Best practice - Main shaft
The main shaft transforms the revolution from the rotor hub into the gearbox with a typical maximum rotation speed of ~20 rpm.
The main shaft is supported by bearings. It is hollow inside, for hydraulic piping and electric cables. The big torque from the rotor is transformed through the main shaft. Therefore the main shaft needs to be large, heavy, and extremely strong.
Back to main shaft
Machining operation overview:
1. Turning – Heavy duty roughing
2. Turning – Semi roughing
3. Turning – Finishing
5. Drilling – Short hole
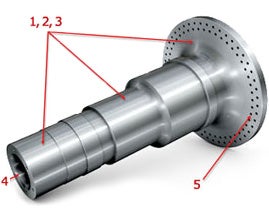
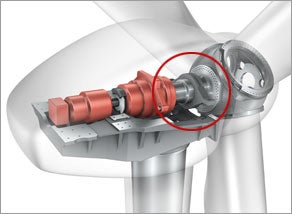
Common main shaft
- 34CrNiMo6, CMC=02.1/02.2
- 42CrNiMo6, CMC=02.1/02.2
- 22 ton blank weight
- 14 ton after machining
- 8 ton of material removed
- Machining time: 30-40 hours
- Forged with a flange
- Typical material:
- Example of a 2MW main shaft:
- Example of dimensions:
- Large dia: 1,800 mm, small dia 400 mm
- Length: 3,500 mm
Workpiece
- Large dia: 1.8 metres
- Small dia: 0.4 metres
- Length: 3.5 metres
- 34CrNiMo6, CMC=02.1/02.2
- 42CrNiMo6, CMC=02.1/02.2
- Forged skin
- Dry machining
- Diameter:
- Material:
- Coolant:
- Challenge:
- Intermittent due to diameter inconsistency from forging and clamping
Holder | Coromant Capto C10 Heavy Duty |
Insert | SCMT 380932-R5 |
Grade | GC4235 |
Depth of cut (ap) | Maximum 30 mm |
Cutting speed (Vc) | 40-90 m/min |
Feed (fn) | 1.2-1.8 mm/rev |
Turning
Heavy duty roughing
The T-MAX® P concept encapsulates the contributions of productive turning. The geometries are carefully designed for perfect chip breaking. Metal removal at high feed and in dry conditions is made possible with state-of-the-art grades for your application.
To optimize productivity with better precision and stability – use Coromant Capto® tool holding system. The modular system is equally effective in turning, milling, drilling and boring.
The same cutting units and adaptors can be used in different applications and machines, which makes it possible to standardize on one tooling system giving substantial reduction of inventory.
Holder | Coromant Capto | Coromant Capto |
Grade | GC4325 | GC4325 |
Depth of cut (ap) | 7-10 mm | 5-10 mm |
Cutting speed (Vc) | 70-120 m/min | 70-120 m/min |
Feed (fn) | 0,5-2,5 mm/rev | 0,5-1.5 mm/rev |
Turning
Semi roughing
A Coromant Capto holder is also the first choice for the semi-roughing operation. Combine with a GC4325 grade for best productivity.
A round insert will give you optimal productivity with high feed and good chip control. If your machine requires lower feeds however, a CNMM-QR is recommended.
Top of page
Holder | Coromant Capto |
Insert | DNMX 150616-WMX |
Grade | GC4215 |
Depth of cut (ap) | 2-3 mm |
Cutting speed (Vc) | 160-220 m/min |
Feed (fn) | 0.5-0.8 mm/rev |
Turning
Finishing
A Coromant Capto holder is also the first choice for the finishing operation. Combine with a GC4215 grade for best productivity and surface finish.
The ingenious design of the Sandvik Coromant –WMX wiper geometry makes multiple feed rates possible with maintained surface quality.
Drilling
Short hole drilling
Just by exchanging a conventional drill with a CoroDrill 880, you can double the number of drilled holes in the same amount of time.
Its step technology gives outstanding cutting force balance, providing significant improvements on productivity as well as of the hole quality. This, in combination with high performance grades makes it outstanding when it comes to rapid hole making.
Hole dimension | Tool diameter (Dc): 39 mm Length (L): 140 mm |
Drill | 880-D3900C5-04 |
Central insert | 880-07 04 06H-C-GR |
Grade | GC1044 |
Periphery insert | 880-07 04 W12H-P-GR |
Grade | GC4024 |
Cutting speed (Vc) | 200-250 m/min |
Feed (fn) | 0.15-0.20 mm/rev |
Coolant | Yes |