Dekarbonizacja dróg na świecie
Według raportu Międzynarodowego Forum Transportowego (ang. International Transport Forum – ITF) globalna aktywność transportowa ma wzrosnąć dwukrotnie do 2050 r. w porównaniu z poziomem z 2015 r. Z uwagi na globalny problem zmian klimatycznych ważnym zadaniem jest produkowanie wydajniejszych pojazdów napędzanych bardziej ekologicznymi paliwami. W swoim artykule Eduardo Debone, Senior Manager w dziale zarządzania ofertą dla motoryzacji w firmie Sandvik Coromant będącej światowym liderem w branży obróbki skrawaniem metali, mówi o tym, jak wybór materiału i innowacje w dziedzinie obróbki skrawaniem metali wspierają przechodzenie na pojazdy bardziej przyjazne dla środowiska.
Pandemia COVID-19 spowodowała krótkotrwałą redukcję aktywności transportowej, jednak nadal przewiduje się, że wykorzystanie pojazdów będzie rosło przez kolejne dekady wraz ze wzrostem liczby ludności na świecie oraz ciągłym rozwojem gospodarczym. Zwiększona produkcja pojazdów w celu zaspokojenia rosnącego zapotrzebowania jest nieunikniona – prawdziwym wyzwaniem jest przestawienie produkcji na pojazdy bardziej ekologiczne. Międzynarodowa Agencja Energetyczna (ang. International Energy Agency – IEA) informuje, że transport odpowiada już za 24% emisji bezpośrednich CO2 ze spalania paliw, a prawie trzy czwarte z tego generują pojazdy drogowe.
Ramowa Konwencja Narodów Zjednoczonych w sprawie zmian klimatu (ang. United Nations Framework Convention on Climate Change – UNFCCC) wskazuje na konieczność obniżenia emisji w sektorze transportu i w roku 2021 opublikowany został związany z tym plan działań na rzecz klimatu (ang. Climate Action Pathway). Wizja UNFCCC przewiduje, że do 2050 r. transport pasażerski i towarowy poddane zostaną całkowitej dekarbonizacji po przejściu na bardziej ekologiczne technologie stosowane w pojazdach. Zmiana ta obejmuje przechodzenie na zeroemisyjne środki transportu oraz zwiększanie wydajności pojazdów.
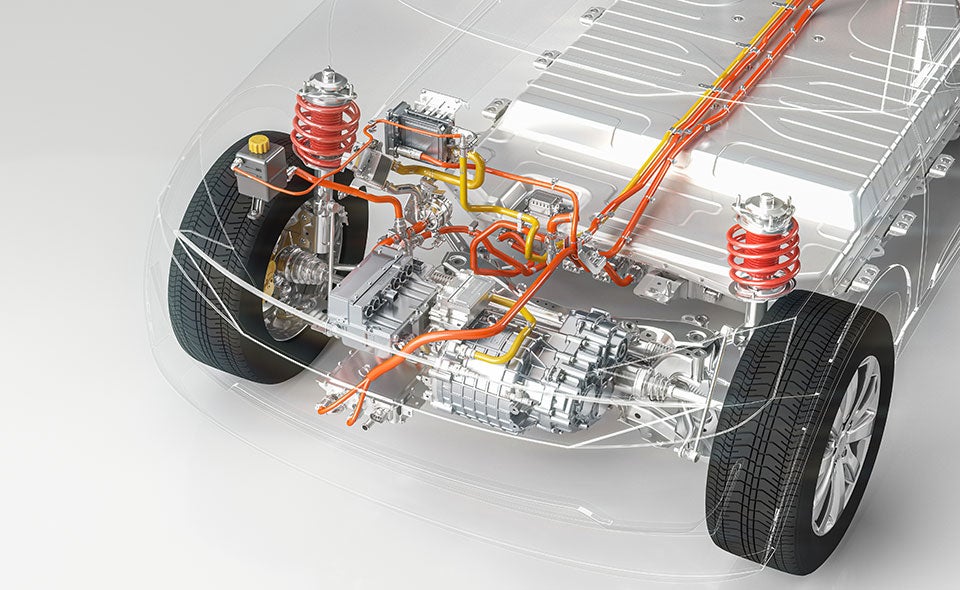
Ewolucja pojazdów elektrycznych
Do zeroemisyjnych środków transportu należą pojazdy elektryczne, które według dyrektora wykonawczego IEA, Fatiha Birola, „mają do odegrania nieodzowną rolę w osiągnięciu zerowej emisji netto na świecie”. Używając energii elektrycznej z sieci, szczególnie ze źródeł odnawialnych, do ładowania akumulatorów napędzających silniki elektryczne, pojazdy elektryczne nie emitują spalin z układu wydechowego i dlatego są opcją bardziej przyjazną dla środowiska niż pojazdy z silnikiem spalinowym.
Według opracowanego przez IEA raportu „Global EV Outlook 2021” na koniec roku 2020 na całym świecie na drogach było 10 mln samochodów elektrycznych, a liczba zarejestrowanych „elektryków” wzrosła w tym roku o 41%. Popularność pojazdów elektrycznych wyraźnie rośnie, a ich upowszechnienie można dodatkowo przyspieszyć, eliminując tzw. „niepokój o zasięg”, czyli obawę, że samochód nie jest w stanie pokonać całego dystansu, aby dotrzeć do punktu docelowego.
