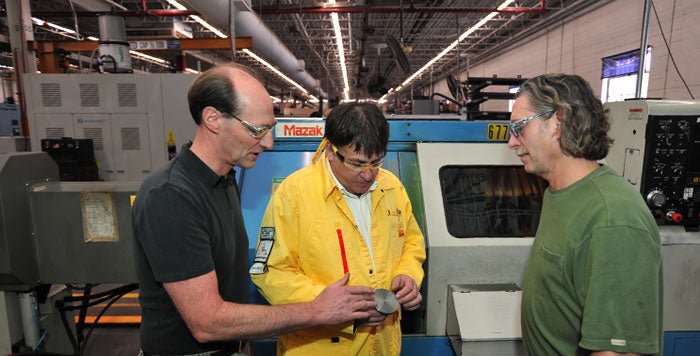
David Turk, Jim Pappas (műszaki szaktanácsadó, Sandvik Coromant) és Tom Waite vizsgálják az alkatrész CoroCut® QD-vel elért felületi minőségét.
Bár megjelentek némileg gyorsabb szerszámozási opciók, David Turk és a BUCHER Emhart Glass nem szívesen váltott volna a jól bevált leszúró szerszámaikról. Egy új termék azonban, amely megháromszorozta termelékenységüket, végül segített meggondolni magukat.
Az üvegedények és palackok olyan elterjedtek, hogy szinte mindenki használt már a BUCHER Emhart Glass berendezésein gyártott és ellenőrzött termékeket. A már több mint egy évszázada kiváló minőségű üvegedényeket gyártó Bucher Emhart Glass kifejlesztette az iparági szabványnak minősülő Individual Section (IS) gépet, amely mára a legszélesebb körben, világszerte használt üvegedénygyártó berendezés. A gép 5-20 azonos részből áll, amelyek mindegyike önálló mechanizmussal rendelkezik különböző méretű üvegedények gyártásához – nagyobbrészt az orvosi, tudományos, élelmiszeripari és italgyártási szegmensek számára.
Az üveggyártásban a vizsgálat és a hibaelemzés kritikus fontosságú lépés. Ahhoz, hogy a Bucher Emhart Glass folyamatosan kiváló minőségű üveget gyárthasson, megvásárolta a Powers Manufacturing vállalatot Elmirában, New York államban 1982-ben. A Powers Manufacturing nemzetközileg elismert, kiváló vizsgálati berendezéseket gyártott.
A BUCHER Emhart Glass elmirai kirendeltsége a mai napig tervez, gyárt, összeszerel és szállít komplex vizsgálóberendezéseket. Az elmirai telephely 140 dolgozónak ad munkát, egy gépműhellyel és egy összeszerelő műhellyel. A gépműhely területe körülbelül 1100 négyzetméter, ahol 25 dolgozó váltja egymást két műszakban.
A műhely hét függőleges, két vízszintes géppel, három 3 tengelyes esztergával és egy 7 tengelyes esztergával van felszerelve. A márka szerinti megoszlás a következő: egy Mazak maró- és esztergagép, három Hardinge eszterga, két Haas gép, egy Komo gép és egy függőleges Bridgeport gép. Az elsődleges anyagok a leadloy 12L14, amely lágy és könnyebb megmunkálni, továbbá az alumínium, bronz és rozsdamentes acél, amelyek megmunkálása nehezebb.
A munkafolyamat az Emhart gépműhelyben számos rövid feladatra aprózódik. Az állásidők csökkentése érdekében az ütemezés a kezelők rugalmasságát követeli meg, mivel a gyakori átállások nagyobb nyomást jelentenek a gépekre és a szerszámokra nézve, hogy minél gyorsabb legyen a munka. Ezek a rövid feladatok optimális forgácsolási sebességeket és hosszú éltartamokat követelnek meg ahhoz, hogy a műhely termelékeny maradhasson.
„A 90-es évek közepe óta használunk Sandvik Coromant szerszámokat, legtöbbször maráshoz és esztergáláshoz” – mondja David Turk, az Emhart Glass gyártómérnöke. „A Sandvik Coromant a legnagyobb lapka- és szerszámtartó-beszállítónk. Vannak mások is, de ők szállítják keményfém váltólapkáink 80-85 százalékát. Jó kapcsolatot ápolunk helyi szerszámbeszállítónkkal, a One Time Tool céggel, és ők javasolták, hogy próbáljuk ki a Sandvik Coromantot – megtettük, és azóta az ő szerszámaikat használjuk.”
