Fremtidens fabrik
Sandvik Coromants værktøjsfabrik i Gimo i Sverige er blevet anerkendt af World Economic Forum som en avanceret Industry 4.0-fabrik.
Sandvik Coromants værktøjsfabrik i Gimo nord for Stockholm er en fabrik med høj automatiseringsgrad, som udnytter de mange fordele med digitalt forbundet produktion fuldt ud. Det blev for nylig anerkendt af World Economic Forum, som udpegede Gimo som et af deres globale “fyrtårn”. Hvert enkelt fyrtårn udvælges på basis af en undersøgelse, som omfatter over 1.000 produktionsenheder, ud fra deres resultater inden for anvendelse af digitale teknologier og fremvisning af konkrete fordele.
Ifølge World Economic Forum har fabrikken i Gimo skabt en digital rød tråd gennem deres produktionsprocesser, som har øget produktiviteten betydeligt. Ét eksempel er den ‘berøringsfri omstilling’, som gør det muligt at skifte designmønstre automatisk, også under ubemandede skift. Førende fremskridt som disse betyder, at Gimo nu bliver en del af det globale netværk af fyrtårne, som åbner dørene og deler viden med andre produktionsvirksomheder.
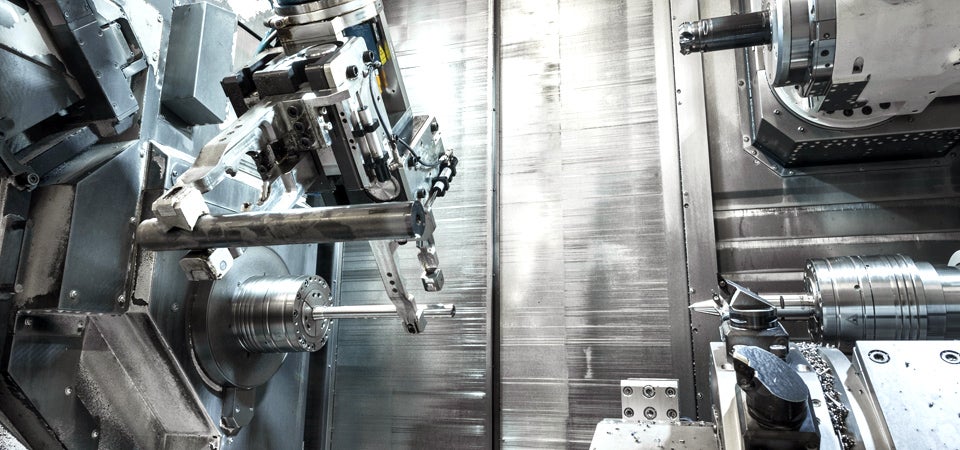
I Gimo er man meget stolte over prisen, siger Lars Matiasson, som er direktør for produktionsteknologisk værktøj hos Sandvik Coromant. Det skyldes, at den anerkender kulminationen af en innovationsindsats, der har stået på i længere tid. “Vejen til digitalisering her i Gimo startede egentlig for 30 år siden med implementeringen af parametrisk CAD/CAM, og nogle få år senere koblede vi det til vores intelligente automatisering i den første digitale tråd i vores produktion. Det har derfor i høj grad været en evolution frem for en revolution.
“Nu kan vi se en digital rød tråd gennem fabrikken, fra lagerstyring og hele vejen til maskinernes performance og til prædiktiv vedligeholdelse. Denne innovationsånd har altid været en top-down-opgave. Direktører og ledere i Gimo har hele tiden opfordret deres ingeniører til at tænke anderledes og skabe forandring. I sidste ende har det handlet om at undersøge, hvordan teknologi kan bruges til at forbedre effektiviteten og øge fabrikkens konkurrenceevne, hvilket igen har bidraget til at sikre en bæredygtig fremtid.”
