Thread whirling application tips
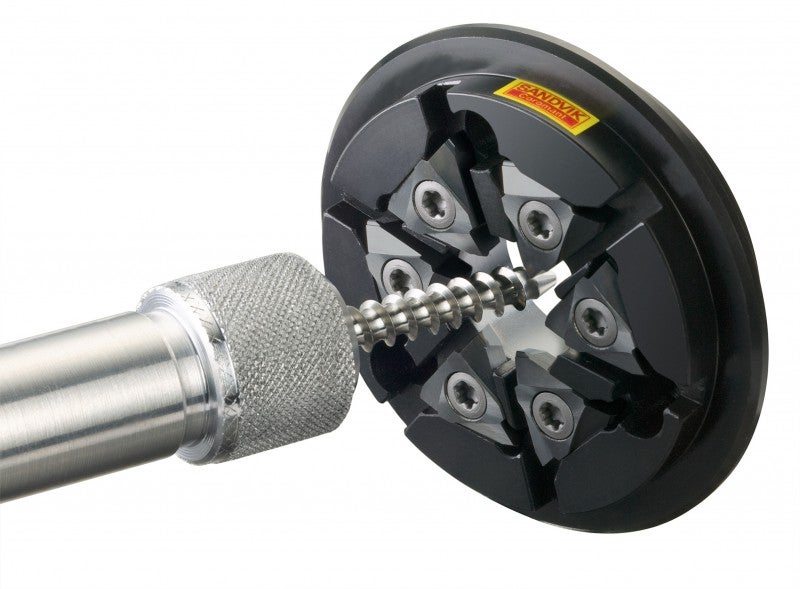
Thread whirling set-up
Follow these steps for a successful set-up:
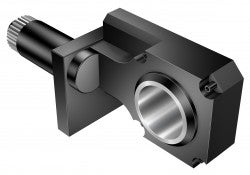
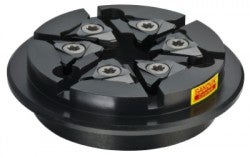
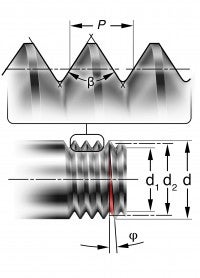
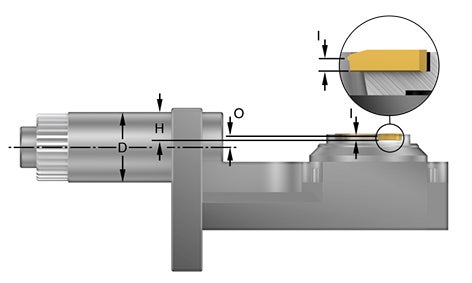
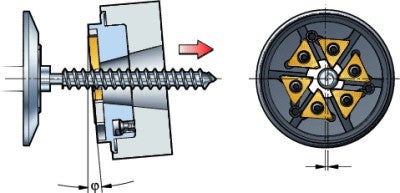
- Check which whirling unit that will be used
- Choose a whirling ring suitable for the whirling unit
- Check thread profile to be machined. Is a standard insert available? If not, a detailed drawing of the profile and diameter will be needed
- Measure the offset of the cutting point versus the swivel axis
a) Take out the whirling unit from the machine
b) Measure the diameter (D) of the drive shaft
c) Install the whirling ring in the drive unit
d) Put the whirling unit body on a flat table and zero the clock at the outer diameter of the drive shaft
e) Measure the difference in height between the outer diameter of the drive shaft and the insert seat in the whirling ring (H)
f) Get the cutting point position for the insert (I) from the insert drawing
g) Calculate the offset (O): O = D/2 - H + I - Talk to a specialist for set-up advice and cutting data recommendations. Preferably use a thread whirling calculator
- Tilt the whirling unit to the desired helix angle of the screw and make sure the tool is maintained centred to the component
- Program the ring off-centre, to get the correct screw diameter
- Rotate the whirling ring and component in the same direction (climb milling) for optimum tool life
- Rotate the workpiece at a slower speed, determined by its diameter and the lead of the thread being made
- Coordinate movement of the whirling ring with the rotation of the component for best surface and productivity
Note! Many thread whirling units have a gear box reduction. Take into consideration that the programmed rpm will not be the actual output in these cases - Run a test component and measure the dimensions of the component. Adjust if needed, see the troubleshooting section
Related information
Troubleshooting
Use this list of causes and solutions for successful thread whirling. It is recommended... keyboard_arrow_right
Thread whirling
Thread whirling is similar to a thread milling process, the difference is that the... keyboard_arrow_right
Bone screw machining
Machining challenge is to avoid burr formation in milled features in the tip when... keyboard_arrow_right
CoroMill® 325
Medical bone screws, implants, feed screws, worm gears and other micro-components... keyboard_arrow_right