Why your machines need to start talking
Technology is vaulting past our wildest expectations, and it’s not slowing down. Industry 4.0 is achieving leaps in mere decades, driving manufacturing to new heights of speed and innovation. Machine learning has only accelerated this phenomenon, excelling beyond all expectations—86% of manufacturing executives recognize the escalating impact of smart factory technologies in the coming years.
Smart factories are pioneering new frontiers every day, but what does a truly smart shop floor looks like in the 21st century? Here, Taline Forsberg, Vice President Digital Products and Services at Sandvik Coromant, lays out her vision.
What are the trends?
Edge computing
Why wait for data to travel when you can process it on the spot? Edge computing puts the brains of the operation right where the action is, on the machine floor itself. This method captures and processes data directly at the source, shortening response times and cutting down on the bandwidth usually swallowed by central servers. It’s all about smarter, faster decision-making that keeps pace with the factory’s pulse.
Robotics
Robotics have moved past the novelty stage and are deeply integrated into modern manufacturing. At our Gimo production facility, a World Economic Forum Lighthouse Facility, robots manage tool changeovers autonomously, no humans required. It’s what the industry calls “lights out” production, and it’s expanding across our operations, powering a new era of efficiency where the machines keep things moving, day and night.
Digital twins
As you might have already guessed from the name, digital twins provide a digital replica of the production line, which is then tested in a risk-free, digital sandbox before a single real component is touched or worse, botched. This allows us to simulate processes and pinpoint potential issues in the digital realm without wasting valuable resources. The power of foresight ensures that when we go live, we’re already steps ahead in quality and efficiency.
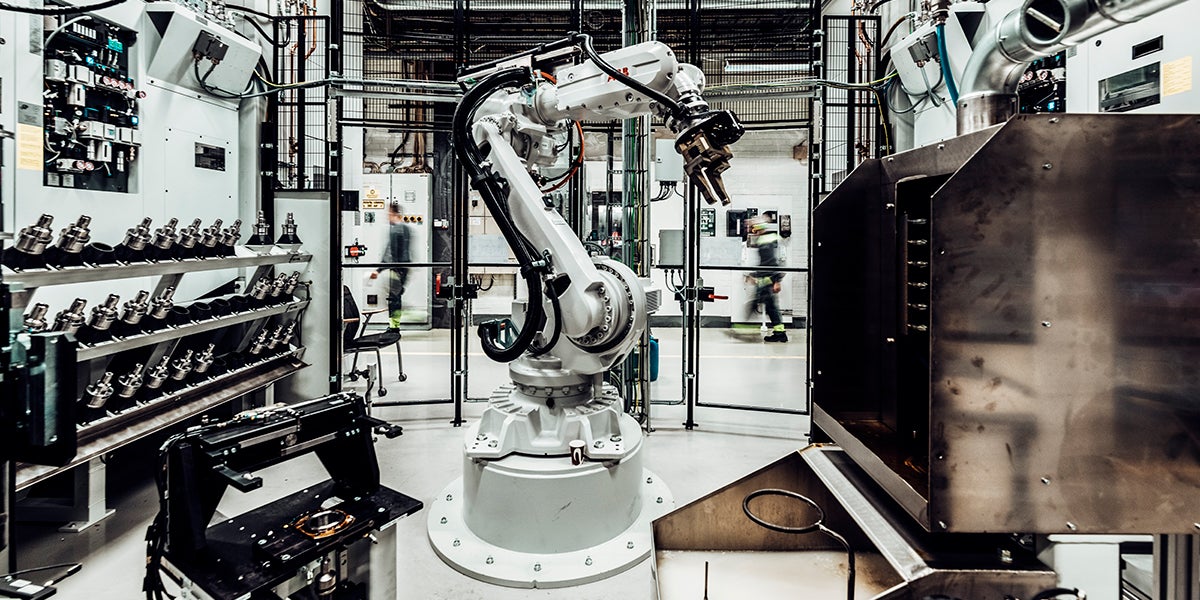
What can product integrations do?
What does product integration entail? It involves merging software platforms, various data sources, technologies, and products to create a complete view of the manufacturing process—it's the grease and gears driving the rapid machinery of modern manufacturing.
Product integration brings several key benefits: it reduces human intervention and predicts workforce needs, improves product quality by incorporating robotics and minimizing human errors, especially in repetitive tasks, and helps manage operational costs by providing accurate forecasts of production expenses. Additionally, it enhances supply chain management by allowing you to track what your production will produce and consume, ensuring that your supply chain is always current.
Real-time data plays a crucial role in improving efficiency by enhancing collaboration and communication between different departments. Integrated solutions bridge the information gap by presenting the same data across multiple sources, enabling informed decision-making. They leverage both real-time and historical data through reporting and maintenance tools, helping prevent issues before they arise. This approach is essential in an industry that is constantly evolving.
But here’s the catch: software solutions are designed to simplify our work, yet they often add complexity with more variables, more data, and a flood of chatty systems connected through the Internet of Things. The task quickly becomes about collecting, sorting, and interpreting an overwhelming stream of numbers, signals, and constant activity. This isn’t just busywork; it’s critical because real-time and historical analytics provide a full view of operations, allowing us to address issues early and forecast needs, from staffing levels to predicting when a machine might fail. It’s all about keeping the factory floor humming, not screaming.
