When one scrapped component is too many
Effects of poor component quality
Having the right quality on each part that is produced is critical. Producing components according to quality expectations minimizes scrap. This becomes especially important when machining expensive, high-value components. The impact you are trying to avoid:
- Increased scrap rate
- Longer time to produce batch
- Higher production cost and lower profit
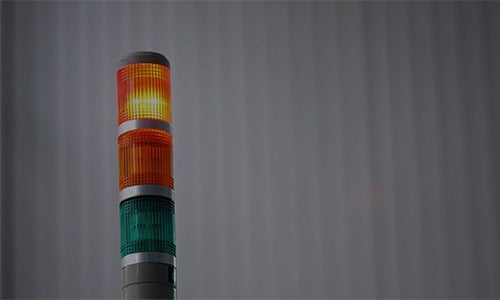
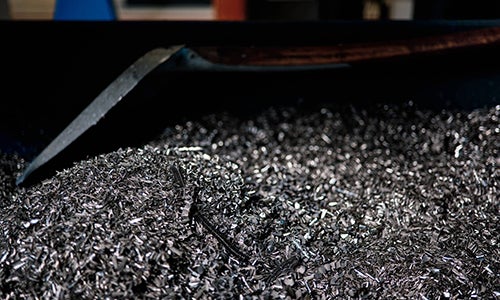
What would zero scrap mean to your business?
Working with advanced production of complex components, just the raw material itself is expensive, and after having put hours of machining into the component, the value of the part is very high. Leaving no room for error.
Common culprits and possible improvements
Challenge | Possible solutions |
Faulty simulation before machining starts | Auto-generated 3D models for accurate programming and simulation |
Wrong choice of tool or cutting data | Data-driven recommendations based on your component feature, material and machine |
Unstable machining process | Modern tooling concepts with predictable and secure performance |
Suboptimal tool path | NC code generated from software ensuring optimal tool path |
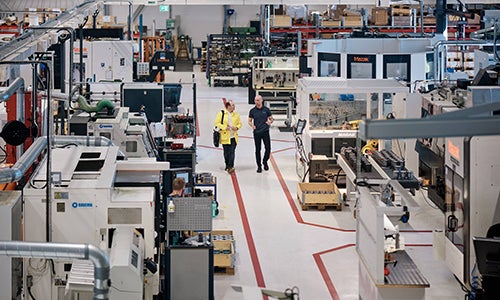
3 potential areas to explore
1. Improve machining predictability
- Secure machining processes without unexpected disruptions
- Timely tool changes and no unexpected damages to the component
2. Increase automation
- Automated NC code and tool model creation secures that optimal tool paths are used as well as removes potential discrepancies between digital twin environments and the real workshop
- Automate manual repetitive tasks in process and operations planning to avoid human errors
3. Access data and best practice
- Avoid quality issues by accessing correct data, such as cutting parameters and machining input and by utilizing knowledge and best practice in operation planning