Not all waste is visible (but it’s costing you)
Most factories don’t lose money in obvious places: the real waste hides in outdated processes, inefficient planning, and silent cost drivers nobody questions. Scrap piles up. Downtime eats into margins. Tools sit unused while operators waste time searching for the right equipment. By the time anyone notices, the damage is done
The solution is obvious: fix the leaks before they drain your profits.
Easier said than done—but we can help you figure out where to start.
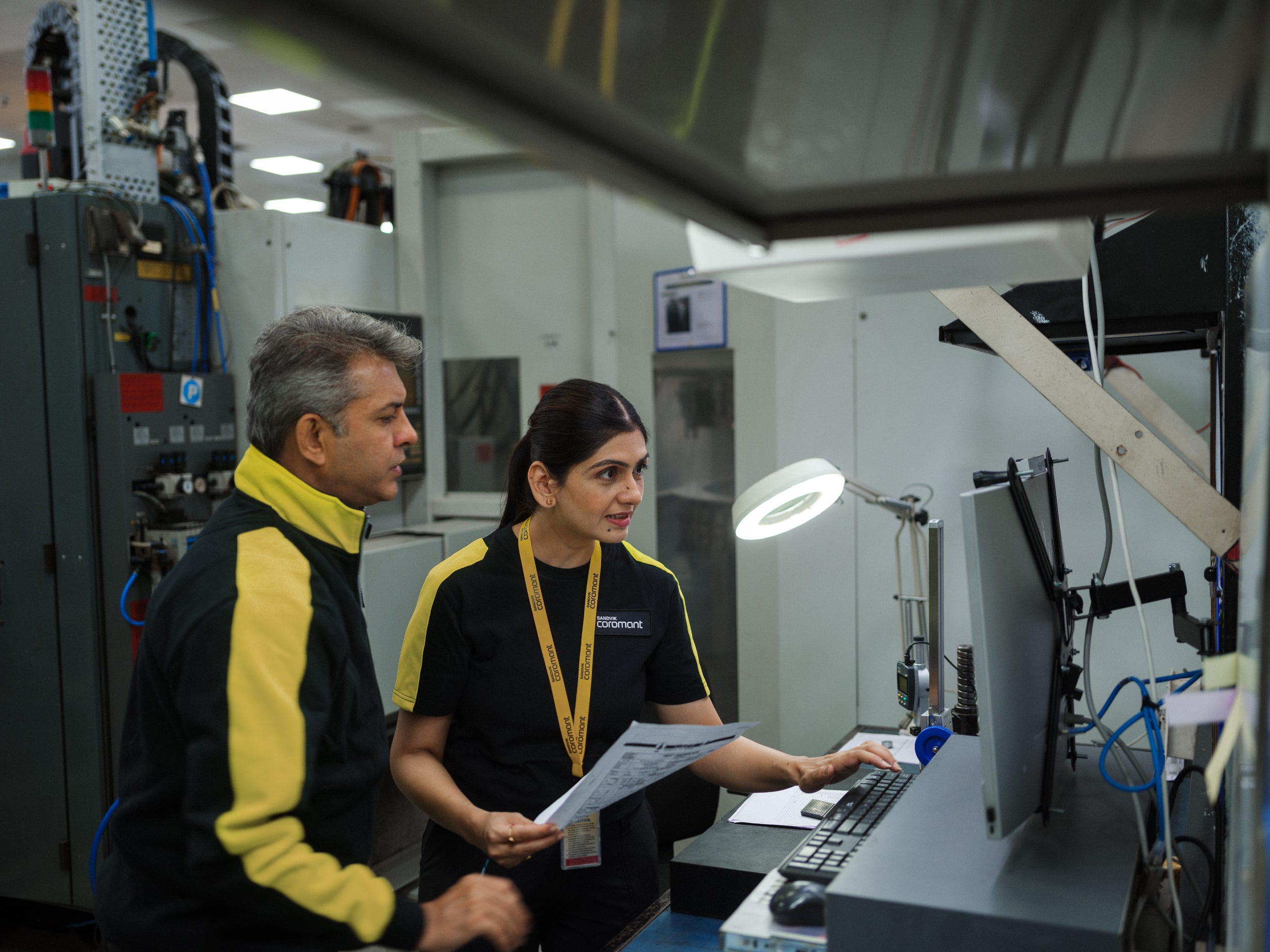
Retrace the steps
It all starts in the early stages of production. Poor design and inefficient planning build unnecessary costs into your workflow before a single chip is cut. A flawed process can’t be saved by perfect execution. By optimizing design, machining strategies, and production logistics from the start, you eliminate waste before it begins.
