How did we make it?
How Sandvik made the world’s first 3D printed, smash-proof guitar
Rock stars have been smashing guitars for decades, few with more enthusiasm than Swedish-born guitar virtuoso Yngwie Malmsteen. Sandvik decided to test their cutting-edge techniques by building the world’s first all-metal, unbreakable guitar and letting Malmsteen unleash his smashing skills on it.
Sandvik gathered experts from across the company to demonstrate how its engineers could use sustainable, cutting-edge techniques to make something that is both highly precise and amazingly durable.
“Advanced materials, precision machining, additive manufacturing, data-driven production—these are the kinds of processes it takes to create something as complicated and beautiful as a guitar for a master musician,” said Klas Forsström, President of Sandvik Machining Solutions. “But we also wanted to show that we could make it unbreakable, no matter how hard Yngwie tried to smash it. This project seemed like a perfect match for our skills and capabilities—and his.”
Collaboration from the start
Months before the Florida concert, back in Sweden, Sandvik gathered experts in materials, machining processes and additive manufacturing from across the company to brainstorm ways to meet the challenge.
Because Sandvik had never made a guitar before, the company collaborated with renowned guitar builder, UK-based Drewman Guitars. “We had to innovate from the top down,” said Drewman designer Andy Holt. “We wanted musicians to say, ‘I have never seen a guitar that’s made like this.’”
Holt said there was a period during the development process where he sent the engineers at Sandvik a new digital design file every day. In close cooperation with the guitar maker they designed what, in the end, both agreed was a masterpiece of technological creativity.
The world’s first smash-proof guitar
Henrik Loikkanen, machining process developer at Sandvik Coromant, has been playing guitar since his youth when he idolized Malmsteen. But he’s never smashed one (“too expensive,” Loikkanen said). So, to understand what happens when Malmsteen destroys an instrument, Loikkanen turned to YouTube.
“We had to design a guitar that is unsmashable in all the different ways you can smash a guitar,” Loikkanen said. “The engineering challenge was that critical joint between the neck and the body that usually cracks on a guitar.” So Sandvik Coromant engineers decided to eliminate the joint. Both the neck and fretboard extended into a rectangular “hub” that would reach deep into the guitar’s body.
Because a scalloped fretboard allows Yngwie to control notes better, engineers had to cut away material in long, smooth arcs between the frets. To make the guitar as light as possible, Sandvik Coromant hollowed out the interior surfaces of the neck and fretboard.
“The height of each fret had to align perfectly, otherwise we would hear the strings touching some of the frets,” Loikkanen said.
Data on the cutting edge
Long, slender components like the fretboard and neck are particularly vulnerable to distortion in the machining process. Advanced software allowed Sandvik Coromant to simulate the task digitally before the first cut was made.
“Precision was critical,” said Henrik Loikkanen. “Our software is built on years of experience. It provides the kind of tool and cutting data recommendations that helped us mill the fretboard down to a challenging thickness of one millimeter in places.”
The automated process also meant the fretboard could be milled in only one machine. The process required 90 separate operations and was completed without stopping the machines to set up new tools and cuts.
“You put in a raw piece of material and out comes a finished part,” said Loikkanen. “It is a more intelligent way to remove material. You can reduce cycle time, add tool life and produce parts at a cheaper cost.”
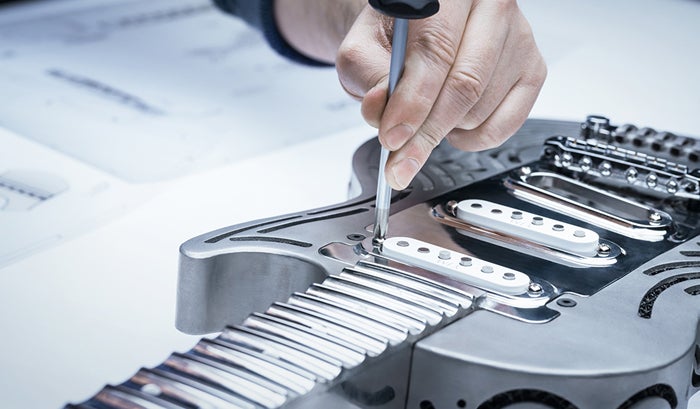
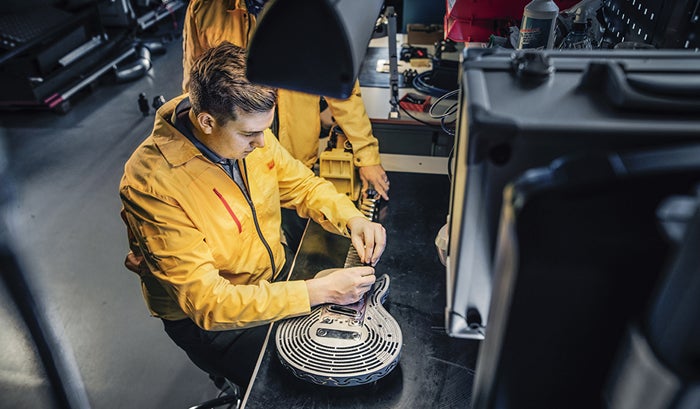
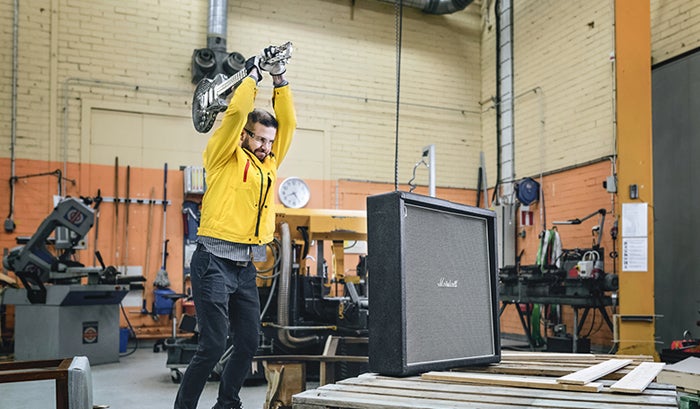
Engineers were able to make each prototype lighter than the previous version, until the final guitar was produced. Fine CoroMill® cutting tools finished the metal in beautifully smooth and shining surfaces.
Loikkanen said that collaboration with other Sandvik divisions was key to producing the smash-proof guitar. He was able to help Sandvik Additive Manufacturing mill the finishes on the guitar’s body and small components, which were all 3D printed using titanium. Sandvik Coromant also worked with Sandvik Materials Technology to select the component steel and incorporate a hyper-duplex lattice structure inside the neck. That teamwork, he said, was the real purpose of making the guitar.
“Sandvik Coromant is famous for helping our customers with complex tasks—not just providing tools but also helping develop the best methods for using our tools in their processes,” Loikkanen said.