Sinds de steen-, brons- en ijzertijd in het verleden zijn de grenzen van de mogelijkheden van de mensheid bepaald geweest door de ontwikkeling van allerlei materialen. In de 21ste eeuw zijn de grenzen van de materiaaleigenschappen steeds verder opgeschoven, met name door de ontwikkeling van de lucht- en ruimtevaart en de automobielindustrie.
Het zit in de aard van de mens om steeds meer mogelijk te willen maken. De automobielindustrie is een goed voorbeeld daarvan. Toen Ford een wensenlijst van materialen voor toekomstige auto's opstelde, stonden daar diverse mogelijk levensreddende materialen op. Professor Pim van der Jagt, hoofd research en geavanceerde techniek van Ford, noemt een aantal punten, zoals een nieuw type staal dat drie keer sterker is dan het staal van tegenwoordig, schuimplastic dat constructies kan stabiliseren bij een ongeval en nano-vuller composieten die het gewicht radicaal verminderen en tegelijk sterker zijn. (Bron: http://articles.sae.org/12297/)
In de moderne tijd kijkt ook de lucht- en ruimtevaartsector vooruit naar taaiere, lichtere en hittebestendigere materialen om de emissies en brandstofkosten te verlagen en hogere snelheden mogelijk te maken. In de luchtvaartindustrie richt men zich vooral op composieten. Dr. Eleanor Merson, een specialist op het gebied van composietonderzoek, zegt “Dertig jaar geleden bestond een vliegtuig voor vijf of zes procent uit composieten. Tegenwoordig is een commercieel vliegtuig, zoals de Dreamliner, voor ongeveer 50% gemaakt van composietmateriaal.”
Met slechts een vijfde van het gewicht van staal, zijn koolstofvezelcomposieten nog sterker ook. De Dreamliner, bijvoorbeeld, heeft koolstofvezelcomposieten in zijn vleugels, staart, deuren, romp en interieur, waardoor het een lichter vliegtuig is. Bij vliegtuigen telt immers elke kilogram. Experts schatten dat door elke kilogram die een commercieel vliegtuig lichter is, de exploitatiekosten ervan afnemen met ongeveer 2.000 tot 3.000 euro.
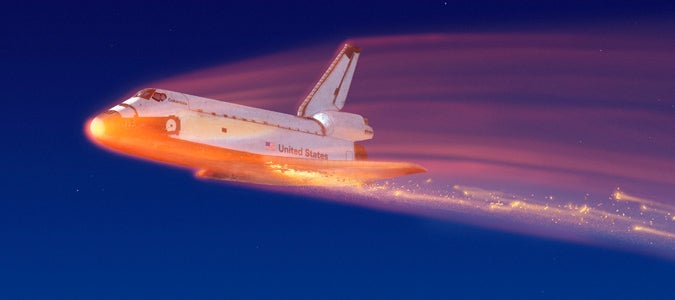
Een Lamborghini vol composieten
Composietmaterialen worden steeds meer toegepast in auto's, windturbinebladen en andere producten. BMW’s elektrisch i3, bijvoorbeeld, is grotendeels van composieten gemaakt. BMW zegt dat door het lichtere gewicht de auto 160 kilometer kan afleggen op een lading. De woest uitziende Lamborghini Veneno Roadster zit vol met gewicht verlagende composietonderdelen die een acceleratie van 0 tot 100 km/uur in 2,9 seconden mogelijk maken. Composieten zijn tegenwoordig weliswaar goedkoper om te produceren en worden door steeds meer bedrijven gemaakt, maar voor de productie van hoogwaardige composieten zijn nog steeds hoge temperaturen, een extreem schone omgeving en arbeidsintensieve processen noodzakelijk. En het bewerken van deze hoogwaardige composieten is een nog grotere uitdaging.
“Verspanen, en met name boren in composieten is een enorme uitdaging,” vertelt Merson, die composieten onderzoekt voor Sandvik Coromant. “Een vliegtuig heeft tienduizenden gaten, en het materiaal is erg abrasief, boren slijten snel in koolstofvezels.”
