Problems that originate from vibrations are frequently encountered in boring and other operations, especially when machining with long overhangs. The vibrations may cause bad surface texture, insufficient accuracy, loss of productivity, increased insert and machine tool wear, as well as noise.
Solving vibration problems will therefore always give you a productivity boost.
Benefits
- Productivity gains of 50-200%
- Strong optimized interface between bridge and damped adaptor
- Improved surface finish
- Improved process security
- High penetration rates
- Reduced cost per component
Features
- Silent Tools™ damper, for long tool assemblies, dimensioned for every adaptor in the assortment
- Short fine boring head in aluminium
- Strong optimized interface between bridge and damped adaptor
- Internal coolant through the assembly
- The optimized lightweight bridges (to be used with damped adaptor) fit together with existing slides and cartridges for both rough and fine boring
- Cartridges assortment, for back boring applications, with diameter range 31–181 mm (1.220–7.126 inch)
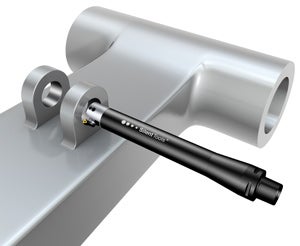
Application
- Boring operations: roughing and finishing
- Cutting data can be increased substantially thanks to eliminated vibrations
Damped CoroBore® 820XL:
- Radial depth of cut up to 8 mm (0.315 inch) (16 mm (0.630 inch) diameter increase) in low alloy steel with twin edge rough boring equipment
- Maximum torque: 2000 Nm (1475 ft/lbs)
ISO application area





Recommendations
- The entering angle should be close to 90 degrees to give more axial cutting forces and less radial/tangential forces
- Use large entering angles and small nose radii to reduce the radial forces, deflection and vibrations
- Small nose radius is ideal for small depths of cut and decrease the risk of vibrations
- Use only one adaptive item between the Silent Tools™ adaptor and the machine tool spindle since further extension will reduce or completely ruin the performance
- Use as light cutting units as possible to improve the dynamic behaviour and effect of the damper
- If possible, use a tapered shank
- Productive boring: Two inserts with the same length and diameter to be able to increase feed
- Step boring: Additional shim under one of the slides if you want to take a large radial cut
- Single-edge boring: Replace one of the slides with a cover to reduce cutting forces and achieve accurate roundness, good surface finish and close tolerances
Damped CoroBore® 820XL:
Machine tools and spindle interfaces
Machine tools and spindle interfaces need to be strong and stable to hold large tools and assemblies as CoroBore® 826D XL. Suitable interfaces are therefore HSK 100 and Coromant Capto® C8 – C10. ISO 50 taper (BIG PLUS included) is too weak for these roughing tools.
Cutting data
The recommended start values for inserts and grades listed at the box shall be followed, but be aware of the many parameters that have to be taken into consideration – such as actual work piece material, spindle interface clamping force, torque capacity at given RPM, net power etc.
Product range
Rough boring | Rough boring | Fine boring | Fine boring |
Boring range Ø 23–150 mm (0.906–5.91 inch) | Boring range Ø 148–300 mm (5.827–11.811 inch) | Boring range Ø 19–167 mm (0.748–6.575 inch) | Boring range Ø 148–315 mm (5.827–12.402 inch) |
Damped CoroBore® BR20 Silent Tools™ | Damped CoroBore® 820D XL | Damped CoroBore® 825 | Damped CoroBore® 825D XL/826D XL |
![]() | ![]() | ![]() | ![]() |
Coromant Capto® back-end couplingCoolant through |