Framtidens fabrik
Sandvik Coromants produktionsenhet i svenska Gimo har utsetts till en avancerad Industri 4.0-anläggning av World Economic Forum.
Sandvik Coromants anläggning för verktygstillverkning i Gimo, norr om Stockholm, är en i hög grad automatiserad anläggning som har anammat de många fördelarna med uppkopplad tillverkning fullt ut. Detta är något som nyligen uppmärksammades av World Economic Forum som utsåg Gimo till en av sina globala föregångsanläggningar (ett s.k. ”lighthouse”). Varje lighthouse väljs ut bland fler än 1 000 tillverkningsanläggningar, baserat på hur väl de har lyckats att införliva digitala tekniker och uppvisa konkreta resultat.
Enligt World Economic Forum har anläggningen i Gimo skapat en digital röd tråd genom sina tillverkningsprocesser, något som har ökat produktiviteten avsevärt. Ett exempel är deras automatiska omkoppling som gör det möjligt att byta designmönster automatiskt, även under obemannade skift. Sådana framsteg i toppklass innebär att Gimo nu blir en del av det globala lighthouse-nätverket där man öppnar sina dörrar och delar med sig av sina erfarenheter till andra tillverkningsföretag.
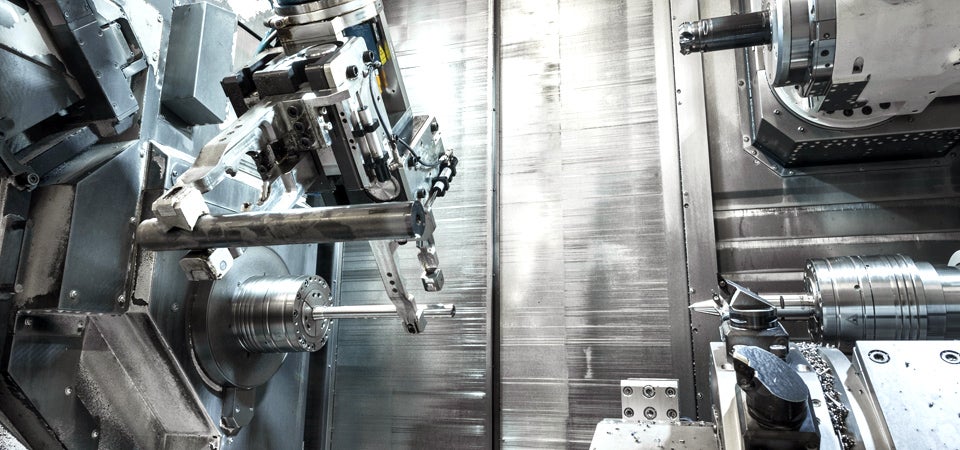
Utmärkelsen har tagits emot med en känsla av stolthet vid anläggningen i Gimo, säger Lars Matiasson, director of production technology tools hos Sandvik Coromant. Inte minst för att det är ett erkännande för de stora ansträngningar som har gjorts för att uppmuntra till ett innovativt tänkande. ”Resan mot digitalisering här i Gimo började faktiskt redan för 30 år sedan med implementeringen av parametrisk CAD/CAM och några år senare kombinerade vi det med vår smarta automatisering, för att därmed skapa den första digitala processen i vår produktion. Det har alltså snarare handlat om evolution än revolution.
Nu ser vi en digital röd tråd genom hela anläggningen, från lagerstyrning hela vägen till maskinprestanda och prediktivt underhåll. Innovationsviljan har alltid genomsyrat företaget uppifrån och ner. Direktörerna och cheferna vid anläggningen i Gimo har alltid uppmuntrat ingenjörerna att tänka annorlunda och driva på förändringar. I slutänden handlar det om att förstå hur teknik kan användas för att öka anläggningens effektivitet och konkurrenskraft. Det, i sin tur, har hjälpt till att skapa en hållbar framtid.”