In de toekomst worden composieten waarschijnlijk verder versterkt door vezels die zijn ontwikkeld op nanoschaalniveau. Men verwacht ook dat wetenschappers tot bijna perfecte oplossingen kunnen komen op atoomniveau. Specialisten van het Duitse chemische bedrijf Altana AG, beweren dat het mogelijk is minuscule nanobuisjes van koolstof te maken die 400 keer sterker zijn dan staal of aluminium en 20 keer sterker dan conventionele koolstofvezels.
Grafeen in smartphones
Materialen zoals grafeen en quasikristallen, waarvan de ontdekkers Nobelprijzen hebben gewonnen, vormen een nog grotere belofte als taaie materialen en kunnen de wereld van het industriële ontwerp volledig op zijn kop zetten. Grootschalige industriële toepassingen worden voorlopig echter nog niet verwacht.
Vorig jaar heeft een Chinese fabriek grafeenkorrels toegepast in zijn mobiele telefoons om de geleiding te verbeteren. Vlokken van quasikristallen zijn ingegoten in bakpannen en metalen chirurgische instrumenten om de duurzaamheid ervan te vergroten. Ofschoon op korte termijn geen grote industriële doorbraken zijn te verwachten, investeert men wel enorm veel in grafeenonderzoek. Grafeen is 200 keer sterker dan staal en is het dunste materiaal op aarde (1 miljoen keer dunner dan een mensenhaar). Tegelijkertijd concentreren onderzoekers bij bedrijven en universiteiten zich op het verbeteren van bekende materialen en technieken.
Lichtgewicht aluminium legeringen hebben nu HSLA-staal (Hoge Sterkte Staal) vervangen in bumpers, veiligheidskooien en zijversterkingsbalken. In vliegtuigmotoren kunnen superharde legeringen die bestand zijn tegen extreme temperaturen de energieconversie helpen verbeteren en de brandstofkosten verlagen.
Coatings harder dan staal
Het fysisch aanbrengen van een stof door opdamping (physical vapour deposition, PVD) of chemisch (chemical vapour deposition, CVD) is een methode voor het bedekken van voorwerpen met een extreem dun maar hard en hittebestendig laagje materiaal. De technieken zijn voor het eerst op grote schaal toegepast in de jaren '80 van de vorige eeuw en worden nog steeds gebruikt voor mechanische, optische en elektronische apparaten.
Sandvik Coromant gebruikt deze methodes voor het verharden van het oppervlak van zijn wisselplaten. De kern van de wisselplaat is gemaakt van gecementeerd volhardmetaal, hoofdzakelijk bestaande uit wolfraamcarbide en kobalt.
“Voeg een twee tot tien micrometer dik laagje PVD toe en de levensduur van de wisselplaat wordt een factor 100 groter,” vertelt Dr. Mats Ahlgren, expert op het gebied van materiaalfysica en hoofd van de PVD-afdeling van Sandvik Coromant. “Niet alleen kunnen onze klanten de wisselplaten veel langer blijven gebruiken, maar ook hun productiviteit neemt toe doordat met deze wisselplaten met veel hogere snelheden en voedingen gewerkt kan worden.”
Op dit moment wordt gezocht naar manieren om de coating taaier te maken om de materialen nog duurzamer te maken.
In de afgelopen jaren zijn we het proces voor het maken van nieuwe coatings steeds beter gaan beheersen,” aldus Ahlgren. “We kunnen de structuur praktisch tot op het niveau van de atomen bekijken onder de microscoop, waardoor we nieuwe oplossingen kunnen analyseren, nog voordat we ze in de praktijk uitvoeren.”
In 2013 heeft Sandvik Coromant zijn CVD-coating Inveio™ gepatenteerd. Met kristallen die alle in dezelfde richting wijzen, was Inveio een grote sprong voorwaarts qua duurzaamheid en hardheid.