Zasięg zależy nie tylko od akumulatora. Obok solidniejszej infrastruktury ładowania i ulepszonej konstrukcji akumulatorów każdy element pojazdu musi być lżejszy. Pojazd elektryczny o mniejszej masie wymaga mniej energii do pokonania danego dystansu i dlatego może dojechać dalej na jednym ładowaniu, co oznacza większy zasięg.
W zmniejszaniu masy pojazdów elektrycznych dużą rolę odgrywa aluminium, które waży zaledwie ułamek tego, co tradycyjne materiały stosowane do produkcji samochodów – stal i żeliwo. W istocie aluminium jest obecnie powszechnie wybierane do produkcji różnych części pojazdów, takich jak podwozie, panele wewnętrzne, obudowa silnika i osłony akumulatorów. Według organizacji Aluminum Transport Group (ATG) zastosowanie aluminium do zmniejszenia masy pojazdu elektrycznego może zapewnić proporcjonalne zwiększenie zasięgu. Na przykład przy zmniejszeniu masy pojazdu o 20% powinien on być w stanie przejechać o ok. 20% większy dystans na jednym ładowaniu.
Profesjonalna obróbka skrawaniem
Części wykonane z aluminium są jednak zawsze trudniejsze do obróbki. Aluminium jest bardziej miękkie niż większość metali, przez co praca z nim może stwarzać problemy. Ponadto temperatura topnienia stali nierdzewnej wynosi 1510°C, a w przypadku aluminium jest to 660°C. Podczas obróbki aluminium niższa temperatura topnienia metalu może, z powodu ciepła wytwarzanego przez tarcie przy dużej szybkości, powodować gromadzenie się wiórów i przywieranie ich do narzędzia. Wióry mogą powodować tępienie narzędzia, utrudniając przecięcie metalu. Oprócz tego producenci mogą napotykać takie problemy jak czasochłonne ustawianie narzędzi, nierównomierne zużycie narzędzi, powstawanie zadziorów i niska jakość wykończenia powierzchni. Wyzwaniem jest także grat i potrzeba stosowania dużych szybkości.
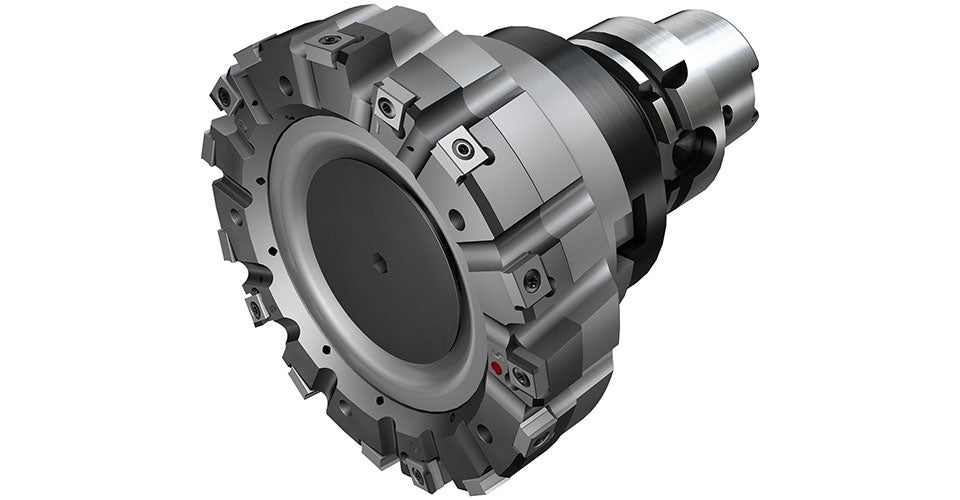
Problemy te można rozwiązać, wybierając narzędzie o zoptymalizowanej konstrukcji, wykonane z zaawansowanych materiałów. Na przykład frez czołowy Sandvik Coromant M5C90, narzędzie z serii M5, został zaprojektowany do obróbki części z litego aluminium z długim czasem frezowania, a także do obróbki zgrubnej i wykończeniowej głowic i bloków cylindrów oraz podzespołów do samochodów elektrycznych. W ramach jednej wydajnej operacji narzędzie M5C90 wykonuje cały proces od obróbki zgrubnej do wykończeniowej. W wielu przypadkach skrawanie może mieć głębokość do czterech milimetrów (mm). Narzędzie to może wydłużyć okres eksploatacji narzędzia pięciokrotnie oraz skrócić czas frezowania nawet o 200%.
Co więcej, frezy z serii M5 wykorzystują rozwiązanie Step Technology, w którym niezwykle trwałe płytki z polikrystalicznego diamentu (PCD) ułożone są w spiralę i stopniowane w pionie, aby usuwać materiał z obrabianego elementu osiowo i promieniowo. Oprócz tego ostatnie ostrze ma geometrię wiper zapewniającą dodatkowo wysokiej jakości wykończenie płaskiej powierzchni. Krawędź skrawająca wiper pozostaje w stałej pozycji, co eliminuje potrzebę czasochłonnego ustawiania. Inne narzędzia w serii M5 to m.in. frez czołowy M5B90 do dokładnej obróbki wykończeniowej oraz frez o mieszanej funkcjonalności M5F90 do obróbki zgrubnej i wykończeniowej mniejszych elementów.
Eduardo Debone
Engineer by formation with Especialization in Business Administration. Proficiency in Product Management, Sales and R&D. 28 years’ experience in automotive and management roles. 18 years in Sandvik Coromant management roles related to Sales, Business Development & Product Management