Mastering machining: Five proven techniques for cutting costs and improving efficiency
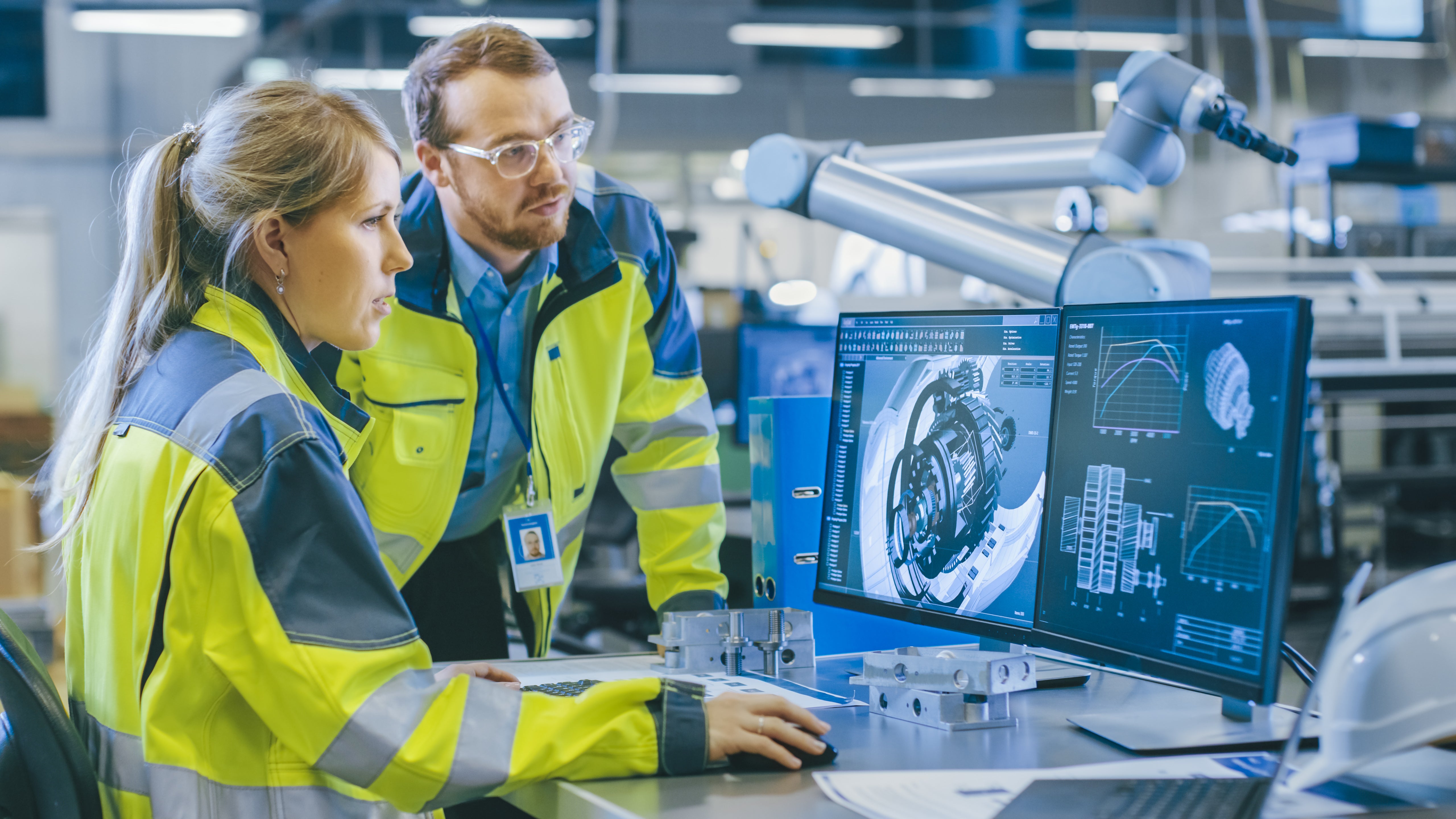
1. Machine with style: It’s not only about the right tools
The right tool will get the job done – but we’re not the type of experts that settle for good enough (and since you’re reading this, you probably aren’t either). The perfect balance lies somewhere between what already works and the unknown – a mere step outside of the comfort zone where experience and innovation collide.