Bár Turk már használt Sandvik Coromant szerszámokat más műveletekhez, nem volt meggyőződve róla, hogy meg kell változtatnia a jelenlegi leszúrási műveleteket az esztergán. Az évek során megszokott folyamat és termék használata közben keresett olyan termékeket, amelyekkel jelentős fejlődést lehetne elérni, de egyik kipróbált termék sem adott túl sokat. A leszúrás gyakori művelet az Emhartnál. Több alkatrészen is el kell végezni.
„Mivel gyakran a befejező művelet a megmunkálási folyamatban, a leszúrás kritikus fontosságú lépés.”
Mivel gyakran a befejező művelet a megmunkálási folyamatban, a leszúrás kritikus fontosságú lépés. A gépbeállítások, programozás és a forgácsképzési műveletek között a kezelők és a gépek jelentős időt töltöttek az alkatrész megmunkálásával, mire a leszúrásra került a sor. A leszúrás előtt már megtörtént az alkatrész esztergálása, menetfúrása, fúrása, horonymarása és simítása. Ilyen idő- és gépkapacitás-befektetés után selejtet gyártani megengedhetetlen. Így ragaszkodni kellett ahhoz a folyamathoz, amiről Turk és az Emhart egyéb dolgozói úgy gondolták, hogy a legjobb megoldást jelenti, hacsak nincs valami új, ami radikálisan növelni tudná a termelékenység szintjét.
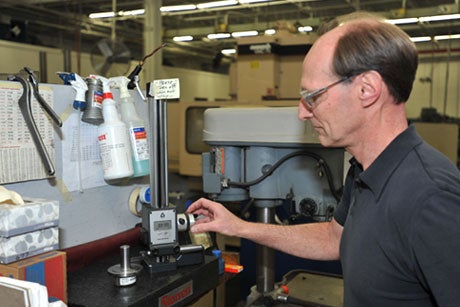
Az átállás igazolása
„Kipróbáltunk különböző lapkákat, különböző beszállítókat, még néhány Sandvik Coromant lapkát is, de nem láttuk azt az előnyt, amely igazolhatta volna a váltást” – mondja Turk. „Mivel sok rövid feladatot kell elvégeznünk, és ezeknél rengeteg beállítást és programozást kell módosítani, olyasmit kerestünk, amely anyagilag is igazolni tudná a váltás jogosságát. Az évek során kisebb növekedést sikerült ugyan elérnünk a sebesség és a hatékonyság terén más lapkákkal és szerszámokkal, de ez nem volt elég ahhoz, hogy váltsunk.”
És bár Turkre egyetlen, a piacon fellelhető leszúró szerszám sem lelkesítette különösen, a kezelő, Tom Waite, kérte, hogy továbbra is kísérje figyelemmel a megjelenő új leszúró szerszámokat 2013 őszén. Közben Jim Pappas, a Sandvik Coromant értékesítő mérnöke befejezte a vállalat új CoroCut QD leszúró és beszúró szerszámának megismerését. Itt volt az ideje, hogy Pappas felhívja Turköt.
„Beszéltünk az új termékekről, eljutottunk a leszúró és beszúró szerszámokig, ekkor megemlítettem Tom kérését az ilyen szerszámokkal kapcsolatban, és mindketten megláttuk a lehetőséget” – mondja Turk. „Jim behozott egy CoroCut QD-t az üzembe, megadta a paramétereket, elővett egy nagy nyersdarabot, és elkezdte a tesztelést. Azonnal meglepődtünk azon, hogy ez a szerszám hogyan képezte a forgácsokat – elképesztő volt.”
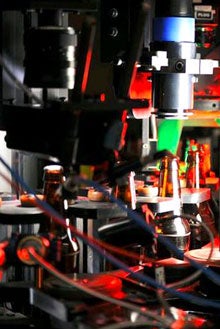
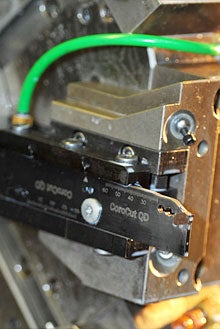
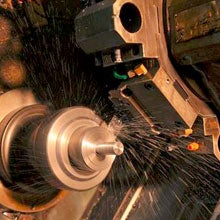
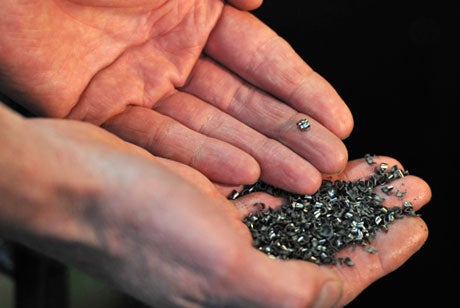
Azonnali javulás
Turk már az első naptól azokat az eredményeket kapta, amelyekre várt a leszúró alkalmazásokban. A CoroCut QD-vel megháromszorozta a fordulatonkénti forgácsok számát és a felületi előtolást. Az anyag olyan gyorsan mozgott, hogy le kellett csökkenteniük az orsó sebességét az éltartam optimalizálása érdekében, amely egyébként Turk szerint szintén jelentős volt.
