Factory of the future
The Sandvik Coromant Gimo tool production plant in Sweden has been recognized by the World Economic Forum as an advanced Industry 4.0 facility.
The Sandvik Coromant tool production plant at Gimo, north of Stockholm, is a highly-automated facility that fully embraces the many benefits of digitally-connected manufacturing. This was recently acknowledged by the World Economic Forum which announced Gimo as one of its global “lighthouse” sites. Each lighthouse is selected from a survey of over 1,000 manufacturing units based on their success in adopting digital technologies and demonstrating tangible benefits.
According to the World Economic Forum, the Gimo facility has created a digital thread through its production processes that has significantly raised productivity. One example is its ‘touchless changeover’ which allows design patterns to be changed automatically, even during unmanned shifts. Such best-in-class advances means Gimo will now become part of the global lighthouse network, opening its doors and sharing knowledge with other manufacturing businesses.
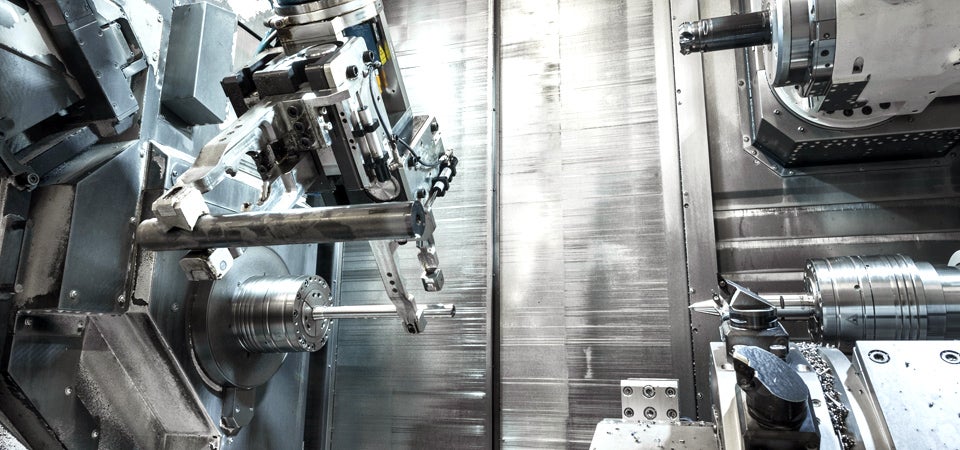
The award has been received with a real sense of real pride at Gimo, says Lars Matiasson, director of production technology tools at Sandvik Coromant, particularly as it recognizes the culmination of long-standing efforts to encourage innovation. “The journey to digitalisation here at Gimo actually started 30 years ago with the implementation of parametric CAD/CAM and then a few years later we connected that to our smart automation, thereby creating the first digital thread in our production. It has been very much an evolution, rather than a revolution.
“Now we see a digital thread running through the plant, from inventory management, all the way through to machine performance and predictive maintenance. That spirit of innovation has always been a top-down commitment. The directors and managers at Gimo have always encouraged the engineers to think differently and to drive change. Ultimately it has been about looking at how technology can be used to improve efficiency and increase competitiveness of the plant. That, in turn, has helped deliver a sustainable future.”
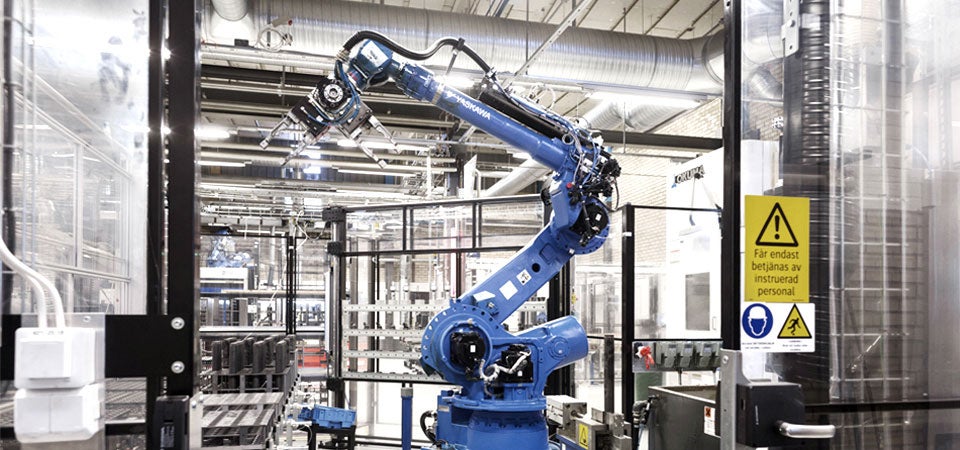
The touchless changeover is a case in point. Historically, design patterns in production cells had to be changed manually, with operators from the day shifts preparing the machines to run through the night. This took time and resources, and limited flexibility during unmanned shifts. The alternative approach was to invest in smart automation with ultra-flexible robots, machines, tools and fixtures which together were able to perform complex touchless changeover without the need for any human oversight.
“People talk about lean production techniques such as single minute exchange of die, but we wanted to go further than that. We wanted zero labour set up,” says Matiasson.
“It was a learning curve. The first automated cell didn’t work as well as we’d hoped. In fact, it was not even as efficient as having one operator and one machine. But that’s the thing about digitalisation - you need to be able to fail to learn. Gradually we managed to make significant improvements and the robotic cells started to reach the kinds of efficiency we needed. Trial and error are important parts of getting better.”

Digital technologies are also being used to deliver improvements in other areas at Gimo, such as maintenance. Increasingly, sensors are being fitted to a wide range of equipment in the plant, collecting data around growing list of parameters such as pressure, temperature, vibration and acoustics. This data, combined with sophisticated analytics, can reveal patterns and problems before downtime occurs.
Engineers now collect data from across the production facility – from the robots, the CNC machines, and even from the cutting tools themselves. Once this data is extracted and analysed, it can present valuable insight into equipment health. That information can in turn be used to predict and prevent failure, and therefore improve plant efficiency.
Increasingly, Sandvik Coromant is also applying real-time analytics to the production environment, enabling it to make even more accurate and timely adjustments to machines. “The stage after that will be to introduce highly-sophisticated techniques such as artificial intelligence and machine learning, where machines can learn from historic data and have an element of self-control. That’s a really exciting area.”
Despite these notable technical advances, and the lighthouse recognition from the Word Economic Forum, the journey to digitalisation at Gimo never stops.