과제: 터닝 센터를 사용할 때 무인 공구 교환을 늘리고 칩 관련 문제를 없애려면?
해결책: 터닝 센터를 자동 공구 교환 및 고압 절삭유 시스템으로 전환하라
터닝 센터는 제조업계에서 가장 많이 사용되는 가공장비이다. 그런데 터닝 센터의 크기와 상관없이 공통적으로 가공 중단 시간이 불필요하게 많이 소요되는 문제점이 존재한다. 그 중 하나는 수동 공구 교환 방식이고, 또 하나는 절삭유가 절삭 부위로 수동적으로 흐르게 되는 절삭유 시스템이다. 따라서 현재 개발 중인 터닝 센터 모델들은 계획적 · 비계획적 가공 중단 빈도를 최소화하는 데 중점을 두고 있다.
오늘날 자동 공구 교환 기능이 없는 머시닝 센터를 구매하려고 하는 업체는 없지만, 터닝 센터의 경우 자동 공구 교환은 표준기능이 아니다. 그 이유 중 하나는 터릿에 적용되는 공용 공구 홀딩 인터페이스의 부재이다. 공용 공구 홀딩 인터페이스가 있어야 자동 공구 교환도 가능해지기 때문이다. 수평 터닝 센터는 Y-축 가공 기능, 2중 터릿, 서브 스핀들, 대량 가공을 효율적으로 수행하기 위한 모니터링 및 계측 기능 등을 갖춘 모습으로 진화를 마쳤다. 그러나 수직 터닝 센터는 여전히 진화 중인데, 현재로선 자동 공구 교환 기능이 옵션으로 들어가는 다음 단계로 진일보하고 있다. 이러한 진화를 이끄는 것은 당연히 제조업계의 니즈이다. 제조업계는 인간의 손이 덜 가고 용도는 더욱 다양한 가공장비를 원한다. 터릿 위치를 제한할 필요 없이 더 긴 보링 바를 이용할 수 있기를 바라고, 부품 이동을 최소한으로 줄이고 싶어 한다.
미래에 자동 공구 교환 장치와 표준 터릿 인터페이스가 가공장비 컨셉의 일부가 될 것임은 자명하다. 공구 개발과 가공장비 개발은 서로를 이끄는 원동력이다. 신기술을 이끌어내거나 신기술에 반응하는 제조업계 그리고 최저 수준의 가공 비용이 힘을 보탤 때, 공구와 가공장비 기술은 한데 맞물려 함께 발전하게 된다.
고압 절삭유 시스템은 최신 가공 기술에 속하지만, 절삭 프로세스에 실질적인 변화를 일으킬 만한 방식으로 활용되지는 못하는 실정이다. 그러나 CoroTurn HP처럼 30~80bar 범위에서 공용 고압 기능을 이용할 수 있는 컨셉이 존재한다. 이들 컨셉에서는 절삭유가 평행 층류로 분사되며, 분사 노즐의 방향이 가공 시 발생한 칩을 들어올리고 터닝 센터의 가공열을 식히며 칩 제어력을 높이는 쪽을 향한다. 이러한 기술을 통하여, 거의 모든 소재를 더욱 효율적이고 안정적인 무인 생산 방식으로 가공할 수 있다.
그러나 칩 분쇄가 더 까다로운 소재의 선삭에 고압 절삭유를 활용하는 경우, 대부분의 공정에 골고루 적용할 수 있도록 절삭유 속도와 압력을 보다 더 높여야 (압력 150bar까지) 그 효과를 극대화할 수 있다. 절삭유 속도와 압력을 높이면, 절삭 과정은 물론이고 가공 부위 및 칩 컨베이어에서의 칩 관리 면에서도 매우 유리해진다. 이 새로운 성능은 터닝 센터에서도 하나의 고려사항일 것임이 틀림없다. 가공요건이 까다롭고 긴 칩이 발생하는 소재는 칩 제거로 인한 시간 낭비가 발생한 여지가 많기 때문이다. 향상된 칩 제어력과 더불어, 높은 가공 신뢰성도 무인 가공을 현실화하기 위해 터닝 센터에 적용돼야 할 덕목이다.