Lean manufacturing techniques focus on improving your entire setup process for faster changes and reduced batch sizes e.g., 5S, SMED, value stream mapping, etc. These can help you get to the core of the problem and pinpoint solutions to increasing costs, lack of consistency, and customer dissatisfaction.
Start by looking at the manufacturing performance data and calculate your OEE score (Overall Equipment Efficiency) over the last two weeks. Same goes for the downtime percentage – if higher than 20%, SMED (Single-Minute Exchange of Die) might be the way to go. If less, consider trying TPM (Total Productive Maintenance). Act fast before things get out of hand and you find yourself stuck on the wrong side of a wide divide from your desired destination.
But speaking of tools… invest in high-performance tools. Using high-performance tools can help minimize tool wear, resulting in a longer lifespan and less overall expenditure. And before you throw your carbide tools in the bin – get in contact to find out how we can recondition or recycle them for you.
2. Tool care: Prevention is better than cure
Well begun is half done, and the best way to guarantee a clean start of the next project is to have a tool management system. Tracking your inventory will help you get the most out of your tools and remind you to replace them when necessary. This can have a serious impact on your profit margin.
Proper maintenance of equipment will also prolong the life of cutting tools and keep the machine running at optimal performance, reducing the need for replacements and repairs. Proactive and planned machine maintenance makes production and planning a lot more predictable and reduces unplanned stops, especially if combined with good ongoing operator maintenance.
3. Automate: Breaking bottlenecks before they break you
Optimising cutting parameters such as speed, feed, and depth of cut can improve machining efficiency and reduce tool wear and lead to longer tool life and lower costs. We know you know.
Then there’s automation – hear us out. We know it isn’t a quick fix for every problem, but it does move around resources in a factory. By automating a chronic bottleneck area, can you move people from that area to do delicate tasks that require closer human supervision? You can and it would be wise to do so.
4. Simulate: Fake it ‘til you make it
When faced with challenges, we put our imagination to work. Your keen expertise is dictated by highly cultivated machining instincts. You have an idea of what works and what doesn’t the moment you set your eyes on a project. You need to test your theory, but money is tight, resources are scarce. How to get cutting parameters right faster and minimize physical trials?
Simulation software has a higher chance of getting it right the first time. Where knowledge and imagination come short (or if you simply want to get this done – fast), simulation will optimize and save you money and time from the start. You won’t have to run single block test. This is a big win for small-batch producers with a never-ending order list of new components and a lot of changeovers.
5. Learn: Challenge your expertise (and ours)
It goes without saying that new technologies can help improve machining efficiency and reduce costs over time. Small actions lead to big changes down the line. Standards will shift (especially as sustainability grows) and today will soon be history – such is the tempo of innovation. But you will stay and carry on the expertise of tomorrow. Staying curious is the key to any machining challenge, be it unplanned downtime or bottlenecks.
That isn’t to imply that learning is a lonely journey. Seeking expert advice is the best way to fast-track your progress. Sandvik Coromant's technical support team can help you improve your machining process and offer assistance with the best solutions for cost reduction. The technical department is not the only party involved – we provide a combination of technical and lean manufacturing guidance for a more balanced approach. Ultimately, we aim to equip you with the tools and knowledge to foresee problems and tackle day-to-day nuisance with swift action and unfaltering confidence.
It never hurts to know just a little bit more on the topic. Keep exploring cost-reduction strategies with seasoned experts from our manufacturing plant in Gimo or get straight to business with our cost-cutting guide: