Best practices for predictable machining
Why it matters
Machining predictability is paramount for ensuring consistent product quality, optimizing throughput, and minimizing waste. In a time when complex requests and material costs keep rising, knowing how a machine will respond in different conditions gives you the opportunity to plan efficiently, ensuring safety and guaranteeing precision.
But predictability isn't just about assurance - it's about harnessing your machine's full potential while saving on time, money, and trouble. Beyond hands-on tips and tricks, this ambition would translate into long-term data analysis and automation on the modern shop floor.
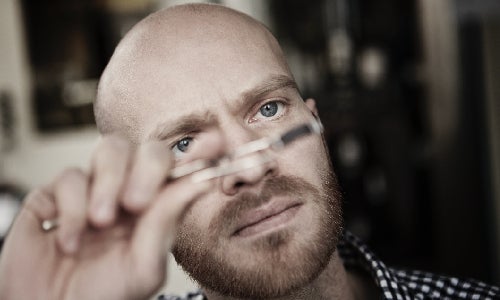
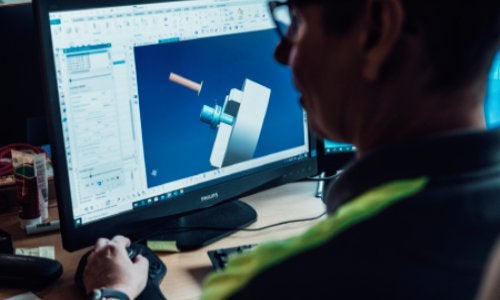
Data eliminates guesswork
Use data analytics to address the early signs of bad, untimely, and inaccurate decisions. Modern machining produces a treasure trove of data which can be analyzed using advanced software tools. Move from intuition to insight with:
- Tool wear prediction: Forecast when a tool is likely to wear out or break, reducing unexpected downtime.
- Error detection: Identify irregular patterns that might indicate a looming problem.
- Optimized operations: Adjust machining parameters in real-time for peak performance.
The right tool at the right time
Choosing the right tools for the job is half the battle. It's a no-brainer, but always ensure you're using tools optimized for your specific material and operation. Regular maintenance checks and timely replacements will keep performance consistency, which is crucial if you rely on fully automated production cells for regular output 24/7.
Remember, predictable machining begins with dependable tools that are in prime condition.
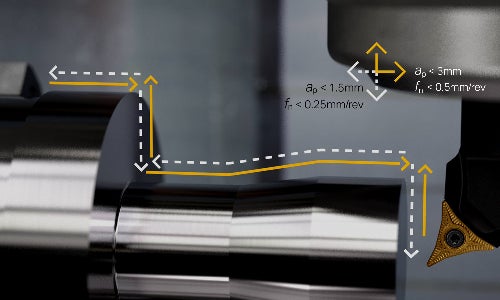
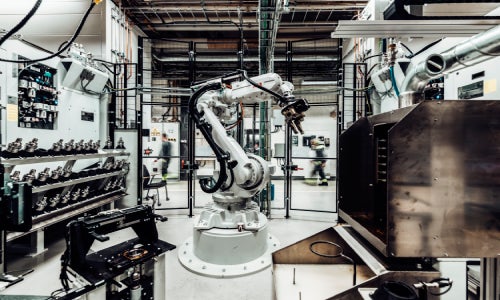
A symphony of integrated systems
The sound of automation. Connect your CAD/CAM, CNC, and other systems to enable digital simulation and verification to minimize the risk of human error. When your design, simulation, and execution tools are synchronized, you can anticipate and mitigate issues before they arise. Integrated systems offer:
- Real-time feedback
- Seamless workflow
- Predictive maintenance
The human touch and upskilling
Without all the aforementioned factors, achieving consistent, long-term machining predictability can be rather challenging.
And while technology plays a pivotal role in some of the decision-making, the expertise of your operators is invaluable. Continuous training, understanding of the machine's intricacies, and staying updated with industry trends can drastically improve predictability.
Machines may do the heavy lifting, but human judgment ensures all the fine-tuning will lead to peak performance and top-notch results.
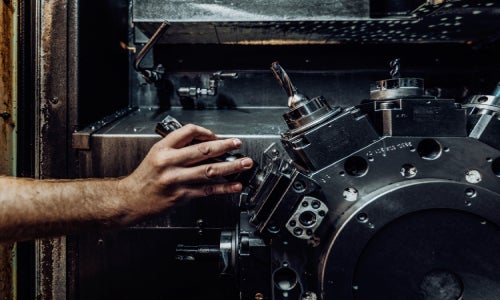
Explore solutions to increase machining predictability
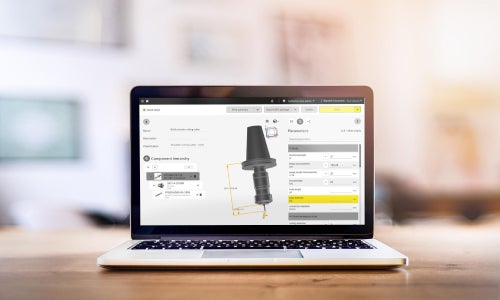
CoroPlus®
The CoroPlus® portfolio contains several connected solutions that will boost the predictability factor in your machining.
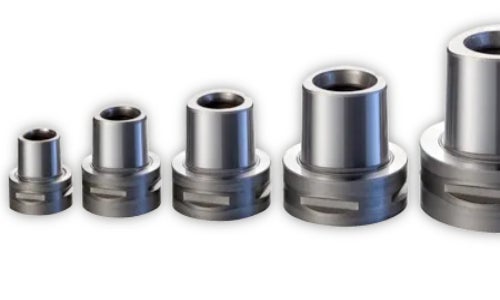
Coromant Capto®
Predictable machining relies on stable tool holding. Find out more about Coromant Capto®.
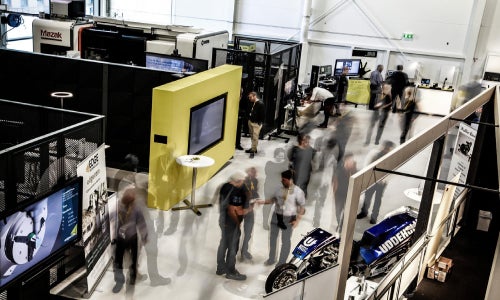
Visit our Sandvik Coromant Centers
The focal point of our machining expertise, knowledge, digital machining, and sustainability.
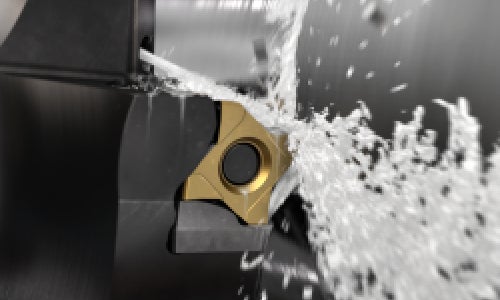
Tooling up for faster payback
Don't let any bad tool decisions tank your bottom line. get it right from the start when buying new machines.