이러한 과제에 대한 해결책의 실마리는 ISO 표준인 Coromant Capto 모듈식 공구 고정 시스템이다. 이 시스템은 고정식 · 드리븐 공구 홀더를 갖춘 터닝 센터들에 수동 퀵-체인지 시스템으로서 널리 사용돼 왔다. 오늘날 수직 선반과 복합 가공기 역시 동일한 인터페이스를 자동 공구 교환 기능과 결합하여 사용한다. Coromanto Capto 개발의 다음 단계를 위한 모든 노력은 자동 공구 교환 기능을 탑재한 터닝 센터의 개발 안에서 이뤄질 것이다.
절삭유 압력 증가를 준비하는 과정에서, 최소 150bar의 압력을 견디는 실링과 함께 새로운 클램핑 매커니즘이 개발되었다. 이 매커니즘은 터닝 센터의 수동 클램핑 유닛과 복합 가공기 회전 스핀들의 스핀들 클램핑에 적용하기에 적합하다. 지금도 개발 중인 이 기술의 주된 장점은 인터페이스가 일정하게 유지된다는 점, 그리고 기존의 절삭 유닛 및 어댑터와 완전히 호환된다는 점이다.
‘‘미래에 자동 공구 교환 장치와 표준 터릿 인터페이스가 가공장비 컨셉의 일부가 될 것임은 자명하다.”
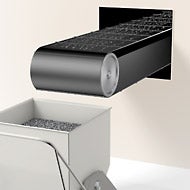
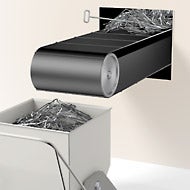
일관성 있는 칩 제어 기능
난삭재를 가공할 때는 칩 제어력을 일정하게 유지하기 위해 고압 절삭유의 도움을 받기도 한다. 그런데 고압의 장점을 최대한 활용하려면, 오늘날 흔히 사용되는 수준보다 더 높은 압력을 활용해야만 한다. 즉 압력을 최대 150bar까지 끌어 올려야 대부분의 공정을 수행할 수 있다는 것이다. 이렇게 높은 압력으로 절삭유를 분사할 수 있게 된다면, 절삭 과정은 물론이고 가공 부위 및 칩 컨베이어에서의 칩 관리 면에서도 매우 유리해진다.
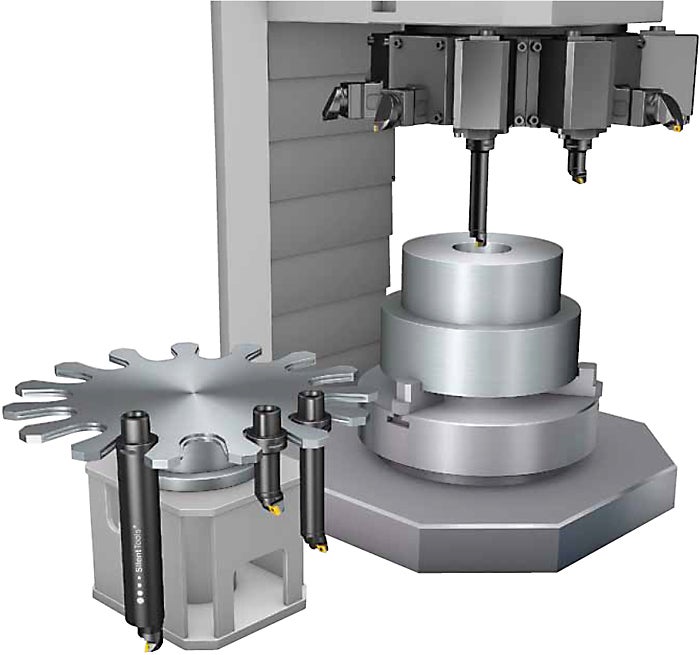
수직 터닝 센터
터닝 센터도 머시닝 센터와 마찬가지로 자동 공구 교환이 되는 방향으로 진화하고 있다. 짧은 공구의 가공 수행력에 방해가 되는 긴 공구의 제거 필요성, 효율성 제고, 무인 생산 실현의 의지 등이 이러한 진화를 이끄는 요인으로 작용한다. Coromanto Capto의 개발도 고정식과 구동식에 모두 사용할 수 있는 공용 공구 홀더 인터페이스를 갖추는 방향으로 이루어지고 있다.
요약
절삭유가 절삭 부위에 분사되는 방식과 공구 교환 시간의 변화를 꾀하는 업체는 가까운 미래에 더욱 높은 경쟁력을 자랑하게 될 것이다. 특히 터닝 센터의 성능 면에서 말이다.
이 기사는 샌드빅 코로만트 고객 매거진인 Metalworking World에 처음 게재되었다.