A jövő gyára
A Világgazdasági Fórum fejlett Ipar 4.0 létesítményként ismerte el a Sandvik Coromant Svédországban, Gimóban található szerszámgyártó üzemét.
A Sandvik Coromant szerszámgyártó üzeme Stockholmtól északra, Gimóban található. Nagyrészt automatizált létesítmény, amely teljes mértékben kiaknázza a digitális gyártás nyújtotta előnyöket. Ezt ismerte el nemrégiben a Világgazdasági Fórum, amely a gimói üzemet nemzetközi referenciahelyszínének nyilvánította. A referenciahelyszíneket egy 1000 gyártóegység részvételével zajló felmérés során választják ki, az alapján, hogy mennyire sikeresen alkalmaznak digitális technológiákat és érnek el kézzelfogható előnyöket.
A Világgazdasági Fórum szerint a gimói létesítmény olyan digitális szálat hozott létre gyártási folyamatai révén, amely jelentősen javította a termelékenységet. Példaként említhetjük az érintésmentes újrabeállítást, melynek segítségével a tervezési minták automatikusan cserélhetők, akár a felügyelet nélküli műszakokban is. Az ilyen kiemelkedő előnyök révén lett része a gimói üzem a referenciahelyszínek nemzetközi hálózatának, aminek köszönhetően megoszthatja tudását más gyártócégekkel is.
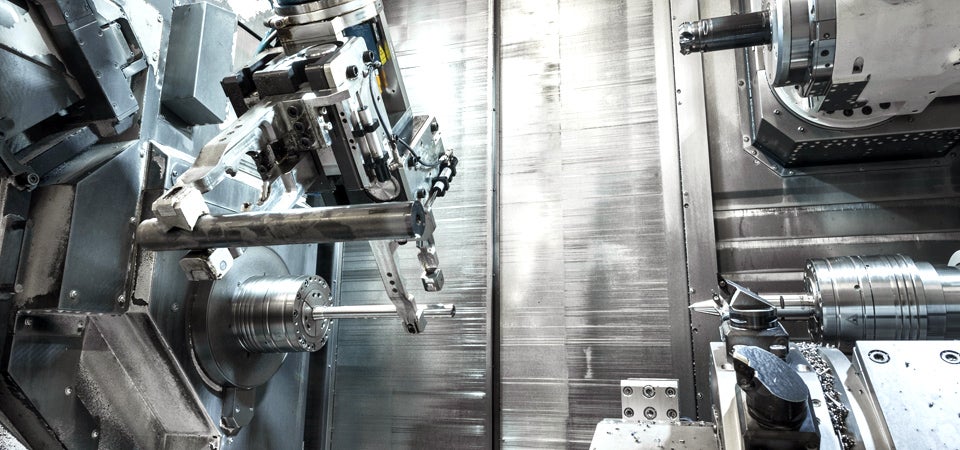
Lars Matiasson, a Sandvik Coromant gyártástechnológiai eszközökért felelős igazgatója szerint a díjat valódi büszkeséggel fogadja a gimói üzem, különösen annak tekintetében, hogy azzal az innovációért tett hosszú távú erőfeszítéseket ismerték el. „Gimo útja a digitalizáció felé 30 éve kezdődött, a parametrikus CAD/CAM bevezetésével, melyet néhány évvel később csatlakoztattunk az intelligens automatizált rendszerhez, és így megszületett az első digitális szál gyártási folyamatunkban. Inkább tartós fejlődés volt ez, mint hirtelen újítás.
Ma már a digitális szál végigfut az üzemen, a készletkezeléstől a gépteljesítményen át a prediktív karbantartásig. Ez az innovatív hozzáállás mindig maximálisan jellemzett minket. Az üzem igazgatói és vezetői a kezdetektől arra bátorítják a mérnököket, hogy merjenek egyedien gondolkodni, és kezdeményezzék a változást. Tulajdonképpen azt szerettük volna látni, hogyan használható a technológia az üzem hatékonyságának és versenyképességének növelésére. És ezzel fenntartható jövőt teremtettünk.”
