Main fitting
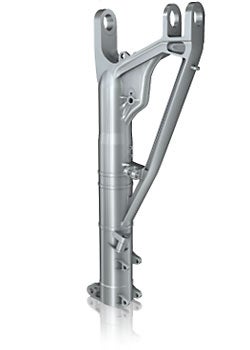
Typical landing gear components are main/nose/centre fitting, piston/slider, truck/bogey beam, drag brace and links. The main materials are high alloy steels such as 300M. But there is a trend that these will be produced in titanium alloys such as Ti-5553. The main challenges in the main fitting are deep hole drilling, internal turning and profile milling.
CoroMill® MS20 – pocketing
- M-M20 geometry gives higher security in tougher applications
- In case of sensitive / vibration prone applications and / or applications requiring a sharper cutting edge, the E-L50 geometry can be used
- The higher edge line toughness of these geometries allows the inserts to be used with higher productivity (high cutting data) in stable operations
- Robust steel shank design ensures better stability and less deflection. The improved tool body material can withstand chip rubbing better
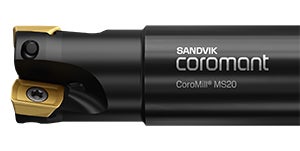
Deep hole machining
The T-MAX 424.10 has setting possibilities on the diameter with exchangeable cartridges and shims. Close diameter tolerance and high surface finish.
Standard diameter range 65-130 mm, Tailor Made diameter range 130-183.99 mm and wide range of engineered solutions Diameter range 184.00-327.99 mm on request.
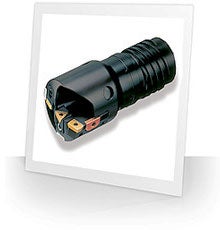
Profile milling
CoroMill® 216 is a robust ball nose end mill perfect for semi-finish profile milling, available cutter dia 10-50 mm. The cutter has inserts with two edges for effective and general contouring and copy milling. Maximum depths of cut up to 44 mm and max feed per tooth up to 0.6 mm.
More information:
Read more about CoroMill 216
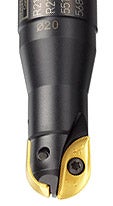
Internal turning
A standard Silent tool boring bar programme up to 250 mm diameter and 14 x dia to length capability is available. This range of tools can produce component features of an extraordinarily high standard.
The serration lock coupling is now equipped with a full range of cutting heads with high pressure coolant capability. The first choice grades are GC4325 for roughing and CB7015 for finishing.
CoroTurn SL70
More videos:
- High pressure coolant
- CoroTurn SL
- CoroTurn SL quick change
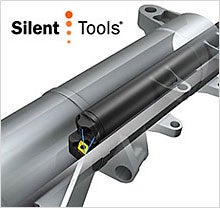
CoroMill® 690
Material: Titanium alloys – Ti5Al-5V-5Mo-3Cr
Component: Engine strut
Coolant: External
Productivity increase: 40%
Increased tool life: 100%
The competitor achieves 50 minutes in cut and CoroMill 690 achieves 85 minutes in cut. The operator said “The competitor cutter has a tendency to move the component, compared to the new Coromant Long Edge which is much smoother cutting”.
Tool: | Competitor | CM690 Dia 84 - 5 teeth |
Insert: | Competitor | R690 - IC 14,5 |
Grade: | Competitor | GC1030 |
vc: | 21 m/min | 21 m/min |
vf: | 2 mm/r | 2.8 mm/r |
ap/ae: | 50-75/20-75 mm | 50-75/20-75 mm |
Tool life: | 50 min | 85 min |
CoroMill 690
Main fitting
Typical landing gear components are main/nose/centre fitting, piston/slider, truck/bogey... chevron_right
CoroMill® 690
CoroMill 690 is developed specifically for high-productivity 2D profile milling... chevron_right
Thrust fitting
The thrust fitting is normally produced in titanium and is located between the wing... chevron_right
Shaft
Made from high alloy steel or inconel the major challenge here is the length and... chevron_right