La fabbrica del futuro
L'unità produttiva Sandvik Coromant di Gimo, in Svezia, è stata riconosciuta dal Forum economico mondiale (World Economic Forum, Wef) come stabilimento high-tech 4.0 di livello avanzato.
Lo stabilimento Sandvik Coromant di Gimo, a nord di Stoccolma, è una struttura altamente automatizzata che sfrutta appieno i molti vantaggi offerti dalla produzione connessa, come ha recentemente confermato il Forum economico mondiale, che ha inserito Gimo nella sua lista di “impianti-faro” dell'industria 4.0 mondiale. Tutte le fabbriche-faro sono state selezionate da un elenco di 1000 siti produttivi, valutando il livello di successo nell'integrazione delle tecnologie digitali con vantaggi concreti.
Secondo il Wef, lo stabilimento di Gimo ha introdotto flussi di lavoro digitali nei suoi processi di produzione determinando un notevole miglioramento della produttività. Un esempio è rappresentato dai "cambi touchless", che prevedono il cambiamento automatico dei design pattern anche durante i turni di produzione non presidiata. Grazie a questi progressi da leader, Gimo entrerà a far parte della rete mondiale delle fabbriche-faro creata dal Wef, e aprirà le proprie porte per condividere le conoscenze con altre aziende manifatturiere.
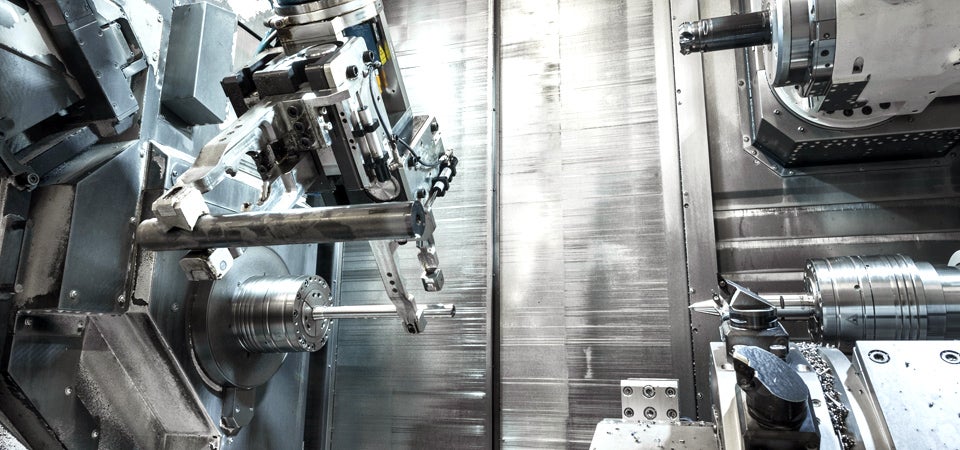
Questo riconoscimento è stato accolto con grande orgoglio a Gimo, dichiara Lars Matiasson, Director of Production Technology Tools Sandvik Coromant, perché ci dimostra che i nostri sforzi per favorire l'innovazione vanno nella direzione giusta. “Il percorso di digitalizzazione di Gimo è iniziato 30 anni fa, quando abbiamo iniziato a usare i sistemi CAD/CAM parametrici. Poi qualche anno dopo li abbiamo connessi ai nostri sistemi di automazione intelligenti, creando così il primo collegamento digitale della nostra produzione. Ma è stata più un'evoluzione che una rivoluzione.
“Oggi questi flussi di lavoro digitali riguardano tutte le aree dell'impianto, dalla gestione delle scorte alle macchine, alla manutenzione predittiva. Questo spirito di innovazione ha sempre animato tutto il personale dello stabilimento, a partire dai livelli gerarchici più alti. I membri del consiglio di amministrazione e i manager di Gimo hanno sempre spronato gli ingegneri a pensare in modo diverso e a farsi promotori del cambiamento. In pratica, ci siamo impegnati per trovare dei modi per sfruttare la tecnologia per migliorare l'efficienza e la competitività dell'impianto. Questo approccio, a sua volta, ci ha aiutato a costruire un futuro sostenibile”.