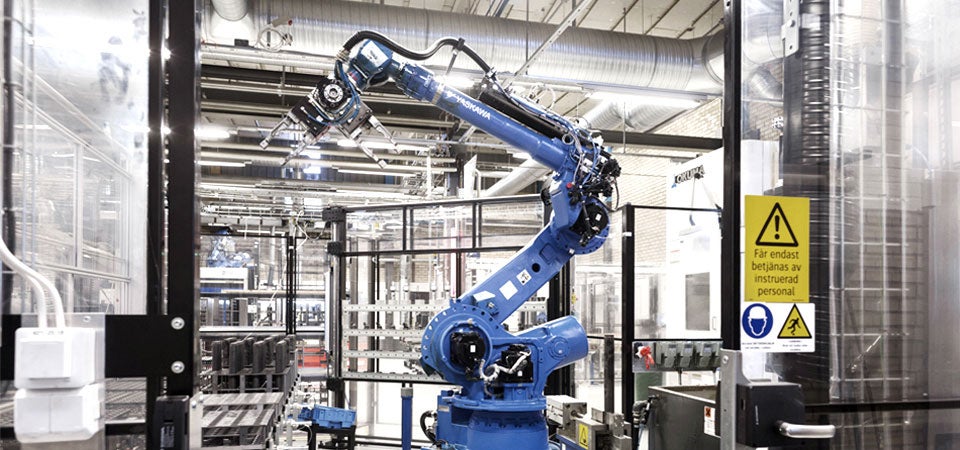
Den automatiska omkopplingen är ett exempel på detta. Förr i tiden behövde man byta designmönstren i produktionscellerna manuellt och operatörerna på dagskiftet fick förbereda maskinerna så att de kunde köras hela natten. Detta var både tids- och resurskrävande, och begränsade flexibiliteten under obemannade skift. Alternativet var att investera i smart automatisering med superflexibla robotar, maskiner, verktyg och fixturer som tillsammans kan utföra komplexa omkopplingar helt automatiskt och utan mänsklig tillsyn.
”Folk talar om resurssnåla tillverkningstekniker som exempelvis formbyten på en minut, men vi ville gå ett steg längre. Vi ville ha en fullt automatiserad maskininställning”, säger Lars Matiasson.
”Det var en utmaning i början. Den första automatiserade cellen fungerade inte så bra som vi hade hoppats. Den var faktiskt inte ens lika effektiv som en operatör och en maskin tillsammans. Men det är det som är grejen med digitalisering – du måste först misslyckas för att lära dig något på vägen. Undan för undan lyckades vi förbättra resultaten betydligt och robotcellerna började komma upp i de effektivitetsnivåer som vi var ute efter. Det är viktigt att prova sig fram för att kunna förbättras.”

Digitala tekniker används också för att ta fram förbättringslösningar på andra områden vid anläggningen i Gimo, som exempelvis underhåll. Sensorer används allt oftare i anläggningens olika maskiner för att samla in data utifrån en allt längre lista över parametrar såsom tryck, temperatur, vibration och akustik. Dessa data kan, i kombination med sofistikerade analyser, avslöja mönster och problem innan driftavbrott inträffar.
Ingenjörer kan nu samla in data från hela produktionsanläggningen – från robotar, CNC-maskiner och till och med själva skärverktygen. När dessa data väl har extraherats och analyserats kan de bidra med en värdefull insikt i maskinernas skick. Denna information kan i sin tur användas för att förutse och förebygga driftavbrott, och därmed öka anläggningens effektivitet.
Sandvik Coromant implementerar även realtidsanalyser i allt större utsträckning i sin produktionsmiljö för att kunna justera maskinerna exakt och i god tid. ”Nästa steg kommer att bli att introducera mycket avancerade tekniker såsom artificiell intelligens och maskininlärning, där maskinerna kan lära sig från historiska data och i viss mån bli självstyrande. Det är ett riktigt spännande område.”
Trots dessa anmärkningsvärda tekniska framsteg och det faktum att de har utsetts till ett av Word Economic Forums lighthouse, är detta bara början på Gimo-anläggningens digitala resa.