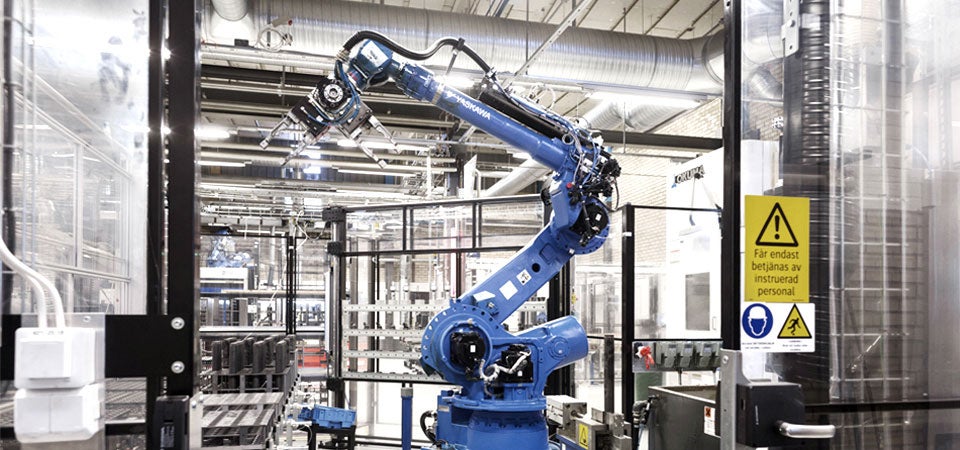
Den berøringsfri omstilling er et eksempel på dette. Tidligere skulle designmønstre i produktionsceller skiftes manuelt, og operatører fra dagskiftet klargjorde maskinerne til at køre om natten. Det tog tid og krævede ressourcer og medførte begrænset fleksibilitet under ubemandede skift. Alternativet var at investere i intelligent automatisering med ultrafleksible robotter, maskiner, værktøj og fiksturer, der tilsammen kunne udføre komplekse berøringsfri omstillinger uden menneskelig indgriben.
“Folk taler om lean produktionsteknikker som skift af forme på et minut, men vi ville endnu mere. Vi ønskede en opsætning, der ikke krævede arbejdskraft,” siger Matiasson.
“Det har været en læringsproces. Den første automatiserede celle fungerede ikke så godt, som vi havde håbet. Faktisk var den ikke engang så effektiv som en operatør og en maskine. Men sådan er det med digitalisering. Man lærer af sine fejl. Gradvist lykkedes det os at opnå betydelige forbedringer, og robotcellerne begyndte at nå den effektivitet, vi havde behov for. Det er vigtigt at prøve sig frem og begå fejl, når man skal forbedre sig.”

Digital teknologi bruges også til at opnå forbedringer på andre områder i Gimo. Det gælder for eksempel vedligeholdelse. Der monteres i stigende grad sensorer på forskelligt udstyr i fabrikken til indsamling af data for en voksende liste af parametre som tryk, temperatur, vibration og akustik. Kombineret med avancerede analyser kan disse data afsløre mønstre og problemer, før de resulterer i stilstandstid.
Teknikere indsamler nu data fra hele produktionsanlægget – fra robotter, CNC-maskiner og også fra det skærende værktøj. Når disse data er trukket ud og analyseret, kan de give værdifuld viden om udstyrets tilstand. Disse data kan så bruges til at forudse og forebygge fejl og dermed forbedre anlæggets effektivitet.
Sandvik Coromant anvender i stigende grad analyser i realtid i produktionsmiljøet, så de bliver i stand til at foretage endnu mere nøjagtige og rettidige justeringer på maskinerne. “Den næste fase bliver indføring af meget avancerede teknikker som kunstig intelligens og maskinlæring, hvor maskinerne kan lære af historiske data og opnå et element af selvstyring. Det er et meget spændende emne.”
Selvom virksomheden har opnået betydelige tekniske fremskridt og er blevet udpeget som fyrtårn fra Word Economic Forum, så stopper digitaliseringen i Gimo aldrig.