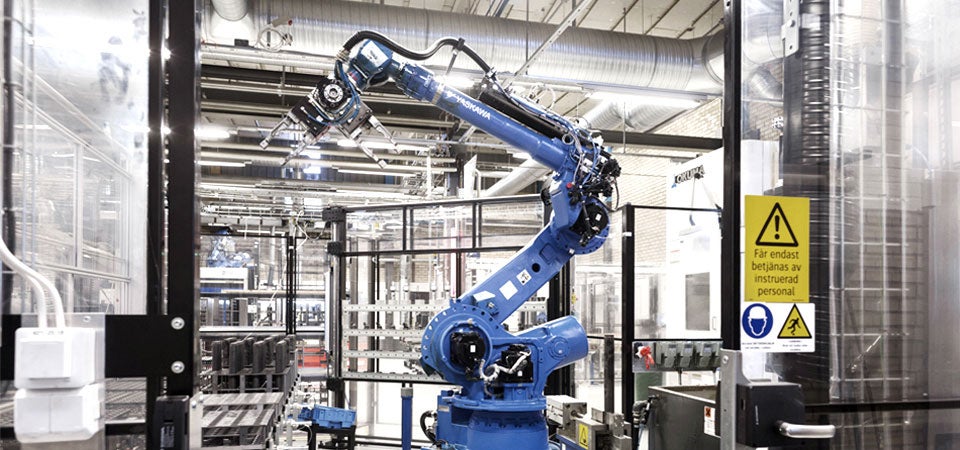
Az érintésmentes újrabeállítás kiváló példa erre. Korábban a gyártócellák tervezési mintáit kézzel kellett cserélni, a gépeket a nappali műszakokban dolgozó gépkezelők készítették elő az éjjeli működésre. Ez időt és erőforrást igényelt, és korlátozott rugalmassággal járt a felügyelet nélküli műszakokban. Alternatív megoldásként kínálkozott, hogy beruháznak az intelligens automatizált rendszerbe, ahol ultra rugalmas robotok, gépek, szerszámok és befogók közösen végezték el az összetett és érintésmentes újrabeállítást, mindenfajta emberi beavatkozás nélkül.
„Mindenki az olyan „lean” gyártási technikákról beszél, mint a süllyesztékek egyperces cseréje, de mi ennél többre vágytunk. A célunk az emberi beavatkozást egyáltalán nem igénylő összeállítás volt” – fogalmaz Matiasson.
„Valódi tanulási folyamat volt. Az első automatizált cella nem a tervek szerint működött. Valójában még azt a hatékonyságot sem érte el, mint egy gép egy kezelővel. De erről szól a digitalizáció: a kudarcokból tanulunk. Fokozatosan jelentős javulást értünk el, és a robotizált cellák közelíteni kezdtek a várt hatékonysághoz. A próbálkozások és a hibák a fejlődés fontos részét képezik.”

A digitális technológiákat a gimói üzem más területein, például a karbantartás során is alkalmazzák fejlesztési céllal. Fokozatosan szereljük be az érzékelőket az üzem különböző berendezéseibe, hogy egyre több paraméterrel (például nyomás, hőmérséklet, rezgés, akusztika) kapcsolatban gyűjthessünk adatokat. Ezek részletes elemzésével még a leállás előtt azonosíthatók a minták és a problémák.
A mérnökök ma már a gyártóüzem minden részéről gyűjtik az adatokat: a robotoktól, a CNC-gépektől vagy akár a forgácsolószerszámoktól. A kinyert és elemzett adatok értékes betekintetést nyújtanak a berendezés működésébe. Az információk segítségével előre jelezhetők és megelőzhetők a hibák, azaz növelhető az üzem hatékonysága.
A Sandvik Coromant egyre nagyobb mértékben alkalmazza a valós idejű analitikát a gyártási környezetben, így még pontosabb és időszerűbb beállításokat végezhet a gépeken. „A következő lépés az olyan kifinomult technikák bevezetése, mint a mesterséges intelligencia és a gépi tanulás, melyek során a gépek a korábbi adatokból tanulnak, és önkontrollra képesek. Ez egy igazán izgalmas terület.”
A jelentős technikai fejlődés és a Világgazdasági Fórumtól kapott „referenciahelyszín” cím ellenére a gimói üzem digitalizációs utazása soha nem ér véget.