Getting it right from the start
Before diving headfirst into data sets from various suppliers that don’t always speak the same language, start by mapping out your data flow. Know exactly where each byte comes from, where it’s headed, and spot any bottlenecks along the way. You can’t tackle everything at once, so prioritize by identifying which data matters most and how you’re going to use it.
Next, understand the specifics of your software: what data it collects, how it collects it, and how it gets transmitted. Rigorous testing is key to ensuring this data integrates seamlessly with your CAM system, staying uncorrupted and intact. Using cloud infrastructure adds scalability to your operations.
Don’t forget the service contracts—make sure your supplier’s support meets your expectations, especially when things go haywire. And let’s not ignore cybersecurity; the more data we exchange, the more important it becomes to keep it secure.
And document everything—what’s been integrated, why, and how it fits into the bigger picture.
Last but not least, there’s the human factor. Equip your team with the right training to handle these new integrations. A solid service contract with your supplier will ensure you get the support you need, especially if you’re navigating new tech or undergoing a major upgrade.
By strategically embracing product integrations, you tap into real-time data, streamline operations, and boost decision-making capabilities. In the evolving landscape of Industry 4.0, well-planned, secure, and thoroughly documented integrations are your best bet for leveraging the full potential of digital manufacturing.
So, why should your machines start talking to each other? Because isolation in a connected world spells disaster. Systems that fail to communicate are a recipe for costly mishaps and operational snafus. More crucially, fostering system-wide communication is essential to keep from falling light years behind the competition. In the fast-evolving landscape of Industry 4.0, staying disconnected isn't just inconvenient—it risks obsolescence. Don’t let evolutionary gaps leave your operation in the dust.
How about AI? Download our free guide How to survive AI and thrive and discover how the most polarizing technological revolution of our time manifests itself in the manufacturing industry.
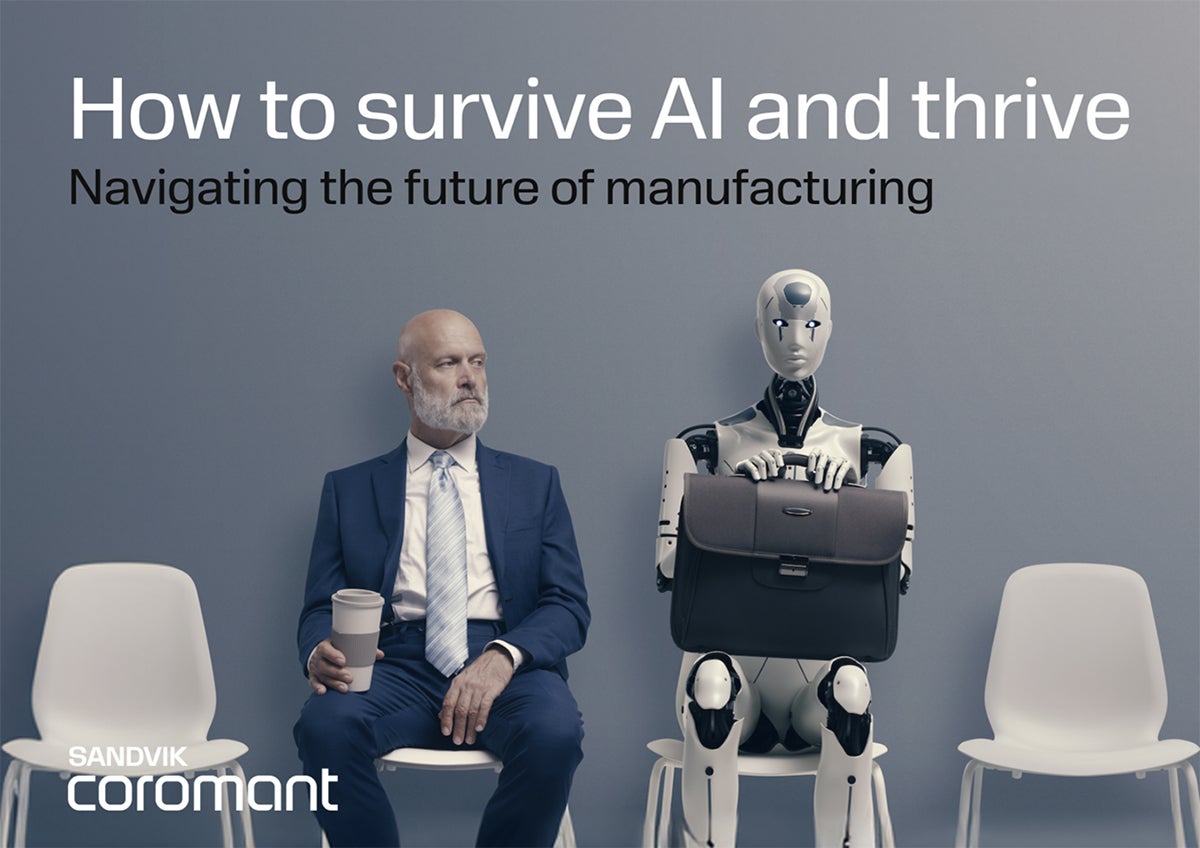