„Azelőtt nagyjából öt lapkát használtunk el hetente; ettől kezdve csak egyet” – mondja Turk. „Ami a sebességet illeti, eredetileg 200 felületlábat értünk el percenként és 0,002 colt fordulatonként, most azonban 600 felületlábat percenként és 0,007 colt fordulatonként, ez drámai növekedés.”
Az anyag gyorsabb mozgása közvetlenül több alkatrész gyártását jelenti. Az időzítés mindig függ az esztergált alkatrész átmérőjétől, de egy 3 colos nyersdarab esetén Waite és Turk a 20 másodperces leszúrási időt 6-8 másodpercre csökkentette. Óvatos becsléssel, egy 10 másodperces időt figyelembe véve (az átmérőváltozások miatt) Turk gyors számításai azt mutatják, hogy a CoroCut QD körülbelül 15 percet takarít meg műszakonként, amely naponta félórát jelent. Ezt az értéket az egész évre vetítve 125 megtakarított órát kapunk.
A világ legnagyobb sebessége sem érne semmit azonban a pontosság nélkül. Az ismételhető egyenes vágások garantálása legalább ilyen fontos.
„A forgácsolás minősége is jó, de szép és egyenes is.”
„A forgácsolás minősége is jó, de szép és egyenes is. Leszúrásnál néha konkáv vagy konvex kúpot kap az ember; befelé vagy kifelé hasasodva” – mondja Turk. „Egy indikátort, vagyis egy kúp mérésére szolgáló műszert használtunk annak ellenőrzésére, hogy a penge az alkatrész felületére merőlegesen haladt-e. A kalibrálás elvégzése után már minden rendben ment.”
Mivel a fő tesztek drámai előrelépést mutattak a termelékenységben, a legnagyobb pontosság megőrzése mellett, mindez végül meggyőzte Turköt. Azonban, mint a gépek fő kezelője, Waite is igényelt némi meggyőző erőt. Ő akkor győződött meg az előnyökről, amikor egy művelet során az eszterga revolverkonfigurációja azt követelte meg, hogy a CoroCut QD szerszám fejjel lefelé álljon.
„Az esztergagépeken gyakori eljárás a forgácsolási felületet lefelé állítani, hogy a gravitáció segítsen a forgács eltávolításában. A gravitáció segítsége nélkül a forgácsok elakadhatnak az összehasonlítva keskeny leszúró és beszúró műveletek során, amely akár 3/16 col (vagy 5 mm) is lehet; ez igen keskeny horony, ahonnan a forgácsokat el kell távolítani” – mondja Turk. „Tom gyorsan hangsúlyozta, hogy mennyire előnyös, ahogy a hűtőfolyadék kimossa a forgácsokat a horonyból – még a normál állású forgácsolásnál is.”
Turk szerint a szerszámon keresztül áramló hűtőfolyadék pontosan a forgácsolóélre kerül, segít növelni az éltartamot és a forgácseltávolítás hatékonyságát. A korábbi leszúró szerszám külső hűtőfolyadékot használt, amely nem biztosította ugyanezt a pontos hűtőfolyadék-rávezetést.
Általában előnyös ösztönösen ragaszkodni a megszokott rendszerhez, különösen, ha nincs jobbnak tűnő megoldás. De gyakran a bevált megoldáshoz való ragaszkodás megakadályozza, hogy az üzem új megoldásokat próbáljon ki, amelyek óriási műszaki előrelépést jelenthetnek. Turk és Waite kiváló példák olyan mérnökökre és kezelőkre, akik türelmesen megvárták a megfelelő termék megfelelő időben történő megjelenését, és elég tapasztaltak voltak ahhoz, hogy váltsanak a leszúró szerszámok új generációjára.
„Turk hirtelen megkapta azokat az eredményeket, amelyekre várt a leszúró alkalmazásokban.”
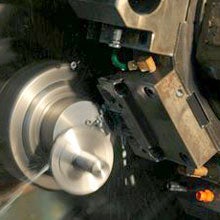
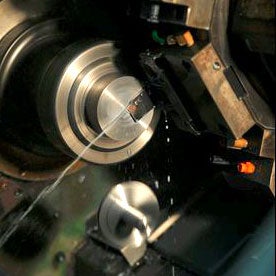
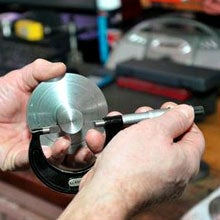