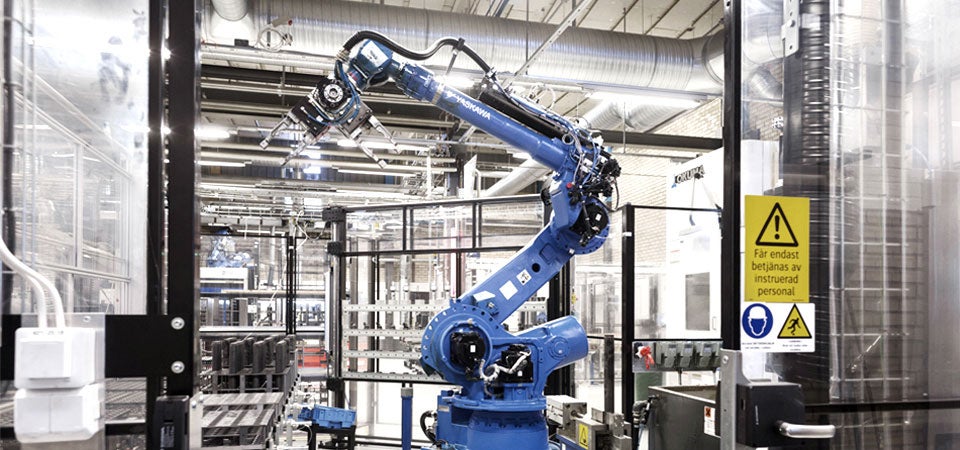
I cambi touchless sono un esempio perfetto di questo approccio. In passato, i design pattern dovevano essere cambiati manualmente nelle celle di produzione. Gli operatori dei turni diurni dovevano preparare le macchine per farle funzionare durante la notte, un processo che richiedeva tempo e risorse e limitava la flessibilità durante i turni non presidiati. L'alternativa consisteva nell'investire in soluzioni di automazione intelligenti con robot, macchine, utensili e attrezzature ultra-flessibili che, nel loro insieme, fossero in grado di eseguire complessi cambi touchless senza richiedere la supervisione umana.
“Quando si parla di produzione snella, generalmente si citano esempi come l'esecuzione di un cambio stampo in un minuto, ma noi volevamo fare un passo in più, volevamo arrivare a eseguire il setup in maniera totalmente automatizzata”, commenta Matiasson.
“Però avevamo molto da imparare. La prima cella automatizzata non funzionava bene come ci aspettavamo, anzi, era anche meno efficiente di una macchina con operatore. Ma con la digitalizzazione funziona così: bisogna saper fallire per imparare. Così, piano piano, siamo riusciti ad apportare miglioramenti importanti e le celle robotizzate hanno iniziato ad avvicinarsi ai livelli di efficienza che avevamo in mente. Bisogna procedere per prove ed errori se si vuole migliorare”.

I tecnici di Gimo sfruttano le tecnologie digitali per introdurre miglioramenti anche in altre aree, ad esempio quella della manutenzione. Oggi si installano sempre più sensori sulle macchine dell'impianto, per raccogliere dati relativi a un numero sempre crescente di parametri, come pressione, temperatura, vibrazioni e acustica. Questi dati, analizzati con sistemi sofisticati, permettono di identificare i pattern e i problemi prima che si traducano in un fermo macchina.
Oggi raccogliamo dati da ogni parte dello stabilimento: dai robot, dalle macchine a controllo numerico, persino dagli utensili da taglio. I dati, estratti e analizzati, forniscono informazioni preziose sullo stato di salute delle macchine, che a loro volta possono essere utilizzate per prevedere e prevenire i guasti e, quindi, migliorare l'efficienza dell'impianto.
Sandvik Coromant sfrutta sempre di più le funzionalità di analisi in tempo reale nell'ambiente di produzione per effettuare regolazioni ancora più precise e puntuali sulle macchine. “Il passo successivo sarà l'introduzione di tecnologie altamente sofisticate come l'intelligenza artificiale e l'apprendimento automatico, che permetteranno alle macchine di imparare dai dati del passato e di acquisire un certo autocontrollo. Le prospettive che si aprono sono davvero entusiasmanti”.
Nonostante questi straordinari progressi tecnologici e il riconoscimento di fabbrica-faro del Forum Economico Mondiale, il percorso di digitalizzazione di Gimo non finisce mai.