Become familiar with the data
Transparency is another game-changer. If you don’t know where the money is going, you can’t stop it from disappearing. Data-driven production planning, real-time machine monitoring, and performance insights give you control over inefficiencies before they become expensive problems.
Use all the tools in your box
And then there’s tooling. Many factories are sitting on piles of unused tool inventory while operators scramble for the right tools. A smarter logistics system keeps what you need at hand, trims excess stock, and frees up capital for more valuable investments.
Automate where needed
Automation is your next step. Manual tasks—programming, tool changes, inspection—steal time and leave room for error. Streamline them. Let technology handle the repetitive work while your team focuses on creative tasks and activities requiring nuanced decision-making.
Manufacturing can be lean, fast, and profitable—but only if you take control of your costs before they take control of you.
Want to know more? Download our guide and discover five key steps to cut costs at the source.
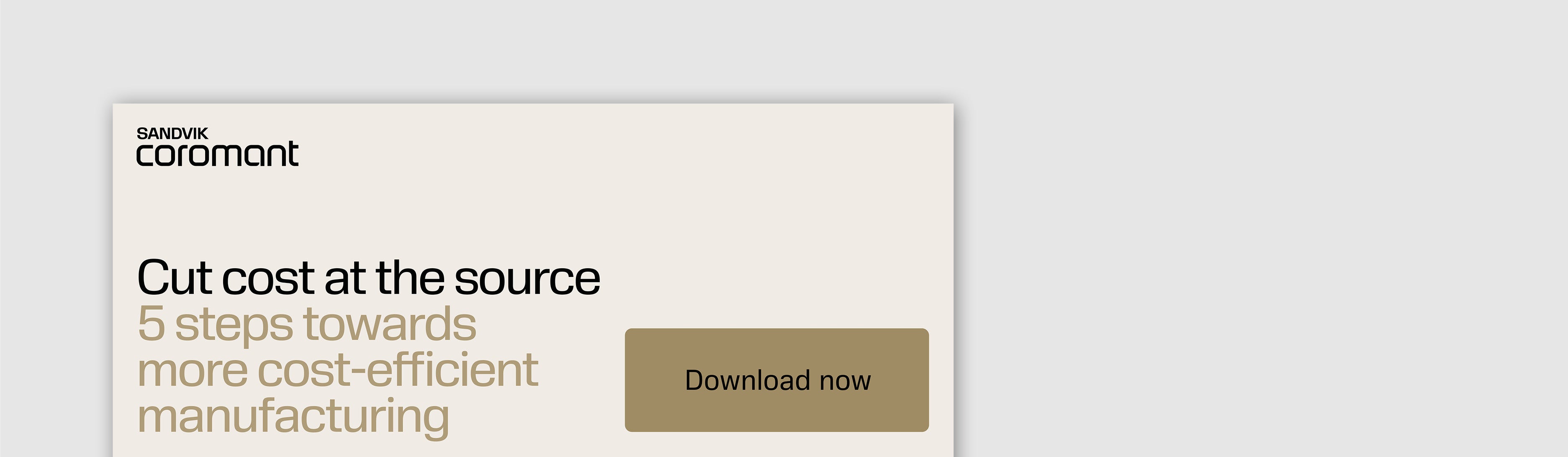