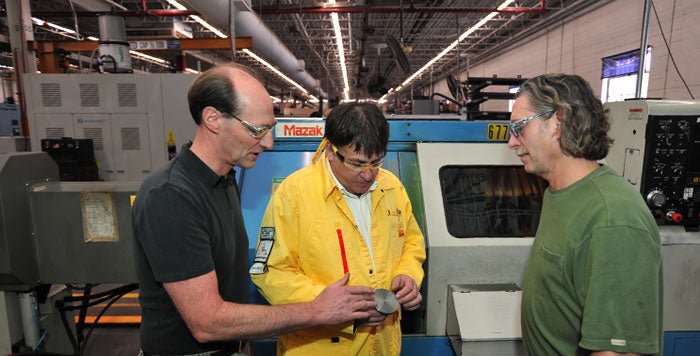
デイビット・ターク氏(左)、ジム・パッパス(中央・サンドビック・コロマントのセールスエンジニア)とトム・ウエイト氏(右)の3名で、コロカットQDによる加工ワークの仕上がりを検証
デイビット・ターク氏とブッハー・エムハート・グラス社は、わずかに加工工程が速くなるツーリングの開発に成功したものの、それまで信頼して使っていた突切り加工工具を変えることに消極的なままでいました。しかし、生産性を3倍にも向上させる新製品を見つけ、ついに工具を変更しました。
ガラス容器やびんはどこにでもありふれたものですが、誰もが一度はブッハー・エムハート・グラス社の機械で成形・検査した容器を使ったことがあるでしょう。高品質のガラス容器を1世紀以上にわたって製造してきたブッハー・エムハート・グラス社は、業界標準のISマシンと呼ばれる機械を開発しました。これは今日、世界中のガラス製造メーカーで最も広く使われている、ガラス容器成型装置です。この機械には5~20の同一セクションの列があり、それぞれのセクションに、異なったサイズのガラス容器成形用のメカニズム一式が備わっています。そのほとんどは医療、科学、食品や飲料産業向けの容器です。
ガラス製造業において、検査と欠陥解析は重要なステップです。最高品質のガラス容器を継続して提供するために、ブッハー・エムハート・グラス社は1982年にパワーズ・マニュファクチャリング社(米国・ニューヨーク州エルミラ)を買収しました。パワーズ・マニュファクチャリング社は、質の高いコールドエンド検査装置の供給で国際的評価を確立した会社です。
ブッハー・エムハート・グラス社のニューヨーク州エルミラ支社では、複合検査機の設計、加工、組立、出荷を行っています。エルミラ支社の従業員は約140名で、加工部門と組立部門のすべてが1つの工場内にあります。施設の工場部分は12,000平方フィート(1,115㎡)を占め、25名の従業員が2交代で勤務しています。
工場には7台の立型マシニング機械、2台の横型マシニング機械と3台の3軸旋盤、1台の7軸旋盤があります。機械は、ヤマザキマザック社の複合加工機が1台、ハーディング社の旋盤が3台、ハース社の機械が2台、KOMO社が1台、ブリッジポート社の立型マシニングが1台と様々な種類があります。主な材料は、柔らかく加工が容易な鉛合金12L14や、加工がより難しいアルミニウム青銅、ステンレス鋼といったものです。
エムハート・グラス社の工場でのワークフローは、非常に多くの短時間作業に分類されています。ジョブの入れ替えが頻繁であるため、ダウンタイム低減のために、可能な限り迅速に稼働できる機械とツーリングが重要となり、オペレータには柔軟な対応が求められます。生産性を維持するため、これらの短時間加工には最適な切削速度と長い工具寿命が必要となります。
「私たちは、主にフライス加工と旋削加工でサンドビック・コロマントのツーリングを1990年代中頃から使っています。」とエムハート・グラス社のMFG/CNCエンジニア、デイビット・ターク氏は語ります。「サンドビック・コロマントは、チップやツールホルダの主要サプライヤです。他にも2、3社ありますが、弊社が使っている刃先交換式超硬チップのおそらく80~85%を占めています。良好な関係にある地元の工具サプライヤのワン・タイム・ツール社がサンドビック・コロマントを勧めてくれました。実際に試してみて、それ以来ずっと使い続けています。」
他の加工でサンドビック・コロマントのツーリングをすでに使っていたものの、ターク氏は、当時旋盤で行っていた部品の突切り加工工具を変えることに確信が持てずにいました。彼は、著しい生産性向上をもたらす製品を探していましたが、今までテストした製品はどれも優れた結果を示すものではなく、工程と使用工具を変えないまま何年も月日が経っていました。突切り加工は、エムハート・グラス社ではあまり行われない加工というわけではなく、実際、いくつかの部品加工に必要となる工程だったにも関わらずです。
「突切り加工は、最終加工工程の非常に重要なステップです。」
突切り加工は、加工工程の最終段階でよく使われるため非常に重要です。突切り加工に至るまでにすでに、機械のセットアップ、プログラミング、前工程の加工などには、かなりの投資、つまりは時間と人の手間が費やされています。具体的には、前加工として部品に旋削加工、タップ加工、穴あけ加工、溝入れ加工、仕上げ旋削加工が行われています。このように多くの時間と作業に投資して作った部品を廃棄することはありえないのです。したがって、何か生産性レベルを劇的に変えるものがない限り、それまで最も確実だと信じていた工程を変えずに続けることがいちばんだとターク氏や彼の同僚は信じていました。
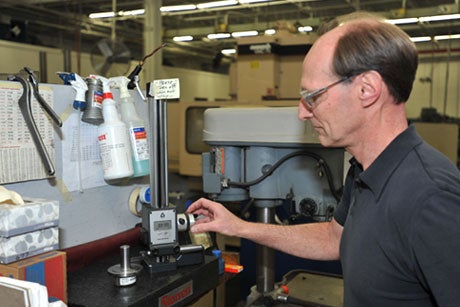
変更の根拠となるもの
「サンドビック・コロマントのチップ数種と、その他のサプライヤーのさまざまなチップを試しましたが、変更に踏み切る十分な結果を得ることができませんでした。」とターク氏は振り返ります。「というのも、弊社の工程では短時間作業が多く、セットアップやプログラム変更も頻繁に行うため、変更の導入にあたっては、投資に見合う多くの効果が得られるかどうかを見極めたかったのです。この数年間、他社チップとツーリングの使用により加工速度や効率において若干の向上が得られたものの、変更に踏み切るには十分ではありませんでした。」
市場に出回る突切り加工用ツーリングはどれもターク氏をうならせることはできませんでしたが、オペレータのトム・ウエイト氏が、2013年秋に再度、新しいツーリングを探してはどうかと社内で提案しました。ちょうどその頃、サンドビック・コロマントのセールスエンジニア、ジム・パッパスは突切り・溝入れ工具の新製品コロカットQDの研修トレーニングを終了し、そうとは知らずまさに偶然のタイミングで、パッパスはターク氏に電話をかけたのでした。
「新製品について話すうちに、突切り・溝入れ工具の話題になり、トムが工具について要望していたことを伝えました。そこで私たち双方にアイデアがひらめいたのです。」とターク氏は言います。「ジムがコロカットQDを持って工場を訪れ、パラメータを設定し、大きな材料を取り出してテスト加工を始めました。始まってすぐ、私たちは切りくずが離れていく様子に強い印象を受けました。それは驚きでした。」
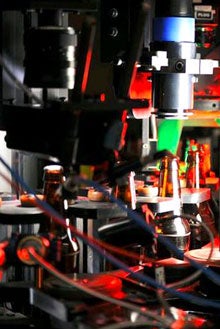
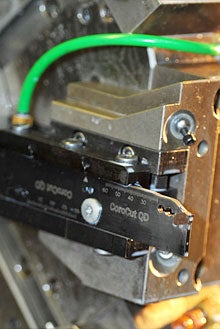
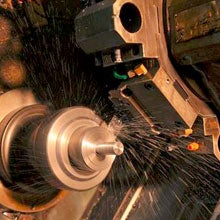
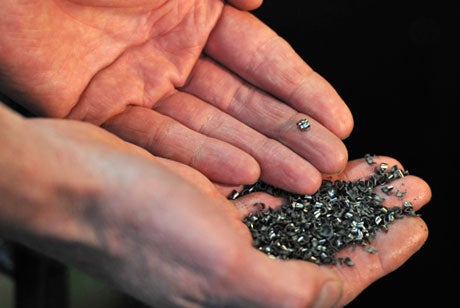
予想を超えた改善
ターク氏は初日の突切り加工から、求め続けていた加工結果を得ることができました。コロカットQDで、1回転当たりの切りくず排出量が3倍になり、送りも3倍になりました。加工中の被削材の移動はとても速く、実際彼は工具寿命を最適化するために(もっとも、寿命の長さが顕著であるとターク氏がすでに語っていますが)、加工を少し止めなければならないほどでした。
「当社ではこれまでは1週間当たりおそらく5枚のチップが必要でした。いまでは1週間当たり1枚にまで少なくなりました。」とターク氏は話しています。「加工速度に関しては、元々当社では1分あたり220フィートの表面を加工していました。つまり1回転あたり.002インチでしたが、今では1分当たり600フィートになり、1回転あたり.007インチと劇的にアップしました。」
被削材をもっと無駄のないように移動させることで、もっと多くの部品を加工することができます。加工ワーク径に依りますが、取代が3インチのワークでは、今まで20秒かかっていた突切り加工時間が6~8秒に短縮できました。1ワークあたりの短縮時間を少なめに10秒と見積もっても(ワークによる径の増減があるため)、コロカットQDはおそらく1シフトあたり15分の時間を節約でき、1日あたりだと30分の時間短縮が可能であるとターク氏ははじき出しました。1年当たりの数値を推定すると125時間の節約になります。
しかし、どんなに加工速度がアップしても精度が伴わなければ役に立ちません。繰り返し精度の保証されているまっすぐな加工こそが重要なのです。
「品質がよく、さらにまっすぐで精度がいい加工。」
「品質がよく、さらにまっすぐで精度がいい加工。突切り加工では、時々テーパ部が凸凹になったり、奥が広かったり狭まったり、正しく加工できないことがあります。」とターク氏。 「当社では計器、つまりテーパ部のチェック用に設計された測定器を使用して、ブレードが加工ワーク表面に対して垂直になっているかを確認していました。一度計器を調整すると、その後その部分の精度は良くなりました。
「主なテストのすべてにおいて生産性に劇的な改善が見られ、精度のレベルもたいへん高いものでした」とターク氏はその印象を語っています。しかし、オペレータであるウエイト氏もまた、十分な結果を必要としていました。加工時に発生したここでの課題は、旋盤のタレット構成により、コロカットQDを逆さまにするのではなく表を上にして使用する必要があることでした。
「旋盤での従来の共通加工スタイルでは、コロカットQDを逆さまに取り付けていました。これにより重力が切りくずの排出をアシストします。重力によるアシストがないと、3/16インチ (5mm) の比較的狭い突切り・溝入れ加工部分に切りくずが詰まることがあります。しかし我々は、新しい工具で、切りくずをこの狭い溝から排出できました。トムは、チップの表面を上にして切削しているときでもクーラントにより切りくずが排出されたのがとても感動的だった、とすぐさま私に話してくれました。」
ターク氏によると、工具内部を通って流れるクーラントは安定した流れで適切に刃先に届き、工具の長寿命と切りくず排出をサポートしています。これまでの突切りカッターは外部クーラントに依存していたため精確なクーラント供給ができませんでした。
現在のプロセスより優れたものがない場合はもちろん、一般的に問題なく機能しているシステムをそのまま使い続けるのは、よい選択です。しかし、確立したプロセスに長い間とどまり続けるあまり、大きな飛躍的技術革新をもたらす新ソリューションについて知る機会を逃してしまう可能性もしばしばあります。ターク氏とウエイト氏は、適切な時期に適切な製品を導入するのを忍耐強く待ち、その結果、突切り加工で重要な変化の判断を下すことができました。まさに十分な経験のあるエンジニアとオペレータの典型的な好例と言えるでしょう。
「ターク氏は初日の突切り加工から、求め続けていた加工結果を得ることができました」
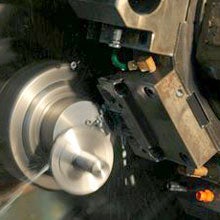
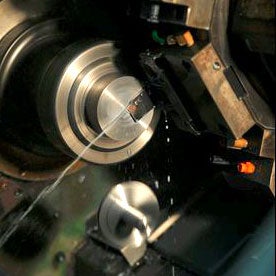
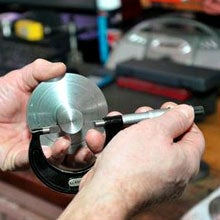