Door taaiere materialen te gebruiken, is er minder noodzaak om een grote massa van logge componenten in een enkele structuur te gebruiken. Ontwerpers worden steeds kieskeuriger in het kiezen van materialen voor onderdelen van een auto of vliegtuig. Sommige machineonderdelen hoeven niet zo sterk te zijn. Dat is de filosofie van Ian Scoley, voormalig hoofd Industrial Design bij Airbus, waar hij zich bezig hield met het cabineontwerp. Scoley, nu hoofd Industrial Design bij C&D Zodiac, vertelt dat hij zich liet inspireren door de botten van vogels. “Deze zijn sterk waar dat nodig is, maar ook licht en open waar flexibiliteit nodig is.”
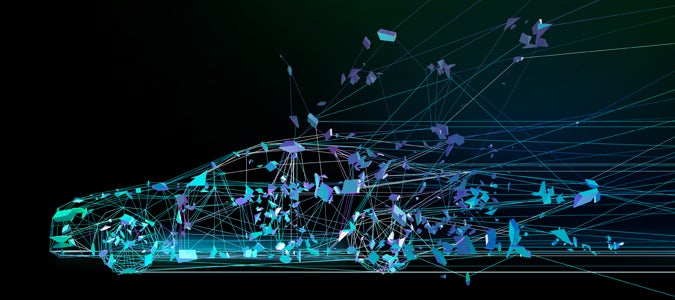
Verbijsterende recycling
Vliegtuigen en auto's verbruiken steeds minder energie en produceren steeds minder uitlaatgassen dankzij de komst van nieuwe materialen en ontwerpen, terwijl tegelijkertijd de recycling ervan steeds belangrijker wordt. Veel composieten, bijvoorbeeld, zijn gemaakt van hechtende bindmiddelen die moeilijk te scheiden en opnieuw te gebruiken zijn. Maar onlangs zijn aluminiumlegeringen voor de auto-industrie gecreëerd met recycling in het achterhoofd.
Tegenwoordig is het hergebruik van materialen namelijk een belangrijke drijfveer bij de automobielproductie. De Europese overheden schrijven voor dat alle auto's zodanig gebouwd moeten zijn dat 85% van de materialen ervan opnieuw gebruikt kunnen worden. “Autofabrieken houden elk onderdeel van de auto tegen het licht om aan die eis te kunnen voldoen,” vertelt Arjen Bongard, een in Duitsland wonende analist van de auto-industrie.
De uitdaging van het hergebruik leidt soms tot oplossingen die tot de verbeelding spreken. Ford is begonnen graanstro en sojaproducten te gebruiken in hun interieurontwerpen, en onderzoekt plasticmaterialen op basis van kokosvezels, wortelen en graan. Het bedrijf streeft ernaar 100% biologisch afbreekbare interieurs te maken.
“Het vinden van alternatieve materialen is een belangrijke traject, net als de noodzaak om kostenefficiënte processen voor de vervanging en recycling te ontwikkelen,” zegt Dr. Anna Hultin Stigenberg, de belangrijkste R&D-expert bij Sandvik Coromant. Stigenberg wat tot voor kort voorzitter van een internationale denktank voor de kennis en innovatie van grondstoffen, een initiatief waarin meer dan 100 bedrijven en onderzoeksinstanties bijeenkomen voor het bevorderen van de ontwikkeling van duurzame materialen.
Op atoomniveau
Waarom tevreden zijn met reeds bestaande materialen? De mensheid kan geheel nieuwe materialen creëren – materialen met specifieke eigenschappen.
“We slagen er steeds beter in nieuwe materialen op atoomniveau te ontwerpen met behulp van moderne microscopen en computerberekeningen,” zegt Hultin Stigenberg.
Sinds het einde van de ijzertijd, zo'n 550 v. Chr., is er geen specifiek materiaal geweest om een tijdperk in de geschiedenis mee aan te duiden. Sommige academici zeggen dat we nu in de plastictijd leven, maar in de toekomst kan onze tijd heel goed het tijdperk van de nieuwe materialen genoemd worden, en de effecten ervan op de ontwikkeling van de mensheid kan wel eens veel groter zijn dan we ons nu kunnen voorstellen.